Auto-cables
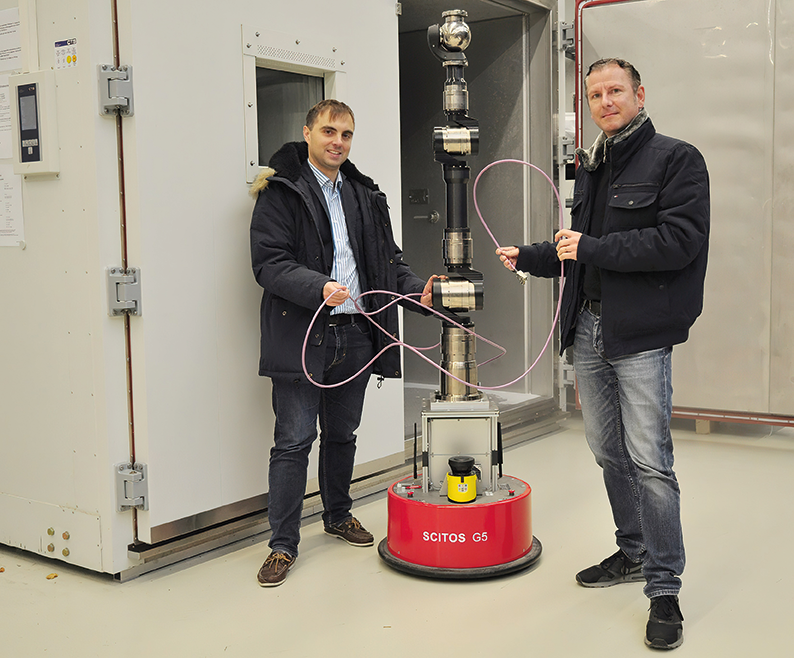
Researchers in Germany have developed a process for the automated manufacture and assembly of cable harnesses (writes Nick Flaherty).
The process, developed at the Faculty of Mechanical Engineering and Mechatronics at the Karlsruhe University of Applied Sciences, will make it possible to use industrial robots to manufacture them flexibly and economically.
Wiring harnesses are among the few parts that still have to be manufactured or processed by hand, especially in automotive and consumer goods production. A highly complex wiring harness connecting multiple sensors and processing units can weigh up to 60 kg, and have a total length of several kilometres in driverless cars, UAVs and many other uncrewed systems.
To reduce the size and weight of the harness, the cables, connections and plugs are becoming ever smaller, making manual construction increasingly difficult. So far, the individual cables have had to be laid on a cable board and bent in certain directions or plugged together. Automation has proved difficult because previous gripping systems could not grip cables that were not placed precisely or to connect plugs.
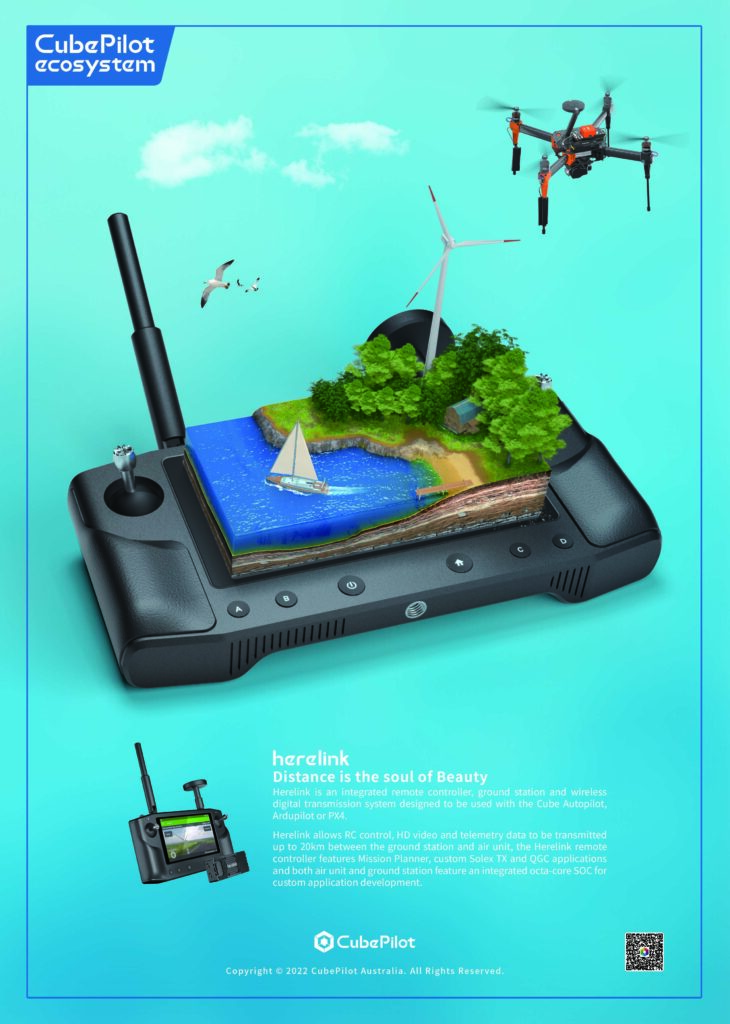
The patented process freezes the entire cabling structure and heats small areas to construct the harness. After the cables have reached a rigid state by freezing, they are shaped by industrial robots.
