SWL Robotics Tiburon
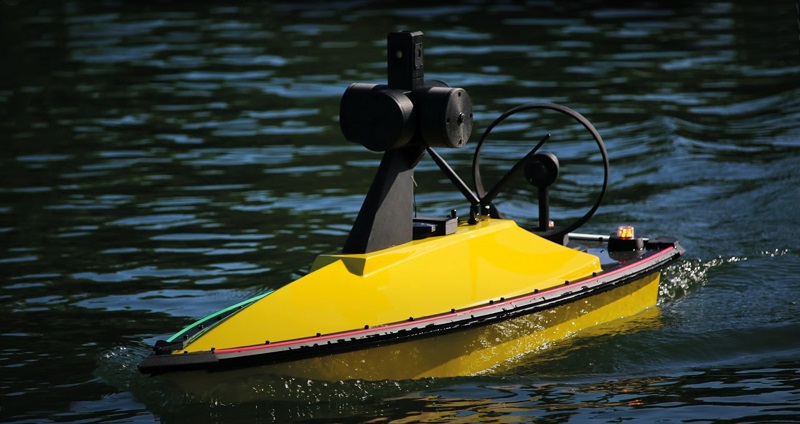
In at the shallow end
Airboat propulsion allows this USV to carry out surveys in water only a few centimetres deep. Rory Jackson examines its development
In the world of autonomous and intelligent systems, competencies developed in one type of vehicle can enable major breakthroughs for others. The marine sector in particular has benefited from innovations originally engineered elsewhere. For example, BeeX Autonomous Systems was able to design and build its A.IKANBILIS UUV thanks to AI technologies its engineers had originally developed for self-driving cars (see UST 47, December 2022/January 2023).
In another example, the hydrofoiling electric speedboats from Swedish maritime EV manufacturer Candela achieve very fine control and banking while foiling – something no other hydrofoil can offer so far – thanks to a heavily UAV-inspired flight controller managing the boats’ manoeuvring (as detailed in issue 11 of our sister magazine, E-Mobility Engineering, Autumn 2021).
In the latest example of how marine systems can be improved by engineers from all walks of life, SWL Robotics has unveiled the Tiburon USV, which has taken inspiration from crewed aviation, UAVs and airboats.
The company was founded by the father of the current president, Enrique Enriquez Jr, who’d had a long career in materials engineering, particularly metals and alloys for aerospace. The two had also founded their first UAV business in 1996, when the world of autonomous systems was far younger.
They sold that business in 2012, and recognised marine autonomy as a more open market and one that would be easy to research and develop for. Being based in Miami, they also had decades of boating experience between them.
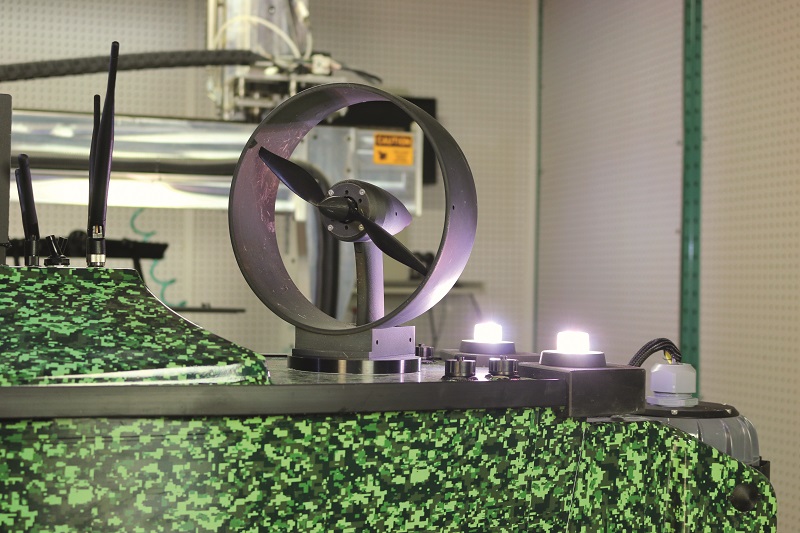
After developing and patenting the 360-ROV, which Enriquez says is the world’s first 360o video-capable ROV, in 2015 the pair realised that the industry lacked first-response type USVs that could deploy ROVs and UAVs. That spurred the concept of the FR-10 (‘FR’ standing for First Responder) USV, a diesel turbine and solar-powered vessel intended to serve as the mothership for ROVs, smaller USVs and UAVs, which we briefly discussed with SWL in UST 32, (June/July 2020).
The first prototype of the FR-10 is expected to be complete and in the water before the end of this year. Given the vessel’s size (about 10 m long) and the scope of it as a project – whose progress was hampered by the Covid pandemic – SWL decided later in 2020 to prioritise the development of the smaller Tiburon (1.5 m long) , as it would take far less time to finalise, certify and bring to market than the mothership.
“That’s why we’ve developed it and brought it forward by a few years in our r&d schedule,” Enriquez Jr recounts.
“In the long term, the Tiburon will very much be part of our mesh network of uncrewed first-response systems. In the meantime though, Miami is surrounded by shallows with shipwrecks, marshes, national parks and reefs that are in constant need of bathymetry surveys, which are typically executed by launching two large boats full of crew members and a lot of equipment.
“We quickly saw we could make something that could do that bathymetry way cheaper and faster, especially if we designed it to survey shallower waters where the 360-ROV and the outboard motors of a bigger vessel would be at risk of grounding or collision.”
The Tiburon was therefore developed with an eye towards fitting all the same capabilities as those large bathymetric survey craft and their crews into as small an uncrewed boat as possible. It is an all-electric vessel built predominantly from carbon composite, with a maximum height of up to 66 cm depending on the sensor mast installed.
Although the end goal is for the Tiburon to be launched and recovered via the FR-10, probably through a built-in motor-actuated slipway or caterpillar track off the mothership’s back, at present it can be hand-launched by a single operator from any boat, beach or jetty.
