ACUA Ocean Pioneer-class H-USV
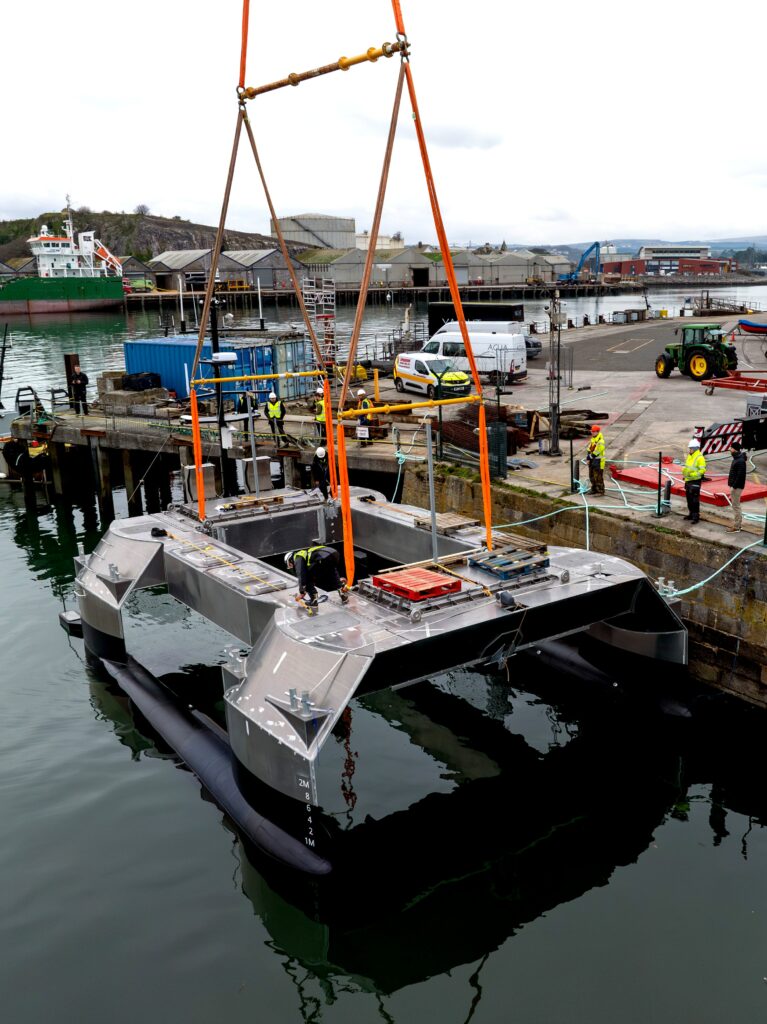
(All images courtesy of ACUA Ocean)
Whatever the weather
Rory Jackson learns about a heavyweight USV aiming to deliver high-quality data in severe sea states
As an island nation, dependent on seafaring vessels for trade, defence and more, the UK’s traditions for innovative and robust shipbuilding date back centuries. Small wonder then that today, amid booming demand for automated ocean logistics, security and mass data collection, British shipyards are steadily gearing up to work on a new generation of large, metallic autonomous vessels that stand to revolutionise how the world’s waters are mapped and studied.
Much of this was planted in 2015, when the Shell Ocean Discovery XPRIZE kicked off a bout of professional USV development never seen before. The winning entry, the Sea-Kit USV, came from team GEBCO-Nippon Foundation Alumni (see Issue 38), which included Neil Tinmouth, who served as COO of Sea-Kit International for the next few years.
Neil gradually noticed the critical limitations of commercially available USVs, particularly the poor reliability and stability of 1-2 m, jack-of-all-trades monohulls when monitoring in open ocean conditions. This motivated him and several others (including his brother, Mike) to start researching beyond the small, traditional boat designs in order to engineer a USV capable of taking over from crewed survey ships.
Through this research, they happened upon the small waterplane area, twin-hull (SWATH) vessel configuration, which held immense promise for creating the new, novel and fit-for-purpose kind of USV they all longed to build – one not only able to survive in open ocean conditions, but able to continue functioning normally with on-time collection and delivery of high-quality data, even amid the harsh waves and weather of severe sea states.
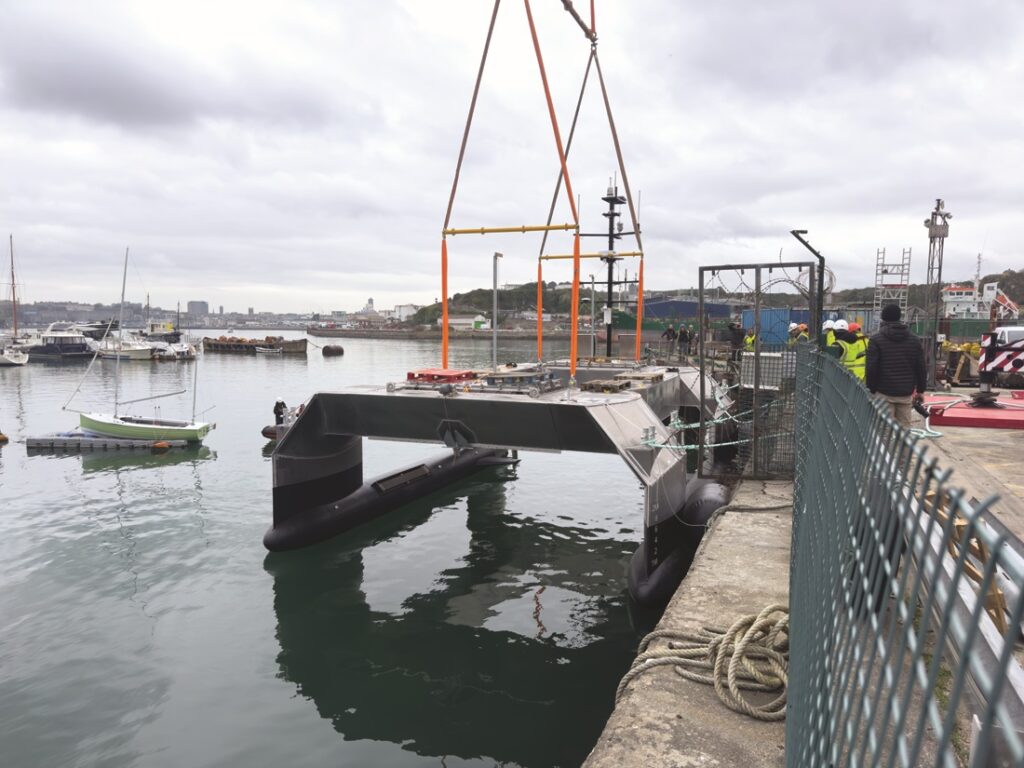
SWATH vessels achieve this by minimising their hull cross-section at surface level, where waves have the greatest impact, and maximising it below surface, where wave excitation drops exponentially. Those well-versed with UUVs and crewed submarines will know that such vehicles are minimally affected by wave action, so if one pictures a catamaran with each of its twin hulls riding atop a bulbous submarine, one is more or less picturing a SWATH vessel.