The cables are placed on a jig built from controllable, moveable and temperature-controlled pins. Cooling can take place in a suitable area or by heating and cooling element contained in the gripper of an industrial robot.
The cables are heated locally at the bending point so that the insulation is not irreversibly damaged during the deformation. The cables are then immediately cooled down again to stabilise the bend. The robotic arms can then align the next section of cable with a predefined force. The cables can also be inserted into connectors during assembly without kinking them.
This allows the wiring harness to be produced shortly before required and to the latest specification, avoiding delivery times that can be several weeks and shortening the supply chain. If a harness can be manufactured within the production run using automation, the so-called one-piece flow also becomes possible, which in turn increases flexibility.
UPCOMING EVENTS
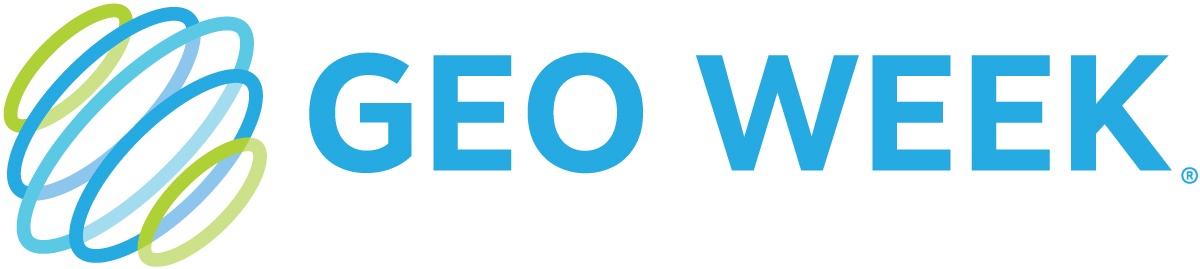
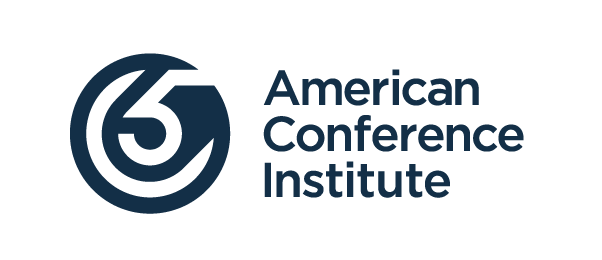