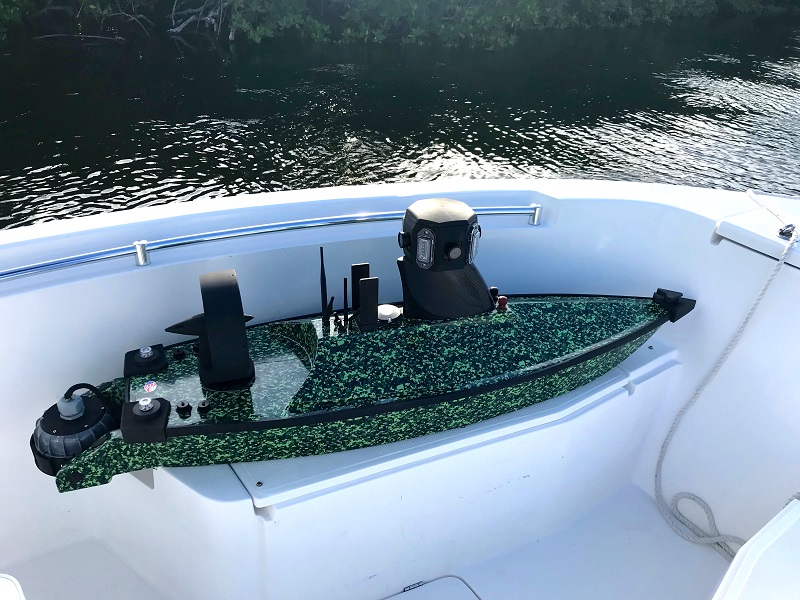
Overview
Notably, the Tiburon has a distinctive propulsion and hull configuration that is very different from the FR-10 or any other USV we have featured to date. Rather than using outboards, azimuth thrusters or waterjets, the system is propelled by an airboat arrangement, with a propeller above the hull that pushes the vessel through the air (as well as through the water).
“That allows us to plane in shallow waters of only 3 in [7.5 cm] deep, meaning we can get really near the shore if there’s anything we want to investigate,” Enriquez says. “For instance, bonefish spend a lot of their lives in mudflats, and are a really prized game fish in southern Florida, so being able to offer studies of them is quite unique.
“The other thing though is that, by using airboat propulsion, we don’t create air bubbles or turbulence anywhere near the transom of the hull. That means the Tiburon gets incredibly good conditions for most anything our prospective customers might want for their data needs – there’s absolutely no disturbance anywhere in the fields of our sensors.”
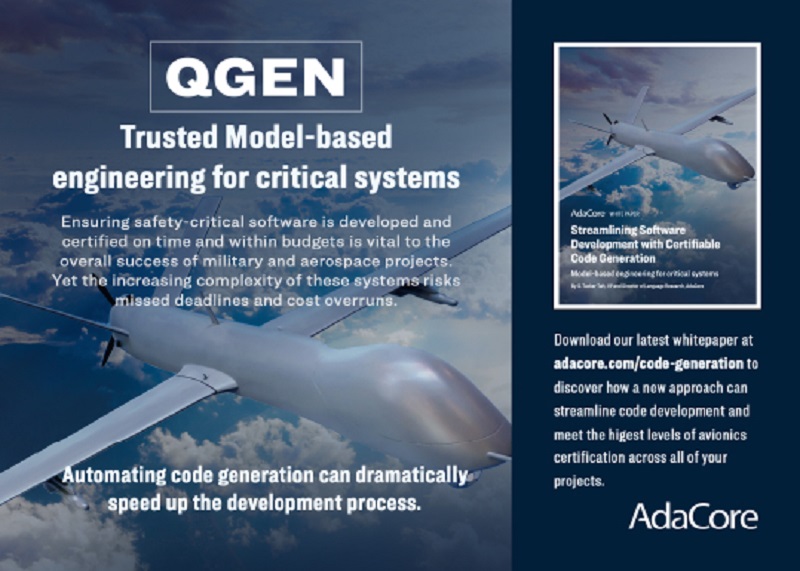
The Tiburon is now in its third iteration, with the first and second prototypes having been developed in 2018 and 2020 respectively. Enrique notes that a fourth version is in the works that will feature some subsystem changes, but that the design and technological principles of the USV are now tested, validated and largely matured. All the additions for the fourth and final version are largely complete and set to be integrated later this year; sales are expected not long after if the trials go according to plan.
As per the airboat design philosophy, a propeller sits on top of a short arm at the rear end of the hull, with a camera mast in the middle that mounts four HD cameras for producing the 360o 1080p video which Enriquez and his father prized in the 360-ROV and in the UAVs designed at their former company.
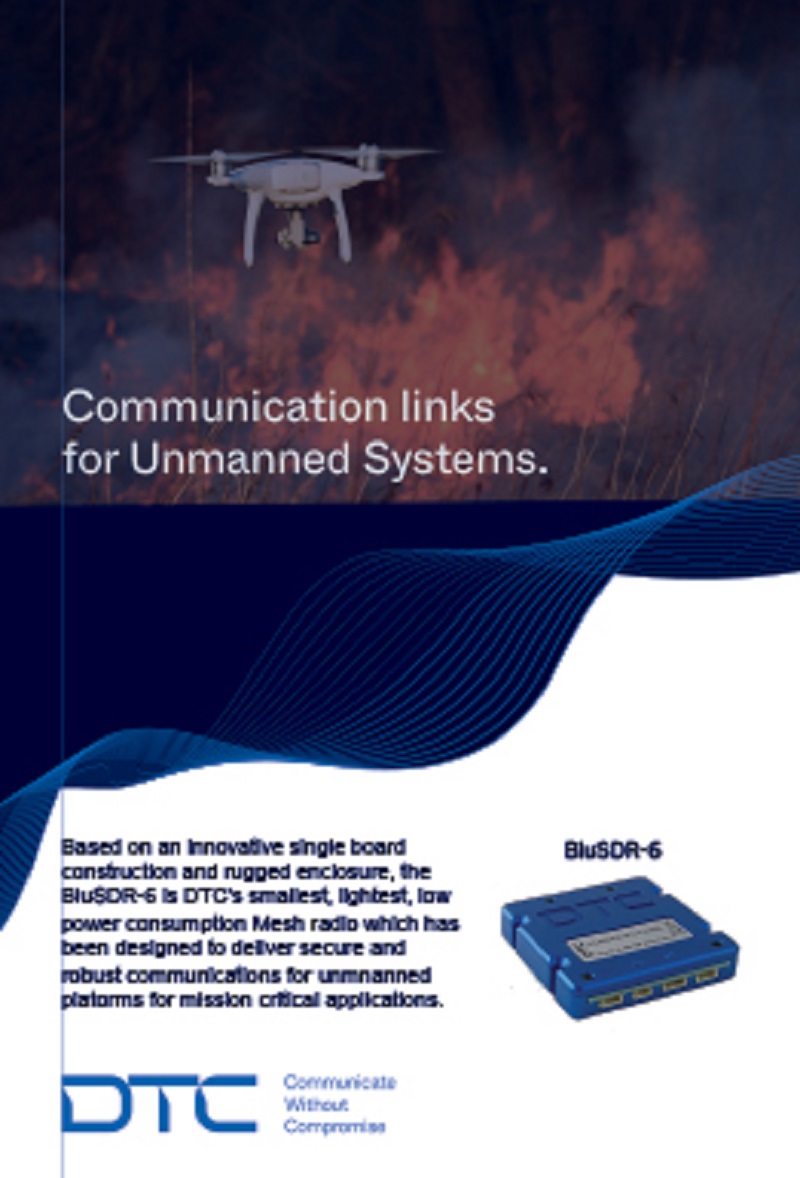
Inside the hull sit all the electric and electronic systems. These include a Cube Orange flight controller as the main computer, a fanless solid-state drive, an industrial computer from Neousys Technology for recording videos from the onboard cameras, control and comms routing, a battery pack with 23 Ah of capacity and 600 Wh of energy, and navigation and comms systems.
