Alpha-Otto REV Force
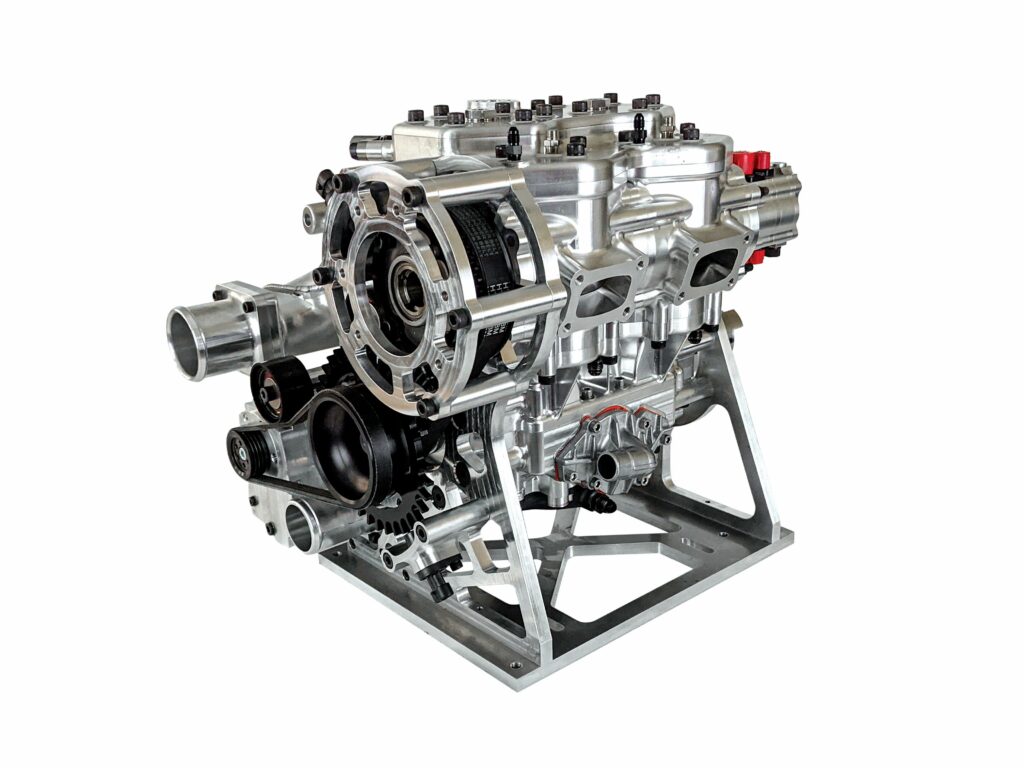
and more without necessitating hardware changes between fuel switches
(All images courtesy of Alpha-Otto Technologies)
Multi-fuel futures
Rory Jackson unpacks a company’s take on low-temperature combustion, through which it is achieving high-efficiency, low-emission operation on a wide range of fuels
We featured Michigan-based Strange Development in 2020 (see Issue 33), for its two-stroke, inline, two-cylinder, spark-ignited REVolution engine, integrating a rotary exhaust valve (REV) to leverage forced induction when adjusting its dynamic compression ratio.
Since then, the company has continued to operate as a multidisciplinary engineering services house, although ongoing development of its engine technology and REV-based operating cycle (now patented) was moved under a new company, Alpha-Otto Technologies, in 2022. Both Strange Development and Alpha-Otto Technologies are creations of John Krzeminski (CEO of the former and CTO of the latter), as is the newest version of REVolution, styled REV Force.
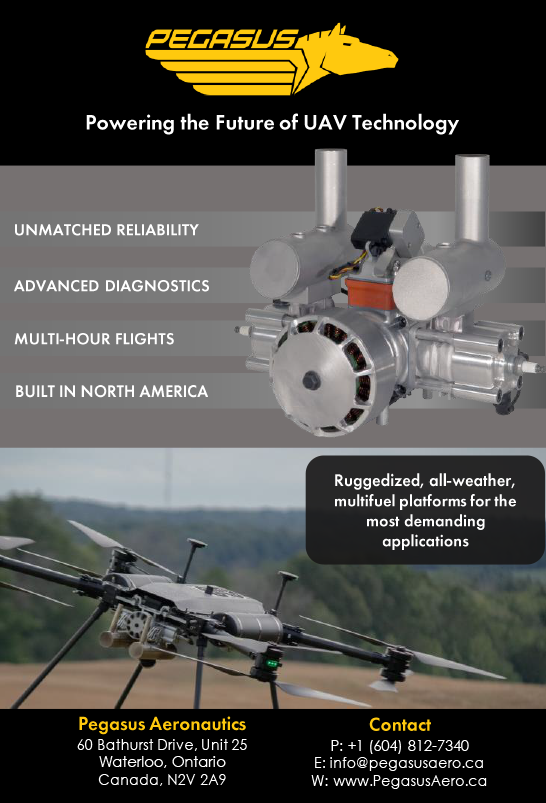
The REV Force remains a spark-ignited, inline, two-cylinder, two-stroke engine with port injection and liquid cooling, today weighing 48 kg and outputting 127 kW (as either shaft power or electric power, thanks to new electric motor-generator integrations), with an expected TBO of 2000 hours – double its predecessor’s lifecycle.
Still integrating its exhaust valve-based cycle, five years of r&d have seen the engine reconfigured with a number of innovations, particularly (but not exclusively) about its ancillaries, which have enabled combustion with a greatly broadened range of fuel, including heavy fuels, biofuels and hydrogen. These include a variable forced induction system (which spurred the engine’s renaming), direct injection (DI), and new approaches to combustion, ignition and engine management.
All of these are largely encompassed under what Alpha-Otto terms its “low-temperature combustion” (LTC) process. LTC generally refers to techniques aimed at achieving so homogeneous a mixture of air and fuel within the combustion chamber that it may auto-ignite (spontaneous ignition without needing a spark or flame) at a lower temperature than is conventionally required.
This would unlock leaner combustions, with reduced and uniform heat distribution throughout the cylinders, and hence lower heat-transfer losses (than in engines burning conventional stoichiometric fuel/air mixtures). That means higher thermal efficiencies, and considerably reduced NOx and soot emissions for such engines.
“In expanded terms, LTC is more efficient than conventional combustion because you’re just losing less heat to everything. Look at a typical thermal map of an engine cycle and you see 55-70% or more of your combustion heat going out of your exhaust,” Krzeminski says.
Naturally, if a greater proportion of the heat from combustion can be contained within the expansion of the combustion gases, less of that heat is lost through exhaust, transfer into the coolant, the metal engine components and so on.
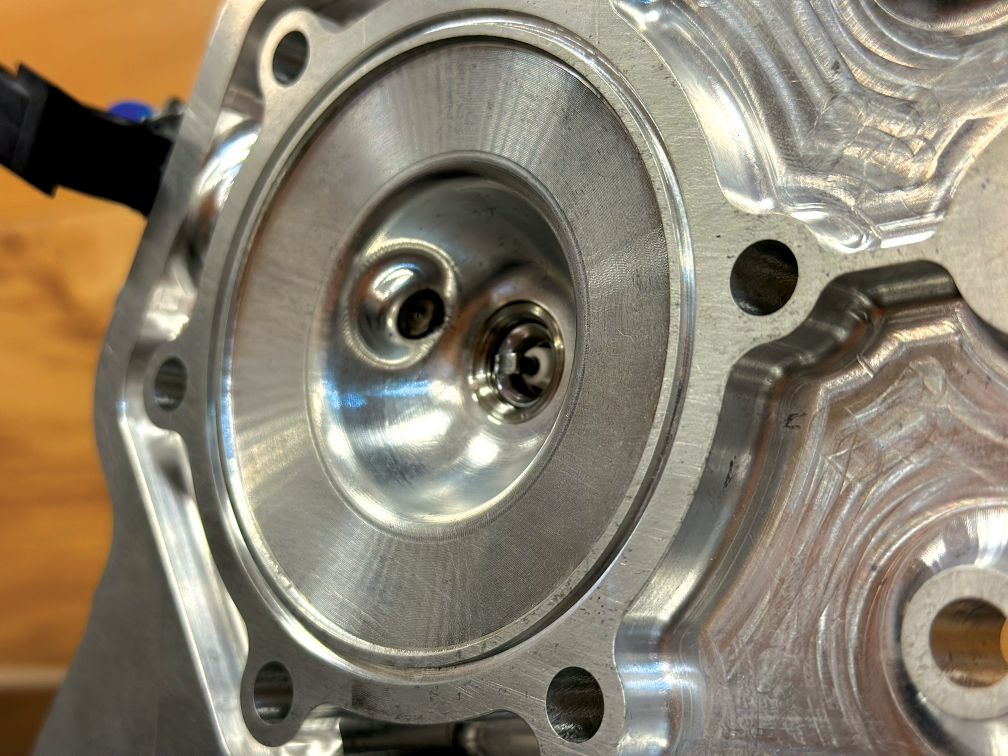
Combustion modes are a defining factor in this: compression-ignition (CI) engines typically achieve about 30-45% in thermal efficiency indexes. Spark-ignition (SI) engines conventionally operate at between 20% and 40% thermal efficiency.
