Ocius Bluebottle USV
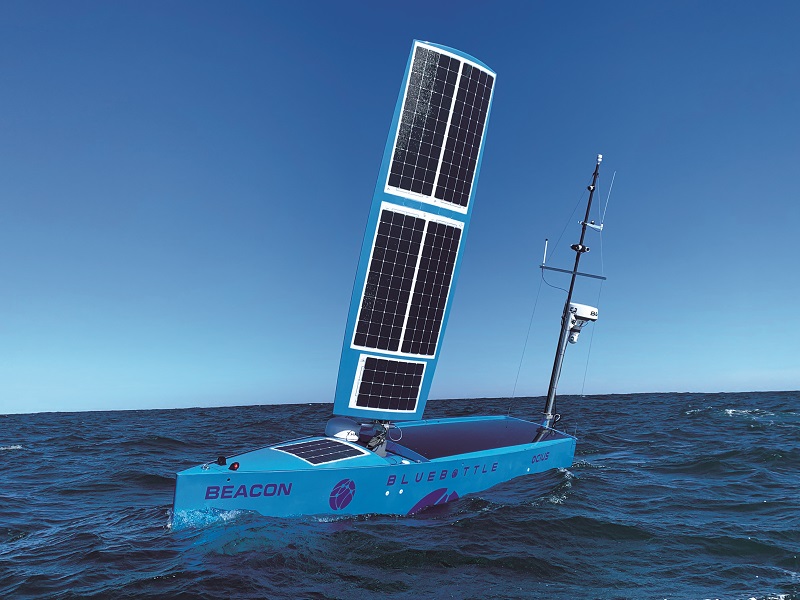
An innovative combination of power sources allows this vessel to provide 24/7 maritime missions. Rory Jackson reports
Round-the-clock patrol
On land, Australia is famed for its range of species and climates, but its coastline is also rich in animal and other resources. Its Exclusive Economic Zone (EEZ) covers about 10 million square kilometres of ocean territory – more area than its 7.69 million square kilometres of land mass, 0.22% of which houses 90% of its population.
Within the EEZ, Australia claims certain sovereign rights to the living and non-living natural resources, from offshore mineral deposits to its growing wind farms industry and the aquatic biodiversity. With such a small population having to care for so much ocean territory, and given the expense and danger of doing so through crewed vessels alone, it was inevitable that autonomous systems would become a huge market on the island continent.
We have previously seen Australian-built platforms such as the C2 Robotics Speartooth LUUV (issue 48, February/March 2023) and the Advanced Navigation Hydrus micro-AUV (issue 43, April/May 2022) attract growing attention. However, the biggest success story so far might be the Bluebottle USV from Ocius Technology.
This is a 6.8 m-long single-hull vessel powered by solar, wind and waves, enabling 150 W for payloads (of which it can hold up to 300 kg) and a theoretically indefinite endurance. The system has been developed by Ocius in partnership with the Royal Australian Navy (RAN), and in June 2023 the navy received its fifth and final Bluebottle as part of a contract worth AU$ 4.9 million.
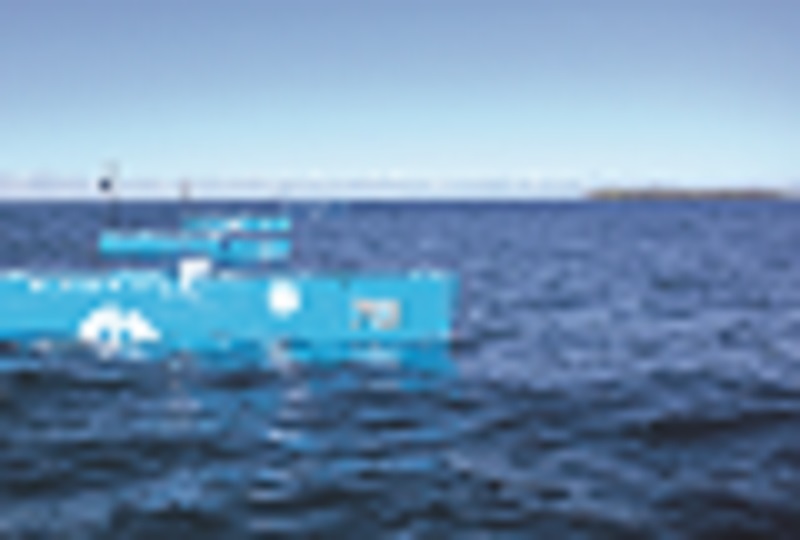
“In addition to the direct manufacturing contract for the RAN, we’ve also been under contract with border forces, as well as a demonstration contract with the Australian Army,” explains Robert Dane, founder and CEO of Ocius Technology. “In that demo, we did 10 days of ISR around an archipelago, with hi-res scans from two USVs informing them on key strategic questions such as where they could or couldn’t land a helicopter.
“Each boat travelled 1000 nautical miles, including the 350 nautical miles to and from the archipelago, without any fossil fuels. The Army told us no crewed boat was capable of that.”
The company also carried out demonstrations earlier this year for Australian marine parks, looking out for Australians fishing illegally in protected waters. Such missions saw a pair of Bluebottles integrating radios so that their operators could talk to the lawbreakers over satcom.
The result of these was a notable reduction in the incidences of illegal fishing, partly because crewed ships are far larger and hence easier to spot over long distances, enabling illegal fishing crews to make an early escape. Bluebottles, by contrast, can lower their sails to hide behind wave heights, and sit undetected for hours recording evidence against the crews.
“We also have a contract with JAMSTEC [the Japan Agency for Marine-Earth Science and Technology],” Dane adds. “We’ve just finished a load of proving with bathymetric equipment for seabed mapping and sub-bottom profiling, and we’re now sending units to a place 800 miles south of Tokyo and 800 miles north of Guam, where there are two active volcanoes.
“They haven’t been surveyed in years because they’re too dangerous for crewed ships. We will survey them for 90 days with 35 m spacing between survey rows, 200-600 m above the seafloor.”