As Mike, now COO of ACUA Ocean, tells us: “Back then, I was an innovation mentor across several uniformed programmes and fellowships in the UK MoD, but I had really wanted to get into the world of autonomy, thanks to years spent in conversation about it, so I founded ACUA Ocean in November 2020. I convinced Neil [now CEO] to join me in summer 2021, bringing with him his knowledge, his background and his network for autonomy related industries.
“We then began working with John Kecsmar and his team at Ad Hoc Marine Designs, who are basically the global leaders in SWATH vessel engineering. We’ve also worked with the University of Southampton Marine and Maritime Institute (SMMI) and the Wolfson Unit, which was a great partner for technical analyses, simulations, wave-tank tests and the like.”
Just as certification is crucial for serious UAV and UGV manufacturers, ACUA Ocean has focused on working with MCA, Lloyd’s Register and other regulating bodies to build its USVs to class and code, and achieve certifiable vessels that are highly functional in open ocean conditions.
Broadly, ACUA Ocean calls its products “H-USVs” (hydrogen USVs) out of a dedication to net-zero operations as strong as its emphasis on regulatory approval. Such approval is expected in Q2 2025, following completion of sea trials and demonstrations of its inaugural H-USV, the USV Pioneer.
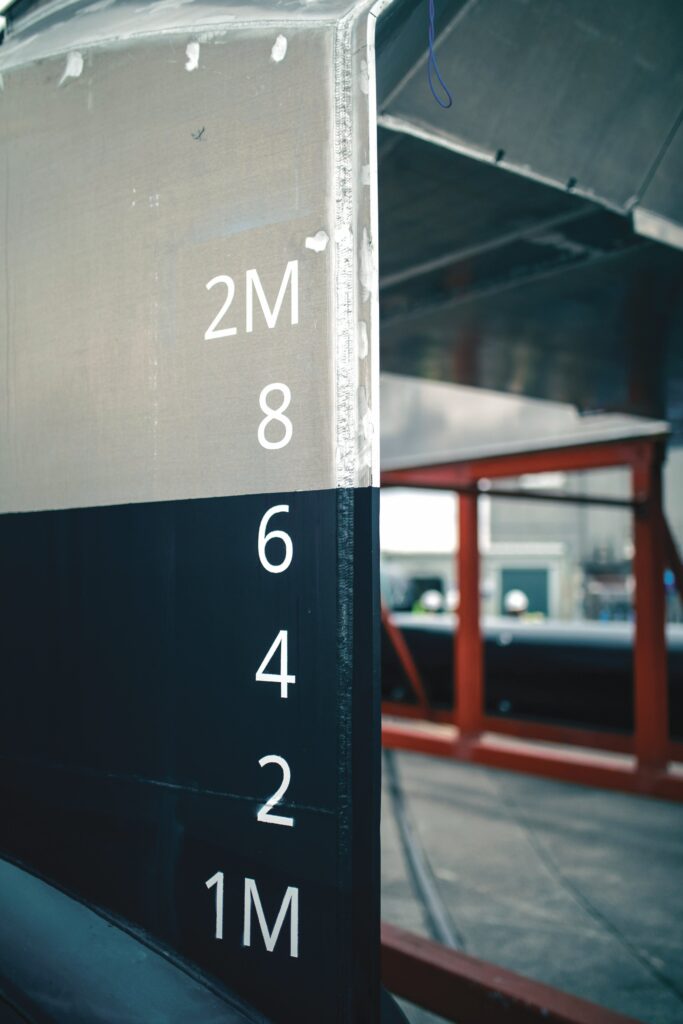
First in a line of aluminium-built, Pioneer-class H-USVs, the 14.2 m-long USV Pioneer displaces up to 25.7 t. It has a 3.7 m-high hull (with a 1.6 m draft, and an 8.1 m total height if the stern electronics mast is included), as well as a 9 m beam.
The vessel’s buoyancy comes from two torpedo-shaped pontoons (‘demi-hulls’), with four lengthy struts at the outermost corners that run upwards to support a body consisting of two longitudinal beams and two transverse beams. These are arranged around a 6.5 m by 3.8 m moon pool, designed with two longitudinally-running mounting booms to accommodate either a standard 20 ft container or two 10 ft ones.
Marked by a plethora of redundancies, including either two onboard hydrogen fuel cells or diesel generators (enabling 18 or 50 days, respectively, of endurance at 4 knots), the design is approved for Cat 0 operations, meaning unlimited freedom to work in open-ocean zones.
“We are working towards MCA Workboat Code 3 approvals for everything on the Pioneer-class minus the hydrogen system, because there are no rules or regulations around hydrogen at this time, so we’ll be taking a risk-based certification approach to verify and justify the safety case for hydrogen,” Mike adds.
“The near-perfect stability of the SWATH design, combined with the dedicated 5 kW of continuous power for payloads and 6.5 t of carrying capacity, mean we’re in commercial talks with a range of ROV OEMs, most having visited our headquarters in Turnchapel Wharf here in Plymouth in November 2024.