As Krzeminski explains: “There’s two ways to get thermal efficiencies close to 60%. First, Formula One engines ignite their fuel/air mix in a prechamber before jetting out across their combustion chamber, achieving borderline CI-type combustion in a SI engine, with near spontaneous or auto-ignition of that fuel/air mixture – with inherently no need for a flame front to move across the stroke, like in a typical SI engine.
“The Formula One way is an excellent method. I honestly have no criticisms of it, and we take a little bit of inspiration from it for our spark-assisted tech. But the Holy Grail is something like homogeneous charge compression ignition [HCCI]. Our LTC is somewhat akin to HCCI-type operations, and what you’re trying to achieve in both is ‘diffused combustion’ in which combustion happens almost instantaneously across the whole combustion chamber.
“That means near-constant volume ignition, with pressure going up exponentially, and without the combustion gases specifically expanding across the space created as the piston thrusts down.”
If achieved, diffused combustion adds dramatic thermal and mechanical efficiency to an engine, but LTC has historically posed a number of optimisation challenges, such as optimising for the correct high levels of exhaust gas recirculation (EGR) for variable valve timing and ignition delay, or for the formation of a dilute cylinder charge with homogeneity across bore and stroke.
Several modes of LTC have been proposed and researched over the last decade, including the aforementioned HCCI, as well as premixed charge CI (PCCI), partially premixed LTC (PPLTC) and reactivity controlled CI (RCCI).
Alpha-Otto’s approach has come about as a result of r&d into areas not strictly related to UAV engines, although its technology comes to us with the company having identified that its newest offerings – in LTC, efficient multi-fuel operations, and hybridisation – bear watching for people seeking high-power output and high-efficiency UAV operations amid insecurity over which fuels ICEs may need to run on in the future, be it in defence, commercial or civil applications.
Stages of Alpha-Otto’s LTC
While the two-cylinder engine block looks unchanged from its form five years ago (and the core principle of using a rotating valve at the exhaust port end to trap supercharged air and boost engine power is still there), its ancillaries have been revamped considerably, with the new LTC operating principles broadly stemming from a close interaction between them.
“The pumping work of this engine is separate from the power cell. Upstream, our air preconditioning and induction system controls the air going into the engine. Downstream, our scavenging and exhaust control system controls the air leaving the engine – with the REV component being a critical part of the latter,” Krzeminski tells us.
“Depending on how exactly we want to fill or evacuate the combustion chamber, we can control for the ΔP [delta P] across that chamber, based on how we control the ways those upstream and downstream systems work together. We can increase the gas pressures upstream or downstream, and control their flow rates as they pass through the combustion chamber.
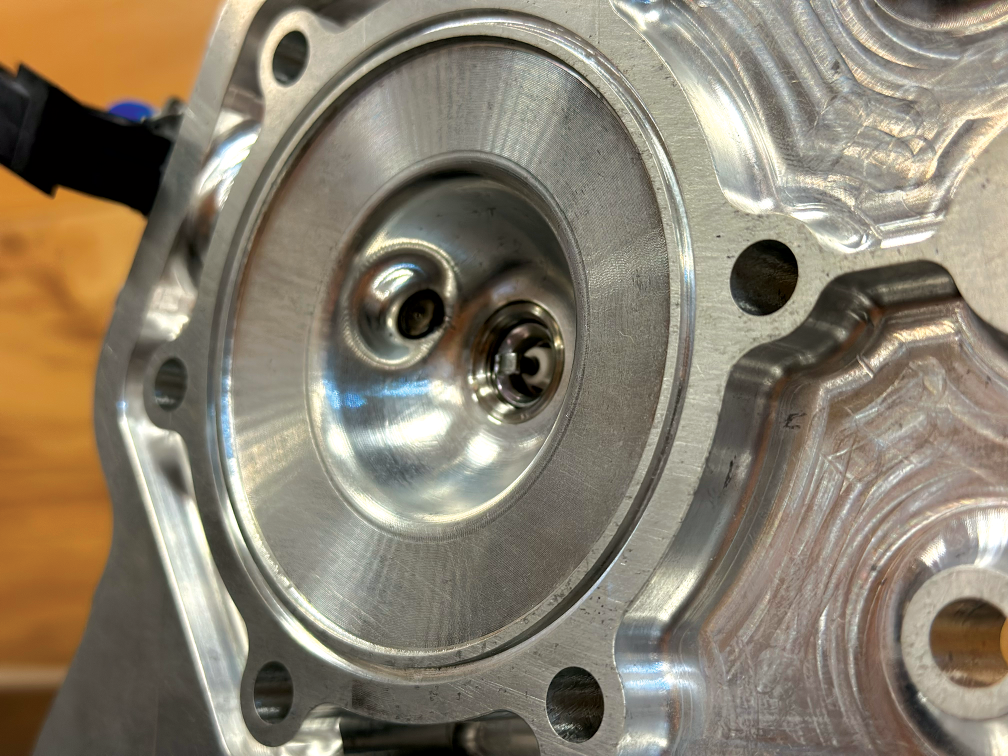
“But it is important to note that those two systems – and hence our solution and LTC mode – could never work without the two of them, and how we’ve very carefully tuned them to interact perfectly over the last five years. Having exhaust control without pressure from upstream, or having upstream pressure without the ability to trap the added intake air in the combustion chamber, just doesn’t work. We have both, and it’s taken a lot of CFD and ECU work to get it right.”
An understanding of the latest technologies defining this engine is best achieved through the lens of its LTC process. This consists of five stages (chronologically and in terms of the related engine parts), with the aforementioned air preconditioning and induction system naturally coming first, so as to precisely regulate intake air temperature and pressure in a way that achieves Alpha-Otto’s desired dynamic compression ratio and conditions ideal for homogenous, diffused combustion.
Then, a turbulent but sustained charge motion in the combustion chamber further hones those conditions and enables a thorough fuel/air mixing, as well as stabilising the subsequent combustion with a lean mixture and uniform diffusion.
The injection of fuel that follows is precisely timed, angled and quantified to prevent premature ignition (this objective being aided through deliberate cooling of the chamber, enabled by the intake and exhaust systems mentioned earlier) and optimise the subsequent combustion.
Here, a DI system enables knock-sensitive fuels such as kerosene and hydrogen to enter the cooled chamber after the ports have closed, again reducing pre-ignition risks, and this aids efficient, homogenous fuel/air mixing (although Alpha-Otto admits its port injection yields such positive and consistent LTC results that DI may not be necessary).

Diffused combustion may then occur via auto-ignition, or through what the company calls “spark-assisted ignition” in the event of poor fuel quality, which interferes with the process.
Then, as mentioned, a scavenging process managed using the REV – responsible for trapping the intake air to increase dynamic compression earlier in the operating cycle – enables precise exhaust flow and internal EGR to optimise the exchange of gases inside the cylinders, controlling residuals and conditions in the chambers for the next cycle to keep peak combustion temperatures low. Each of these five steps in Alpha-Otto’s LTC cycle will be explored and detailed below.
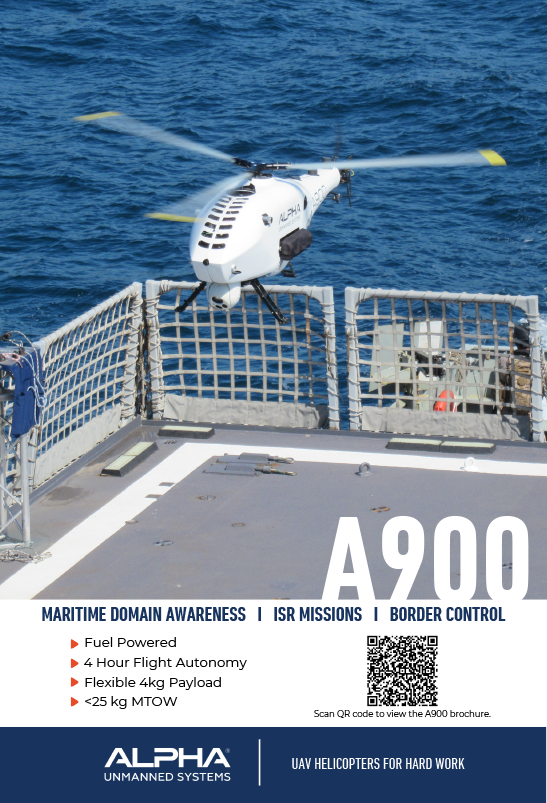
“These are all part of the same overall process, and we had the REV and supercharged induction on our last engine in 2020. But, since then, while correlating our engine to Gamma’s GT-Power 1D simulation software and also performing tests using kerosenes, we started gauging heat release and losses against different phasings of the exhaust valve, and discovered we could achieve this combustion mode at low temperatures precisely because of our unique intake and exhaust, with adjustments for the added three stages in between,” Krzeminski explains.
Forced, variable induction
Air first enters the REV Force’s intake manifold through an initial throttle valve, beyond which is a passage into the cylinders’ intake ports. That passage runs into a belt-driven supercharger, which compresses the air and blows it through a heat exchanger, which can function as an intercooler or a heater.
Downstream of the heat exchanger is a secondary bypass valve, which can redirect the supercharged and conditioned air back to the throttle to control or meter (with quick response) how much of the preconditioned air reaches the combustion chamber, and how much gets cycled and fed back into the compressor.
“With this arrangement acting as the engine’s forced, variable air pump, rather than relying on the piston, we can precisely control the volume and flow of air into the combustion chamber.