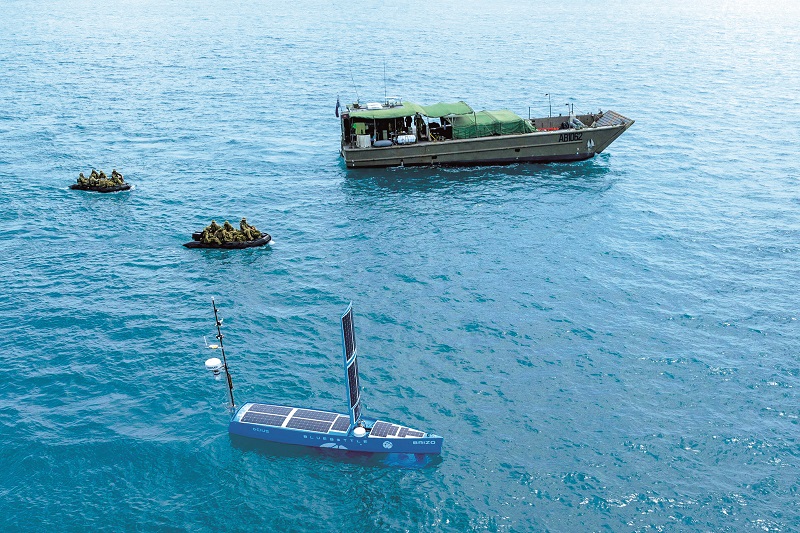
Development history
Named after the jellyfish-like Portuguese man o’ war (which are referred to as ‘bluebottles’ found mainly in the Pacific), the Bluebottle USV has been developed using lessons drawn from Dane’s 25-year background in naval architecture – and, unusually for USVs, with considerable inspiration from the racing world.
“In 1996, I saw a solar boat race in Canberra. The boats all looked like solar racecars, with flat solar tops, and I thought: why wouldn’t they angle their solar panels to face the sun, and use them as sails which could also fold down in a storm or headwind in a seaworthy way?” Dane recounts.
“A year later, a bunch of friends and I entered a boat designed just like that. The judges approved the design, and we won a 60 km race by 30 km, purely because we could angle our solar sail to face the sun or use it to harness the wind and fold it in a headwind.”
Although that design was a catamaran, it was the origin of the Bluebottle concept, and Dane founded his company soon after to pursue its commercial development.
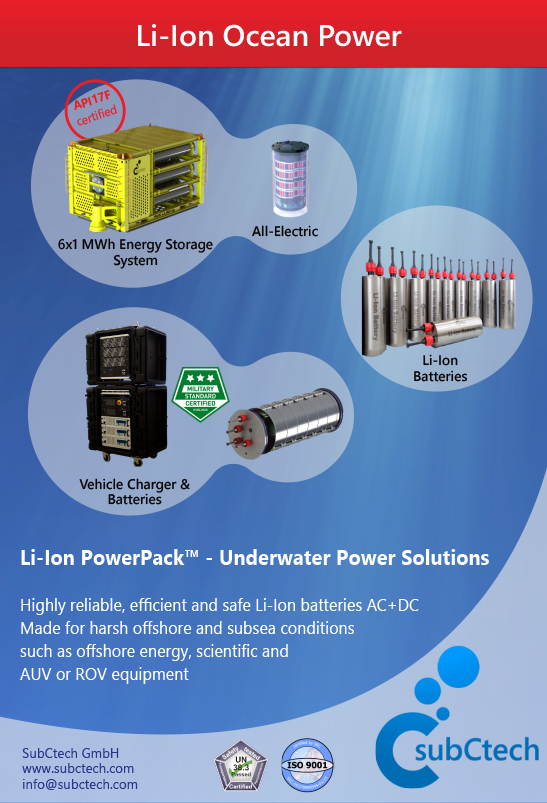
Originally founded as Solar Sailor Holdings in 1999, the company name was changed to Ocius (Latin for ‘fleet’) in 2014. Its headquarters are at the University of New South Wales (UNSW) in Sydney, where most of its r&d takes place.
Soon after founding Solar Sailor, the company worked on a solar and hybrid-electric ferry, initially just for the 2000 Sydney Olympic Games, although by 2013 six had been sold around the world.
Dane notes, “Four of the ferries still run in Hong Kong, from the mainland to a golf course. In 2007, we were asked by people in the US defence community if our tech could be used to build a platform that could go to sea ‘forever’. They asked me a bunch of questions, and I answered each one with, ‘Yeah, we can do that.’ Things like powering it for 10 days at 10 W, having 40 W continuously 24/7, producing kilowatts for a few minutes at peak, it was all achievable.”
Although the defence people eventually opted for another OEM with a diesel-electric design, Dane built a prototype based around the queried specs anyway, a USV about 3 m long named Nemo. It was displayed at conferences in 2013, and drew the attention of Australian defence personnel and Thales Australia. That led to a contract in 2015 to build what would become the first Bluebottle, named Bruce.
During the subsequent years of optimising and maturing the Bluebottle design, Ocius was also contracted by Australia’s Defence Innovation Hub in 2017 to build an intelligent C2 network of persistent USVs. This was key to Ocius choosing its location at UNSW: computer science is a vigorously promoted course and department there, and the company has taken on many of its most valued researchers from it.
Dane adds that from 2020-22, Covid-19 showed that, unlike crewed naval inspection assets, USVs could be launched and operated 24/7 during pandemics, using satellite-based hand-offs of control from one GCS operator to another, regardless of distance.
“We completed a contract to build and demonstrate five next-gen Bluebottles for the armed forces out of Darwin in March 2022,” Dane says. “When border force admirals realised that it had been a demonstration contract and it had finished, the USVs were quickly brought back on board. That culminated in the purchase of five new units, which concluded recently.”
Most recently, in June this year, Ocius signed a AU$2.7 million 12-month contract to operate four Bluebottles for the RAN.
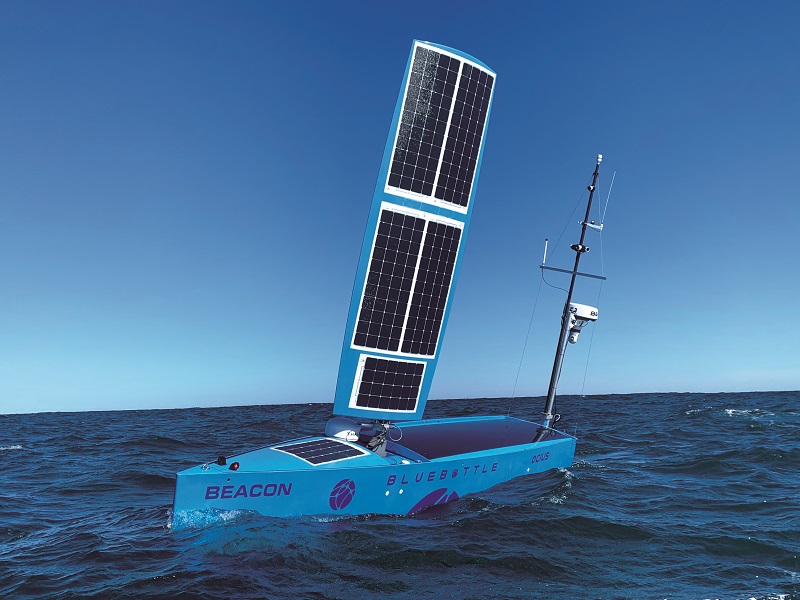
The Bluebottle’s anatomy
The Bluebottle is a single-hull vessel with one sail, both sail and top deck being covered with solar cells. The deck is referred to as a false or solar deck, as the real deck sits under it, directly enclosing the USV’s internal bays, with the top solar deck placed on top separately.