“Our first industrial application will probably involve deploying up to 1 t ROVs in asset integrity inspections and light intervention, pipeline inspections, wind-farm monitoring, data cable surveying, and the like.
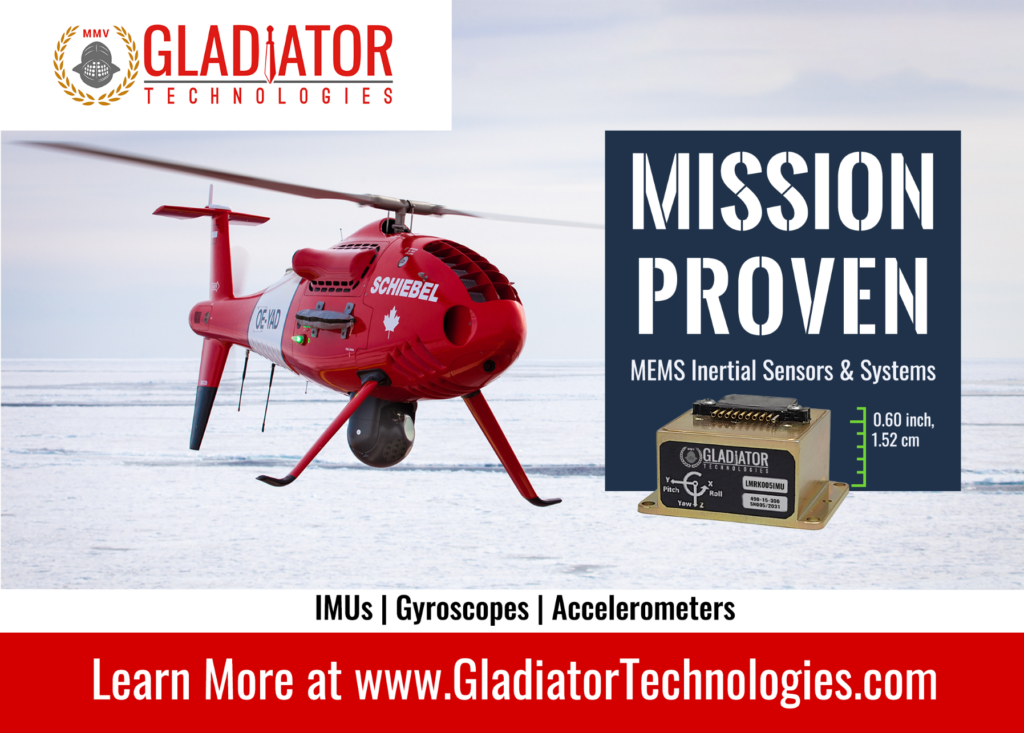
“Beyond that – and there are a multitude of prospective dual-use customers – could be highly stable launch and recovery of UAVs for monitoring wind farms or illegal fisheries. Any echosounders, sondes and so on can work from our moon pool, just as in a crewed vessel, but saving crews the need to live for months at sea amid horrendous sea states.”
From Southampton to Wight
Following an introduction to Ad Hoc in December 2021, Kecsmar became the design authority for the USV’s hull and structures, and it has since led most of the CAD and FEA work, including through all three rounds of the Clean Maritime Demonstration Competition (CMDC), where ACUA secured total project funding of more than £5 million across CMDC Rounds 1, 2 and 3.
Southampton, meanwhile, provided critical input on stability calculations, particularly through wave-tank testing, with the three partners’ collaboration progressively iterating its initial prototype into what became Pioneer.
By July 2023, such testing included affirming the prototype design’s ability to launch and recover 1 t payloads in various sea states.
“We could, for example, simulate all sorts of slamming effects of waves on the hull, which is a lot more difficult to validate and verify via CAD. There isn’t a lot of data available for digitally simulating SWATH vessels to begin with, so it wouldn’t have made much sense for us to do the traditional thing of starting in digital environments and then trying to replicate and verify our results in real-world tests,” Mike says.
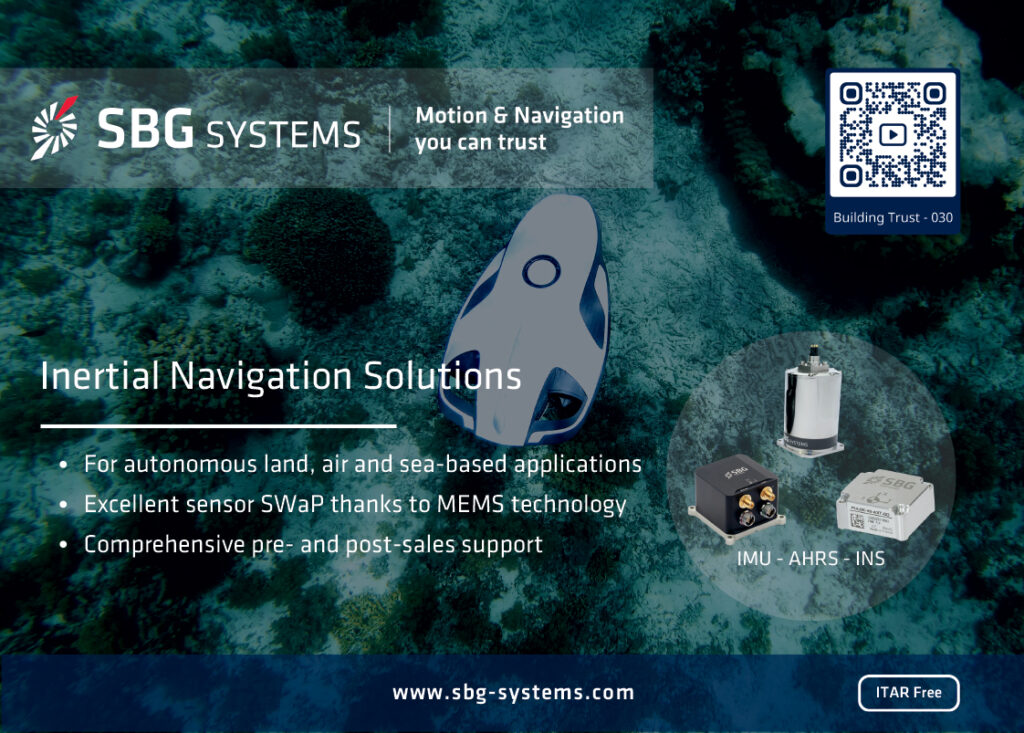
Pioneer’s full-build phase began in February 2024. The construction of the first complete unit was led by Aluminium Marine Consultants (AMC), a company and shipyard on the Isle of Wight, specialising in aluminium workboats. AMC gave critical input on best practices for shipbuilding, particularly in correcting the guidelines based on ACUA Ocean’s blueprints to achieve better efficiency, structural integrity, and so on.