“For instance, we can reduce the air’s density by heating it up greatly and putting it under low pressure, so if you’re idling or otherwise need more efficiency, we can really increase the volume of air going into the cylinder, separately from an increase in mass,” Krzeminski says.
“This enables us to tailor the properties of the intake air for maximising thermal efficiency, or peak power or continuous power, without needing to change the hardware. It also means we can pre-heat or pre-cool the air, and increase or decrease the dynamic compression ratio, as is optimal for each of the different fuels or conditions we want to fly.
“To run in high efficiency with hydrogen, we heat the air to between 100 C and 200 C, or to fly efficiently with altitude compensation we still might heat the air, but focus more just on increasing pressure to compensate for the ambient air density drop. We have tested REV Force successfully on both kerosenes and hydrogen, and sustained thermal efficiency results of 42-52%.”
Achieving such fuel and environmental versatility depends not just on this air preconditioning in and of itself (with successful tests of REV Force running on both kerosene and hydrogen), but also highly optimised control strategies within the ECU to account for the different mechanisms at play.
Air can be warmed either by the heater (with EGR, or with liquid coolant running from the exhaust ports and cylinder heads) or by compressing it; throttling upstream of the supercharger inherently puts the compressor at a low flow rate with a high ΔP, creating immense heat.
“When we’re looking to go into a high-efficiency mode quickly, relying on the transient response of a coolant system alone to pump heat around the engine can mean you’re not getting heat to the combustion chamber fast enough. Our preconditioning system allows us to create a lot of heated or pressurised air quickly, and the bypass system means we can quickly dial back and recondition whatever kind we’ve been sending,” Krzeminski says.
As well as devising this air preconditioning approach since 2020 (complementary to the pre-existing REV-based scavenging and exhaust control system, and for its planned multi-fuel strategy), Alpha-Otto has engaged in CFD optimisations of its intake manifold’s internal geometry, after finding a slight bias of turbulence favouring the rear cylinder over the front cylinder through testing.
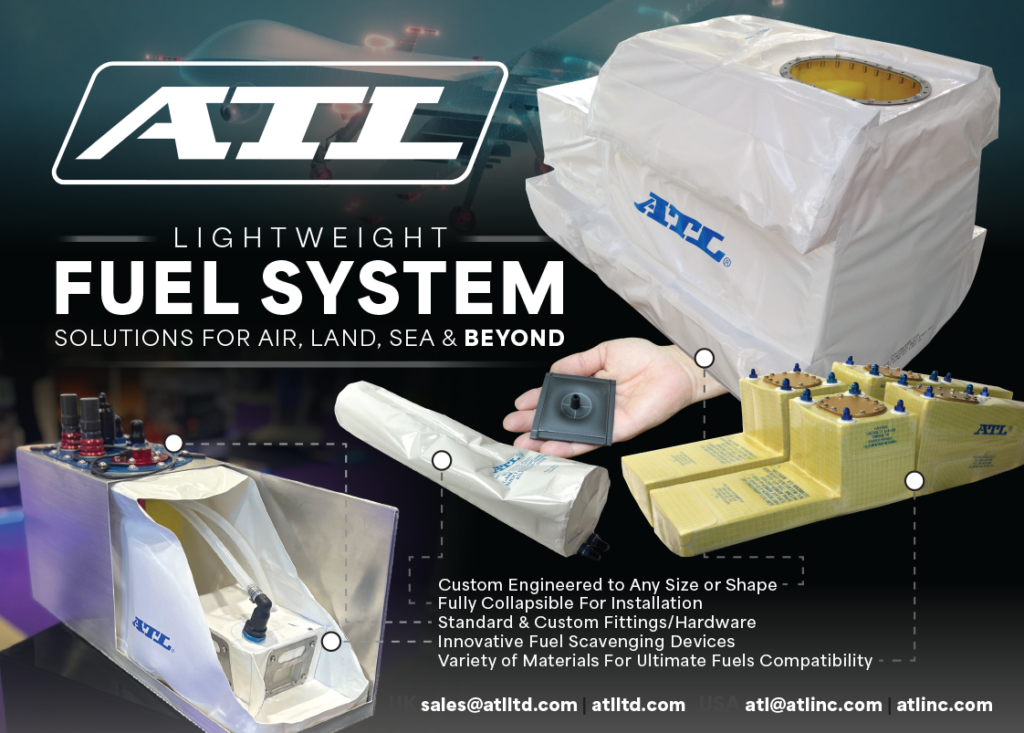
Additionally, as we reported five years ago, Strange Development went from a centrifugal supercharger to a Roots-style supercharger to improve intake pressure at low and idle speeds, particularly for starting power. But, more recently, Alpha-Otto has switched to a screw-type device from Sprintex Superchargers.
That has helped to greatly optimise for ΔP across the air preconditioning system at low rpm conditions, thanks to the manner in which it compresses air internally, and the fact that it can alter the volume and pressure of air passing through it, thereby also generating heat (none of which a Roots blower does).
“People talk about Roots blowers being the most efficient positive displacement devices because you compress after the supercharger and then don’t create heat, especially if you have a bypass valve, but we often actually want that heat, so it’s valuable to us to have a compressor that acts as a secondary heat source,” says Krzeminski.
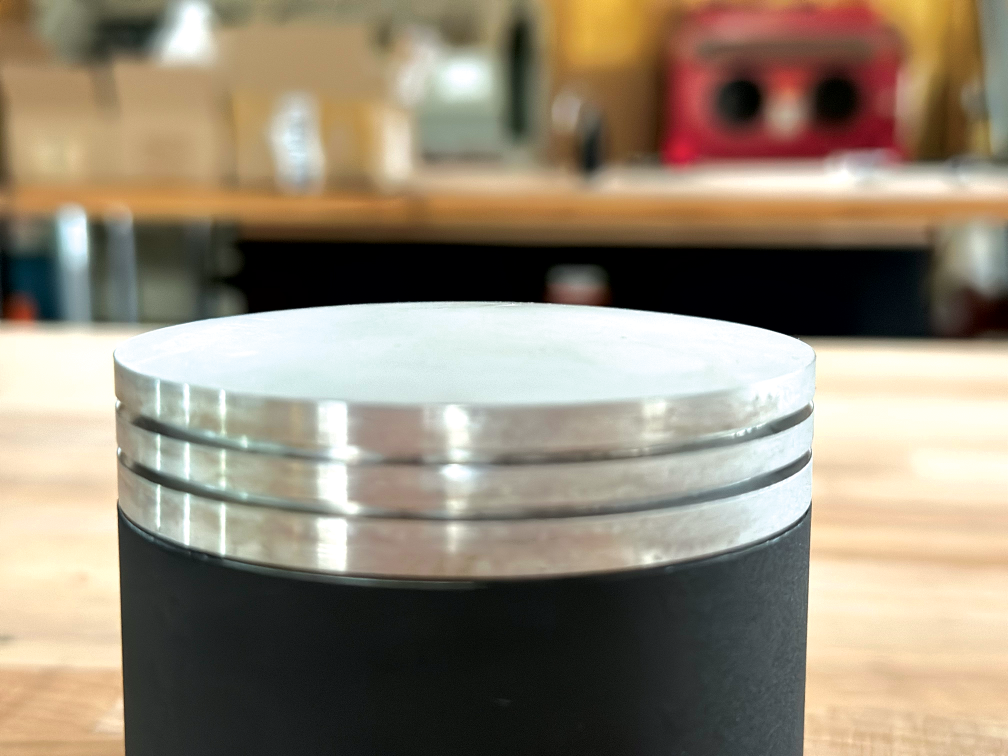
The domed-pistoncrown shape helps deflect intake air in a way that aids turbulence and charge motion in the REV Force’s cylinder
“Although right now the supercharger is oiled from its own sump, we are planning on integrating it with our own oiling system to have everything work more tightly together. We’re also planning to test the overall engine with both this supercharger and a turbocharger as well.
“The supercharger is belt-driven, but to offer a high-efficiency mode we really want to be able to dispense with that parasitic loss, so a turbo would enable us to unload the supercharger and maintain a desired compression without shaft efficiency suffering.”
Turbulent charge motion
Charge motion refers to the quantity of kinetic energy in the air at the desired moment of ignition, and it is a key contributor to both flame propagation in spark-ignited engines, and the chance of successful auto-ignition and diffused combustion, given a homogenous fuel/air mixture across the combustion chamber.
“It can be hard to get good charge motion in a four-stroke because they pull in air as the piston goes from TDC to BDC and back again, and the air slows as it flows around the poppet valves and fills up the chamber, unlike in a two-stroke cycle, where the motion induced by the scavenging and the open ports ensures relatively high turbulence and hence charge motion,” Krzeminski says.
“Our supercharger pumps air in, and the internal geometry we’ve engineered means we’re directing air into the chamber with the exact angle needed to create as much charge motion as possible before immediately compressing it with the piston and igniting it. While a four-stroke goes through a full, 360° crank rotation to draw in air, we are getting all of our air in just less than 180°.
“That first maximises and then preserves the kinetic energy of the air, because our intake port isn’t fully opened until our piston is at BDC. It starts to move back up right after air starts entering the cylinder and then we ignite before TDC.”