Inside the hull are three compartments. At the front is a mechatronics bay containing the sail and rudder controls, while a 600 litre payload bay sits at the middle and is designated for a customer’s use. In a ‘standard-issue’ Bluebottle this is largely empty, save for a 150 kg winch that drops and displaces water ballast in the keel so as not to change displacement or trim. The payload bay meanwhile can take another 150 kg of dry systems.
“The rudder is at the front and has a flipper on it,” Dane comments. “The flipper is how we harness wave power for propulsion: you point the rudder where you want to go, and the boat heads in that direction. That layout also frees up a lot of space in the aft and separates the mechatronics from the main computers.”
Various systems can be lowered in and out of the water using the winch. For example, Ocius is working with Thales to integrate and test the latter’s thin-line fibre optic towed array on the winch in multiple Bluebottles. This will enable autonomous detection, classification and localisation of any surface or subsurface vehicles emitting or reflecting acoustic noise.
Long range low-frequency underwater comms will also be integrated as part of that project for covert comms from the USVs to underwater allied vehicles or infrastructure.
The third compartment at the aft is an electronics section. It contains seven watertight boxes corresponding to key functions such as the main computer, navigation, power management, control and comms.
These enclosures interface with a rear-mounted mast, where additional payloads such as cameras and radars, as well as other mission-critical systems such as mesh radios or GNSS antennas, are mounted.
“The mast is also easily customised for whatever the user wants,” Dane says. “The boats going to Japan for example will have mast-mounted GNSS, and downward-pointing cameras looking for fluorescence in the water.
“A lot of the Bluebottle is customisable; sensors for example change a lot depending on customer needs and preferences. What tends to stay the same between missions – our real core IP on the USV – are our zero-emissions power and energy systems for long-endurance, highly persistent propulsion that enable it to go on until every autonomous mission is completed.”
The Bluebottle is considered by Ocius to be at a TRL of 9, and is approved by AMSA (the Australian Maritime Safety Authority) to operate unescorted anywhere in Australia’s EEZ. This had enabled it to accrue 23,798 nautical miles of survey distance at the time of writing.
In addition to the five sold to the RAN, the company itself owns seven Bluebottles, using them as demonstrator or contract vehicles in collaboration with prospective customers.
“Over more than 23,000 nautical miles we’ve lost two solar sails, one rudder, lots of flippers, and power to the propeller a few times, but because of redundancy of power from solar, wind or waves, we’ve always been able to stay safe and 99% of the time get ourselves home,” Dane recounts.
In addition to these and the five built and delivered to the RAN, three more were in construction at the time of writing and lined up for work in the defence and oil & gas industries.
One, called Bathy, will be a prototype of a new class with a 5 kW diesel generator in the payload bay and 400 litres of diesel fuel in the keel where the winch would normally go. This will increase the power output available for hydrography so it can use high-end bathymetric echo sounders for seafloor mapping.
Solar power
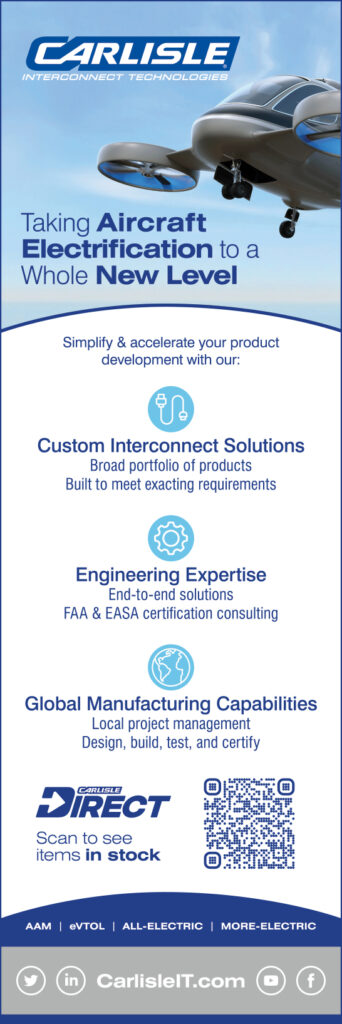
Power supply is a matter of careful balances and trade-offs. Around 120- 150 W is needed to run the Bluebottle 24/7, and if there are 8 hours of sunlight in a day (and propulsion produced using the rudder-flipper and sail rather than the propeller), the solar array will produce 300 W per hour on average. That makes for 150-180 W of surplus power for payloads or for storage in batteries.
“We really only use the propeller in doldrums, for collision avoidance or for quick dashes to catch sight of something like fleeting criminal or biological activity,” Dane adds. “At full battery, we can do 6 knots for 10 hours, but we try to get by on windsailing and flippering at 2-3 knots, saving the excess solar energy gathered during the day to give a constant 150 W to the payload sensors.
“We also try to maximise the solar power throughout the day. For instance, when the sun rises or sets it’s at a low angle, giving the Bluebottle with the sail down only about 80-100 W, but with the solar sail deployed we get 400-
500 W at dawn and dusk. Similarly, if we get strong winds around midday we can lower the sail and flipper straight into the unfavourable winds, using zero throttle but generating 500-700 W.”
The sail is deployed autonomously, using an electromechanical actuator in the forward hull compartment to lift or lower the mast. When not in use, it sits flat on the deck, and has an identical layout of solar cells on the sail as on the deck. “It’s like the wing of a bird – it folds completely away but doesn’t take up any valuable payload space,” says Dane.
Lower decks
Most of the Bluebottle’s solar cells are assembled and provided by Solbian, and are designed around a crystalline silicon semiconductor with a 21.5% solar conversion efficiency. Ocius selected them for their modularity, as well as their proven efficiency in competitive environments – Volvo for example uses them in round-the-world races.
“They’re encapsulated, so we can install them on the decks and the solar sail, and bend them,” Dane observes. “They don’t seem to be affected by salt residue, even though we’re averaging 30-50 days at sea per mission.
“That means there’s been no noticeable reduction in solar power despite the high potential for stains and damage on them, they’ve really been very reliable. Theoretically we could use other suppliers as well – we’ve designed the boat to allow it to take industry-standard solar panel sizes with as little dead space as possible, although the triangular shape of the bow has some wasted space.
“However, a company called Praxis in southern Australia is customising the forward bow deck panels. That will give us about 30% more solar area on the hull. Our engineers aren’t certain we need that, but we’ll try it to see if it enhances our capabilities.”
For storing solar energy, earlier versions of the Bluebottle integrated four batteries of 2.5 kWh each, whereas now the USV’s pack consists of six modules with 3.5 kWh each, for 21 kWh total, and with COTS products typically ordered from various European suppliers.