As a result, the Pioneer-class USV solution is designed for manufacturing, forgoing traditional shipbuilding practices in favour of a modular approach in which different parts of the vessel can be cut, brought on-site, matched and welded together to meet customer needs exactly without sacrificing lead times or cost-efficiency.
“Things like our electrical racks, fuel-cell skids or battery skids can all be built at a separate location, moved to the Isle of Wight and dropped into a H-USV hull, so there’s no conflict of activities that might happen if welding and hotworks were co-occurring with electrical outfitting, plumbing, piping and so on,” Mike says.
“Traditional shipbuilding is long and laborious, whereas modularity of internal systems means things can be quickly rack-mounted and dropped in. It also means repairs don’t entail taking Pioneer out of the water for weeks; a damaged rack or section can simply be removed and a purpose-built one slotted in its place. That increases MRO efficiency and reduces operation downtime.”
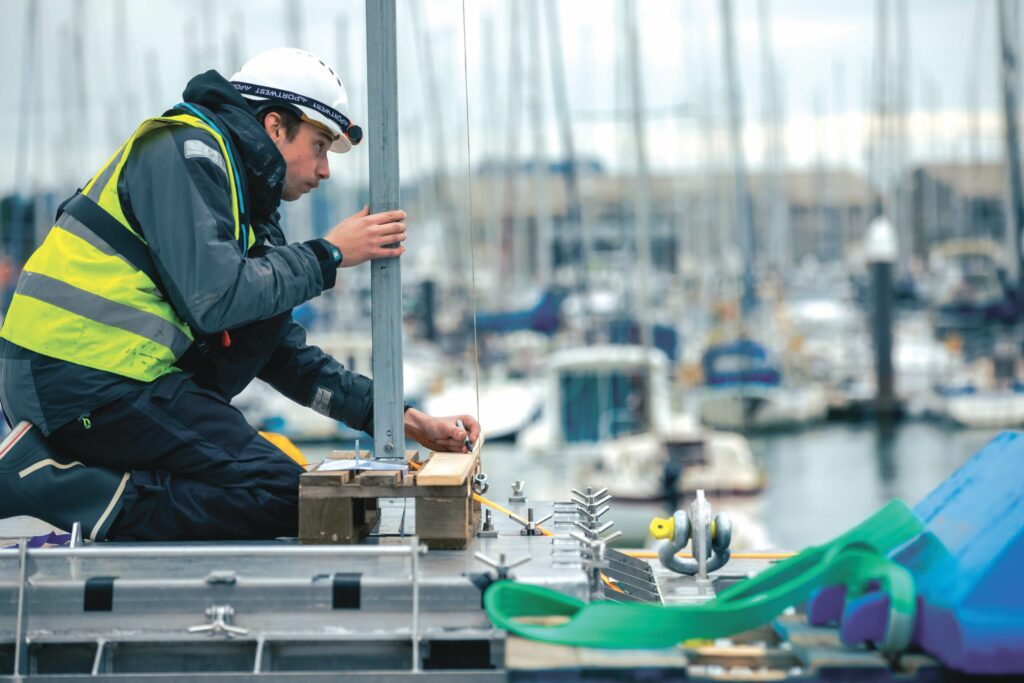
In tandem with AMC building USV Pioneer, ACUA Ocean recruited two naval architects from Babcock International Group to handle the integration and optimisation of subsystems, which sparked a noteworthy expansion of ACUA’s staff. As of December 2024, they number 22 people, up from seven in December 2023.
Naval architecture
The SWATH configuration gives Pioneer a distinctly square shape when viewed from above, sacrificing speed in favour of stability – an apt trade, given this USV’s operating speed of 4 knots (industry-standard ROV survey speeds are 1-3 knots). The shape and high ratio of below-surface displacement to above-surface displacement keep Pioneer’s pitching and heaving to an absolute minimum, giving sonar imagery great consistency and sharpness (as well as camera, Lidar, and other geospatial and hydrographic sensor data).
“Test data has shown we can deploy an ROV amid waves of at least 4 m in height,” Mike adds.
The USV’s deck features a few hatched compartments. One, within the aft transverse beam, houses an electrical rack with all of the control and intelligence systems (behind which is a mast mounting all of the communications systems, as well as some navigation and survey systems).
For redundancy’s sake, a forward electrical rack in the forward transverse beam has redundant systems for communications, power and controllers. The forward rack offers capacity for dedicated payload computers, such as user-defined or -supplied programmable logic controllers (PLCs).
Each of the longitudinal beams holds two additional, smaller, hatched compartments. The two forward ones contain racks for Pioneer’s batteries (supplied by Kreizel in Austria), while the aft starboard one has a fuel-cell rack, as will the aft port hatch in future (a single fuel cell being sufficient for initial demonstrations and deployments).
“For the purposes of the CMDC, we were a hydrogen-electric vessel, and in the long term we think hydrogen will play a huge role in the route to net zero, but for a lot of prospective operators of Pioneer, hydrogen is a foreign entity. They’re interested in what it could mean in the future, but they’re not comfortable with it at the moment,” Mike explains.