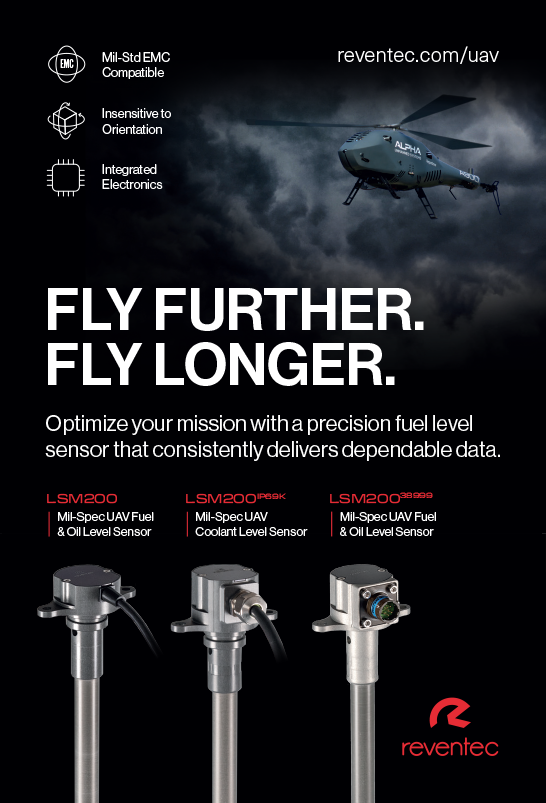
This quality is critical for achieving a homogeneous mixture of air with almost any fuel, and it is especially crucial to how the REV Force runs smoothly on hydrogen and JP-8. These are two of the most knock-sensitive fuels that Alpha-Otto’s target customers wish to use, and knocking occurs primarily as a function of hotspots forming in the cylinder.
By keeping the air moving before ignition, the engine achieves not only a uniform distribution of fuel and air across the combustion chamber, but also a uniform temperature spread. Hence, hotspots cannot form and knocking is not initiated.
There are a few critical aspects of Alpha-Otto’s engineering that are key to how it achieves a turbulent charge motion. One is the previously discussed air preconditioning, by which air pressure, volume, temperature and velocities are optimised to maximise turbulence, so controlling the interplay between the air and fuel at hand.
The next aspect concerns the geometry of how the intake ports are oriented into the combustion chamber, and Krzeminski describes this as being the most important contributor.
While traditional transfer ports are forgone due to the absence of crankcase scavenging, each cylinder’s air inlet nonetheless starts on one side of the block and then splits into two pathways that wrap around the cylinder, running in opposite directions, each one entering the cylinder at the opposite side to the air inlet.
“As well as that wraparound motion, the ramp and the angle created inside the intake port are really critical, not just for creating charge motion but also for mixing fuel and air by forcing the air up into the top of the combustion chamber, so it then splashes out and down,” he explains.
“We have also redesigned all our port openings with something of a bellmouth shape, which naturally helps the gas ‘grab’ the sides of the walls, resulting in a perfect laminar flow with no pressure drop along the way, unlike a straight pipe, which tends to result in a low pressure drop and struggles to preserve kinetic energy of the gases.”
Another vital geometric factor comes from Alpha-Otto’s piston crown, which features a dome shape carefully optimised to deflect intake air upwards in the manner suggested, and aid turbulence and charge motion, but without accidentally causing air to spray towards the exhaust port.
“The air goes above the exhaust port and then pushes up into the combustion chamber. Since we have a cross-flow scavenging design, with the intake ports across from the exhaust port, albeit lower down, getting the piston crown shape perfect was absolutely critical, both for incoming air and for enabling burnt exhaust gases to rush out efficiently too,” Krzeminski adds.
“Some of your readers might remember the really old two-stroke piston crowns that had a weird sort of ‘wing’ shape on top of them, for a similar kind of deflection effect; an asymmetric piston wouldn’t work in our application, as our piston crown shape has to let air in as well as it lets exhaust out, and work together really intricately with the port locations and alignments.”
The timing and metering by which the REV allows gases out of the chamber has also been critical, and precisely tuned, to controlling the turbulence, charge motion, and mixing (this is explained further on).
Optimising the port and piston geometries, along with the air preconditioning and exhaust management, took extensive CFD work.
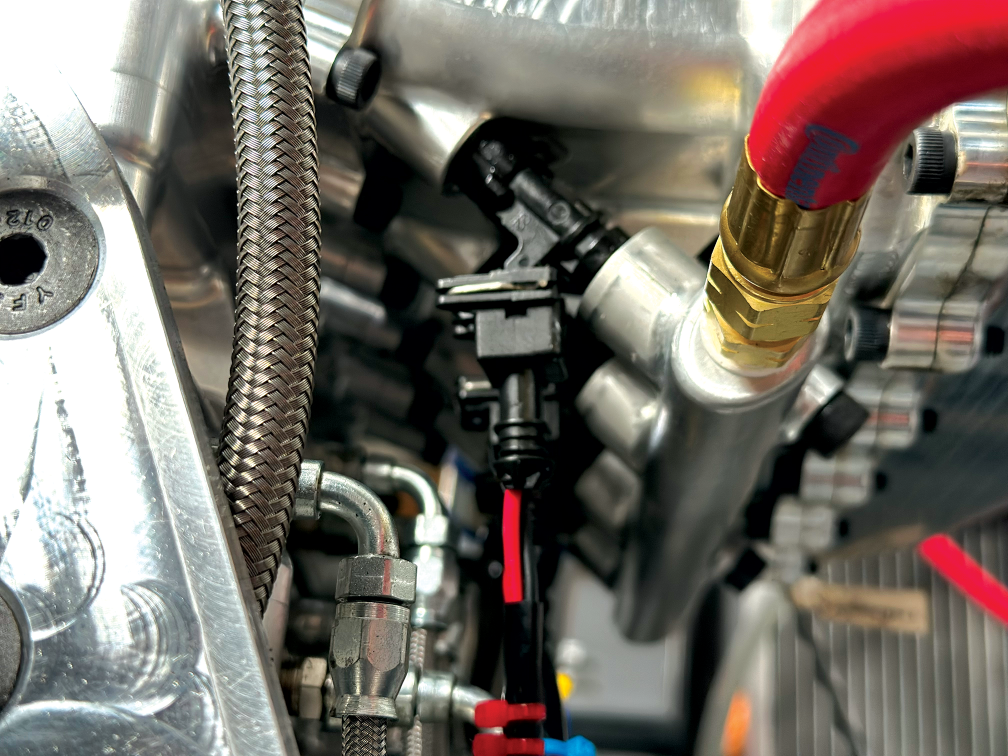
strategy there, although direct injection will be most useful in JP-8 applications
Beyond simulations, Alpha-Otto sought novel means of recording airflow experiment results inside the cylinder, including the use of a see-through cylinder head, placements of ribbons inside of the cylinder and close examination of oil deposit patterns inside, to understand where the air was flowing into and throughout the cylinder.
“Also, given that we have persistent airflow, with some air blowing into the piston skirt even when the intake port is closed, we’ve adjusted our piston-ring design such that there’s a compression ring and an oil-control ring at the bottom of the skirt, contrasting with the two compression rings around the top of the skirt,” Krzeminski adds.
“You’ll remember that we keep the crankcase as sealed from the cylinder and as close to vacuum-like conditions as possible to prevent drag losses on the crankcase as we go from 6000 rpm to 8000 rpm, so it’s absolutely crucial we avoid even a tiny amount of blow-by.”
Injection question
The REV Force engine has been equipped with two direct injectors and four port injectors across its two cylinders, as part of Alpha-Otto’s strategy of researching and enabling a wide range of fuels within one engine.
“Being able to inject fuel directly into the engine after the ports shut is advantageous for liquid-based fuels where hydrocarbon contamination of the exhaust stream is a concern, and for DI of gasoline or ethanol-based biofuels. DI really isn’t novel anymore, and there’s COTS systems we’ve bought and integrated for that,” Krzeminski says.
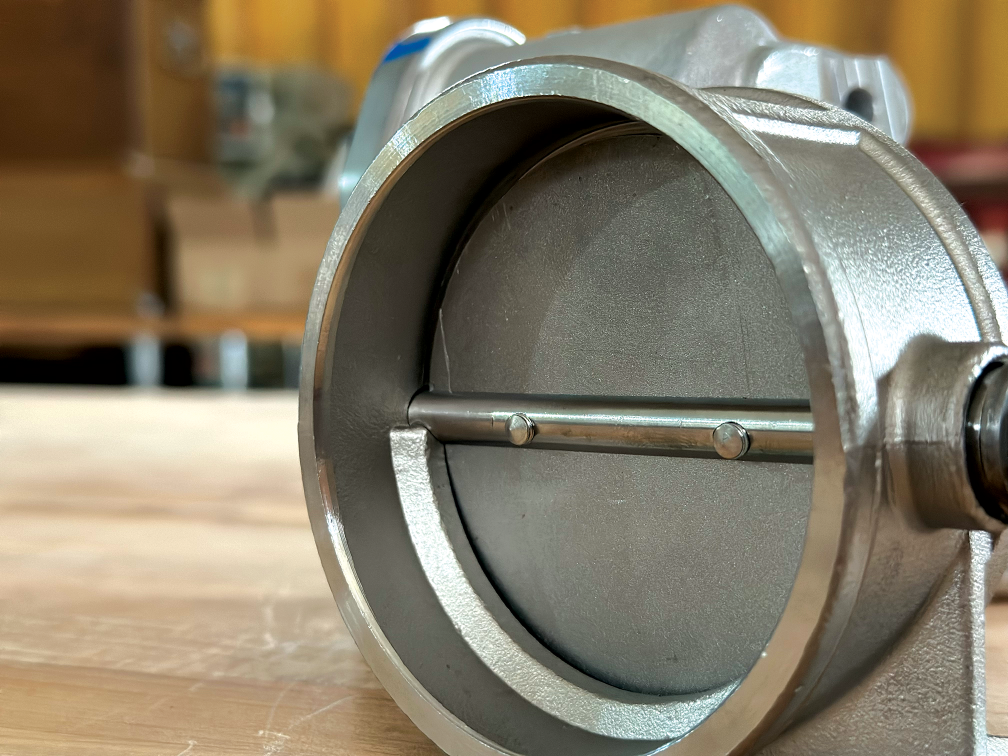
“However, in addition to having the REV open and shut the exhaust port, we’ve added a back pressure valve – a normal, servo-controlled butterfly – just downstream of the REV. That allows us to trap and create a ‘slug’ of exhaust air that stops fresh intake air from leaving the combustion chamber. Because of this, we’ve found no hydrogen in our exhaust when using the upstream port injection.”