The hull itself is fibreglass, and is currently carried out by Van Munster Boats, one of Australia’s leading naval architects.
“We’re a displacement boat with no lifting surfaces, and we don’t go faster than hull speed, which is 5.8 knots, Dane says. “Really, weight is our friend, so carbon fibre is of no real benefit to us in terms of the outer hull.
“The advantages of fibreglass, such as its water resistance, cost and other factors win out here. But the solar sail and decks are carbon fibre since those parts need to be lightweight and strong.”
That lightness enables the Bluebottle to be launched and recovered by two people from a standard boat ramp, without a crane or other mechanical infrastructure. Dane notes, “This was born out of necessity: we didn’t have a lot of money in 2015, and not needing a crane has saved us fortunes over the years in operating costs. It also gives Bluebottle customers a low logistics profile.”
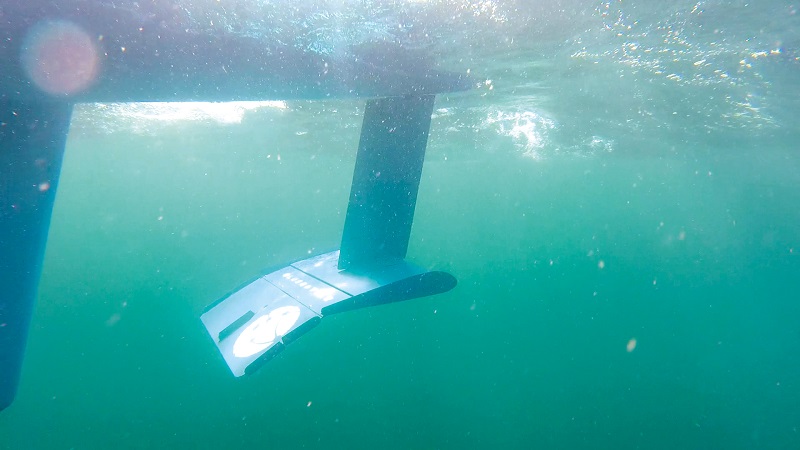
Rudder-flipper
Although the rudder section looks conventional (aside from its location beneath the bow), being a vertically disposed member extending down from the hull, the flipper protrudes as a perpendicular member from the end of the rudder, and resembles the flipper of a cetacean.
As the USV pitches in the ocean waves, the flipper – being made of an undisclosed special flexible material – is deflected relative to the rudder, after which it oscillates in an elastic manner, back towards its original shape.
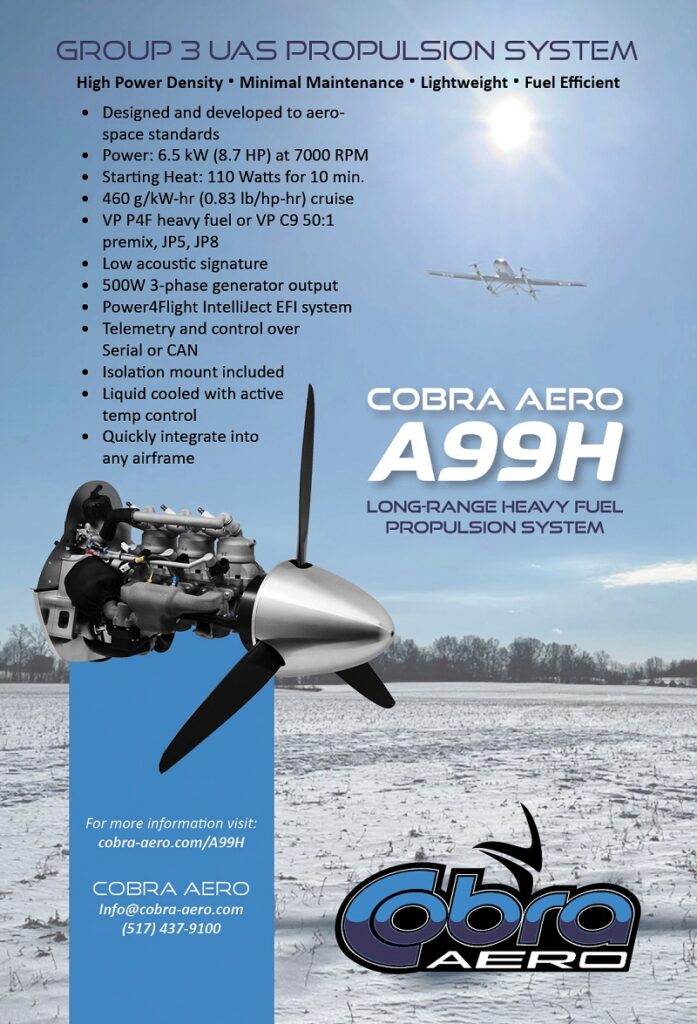
The flipper has been designed such that the speed and motion in which its material oscillates are essentially synchronised to how fast and hard the Bluebottle is pitching in the waves. As the hull heaves up and down, the flipper also waves up and down, propelling the USV forwards as a whale or seal would be propelled by its own flipper.
“Optimising that hasn’t been simple,” Dane says. “In the past we’ve tended to go back and forth on sizes and stiffnesses, but now we have a student doing a PhD on it.
“For the rest of the gear we tend to get naval architect and boat builder advice, and then just put the boats out there until they break. Then we solve what broke, and repeat to see what else breaks.”
Data links
While comms such as payloads and computer electronics are user-defined from mission to mission, some data link systems are preferred by Ocius and are standard issue for the Bluebottle.
“We have a high-bandwidth Certus system and a low-bandwidth IridiumGo – both satcom for BVLOS given our range and endurance capabilities. The high-bandwidth link costs about AU$ 2000 per month, while Iridium’s is about $ 90,” Dane says.
“Then we have radio, wi-fi and 4G cellular systems too, so as soon as we get within mobile phone range we can do high-bandwidth comms fairly easily.”
Ocius has also used mesh radios from Silvus in its networked fleet and war games exercises for the Australian defence services, enabling radios on land systems and UAVs to communicate and coordinate movements with the Bluebottles, as well as relaying HD video and other dense payload data packets back to GCS operators.