“So there will be diesel-electric variants of Pioneer, although still saving hugely on emissions over diesel crewed vessels by eliminating all the extra weight and space needed for sustaining crews onboard. We will provide whatever fuels customers are comfortable with, but, whatever the fuel, it will always be an electric powertrain with a hybrid-fuel range extender.”
Much of the powertrain engineering has been led by Charles Anuyagu, senior robotics engineer at ACUA Ocean, who previously worked on software for Mercedes F1’s power unit development division, enhancing its performance and reliability for the Mercedes-AMG Petronas F1 and Mercedes’ customer teams.
“We’ve two thrusters, one at the back of each pontoon, with rudders mounted behind each for steering,” Anuyagu says.
SWATH vessels
It may seem odd that SWATH vessels are not more prevalent. However, as indicated, their hydrodynamics are not optimal for speed due to factors such as the increased surface drag inherent to their design compared with conventional catamarans, and their inability to plane; the Pioneer thus has a maximum recommended speed of 6.5 knots. Any higher and efficiency losses become significant. So, SWATHs can move adequately for a survey mission, but not so much for, say, sea rescue, interdictions or racing.
“But, more crucially, SWATHs are very difficult to engineer, because they’re incredibly trim-sensitive,” explains Oliver Mulcahy, CTO of ACUA Ocean.
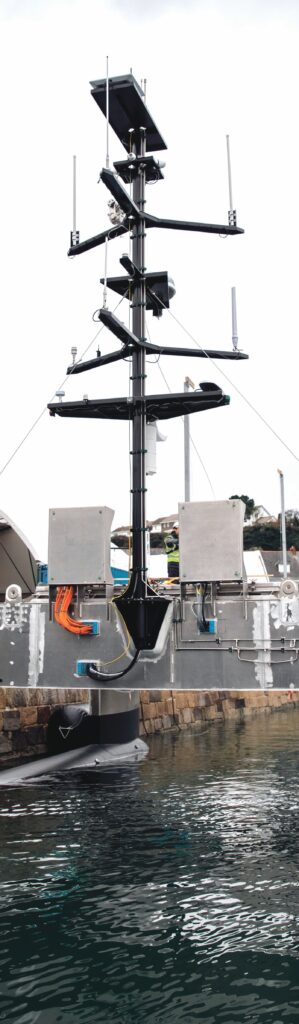
Trim refers to the balance of a vessel in its longitudinal axis between bow and stern, and potential changes in that balance during operation.
“That makes them very difficult to use for crewed vessels, because you have to spend a lot of time optimising the trim of the vessel in a way that accounts for the movement of people. If crew and passengers never moved, that would be great. Better still is if you have no people onboard in the first place.”
SWATHs present certain integration challenges, given how much mass must be placed below the waterline. Mulcahy and Mike proffer the example of how painstaking design would be if Pioneer ran on direct-drive diesel powertrains inside its demi-hulls: one would need to determine the ideal points for inlets and exhaust, and engineer a means for easily accessing the engine for maintenance.
“The ability to store battery energy cost-effectively and space-economically for electric powertrains has been maybe the single-biggest change for marine engineering in the last decade, enabling vessels like ours that are electrically driven, but reasonably agnostic to the energy source,” Mulcahy says. “So, range extenders can be placed quite far from the drive system, sparing us from needing to miniaturise or deconstruct things like fuel cells or ICEs for integration’s sake.”
Despite the non-traditional nature of SWATHs, John Kecsmar’s work on Pioneer began with quite traditional hand-drawings – rather than starting in CAD, such as Ansys, OnShape, SolidWorks and Maxsurf, although these four were later used to optimise Pioneer’s design in combination with lessons learned at Southampton.
To build a ship
Aluminium alloy was used in the early scale prototyping phases due to its workability: it can be bent or cut to enact iterative changes, even if one has already riveted it onto a chassis, with little impact on structural integrity. ACUA Ocean had then intended to switch to composites for the final build prototype seen today, but pivoted back to aluminium alloys after the benefits of working with AMC convinced them to do so.
“AMC has just about the best reputation in the UK as a combined shipyard and consultative partner. Our design evolution hasn’t been an easy, straight line, and them having the know-how to support and validate our design corrections isn’t the only good thing,” Mike says.
“They’ve also been very open and willing to learn with us through the grey areas along the way, which is crucial given how much of Pioneer is unusual, veritably ‘pioneering’ technology.”
Most struts and panels of aluminium are bolted or welded together. The latter has been performed by coded welders to ensure MCA approval of the structure, with ACUA working with Lloyd’s Register to ensure routine surveys of the build.
“The bigger, wider sections are welded together, while bolts feature most prominently in our patches and in elements of the transverse beams,” Anuyagu says. “That enables us to look very closely at those individual parts of the vessel when we need to, and bolts are amazing things for load transfer in operations, so it makes sense to use them in those otherwise stressed sections.”
Pioneer’s two pontoons and four struts were constructed to specifications first, largely from cut and shaped aluminium; their build commencing in March 2024, following the conclusion of their designs in February. The transverse and longitudinal beams followed.
The powertrain had been designed and prototyped to the scale of the full build earlier to validate mission-critical parameters such as high-voltage charging and discharging. The power subsystems such as electrical racks and skids were co-developed and built with Trident Marine Electrical. Electronics such as navigational and C5 (command, control, compute, communications and cybersecurity) systems were then selected, and plugged into the power network.
“There wasn’t much cable management or integration work back then as there was no vessel to put it all into, but we still needed to test all that hardware and optimise all our code to get the system working, from powertrain to compute systems,” Anuyagu recounts.
“So, once we were satisfied that safety and performance could meet code requirements, we packed everything into a freight container and sent it here, to Plymouth. From September, we began the work of mounting its parts and routing cables inside the built vessel.”
The view from the top
The USV’s capacity to survive at sea has depended on rigorous testing and redundancy. As an example, Anuyagu notes: “Recently we’ve been doing bilge-pump testing. In a crewed vessel that means you just flick a float switch and you look to see if your bilge pump has come on; that’s a closed loop.