Alpha-Otto has also looked into creating its own DI system, pressurising fuel in the pump before driving it into an injector for it to mechanically spray the atomised fuel via hydraulic pressure, and the company anticipates optimising and manufacturing such systems for defence applications relying on JP-8, owing to that fuel’s corrosiveness and the durability limitations of electronic injectors when handling it.
“But there are so many optimisation problems with DI, including droplet size, dispersion, wall washing and, of course, mixture homogeneity. As it stands, our port injector is positioned on the floor of the intake port and angled up into the cylinder, such that it sprays up into the combustion chamber at the cylinder head pocket,” Krzeminski says.
The company has found this strategy resembles DI enough, particularly in terms of the fuel efficiency gains versus an earlier, more conventional injector location and angle, that its tests show little gain when spraying from the direct injector in the cylinder head.
It is meanwhile considering trialling a sleeve-mounted, sideways injection system (akin to Suter Industries’ semi-direct injection; see Issue 60), but notes its present port-injection approach is already optimised for diffused combustion, so any new approach will incur fresh, painstaking months of optimisation to suit its LTC mode.
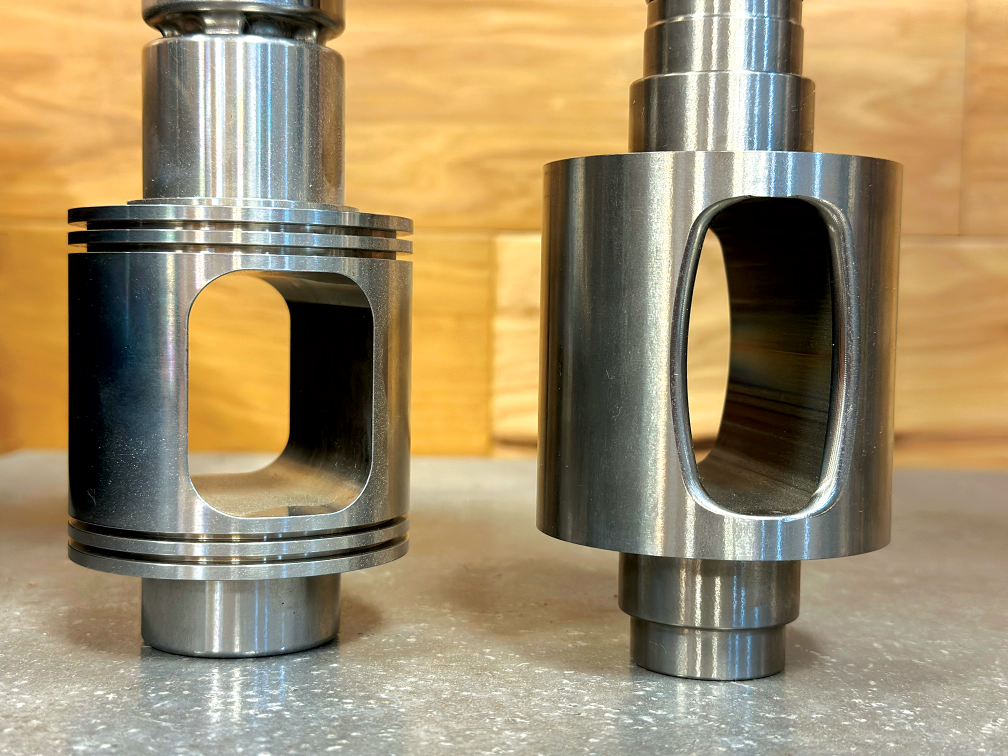
“All that said, the two-stroke architecture lends itself well to DI integration. We have a sizeable combustion pocket inside the cylinder head, so we have a lot of room for packaging an injector through that,” Krzeminski notes.
“The one we’ve used there is a bent stream injector, from which fuel flows down into the cylinder, but we have done a lot of work to determine the best time to inject, and we’ve actually found the best time is actually while the intake port is still open, because we get a tremendous amount of charge motion at that instant, so that’s how we get the most mixing. Traditional spark-ignition engines, by contrast, tend to inject later in the combustion cycle.
“We’ve looked into strategies built around that, and there are benefits to mixture homogeneity, especially if you can do multiple quick injections throughout the compression stroke, but other than enabling kerosene operations, especially JP-8, we are still leaning more towards our port injection plus diffused combustion approach because of its fuel-agnosticism benefits, and because it doesn’t bring the drawbacks of having to inject fuel at very high pressures.
“But, if a defence customer specifically wanted JP-8 – and by and large, we’ve found the boots on the ground do – then we’d likely optimise for the last 1% of power with a DI plus CI version of REV Force.”
Spark-assisted ignition
One area where LTC falls short of Alpha-Otto’s wishes is when aiming for peak power. At such speeds diffused combustion becomes difficult to manage, and a spark plug in the cylinder head pocket kicks in to continue power output until operations return from peak power to peak efficiency mode.
“Auto-ignition is a spontaneous reaction by nature, and hence unpredictable, so we’re continuing to compare pure auto-ignition versus our spark-assisted auto-ignition.
“The latter encompasses moments where we have almost ideal conditions for auto-ignition, but still need the spark plug to push it over the edge into combustion, as triggered by the ECU when auto-ignition isn’t happening,” Krzeminski says.
Those moments are likely to come more often than expected and not only when running at redline speeds. While Alpha-Otto is undaunted when asked to achieve auto-ignition in lab conditions, and will gladly demonstrate it for any well-intentioned visitors, in the field, fuel inconsistency is a widespread problem.
“It’s very hard to get ideal conditions in terms of fuel purity. A tank of supposed 87 Octane just doesn’t look the same in one location versus another,” Krzeminski explains.
“Even automotive hydrogen comes in purity levels from 95% upwards, and price increases exponentially with purity. Hence, there’s a lot of push in the hydrogen community for engineers to power mobility on low-purity hydrogen, because that can cut the cost by 50% compared with max-purity hydrogen. So it’s critical to always have the spark as backup in case the ignition event isn’t happening when we expect it to, so that combustion happens no matter what.”
Lastly, the spark plug acts as a useful backup amid high transients, with Alpha-Otto noting that, in general, diffused combustion works best when the engine runs at a consistent, stable rpm that is suited to efficiency maximisation.
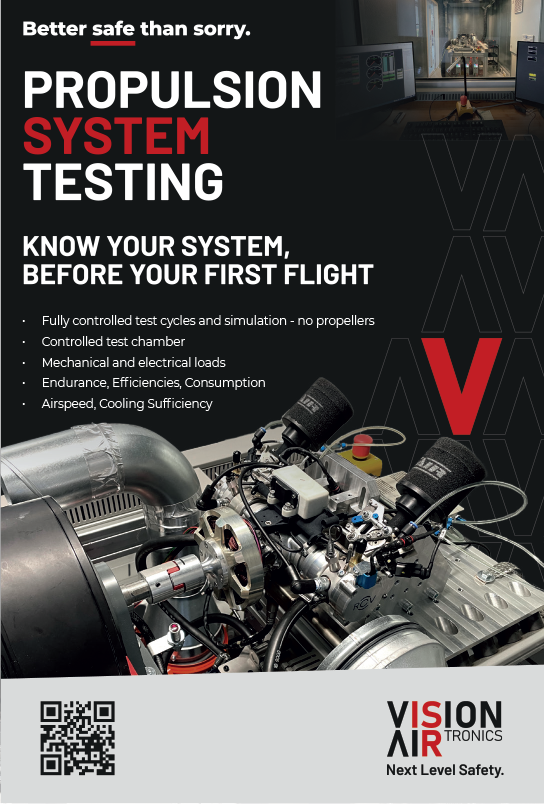
So, while some end-users would doubtlessly want to use at least some of the REV Force’s 127 kW for shaft horsepower, particularly when driving a main propeller, the company concedes that its ultimate value in the uncrewed space would likely be as a constant speed range extender in hybrid powertrains (or as a ground-based stationary power system for field-recharging battery packs).