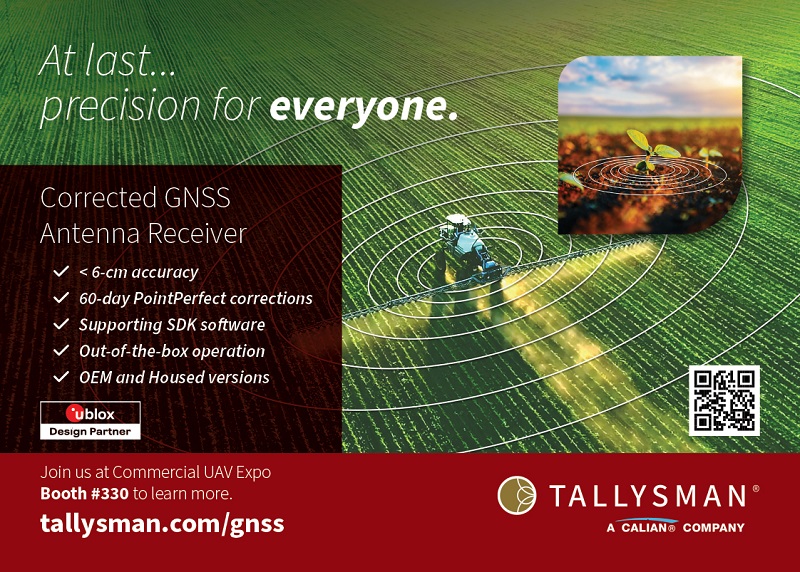
“In most cases though, satcom is what works best for us,” Dane adds. “We’re not trying to do any operations within
20 nautical miles of the coast, we’re aiming to provide capabilities hundreds of nautical miles BVLOS, where users would rather avoid using a crewed ship, as they’re expensive to obtain and operate, and it means unpleasant work and a long time offshore for the crews. Through satcom they can stay onshore and monitor as the USV works.”
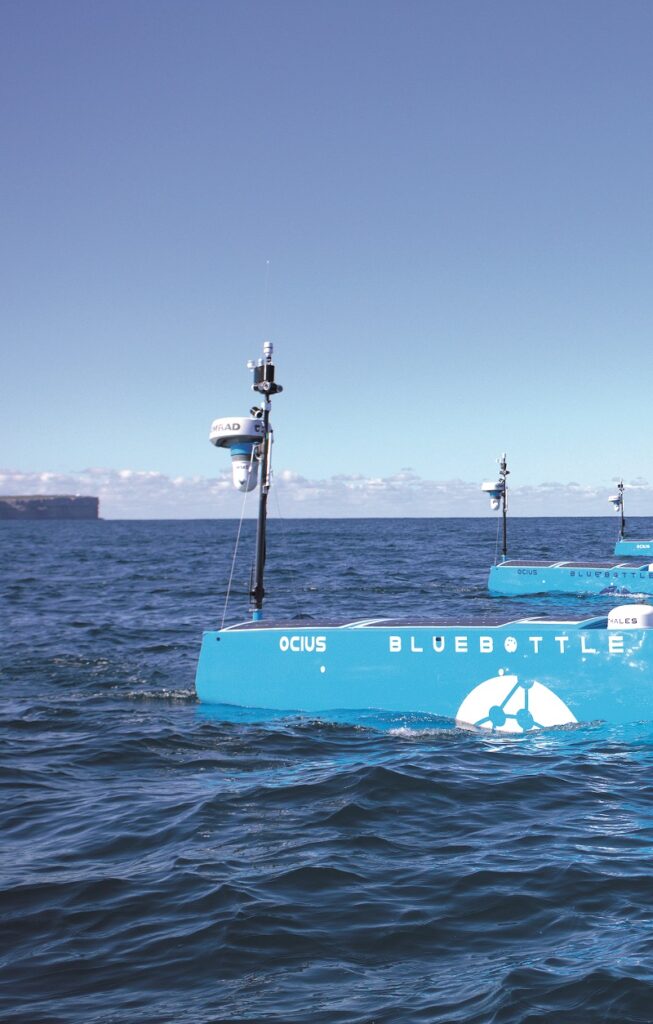
Other projects
In addition to the various projects mentioned, Ocius is also under contract with Australia’s Department of Defence to build an autonomous robotic system for the launch and recovery of UUVs, currently being developed as a solution called the iDrogue.
“We’ve noticed at war game-type exercises involving Bluebottles that when it’s been playing mothership to an AUV, there’s been something lacking in launch and recovery methods,” Dane says.
“Normally a small Bluefin-9 or Remus 100 type AUV for instance is launched by personnel in a RIB who just throw it overboard, but then to recover it they have to physically hoist it out, which is a precarious job. I asked why they didn’t use a net, and they said nets can damage the sensors.
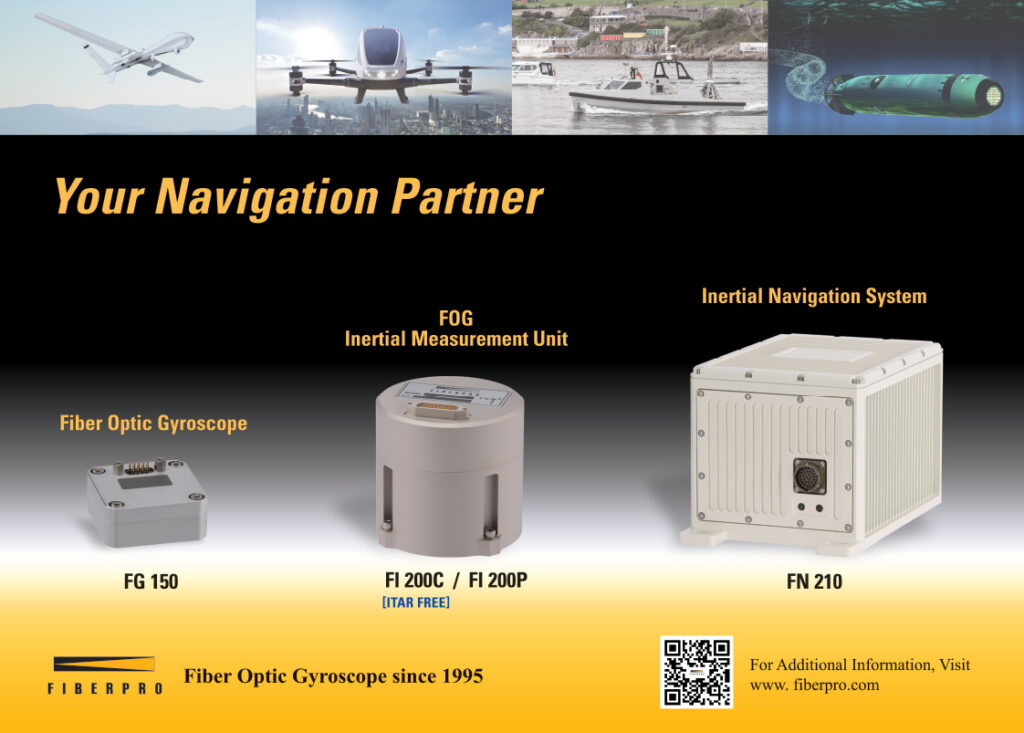
“We then asked why they didn’t use an ROV to capture the AUV while the latter sits stably at a calm depth, instead of when it’s on the surface oscillating up and down with the waves. In a nutshell, that is where the iDrogue came from.”