The hull itself is made from carbon fibre and several additively manufactured metal parts. In his materials engineering days, Enriquez Snr made numerous advances in additive manufacturing (AM), so this is a major area of SWL’s competencies.
Airboat powertrain
The choice of airboat propulsion configuration arose partially out of SWL’s initial wish to be different from well-known autonomous vessels in the US, such as Maritime Tactical Systems’ high-speed, highly aero and hydrodynamic watercraft and Saildrone’s wind and solar-powered boats (as featured in UST 38, June/July 2021).
“We looked around, and our eyes landed on the Everglades, where airboats are a very successful vehicle, with good reason,” Enriquez says, referring to the area’s shallow, marshy waters and the dangers of using submerged thrusters there. Such thrusters can be damaged or cause harm to marine flora or fauna, a paramount concern for many of SWL’s customers regarding autonomous boats.
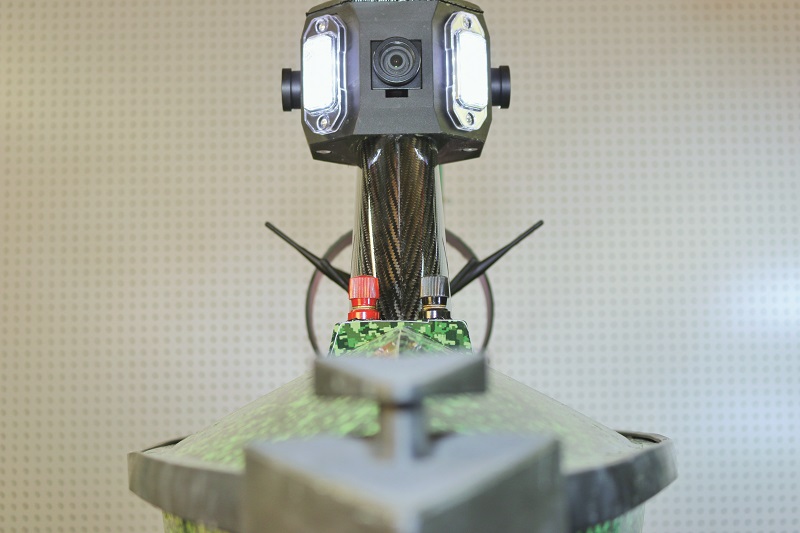
“Airboat propulsion also enables the Tiburon to manoeuvre in shallow or debris-prone environments such as the canals around Miami, where some of our local universities want to run pollution tracking and clean-up efforts. That made us realise the airboat configuration’s advantage in high-resolution hydrography.”
In its present configuration, the Tiburon’s power comes from a shrouded propeller driven directly by a 400 W BLDC electric motor. The motor sits in the hub of the propeller and on top of a small vertical arm roughly the same height as the shroud’s radius, with the arm on top of a rotating base. The base is servo-actuated to provide the vessel’s steering.
The propeller meanwhile has a diameter of 20 cm and a pitch and geometry optimised for torque, in order to carry heavy sensors while avoiding high tip speeds and noise, although different props can be used with different speeds to trade off between speed and torque.
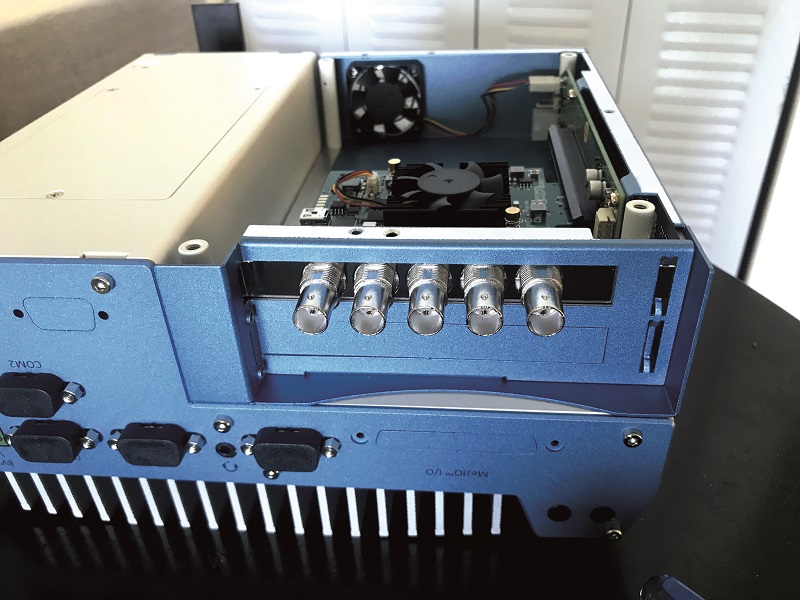
“We got our patent after 11 months,” Enriquez notes. “It was very straightforward and no changes were needed from our original version, partly because it seems that no-one else is doing this, despite all the benefits of the airboat design for hydrographic surveys.
“The 400 W motor provides a maximum speed of about 6 knots, and its efficiency is particularly good at around 4 knots, which is good for getting accurate and data-dense readings from the sonars, DVLs and so on.”
The batteries
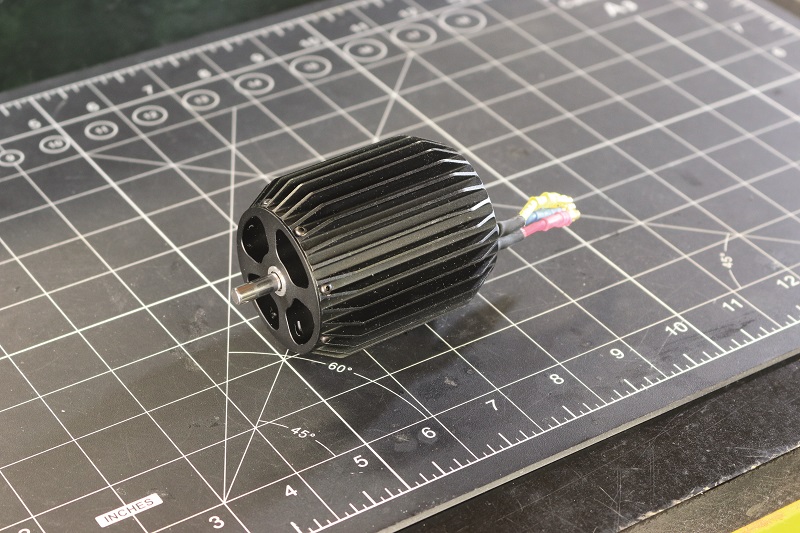
The Tiburon’s exact endurance varies according to the degree to which all the onboard systems are used simultaneously throughout each mission. However, Enriquez notes that a 2 hour minimum runtime has been achieved when running the electric motor, HD cameras, video streaming and all other systems at their peak power, and says a maximum endurance of more than 4 hours is achievable with the present batteries.