Variable REV timing
As indicated, a back pressure valve is now installed downstream of the cylindrical REV, bringing an extra degree of control over exhaust gas movement in the REV Force engine.
A few other qualities about this core aspect of the engine’s technology have also changed since our investigation five years ago. For one, the shape of the valve has been optimised to achieve better control fidelity over airflow.
“The last valve was almost like a switch: air either flowed through the exhaust port or it didn’t. We wanted to change both the port and valve shape to allow more finite variations in flow, and more finely tune how air moves into and through the exhaust system,” Krzeminski explains.
“So, while the REV from five years ago was very straight, now the orifices and port are more ovular, which allows a more sinusoidal curve in terms of airflow rates as it rotates, and opens and closes.”
Furthermore, while some may recall that we previously reported on REVolution’s rotary valve being belt-driven by the crankshaft, Alpha-Otto has disclosed to us that the design (in both REVolution and REV Force) actually features an additional planetary gear component between the belt and the rotary valve. That gearbox is servo-actuated during operation to phase the relative angle between the rotary valve and crankshaft, hence serving as a variable valve-timing (VVT) mechanism.
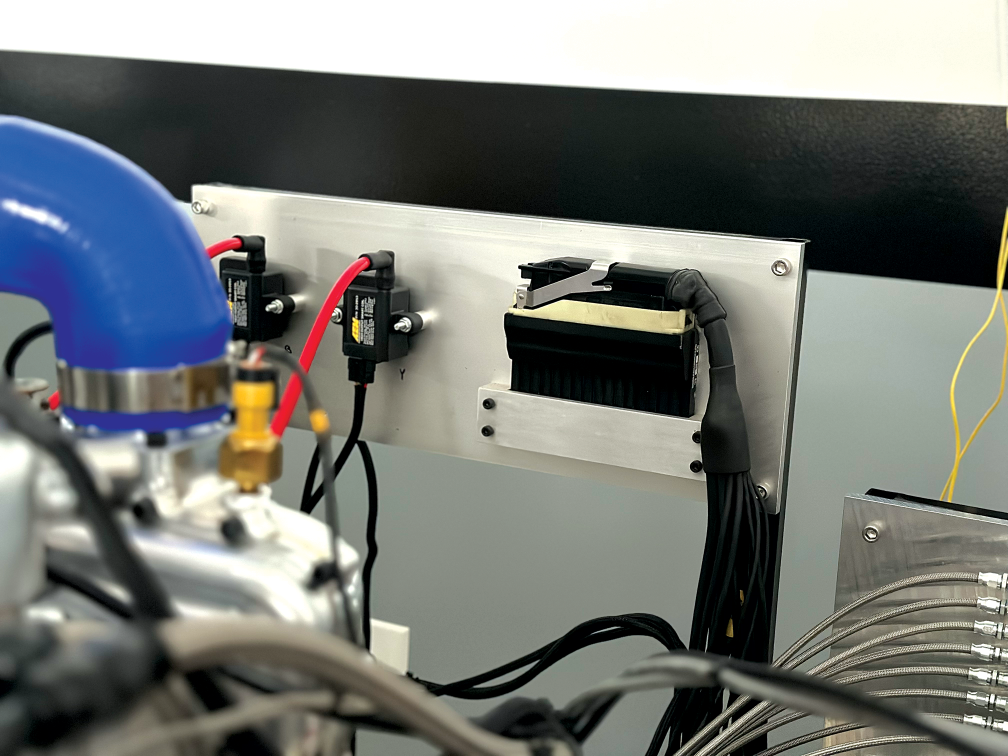
“Much like when one is developing a cam phaser for VVT, we’ve spent a lot of time evaluating crank position and exhaust valve position, and changing the latter depending on either the combustion mode we want to run or the speed load point,” Krzeminski says.
The planetary gear works continuously, phasing the valve anywhere over a 360° range. That means, for instance, that the valve could be made completely wide open, or bordering on shut, as the piston fires downwards and opens the inner exhaust outlet to the combustion chamber, effectively enabling throttle control over the engine exhaust and scavenging.
“That essentially means that, instead of our normal operating cycle, where the REV shuts the exhaust port at piston BDC, so that the supercharged air can flow freely, and the compression and power stages last just as long as each other, we can phase the valve 180° and create an Atkinson-cycle in which the power stage lasts longer than the compression stage,” Krzeminski explains.
“This could work especially well for VTOL transitioning aircraft, where for 5% of the time they’re in VTOL and need peak power output, and don’t care so much about thermal efficiency, but then they’re cruising for 95% of air time and need the high-efficiency mode for that.”
Combustion control
We previously wrote that the REVolution ran on a Cosworth ECU, and the REV Force uses the same solution for standard spark and injection timing. Since then, however, Alpha-Otto has engaged in developing its own proprietary control algorithms and controllers in Simulink as an alternative means of engine management, for which the Michigan-based outfit is mulling over the use of a different, more aviation-oriented ECU that is better suited to both LTC management and UAV applications.
“Some newer Cosworth ECUs would be capable in this regard, and we’re certainly not about to become an ECU manufacturer, but REV Force operates so differently to normal engines that it’s very difficult to use an off-the-shelf solution. In most of our bench tests, we’ve actually been using a PC directly wired into the engine to run it,” Krzeminski says.
The principle challenge that Alpha-Otto undertakes in this development is combustion control, in which the engine detects either the fuel type and quality or monitors combustion (the company having looked into many approaches for that), and responds by switching between fuel-specific calibrations or mappings embedded in the ECU.
“If you look at the profile or tracings of pressure sensor data in a cylinder, it tells you a ton about what’s happening in its combustion chamber: you can see clearly if you’re getting detonations, if ignitions happen too early or too late, and so on,” Krzeminski says.
“So, in future, instead of prioritising the analysis of conventional things, like throttle position, CHT and so on – which are, of course, very important – we’re going to really be studying combustion analysis, and what we need to see in TPS, rpm, CHT, EGT, MAP, or what have you, in order to be getting the correct, diffused combustion.”
Long term, Alpha-Otto plans to use machine learning (ML), given the relative ease in having a ML architecture (such as a transformer neural network) study and learn how different permutations of engine-sensor data could be indicative of successful diffused combustion, and refining it over time to eliminate false positives and false negatives.
“We can’t just use basic physics calculations and try to compute all of this on the fly. It’s just too much data to crunch. But we can monitor the pressure profile in many different ways,” Krzeminski explains.
“For example, you can measure ΔP across the cylinder, like I mentioned, with fairly inexpensive instruments, or just put a cylinder pressure transducer in – the latter is what we use in testing. Granted, we don’t want to do that in operation; we want to use proxies for what’s going on in the combustion chamber.
“Big picture: we want to identify and understand diffused combustion traces and back-calculate via ML where pressure, temperature, spark timing, exhaust valve timing and ΔP all need to be to reach that perfect profile for LTC.
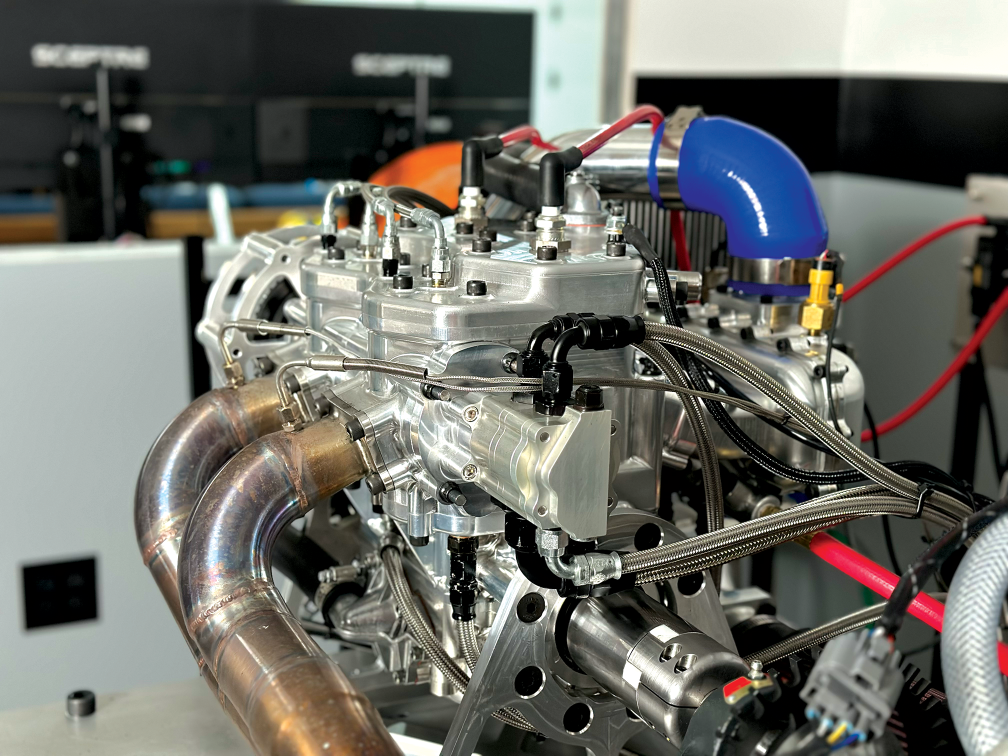
“That will enable us to maintain peak efficiency for cruise or range extension work. But, with real, ML-powered understanding of those traces, we’ll also be able to move the boundary conditions and adjust the ECU’s outputs as needed to move in a stable way towards either peak power or maximum continuous output.