Although the exact specifications of the iDrogue are undisclosed (it only exists as a first prototype), the concept consists of a boat-launched, tethered system, equipped with sonar, cameras and a means of communication with the AUV, and designed to make it unnecessary to modify AUVs for compatibility with the iDrogue.
Once the iDrogue has identified the AUV using its sensors and comms, it will approach it using eight azimuthing thrusters disposed about a hollow tubular hull (matching the torpedo-like shape of most AUVs).
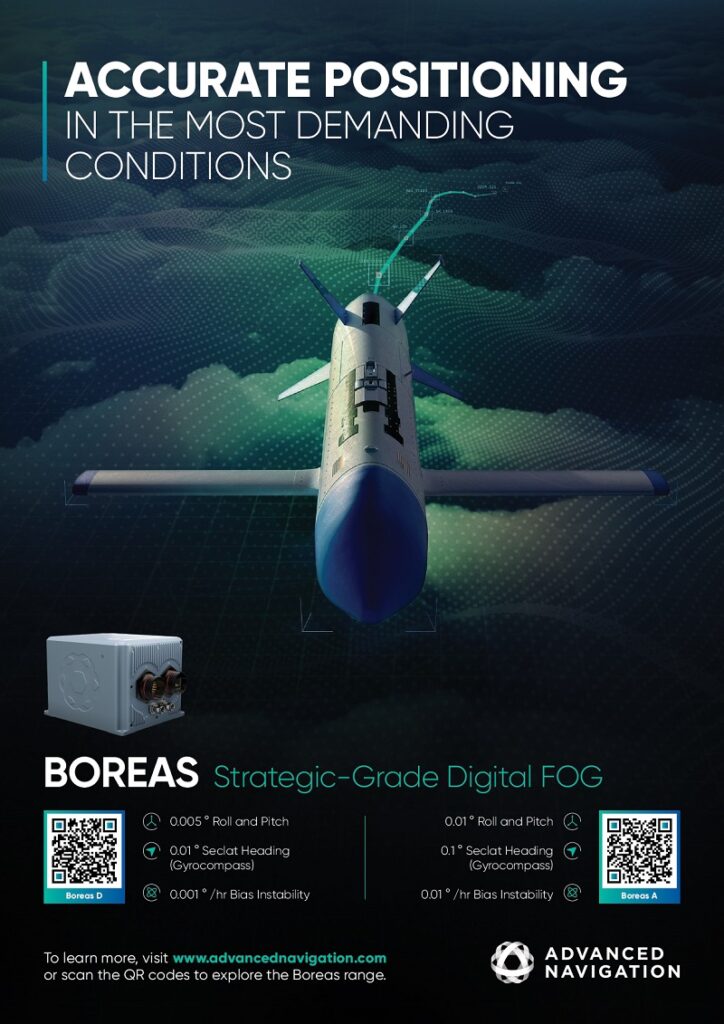
At the front of the hull is an aperture to allow the AUV to enter. Four soft robotic arms made of a flexible housing material can grasp and undulate to first manipulate the AUV into the aperture, then hold it there. The iDrogue hence resembles a squid, moving and recovering an AUV as a squid devours its prey.
Dane says, “I see myself increasingly handing off production and operation of Bluebottles to a separate team, and focusing more on our growing ecosystem of uncrewed systems, like the iDrogue, the Bathy and a newer USV concept we’re nicknaming Shipmate.