“But, turning on the bilge pump in an uncrewed system requires automated elements in the PLC code, because there’s no-one onboard to look and confirm if it’s working. First, the USV must recognise the input, then you need it to correctly respond by switching on the bilge pump and, most critically, the system then has to send the current needed by the bilge pump all the way down the line. So there’s multiple stages that need to be examined if the pump doesn’t activate.”
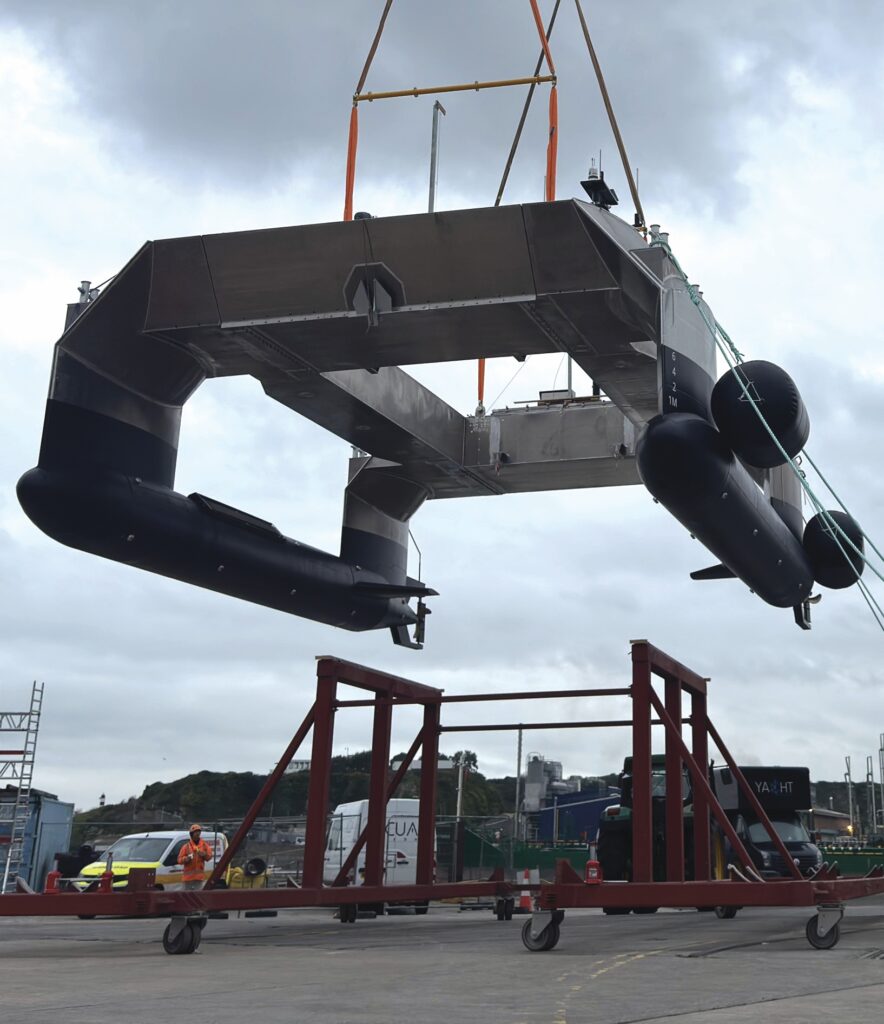
Hence, there is scepticism over the ability of USVs to work consistently at sea without ever needing someone to check on them, and the prospect of having to mount a crewed mission to go out, find and retrieve a malfunctioning USV is a sobering one to move past.
The mast atop Pioneer’s stern is the most outwardly visible of ACUA Ocean’s countermeasures against such scepticism, with a multitude of redundant systems for navigation, communications and maritime safety.
“We’ve got a Teledyne FLIR EO/IR camera that sits atop the mast for above-water survey and situational awareness, and moving down you see a Starlink high-performance flat panel for high-bandwidth satcom,” Mulcahy says.
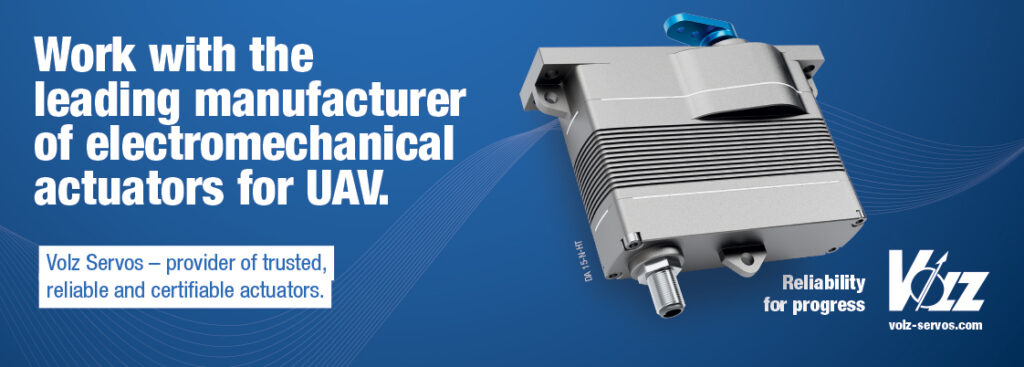
“Below the Starlink is a suite of fixed cameras from Garmin, facing all different directions and mounted on a set of three-way, yard-armed spreader bars. Down from that is a Redvision camera for providing both daytime CCTV and also a spotlight functionality, both of which will help a lot with self-surveillance, checking for issues on our own vessel, even for seemingly trivial things like accidentally dragging a lobster pot behind us, as those can and have downed USVs crossing oceans before.”
Those cameras bring the added benefit of amassing training data, with copious real-world, in-context video and imagery for training future AI systems to be used on Pioneer-class H-USVs, and others.
Three antennas sit about the Garmin cameras. One provides a Class A AIS link and the other two are VHF antennas: one connects to a Digital Selective Calling radio, and the other to a Channel 16 Dual Watch radio (both being established radio protocols for distress and safety messages at sea).
“Moving down, we have a Simrad radar – a HALO24, specifically – and below again is a second three-way spreader bar, which mounts a 4G antenna, a wi-fi antenna and an Airmar 200WX weather station,” Mulcahy says.