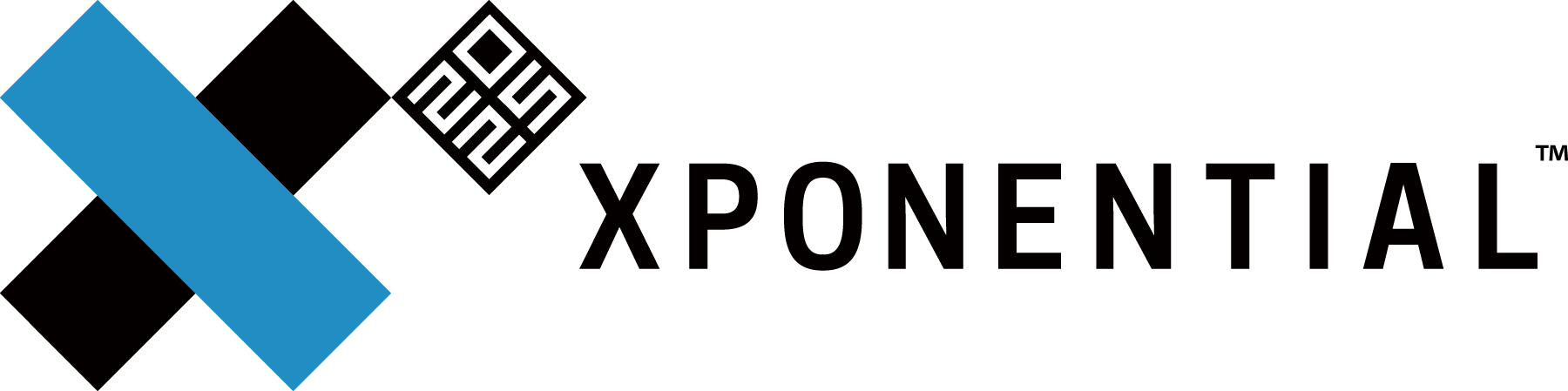
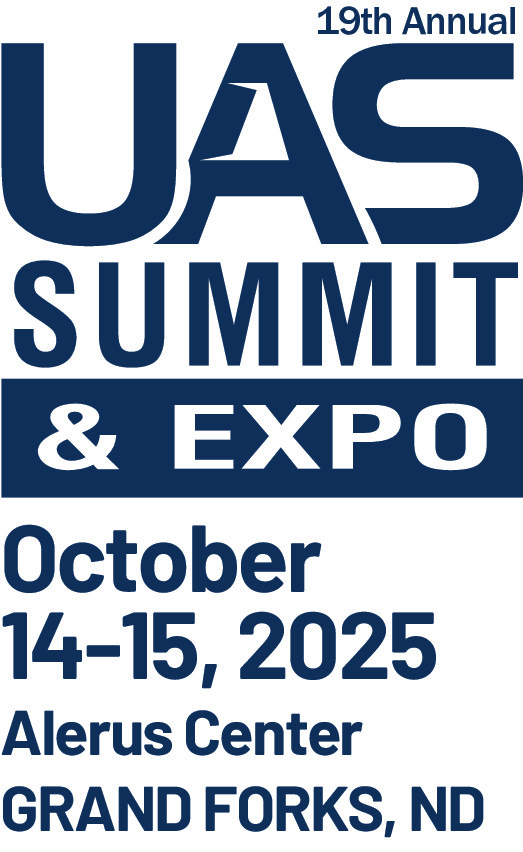
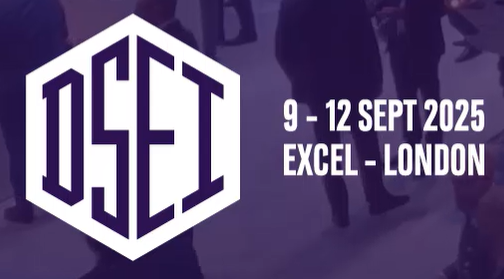
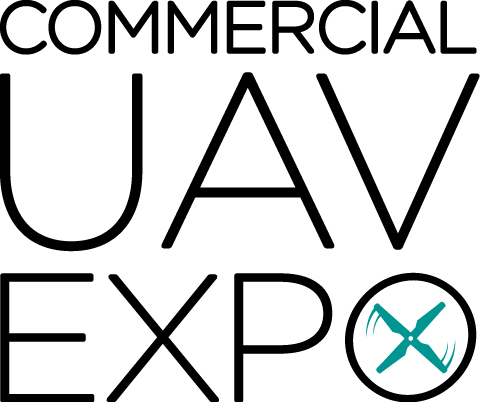
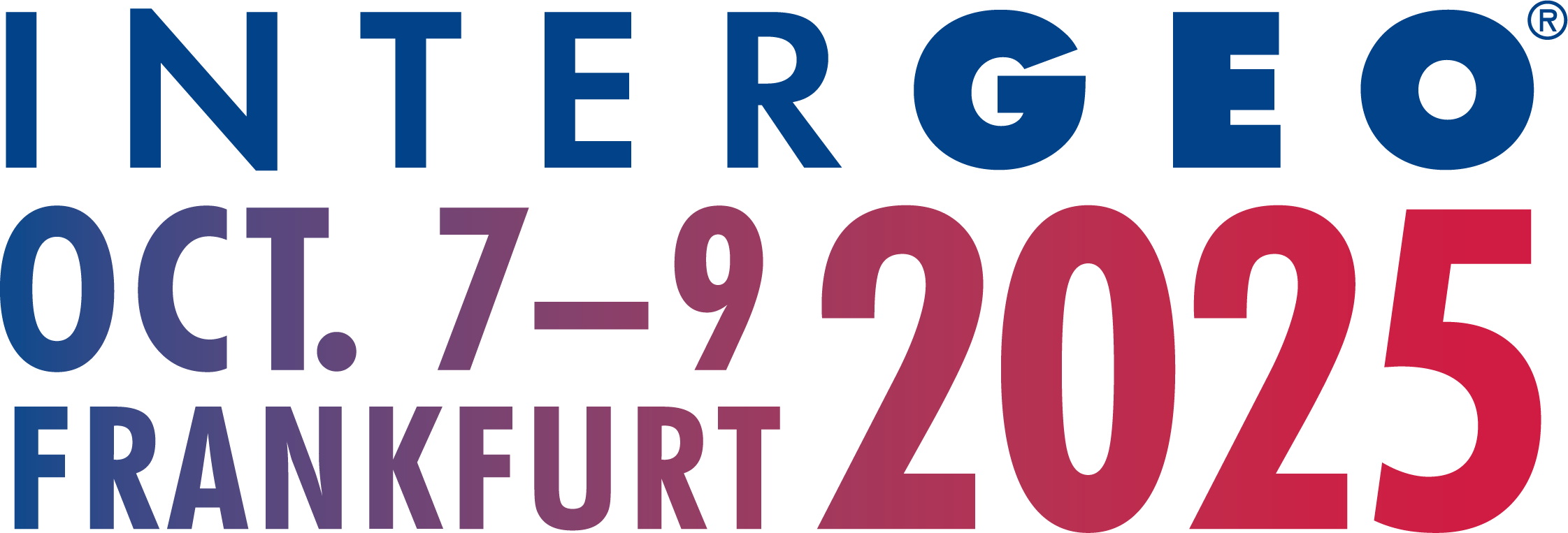
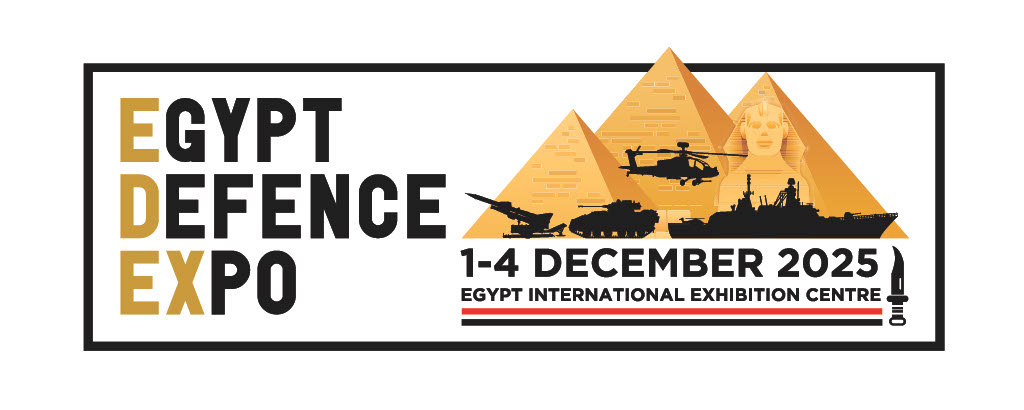
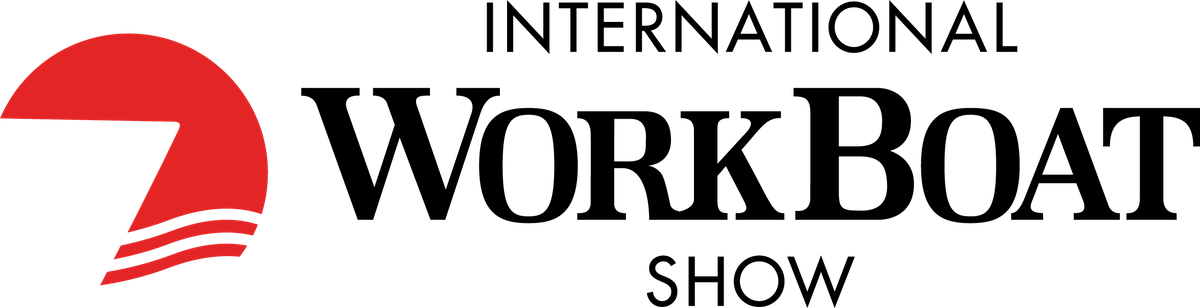
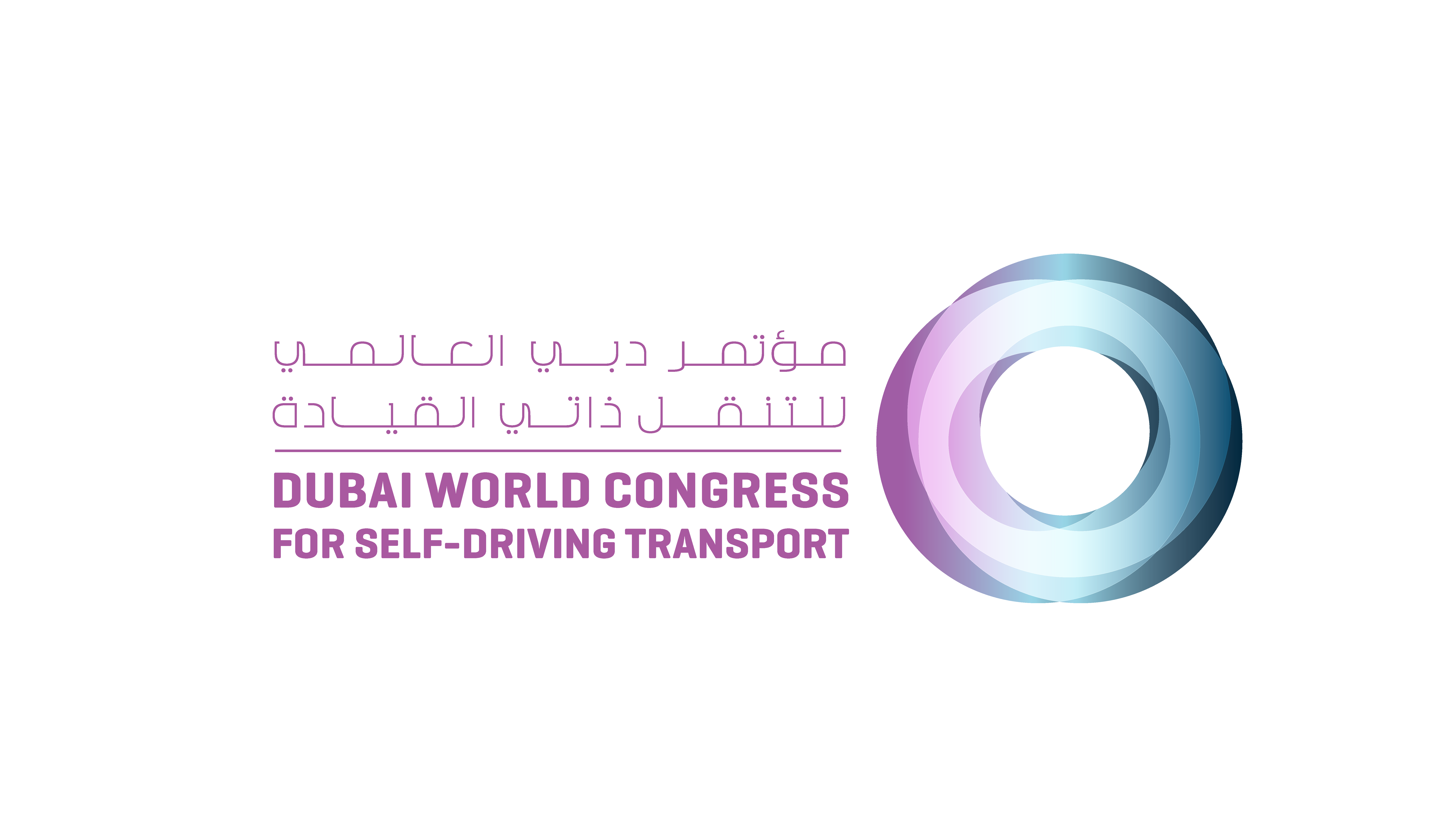