“The Shipmate is essentially an 11 m Bluebottle with a range of 125 nautical miles at a speed of 35 knots, carrying 250 kg of payload. It’ll use something other than a solar sail, and we’re now starting to build a scale model. But with rising border tensions around the world, and in particular the war in Ukraine, we’ve been asked about producing a high-speed, over-the-horizon vessel that could also be a ‘sacrificial buddy’ for defence or special forces.
“As a company, we’ve gone from about 10 people in mid-2021 to 45 now, so we’re able to take our technology in more directions simultaneously. It really is an exciting time to be designing and building autonomous systems.”
Specifications
- Bluebottle USV
- Solar-electric
- Length: 6.8 m
- Beam: 1.1 m
- Draft: 1.4 m
- Height above waterline:300 mm to hull, with a varying aft mast height depending on mission, 4m with solar sail
- Height overall: 7 m
- Maximum power output: 3 kW
- Maximum speed: 6 knots
- Operating speed: 2-3 knots
- Onboard energy storage: 21 kWh
- Maximum endurance: Theoretically unlimited
- Propulsion: Combined solar power via propeller, wind via sail and wave via rudder flipper; exact combination depends on local conditions
- Payload capacity: 600 kg
Some key suppliers
- Design: 123 Design
- Construction: Van Munster Boats
- Solar cells: Solbian and Praxis
- High-bandwidth satcom: Certus
- Low-bandwidth satcom: Iridium
- Mesh radios: Silvus
- Sonar array: Thales Australia
UPCOMING EVENTS
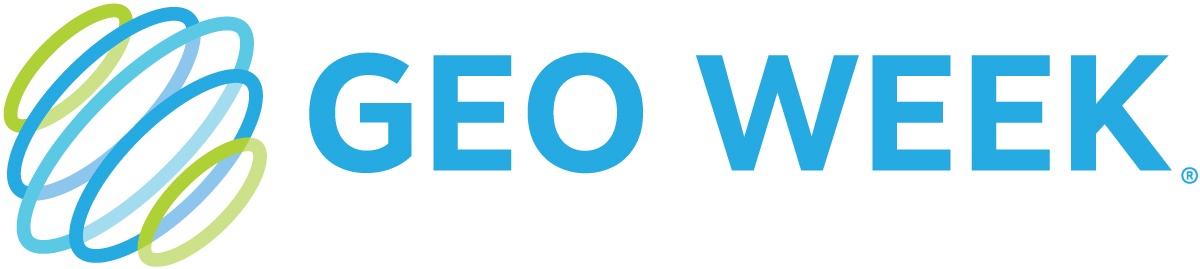
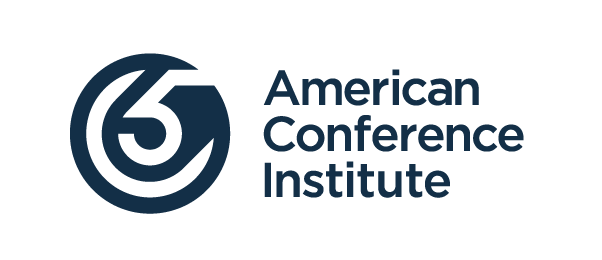
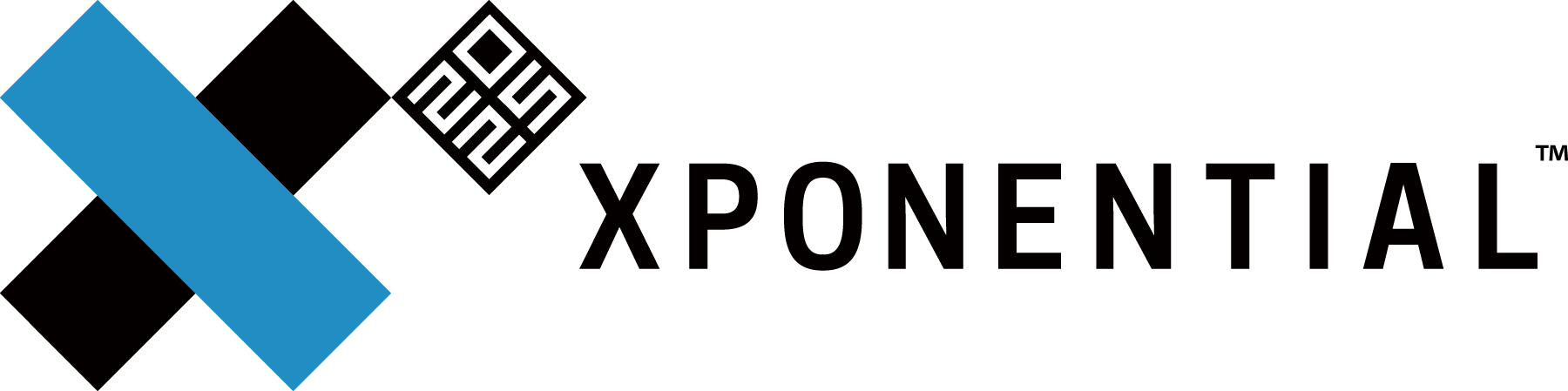
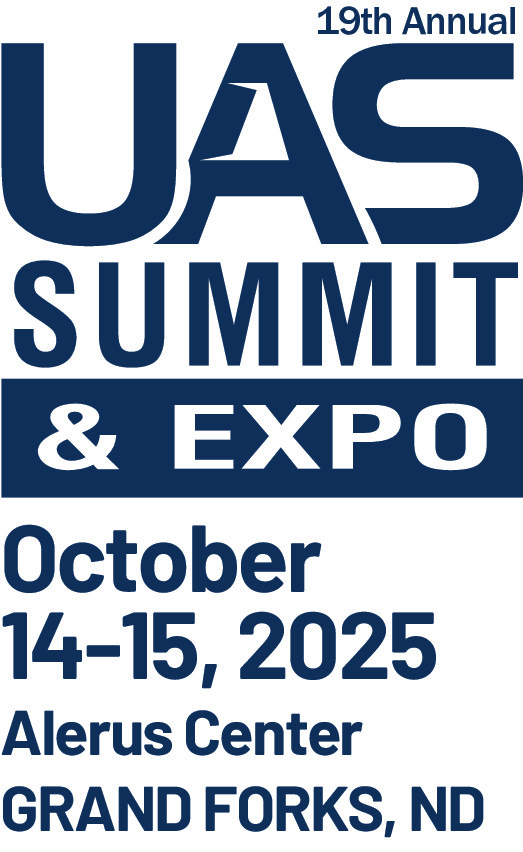
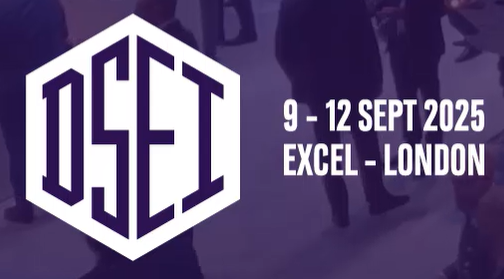
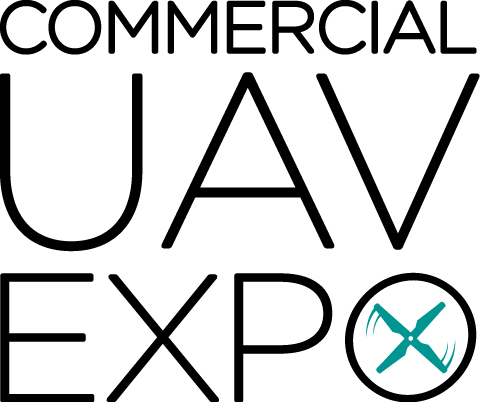
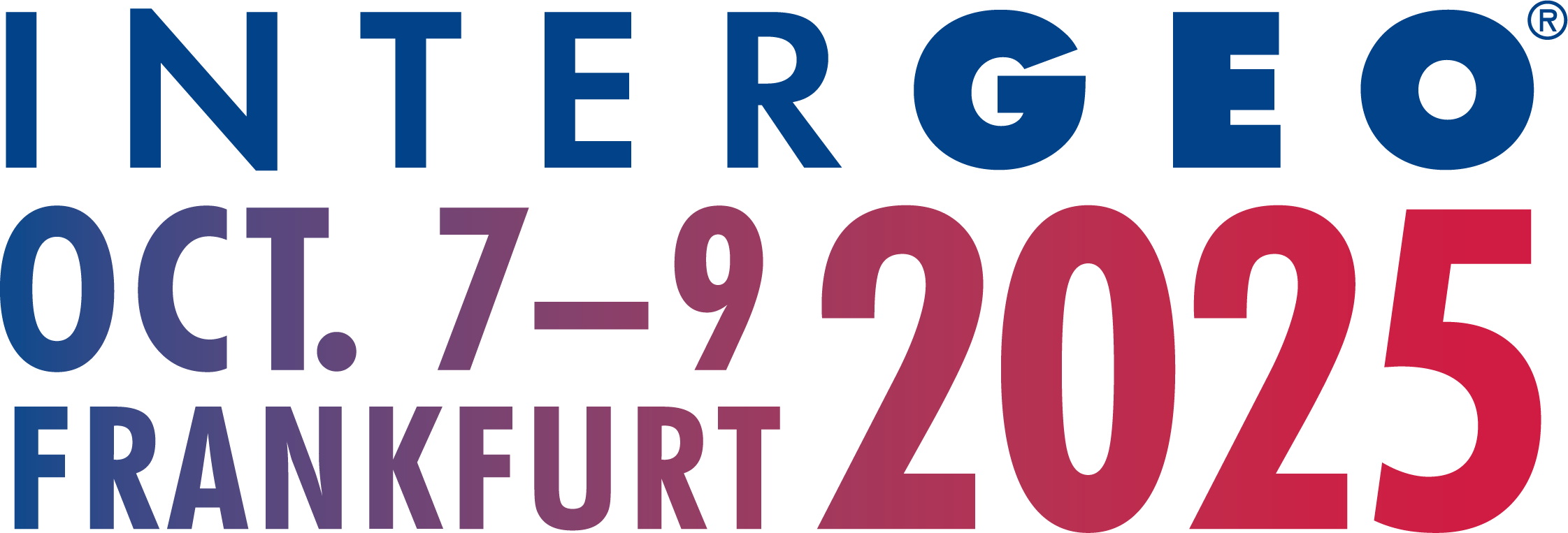
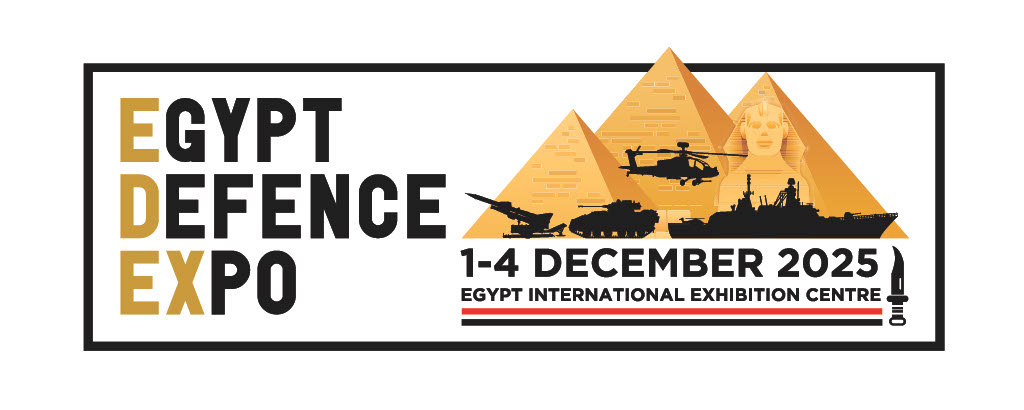
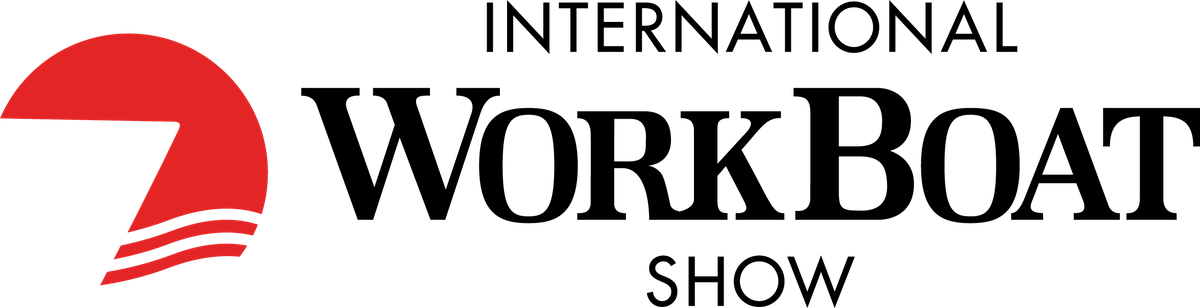
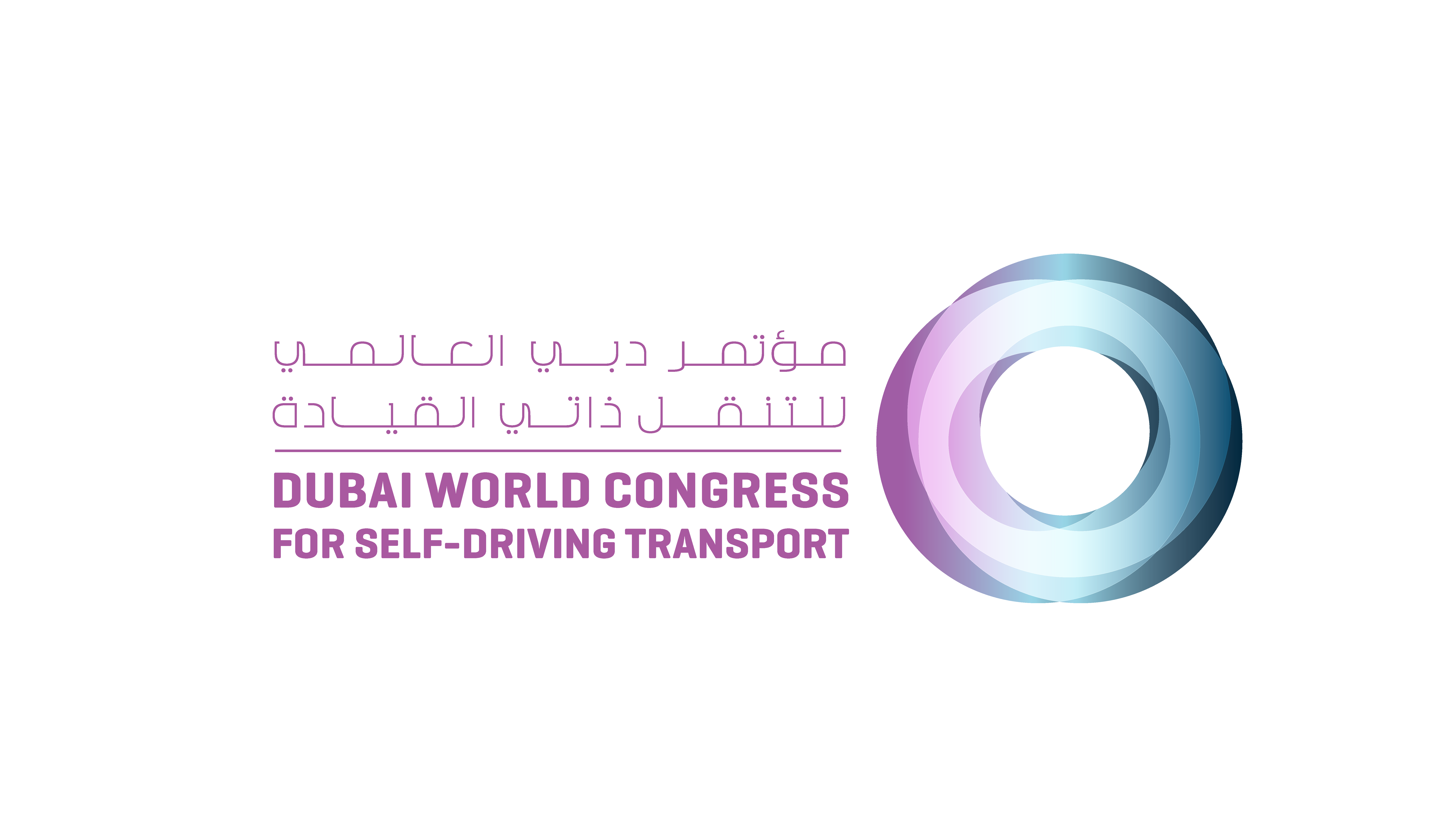