“Fuel cells are well-established among automotive groups like Hyundai and Toyota, but the marine context is very different from the automotive context, and it’s hard to find maritime fuel cells outside of giant, megawatt-level systems way oversized for our needs,” Anuyagu says.
“As well as giving us our on-location weather data, the 200WX integrates a GPS radio, as well as a three-axis gyroscope and accelerometer, thereby acting as a secondary source of heading, pitch and roll information.”
Slightly inboard of the 200WX is a small UHF antenna for LOS operations, and underneath that spreader bar is an array of localisation devices. While ACUA Ocean tries to stay agnostic about navigation suppliers (as almost all maritime customers will have their own specific, individual attachments to one navigation supplier over another), the USV Pioneer is carrying a Hemisphere Vector V500 GNSS Smart Antenna, a magnetic heading compass and a NavtechGPS system, at least for its initial sea trials.
Level 3 autonomy
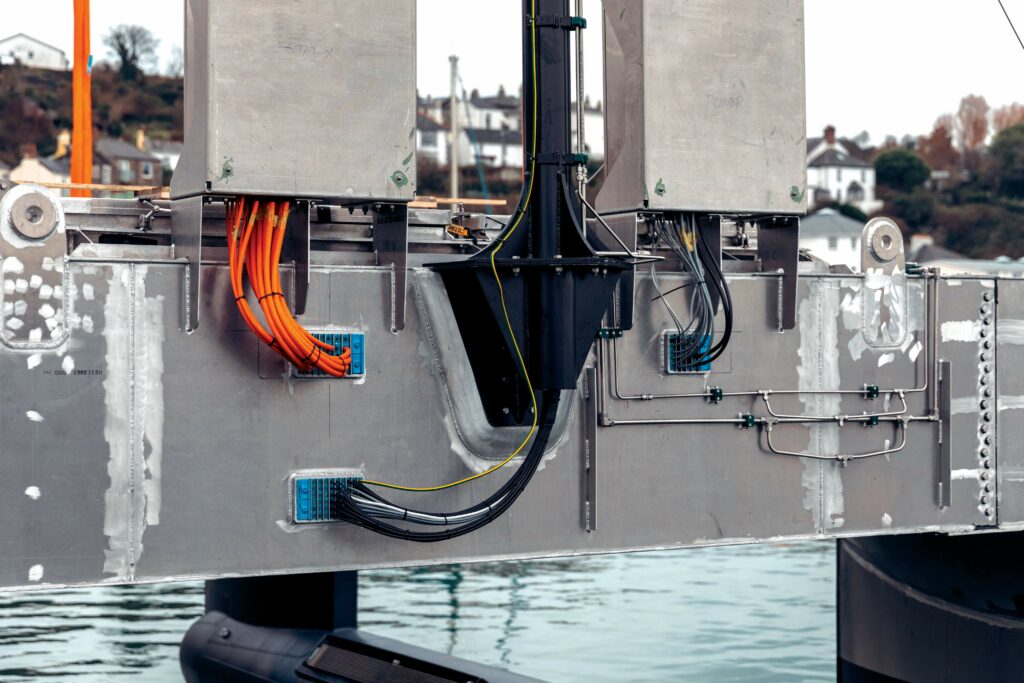
To conform with safety regulations, the Pioneer-Class will initially be operated at Degree Three of the International Maritime Organisation’s Maritime Safety Committee’s regulatory framework for maritime autonomous surface ships (MASS). This means it will be able to handle itself and most onboard safety-critical systems in most instances, with an operator in-the-loop to monitor its missions at all times and step in to take control where necessary, but under virtually no circumstances will personnel be present onboard the MASS.
“That’s geared our onboard control architecture, as IMO Degree Three still requires considerable computer hardware, but, fortunately, the Robosys control software we’re using comes with an OEM-recommended compute unit,” Mulcahy says.
Centralised control of Pioneer’s functions rests with two main computers. The first is ACUA’s C5 module, which is Linux-based and connects via four different CAN buses to most subsystems. It runs ACUA’s proprietary remote software (built around a NATS infrastructure-based middleware), and is passively air-cooled to avoid adding surplus motors and pumps.
The other main computer is the powertrain control unit delivered via Robosys Automation, which is a Windows-based system running a bespoke derivative of Robosys’ AI Survey software and connecting to the various powertrain components via a dual redundant CAN bus.
Moon pool
The moon pool is designed with mounting points for standard ISO blocking arrangements, enabling anyone with an ISO container or payload they would like to install in Pioneer to pull up the ISO standards, find the spacing and adopt it to drop their system into the moon pool (including mechanisms for lowering payloads, ROVs and so on into the water, as well as retracting or recovering them similarly afterwards).
“As Pioneer is mostly aluminium, the degree of aluminium needed to support ISO containers across the span of the moon pool would’ve been enormous, so we built the mounting booms from steel, which in turn means a galvanic mismatch because now there’s aluminium and steel in contact,” Mulcahy says.
“But, once you recognise the problem, it’s just a matter of using appropriate galvanic isolation and protection measures, such as rubber sheeting or other materials, as well as a shorter maintenance survey interval to make sure the mitigation is holding up.”
Detailed FEA simulations and studies have helped understanding and design optimisation of how loads carried in the moon pool are transmitted through the hull, as well as affirming that weight significantly exceeding the 6.5 t payload capacity can be handled by the structure amid extremes of sea states and movements in all three axes (wave-tank testing having played a key role here).
“At the back end of the frontal transverse beam there’s an empty gland – a fire-rated, pressure-rated, gas-tight frame provided by Roxtec for wire management in a sealed manner through bulkheads – which can be used to electrically connect payloads to the forward electrical rack, with space and weight provision for up to three racks of equipment, such as computers for running payload systems,” says Mulcahy.