Those are built around LFP (lithium iron phosphate) cells, with the inherent behavioural properties of this cathode system having been a major factor of their selection. “With a lot of lithium-ion materials, you find that the voltage decreases as the battery discharges energy, so you actually start to lose power over the mission’s runtime,” Enriquez explains.
“These LFP batteries stay at the same voltage though – about 25 V DC in our use case – and the drop won’t come unless you get right to the end of battery capacity, before you have chance to recharge.”
As the drop in voltage comes nearly instantly, at a known and predictable point in the battery cycle, the Tiburon’s autopilot can be programmed to send a warning message to the GCS operator to end the mission shortly and return the vessel to its recovery point (if a timely return has not already been input into the waypoint schedule) as a function of runtime and SoC measured by the BMS.
“And of course, specific energy was critical – the batteries weigh 5 kg. We want to achieve as much runtime and distance as possible between maintenance stops, and the more payload weight our customers want, inevitably the slower the vessel will move, so energy versus weight is everything to us,” Enriquez says.
Powertrain roadmap
The next iteration of the Tiburon will feature a significantly upgraded powertrain, albeit with the same general configuration as the present third version. At the upper rear, the 400 W airboat drive will be replaced with a customised 24 V DC, 2.4 kW electric motor and a 34.3 cm propeller (from an undisclosed supplier) that is optimised for producing torque in the air.
Naturally, high speeds are not a strict requirement for survey USVs, and in fact can be detrimental to the density and quality of sensor data. The motor is therefore not intended to propel the airboat quickly, but will instead enable much heavier combinations of onboard sensors, since numerous SWL customers have increasingly asked to use payload sensors of greater weight and power than Enriquez and his team had originally anticipated.
To ensure enough runtime for surveying large areas of sea and offshore assets (and prevent the mothership having to constantly retrieve Tiburons that have run out of energy), the batteries will be augmented with Honeywell’s 1.2 kW UAS fuel cells, specifically the kind we investigated in UST 46 (October/November 2022).
SWL is now in discussion with Honeywell to fit at least 600 W of the cells in the Tiburon, with the main constraint on the hydrogen powertrain being the amount of space to be occupied by the tank of compressed hydrogen.
“We anticipate a minimum endurance of 4 hours at full load, although we don’t expect anyone to operate a Tiburon at full load for the full length of any mission. In fact we’re going to integrate an anchor system, nothing too long or heavy, so that the vessel can station-keep for extended point surveys without needing to power its motor,” Enriquez adds.
“Realistically, we could get a maximum reliable endurance of up to 10 hours using those fuel cells, between refuels and recharges. And if we choose to integrate solar panels as well, we’ll obviously push that further.”
In order to manage their current and future electric motors with the degree of torque control and dynamics desired, SWL selected motor controllers from APD. These have added capacitor banks for protecting the motor controllers from the current peaks that higher-torque electric machines inevitably produce.
SWL adds that the ability to tweak and customise the motor controller to its specific use was key to its selection of APD controllers. “We also find they are being used in UAVs with similar end-users to our target demographic,” Enriquez notes.
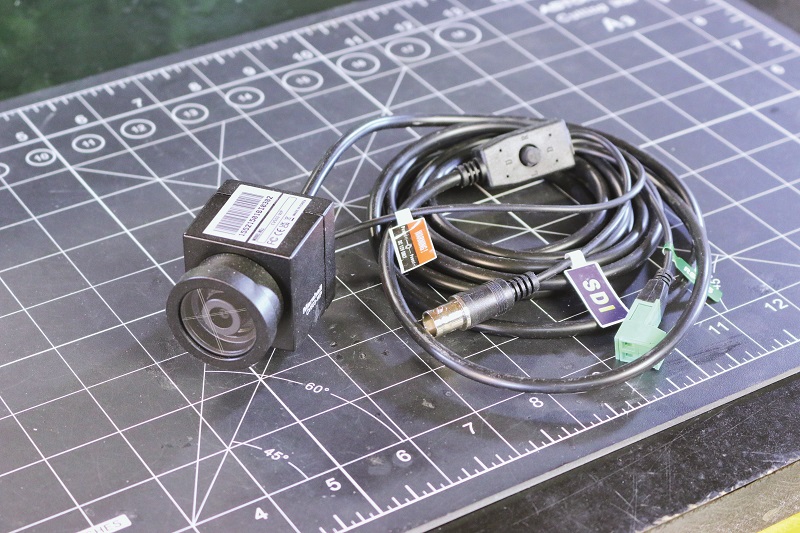
The hull
As discussed, the Tiburon is made not from fibreglass, as is most common for marine vessels, but carbon composite, a crucial component for saving weight in its body. Enriquez describes the body as “important, but not directly adding to the craft’s capabilities, unlike the computers and sensors”, and the weight saved in the hull is allocated accordingly to the payload capacity.
SWL’s partner here is Citius Composites, which had previously cut its teeth on Lockheed Martin’s VTOL UAVs, with considerable work specifically going into the aircrafts’ battery containment sleeves.
“The battery’s enclosure is of course a safety-critical component for containing harmful gases or sparks in the event of a crash, but we have also looked into ways of saving weight in the motor stand, the motor shroud, really any of the material sections on the craft,” Enriquez explains.
“And when we seal the craft, it effectively becomes a monocoque, one that’s strong and feels like a solid, single piece of composite. That’s important, as the vessel needs to endure impacts well and keep functioning.”
Along with Citius’ carbon fabrics and manufacturing, SWL selected resin systems from its preferred supplier Scot Bader as the matrix material. The resin of choice is more flexible than most, in order to reduce the brittleness that CFRP can exhibit.
Using carbon fibre safely and effectively in a marine vessel has not been straightforward for SWL’s engineers at all times, given the risk of galvanic corrosion of metals connected with carbon composite.
Additively printed aluminium parts have therefore been a critical enabler in terms of assembling and integrating the Tiburon’s electronics safely about the carbon bulkheads. SWL’s competencies in AM motivated it to scrutinise potential suppliers until it was satisfied that Addman could provide what it was looking for.