“It would be a lot like how conventional engines today use an O2 sensor, but instead of looking at oxygen we will be looking at combustion and toggling engine parameters to get it to where we want it to be.”
While this will take more r&d, Alpha-Otto is prepared to supply engines running on the Cosworth ECU, embedded with a prototype version of its map-based combustion control strategy, which it could update over the air in future.
Holistic adjustment
In addition to offering a fine-tuned ECU in future, Alpha-Otto has been testing a shaft-mounted, axial-flux motor generator with dimensions of about 30 cm x 10 cm, and large enough to turn the REV Force’s full shaft horsepower into electric current, or drive the shaft to double its output (drawing upon battery energy to do so).
“Axial-flux tech, in general, works very synergistically with spark-ignited engines. Traditional radial-flux alternators upwards of 100 kW have massive magnets and can’t generate power at extreme speeds of 5000-6000 rpm or higher; instead being better suited to 1800-2600 rpm,” Krzeminski says.
“There are certainly electric motors that can output power at higher speeds than that, but in terms of power generation our axial-flux supplier’s [name withheld due to NDA] technology has proven incredibly efficient at 5000-6000 rpm, so it matches nicely with our engine.”
Should collaboration with its partner continue well into the future, Alpha-Otto envisions integrating the motor-generator system more tightly with REV Force and any future versions of the engine that may follow. This may include combined oil management and thermal management (including heat recycling from the motor-generator to the engine to complement the EGR).