As Enriquez Jr says, “A lot of companies and engineers use AM to replicate a part they could have just CNC-machined, but what we needed was a group that was capable of thinking about and experimenting with different component geometries to see how much lightness and strength you can get by shaping a part differently.
“Addman has a huge additive printing house in the US, and they’re often contracted by the US government for work on rockets and hypersonic missiles. Our use case is different enough for them though that it actually challenges their machines and gets their engineers working on new r&d.”
Scot Bader’s resins were also used in bonding the composites with the additively printed aluminium, something Enrique notes that no-one else is doing in the marine space; only automotive cases such as Chevrolet and its new C8 Corvette aluminium bumpers and carbon fibre body are known at the moment.
For further safeguarding against corrosion and wear, all the Tiburon’s hull parts are coated after manufacturing but also wrapped in a 0.127 mm film. The exact nature of these is undisclosed, but they protect the hull against UV light as well as saltwater.
“To make our hull thin and lightweight, we and Citius have developed a proprietary and detailed laminate schedule [the list of sequential layers of materials used in building up a layer] that gives us the full mechanical and lifespan potential of CFRP,” Enriquez says.
“While maybe not quite as strong as a fibreglass composite, it saves way more weight than would be possible with it. We and our customers have run the Tiburon through hundreds of hours of tests and work in the field, and it has never suffered significant damage – in fact it’s stronger than we expected.”
Although all the hull materials are now chosen and treated to SWL’s satisfaction, the fourth iteration of the Tiburon will incorporate two carbon fibre pontoons and some dorsal fins, for greater stability at high speeds. The company anticipates this version to be capable of at least double the current design’s speeds, but emphasises that it is selecting a propeller drive for torque, and will limit the top speed if necessary for the sake of enhancing torque.
Autonomy and navigation
As mentioned, the Cube Orange is currently the main autopilot computer, with Herelink+ and Here3 systems used as the GCS and GNSS respectively. Enriquez praises this system as a highly effective technology that has enabled detailed mission planning and sensor programming for every SWL customer and use case to date.
However, SWL also plans to deploy Honeywell’s navigation, autopiloting and satcom systems for use cases that extend to the open ocean. That is due partially to the greater experience and therefore maturation of Honeywell’s systems in heavy-duty ocean vessels (Cube Orange is still a UAV autopilot in principle), making them suitably robust computers for BVLOS work around offshore oil rigs, wind farms or maritime border regions for example.
“Also, for users without much programming ability but who nonetheless want a detailed and easy-to-use interface with lots of features, we feel Honeywell will cater better for that market,” Enriquez says. “We’re in discussions with Honeywell, and they’re taking an active interest in configuring their small UAS navigation technologies for our use case, as we’re set to be the first company to use their systems in an uncrewed marine vehicle.”
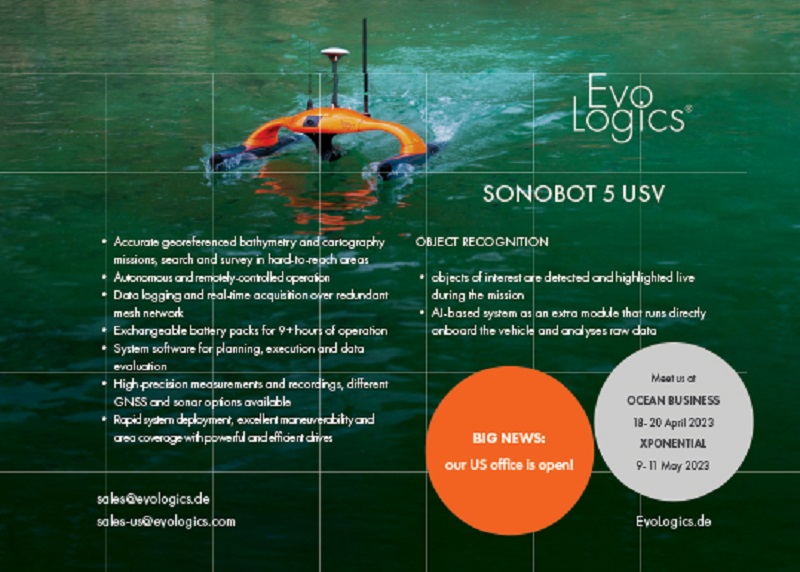
To date, SWL has already integrated Honeywell’s industrial computer and junction box into the Tiburon, effectively as a switchboard for control and comms with onboard sensors, so it makes sense to adopt further Honeywell systems for a more streamlined integration between the autopilot, junction box, satcom and fuel cell controller.
“A core goal was always to produce a system that made effective use of two onboard computers, so less like a hobby drone and more like an industrial-grade system. Make no mistake though, the Cube Orange is still a great autopilot for us at SWL, and it’s been key to the testing, development and debugging of the Tiburon,” Enriquez says.
“So, naturally, any of our USV customers familiar with the Cubepilot ecosystem and capable of the programming needed to configure it will be more than welcome to request a Tiburon that runs on Cube Orange, and we’ll be happy to continue supplying that.”
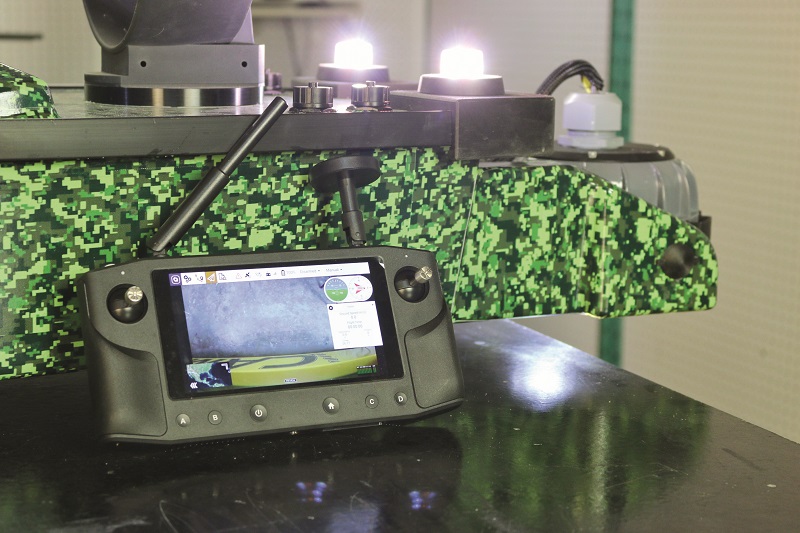
Survey philosophy
While various types of sensor can be installed in the Tiburon’s transom, the most common ones are the Teledyne BlueView MB1350 multi-beam profiler, Teledyne RDI’s Wayfinder and Pathfinder DVLs, and any Teledyne FLIR sidescan sonars, particularly fish finders for fish farm surveys. Naturally, others such as water quality sensor sondes have also been used.
Although the Tiburon will be used in a wide range of open sea environments once deployed as a ‘child’ system to the FR-10 mothership, SWL does not envision it being used as a standalone system outside any waters of more than 30 ft (9.14 m) depth.
“Our niche with the Tiburon when operating solo lies in surveys of lakes, confined areas, canals, swamps and shores,” Enriquez explains.
“In the long term, we expect to carry, deploy and recover maybe three Tiburons from one FR-10, along with a quadcopter and ROV, with the mothership and quadrotor working as comms relay systems for the mesh network of uncrewed systems and parties monitoring the mission. We don’t envision the FR-10 being equipped with survey sensors, although it easily could be if end-users ask for that.”
Data links and remote systems
SWL’s vision of a mesh network, enabling group coordination or potentially swarm behaviours in navigation and survey, has been supported by its work with Domo Tactical Communications (DTC). In principle, the low weight and size inherent in DTC’s software-defined radios for small UASs was a significant draw to Enriquez and his team, as was their low power draw.
“The other part was the extensive support from them,” he says. “I’ve been given direct lines to their engineers and their vice-president, and all that has really facilitated our integration and use of their radios. I have to say their support has been better than any company I’ve ever worked with.
“Being bought by Codan [a comms systems supplier in Australia] was also a major factor for us. I feel that Australia is making the biggest technological moves for the uncrewed space right now, and with DTC’s encouragement and support of our r&d I expect the country to be a big market for the Tiburon and our other vehicles in the future.”