“Some of your readers might know how Wankel rotary engines suffer a particular challenge of cooling their internal rotor. Big electric motors have a similar problem in that their stator can be pumped with water pretty easily, but their rotors aren’t so easy to cool, but pump oil through its shaft and suddenly it becomes incredibly cooled and efficient,” Krzeminski says.
“Combine that with an engine and suddenly you can develop a combined cooling strategy for both the e-motor and the ICE. Just as with the subsystems and stages of our LTC, there are huge efficiencies to be gained from integrating systems together and having them work holistically.”
Going forwards, Alpha-Otto plans to continue optimising the electrical and electronic aspects of its engine, and it is open to new potential suppliers, partners or other contributors whose specific insights and applications may provide valuable – and fascinating (to Krzeminski and his industrious colleagues) – directions in which to hone the REV Force technology for meaningful ends.
Key specifications
REV Force
Inline two-cylinder
Two-stroke
Spark-ignited
Gasolines, kerosenes, biofuels, hydrogens
Supercharged
Liquid-cooled
Crossflow porting
Weight: 48 kg
Maximum power output: 127 kW
Maximum torque: 160 Nm
Maximum speed: 8000 rpm
Bore: 74.8 mm
Stroke: 65.8 mm
Displacement: 578 cc
BMEP: 17 bar
TBO: 2000 hours confirmed (higher expected, pending future testing)
Some key suppliers
ECUs: Cosworth
Throttle: Bosch
Superchargers: Sprintex
Fuel injectors: Bosch
Fuel injectors: Magneti Marelli
Coatings: Line2Line Coatings
Bearings: NTN Bearings
Reed valves: Boyesen
Cylinder sleeves: In-house
UPCOMING EVENTS
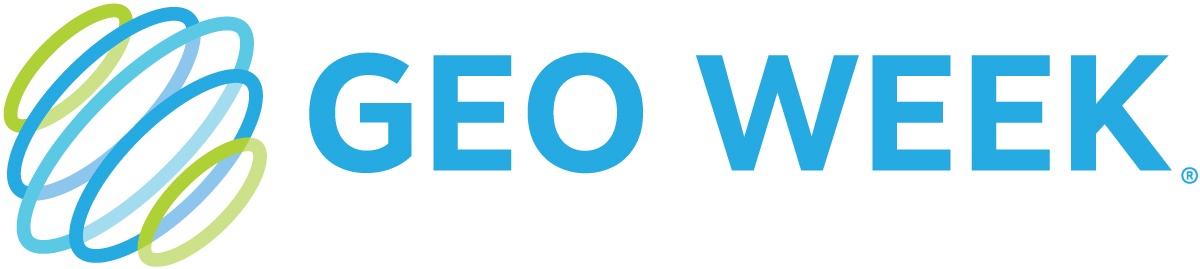
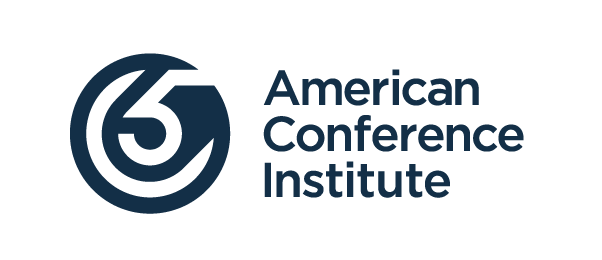
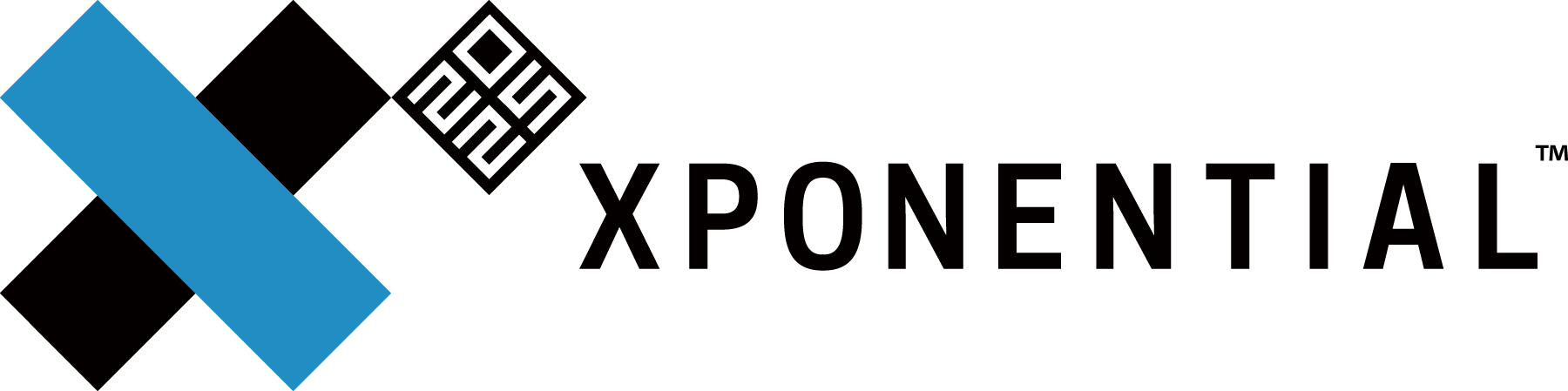
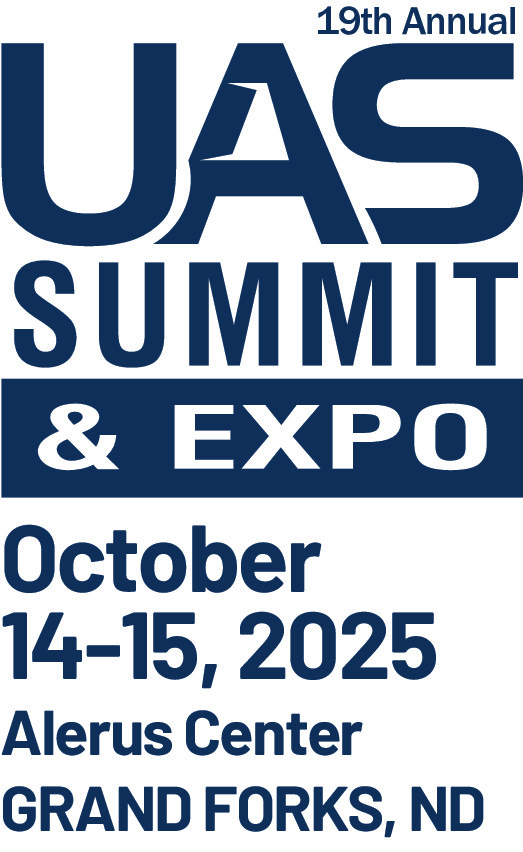
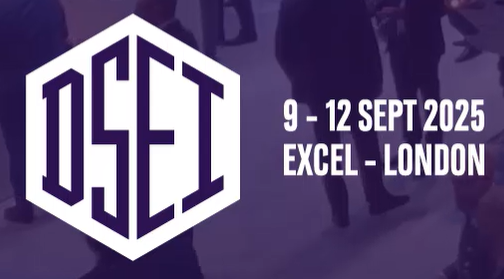
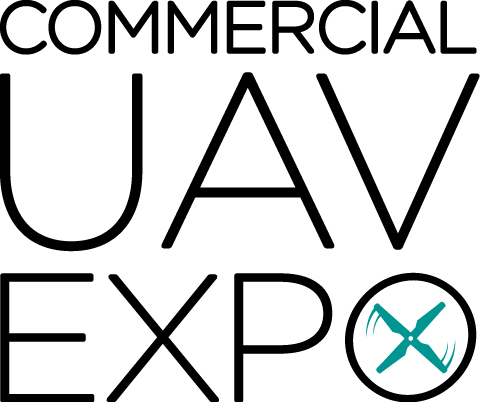
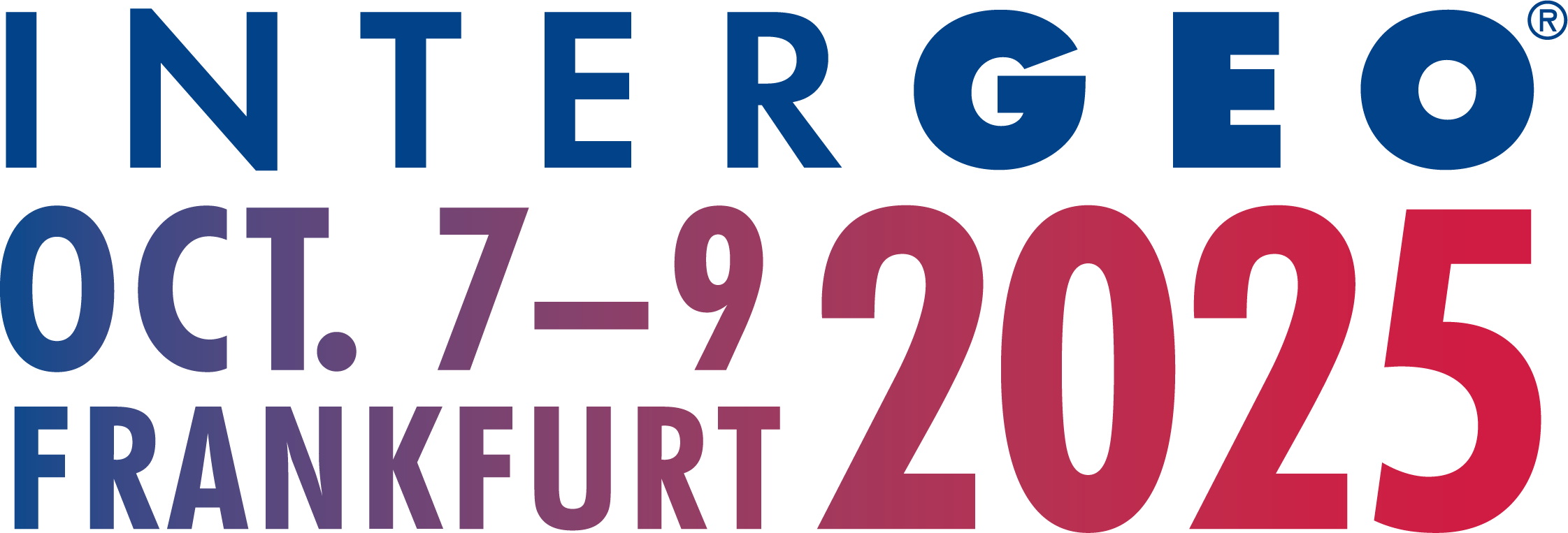
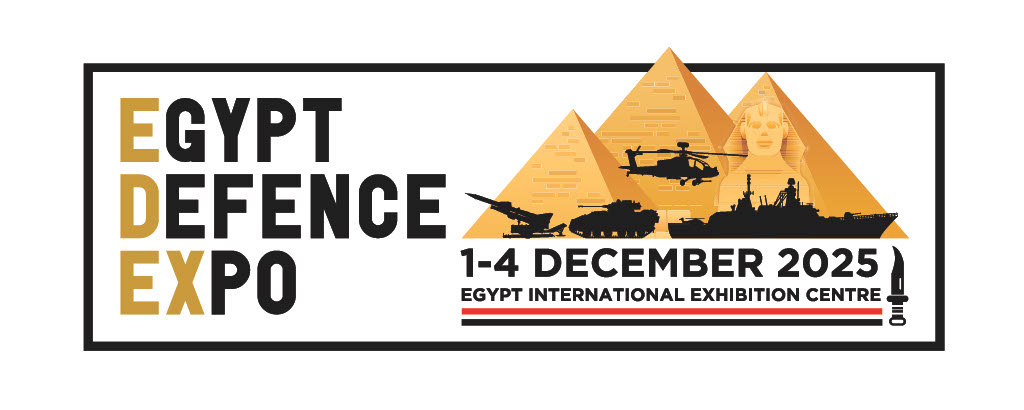
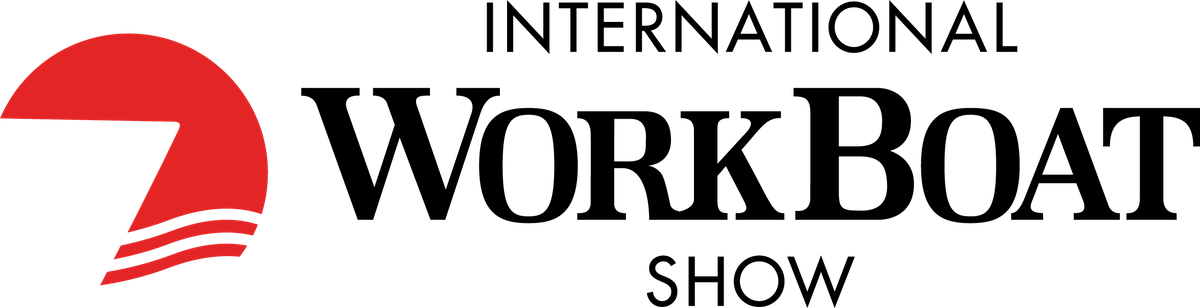
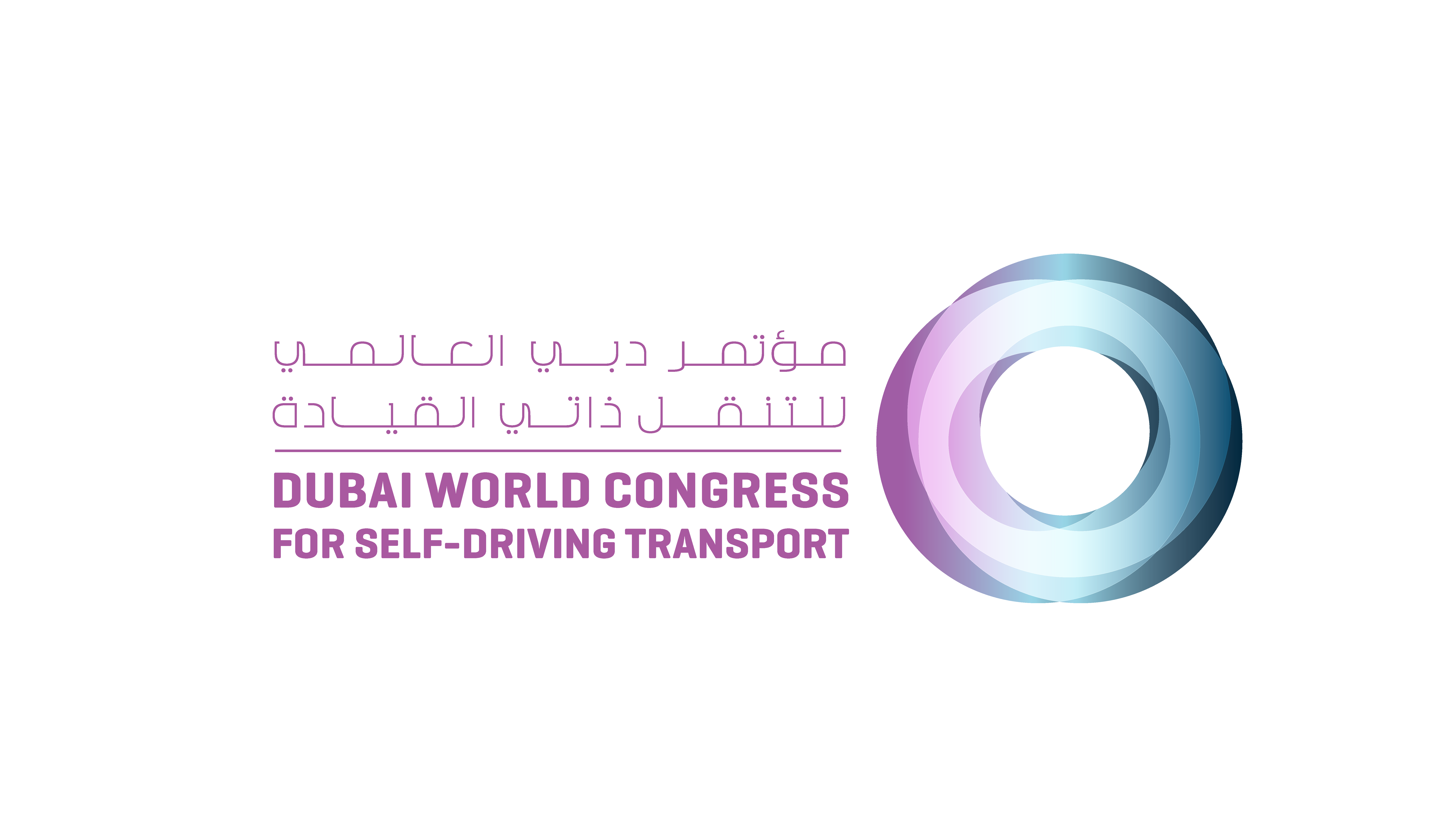