He notes that DTC regards SWL’s operating model as the ideal use of its radios. The idea is that the FR-10 will sit in the middle of the ocean as a coordinating node for all the other uncrewed systems’ commands (in terms of navigation and survey behaviours) where its comms will be free from RF obstructions and congestion, with additional mission-critical information coming from the 360-ROV below via its tether.
Throughout the trials and use cases, SWL also reports finding minimal packet drops at long ranges in DTC’s data links, particularly compared with other radios they have tested. Lastly, the 128-bit encryption used in DTC’s systems has satisfied SWL’s requirements for comms security, given that some emergency response comms will be of a sensitive nature.
“And as well as DTC’s antennas being well-shielded, we’ve grounded them carefully and studied waveform propagations from the Tiburon; we’ve yet to experience any performance issues from them,” Enriquez concludes.
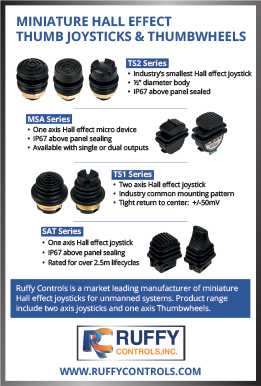
Future plans
SWL’s close relationship with DTC is also pushing it to look towards some emerging use cases it feels the Tiburon is suited to. For instance, the rapidly growing use in the US of Microsoft’s HoloLens mixed reality technology – both in the military with respect to Future Combat Systems projects and in industrial applications – is being supported by DTC’s comms systems in some real-time contexts.
“Before long, uncrewed systems are going to need to integrate smoothly into the HoloLens and communicate their live survey information in real time to soldiers and strategists,” Enriquez says. “I feel we’re well-set for moving our vehicles into that architecture.”
And while much of the Tiburon’s design is now mature, with essentially all the remaining changes set within its roadmap for this year, as indicated earlier, Enriquez is tempted to make one more addition to the vessel in the future: solar panels.
As well as enabling range extension and the ability to recharge without returning to its operator or mothership, putting solar panels on the Tiburon will allow SWL to begin performing experiments and collecting data on how the technology performs in its operating environments.
That knowledge will be vital to future integrations of solar cells on the FR-10’s top deck, to enable SWL to select the optimal photovoltaic materials, anti-reflective coatings, protective encapsulants and electrical parts for the larger USV. That will give the Tiburon’s survey missions and the FR-10’s comms relay duties as much energy and runtime as possible, given that SWL’s primary target market is first responders.
At the time of writing, the exact choice of solar cells was open, although any readers curious about currently available solar technologies for uncrewed systems can turn to page 98 to learn more.
Specifications
Tiburon USV Airboat
- Some key suppliers
- Autopilot: Cubepilot
- Autopilot: Honeywell
- Industrial computer: Neousys Technology
- Navigation systems: Cubepilot
- Navigation systems: Honeywell
- Satcom: Honeywell
- Radio comms: Domo Tactical Communications
- Motor controllers: APD
- Cameras: Marshall Electronics
- Payload sensors: Teledyne
- Payload sensors: FLIR
- Payload sensors: Honeywell
- Additive manufacturing: Addman Engineering
- Carbon fibre: Citius Composites
- Resins: Scot Bader
UPCOMING EVENTS
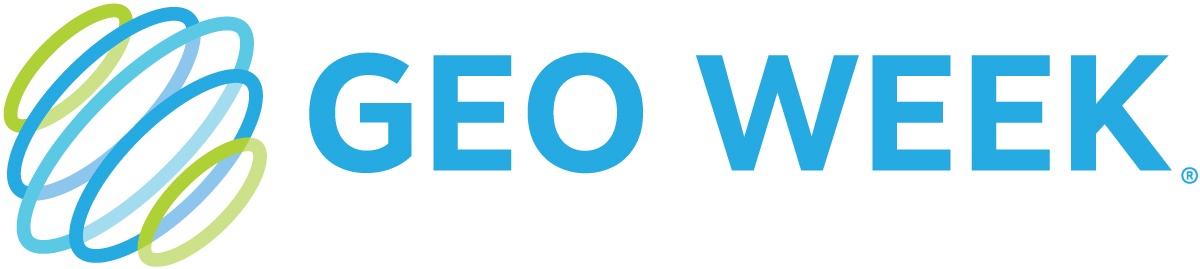
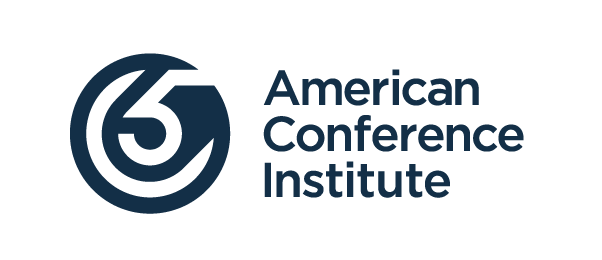
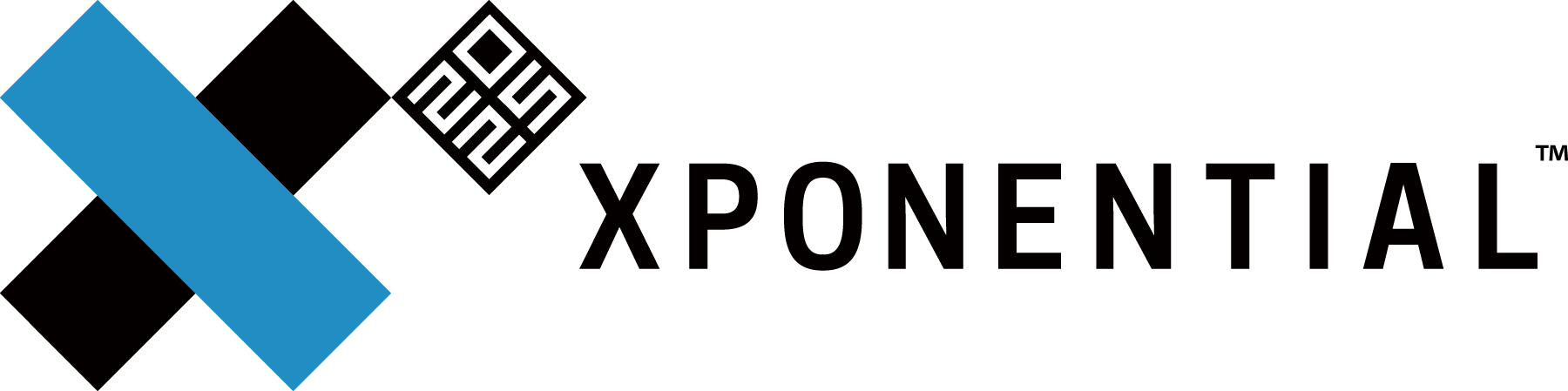
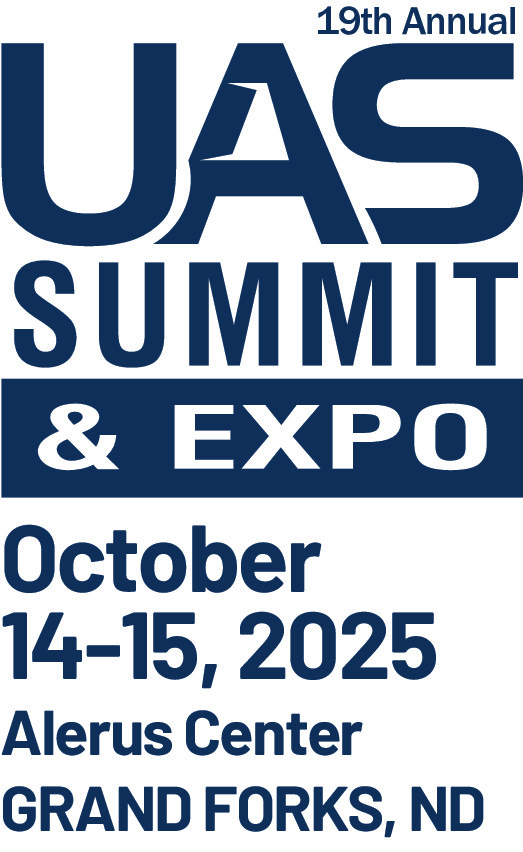
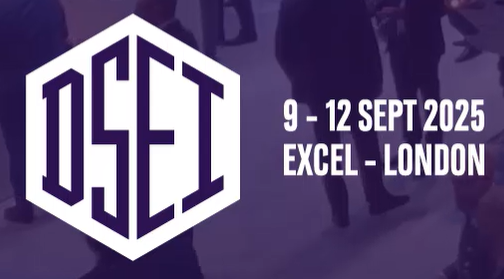
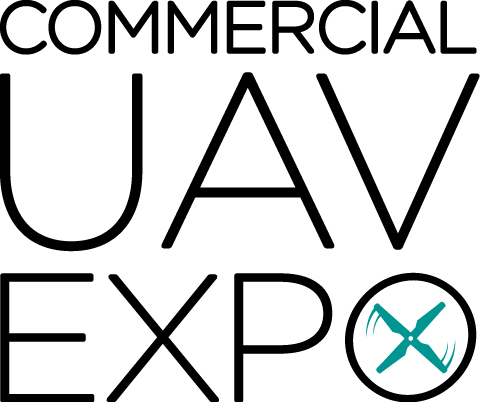
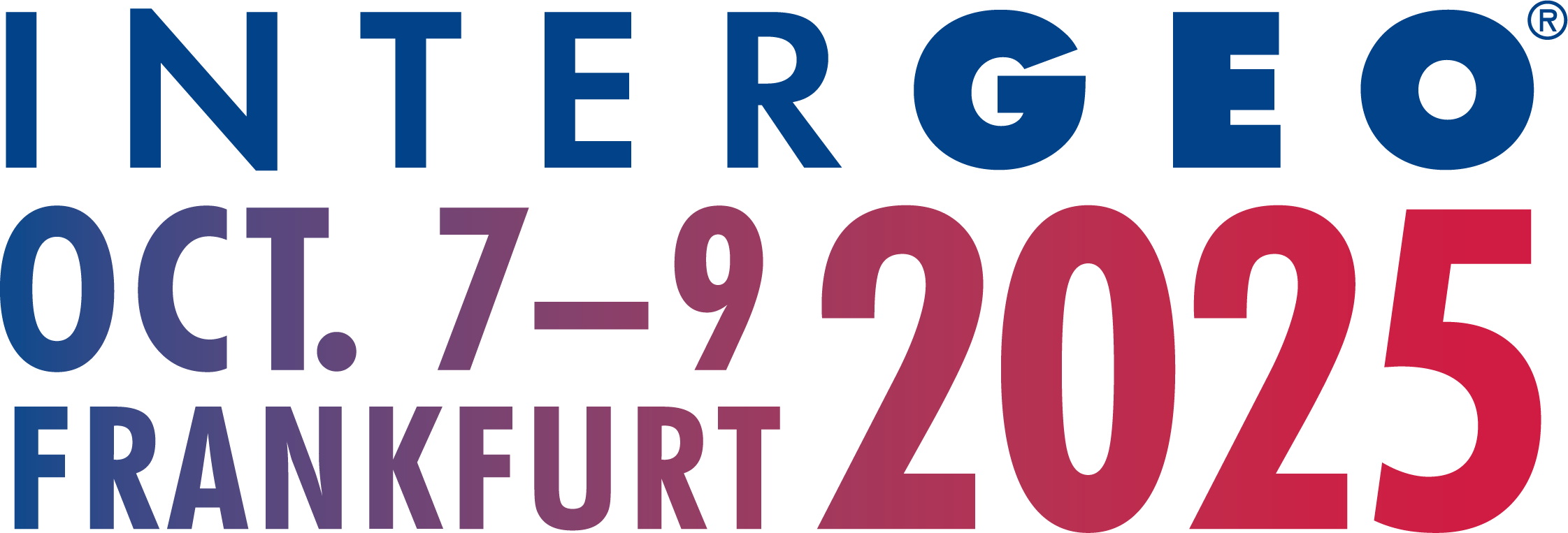
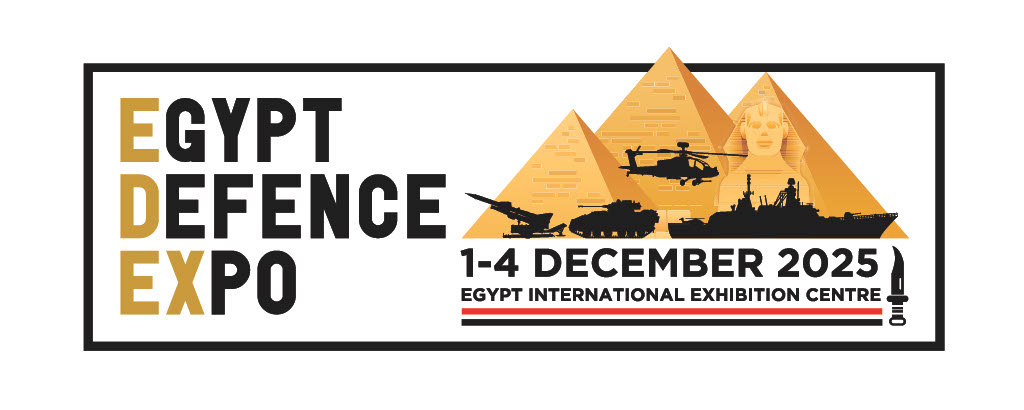
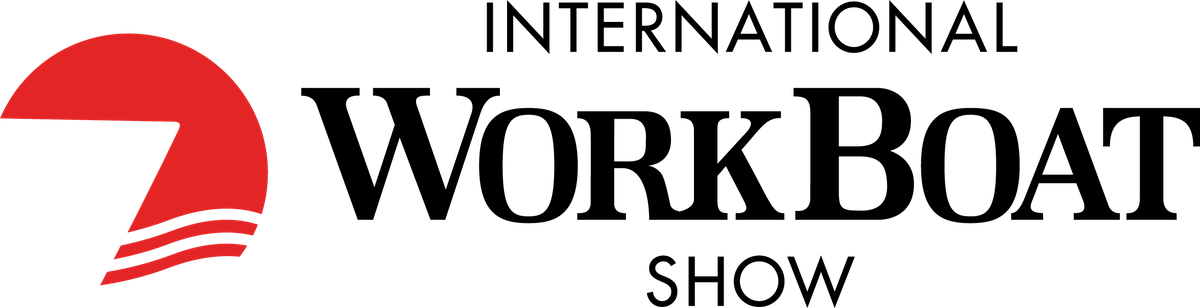
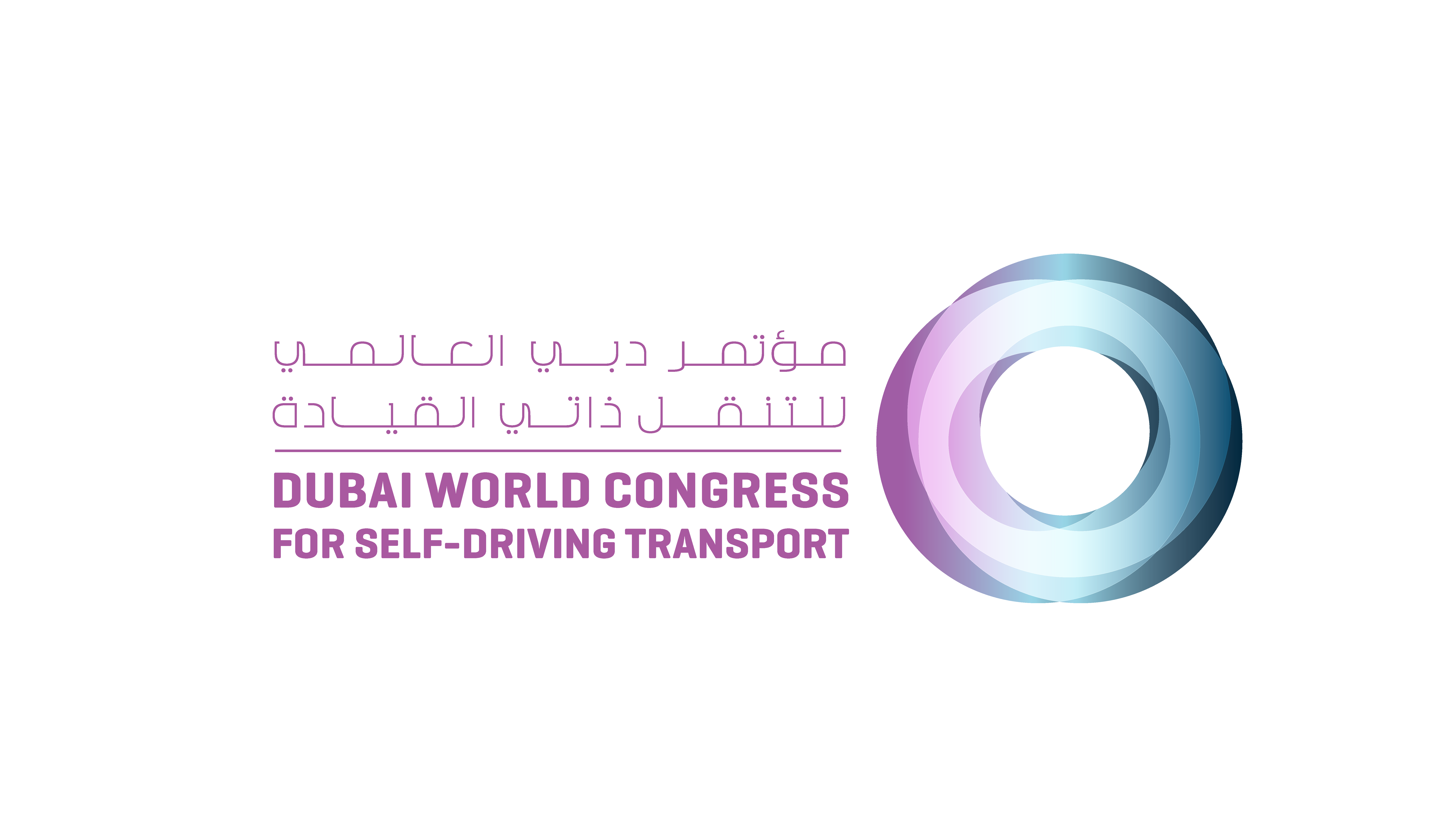