Hydrogen systems
ACUA Ocean’s initial approach for the storage and delivery of hydrogen will involve placing a hydrogen storage unit in the aft region of the central moon pool area. The unit is a modular frame that can hold up to nine cylinders of H2 stored at 350 bar (each cylinder holding up to 10 kg or 333 kWh of hydrogen gas), although just three cylinders are installed for the first sea trials.
Gas travels from the module via a connection through the starboard-aft quarter to the fuel-cell supply valve, entering the fuel cell at approximately 7-8 bar; that fuel cell being a bespoke unit from US-based Nuvera.
“Nuvera were very open to our concept, and the 45 kW net power output of our fuel cell fits our power delivery needs exactly, giving us plenty of capacity for extra payload systems in the future. Their tech is also very efficient, hitting 58% thermal efficiency, whereas most fuel cells are still only doing 50-52% at best.”
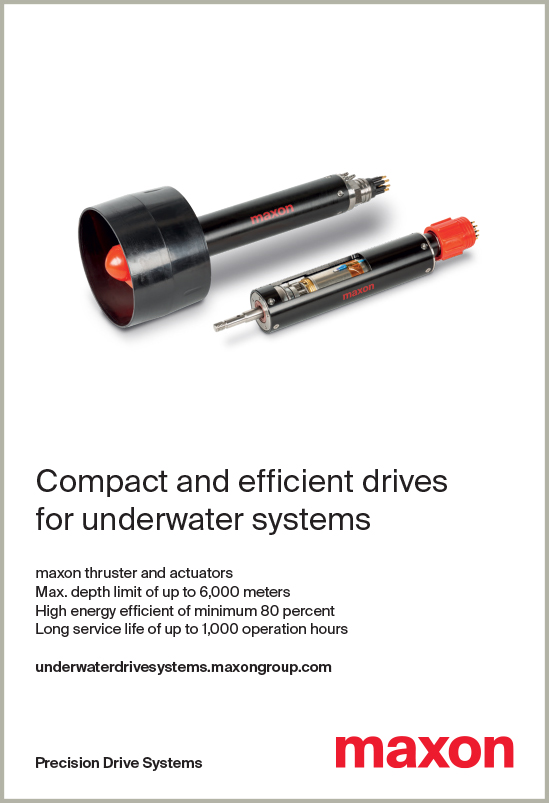
Batteries and electrics
The two main battery packs are Kreizel units, running on 21700-type, lithium-ion, cylindrical cells, with each pack containing up to 63 kWh and providing a 400 V supply to the powertrain.
“They’re very high-performance batteries, and I consider them equivalent to motorsport-level systems I’ve seen. For example, they can discharge up to 250 kW for 10 seconds, which can be useful in certain emergency or application-specific contexts, but most important to us is their 400 V DC bus and that their modularity enables them to be strung together in groups of many,” Anuyagu says.
“Long-term, if we or a buyer wants to expand that electrical energy storage, in Pioneer or a larger class of H-USV, the battery architecture can be easily scaled up, and the control system doesn’t change. An individual CAN bus connects the two packs together, such that they’re treated as one battery. The operator doesn’t see battery one and battery two; they just see one battery capacity.”
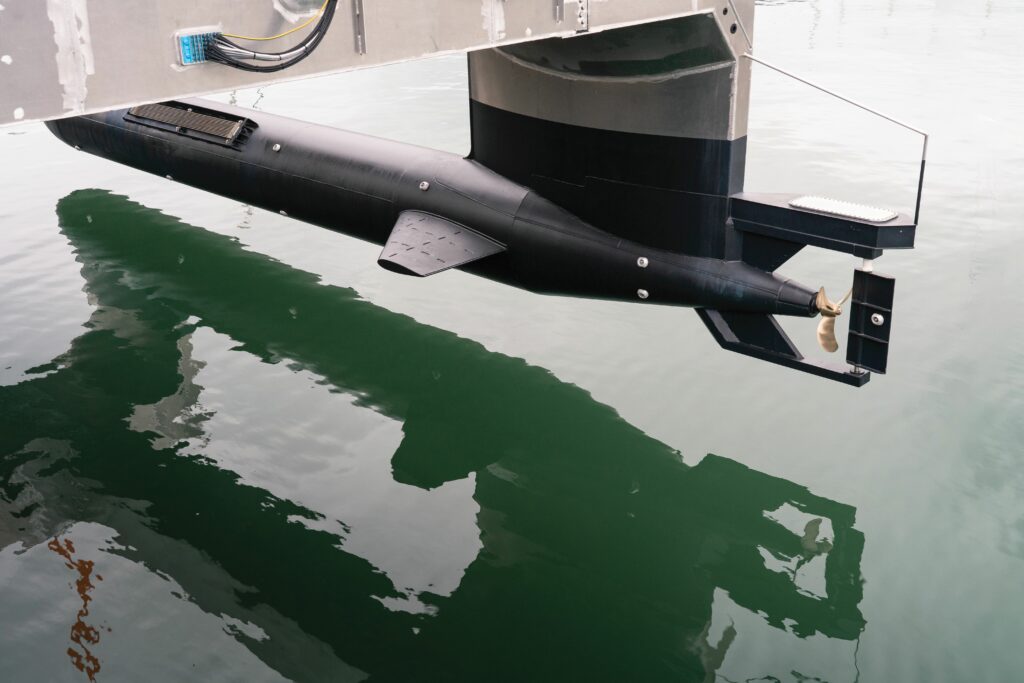
The vessel’s control systems and various other electronics run off a lower-level, 24 V bus, enabling compatibility with the 10-30 V range of most of the USV’s non-powertrain subsystems.
Two battery packs from Victron Energy sit in the electrical racks and power the 24 V bus – one in the forward rack and one in the stern rack – even though each battery is capable of powering both racks. Each Victron pack is a turnkey, COTS system, built around LFP cells, and it has its own BMS and sensors.
Thermal management
The efficiency of the USV’s components, along with being surrounded by splashing sea water, means that most active cooling is only required when the batteries are being charged.
“Usually, you think of battery discharge being a huge source of heat, but because we want to fast-charge at 22 kW using a three-phase AC input that actually creates more heat than the vessel in operation,” Anuyagu says.
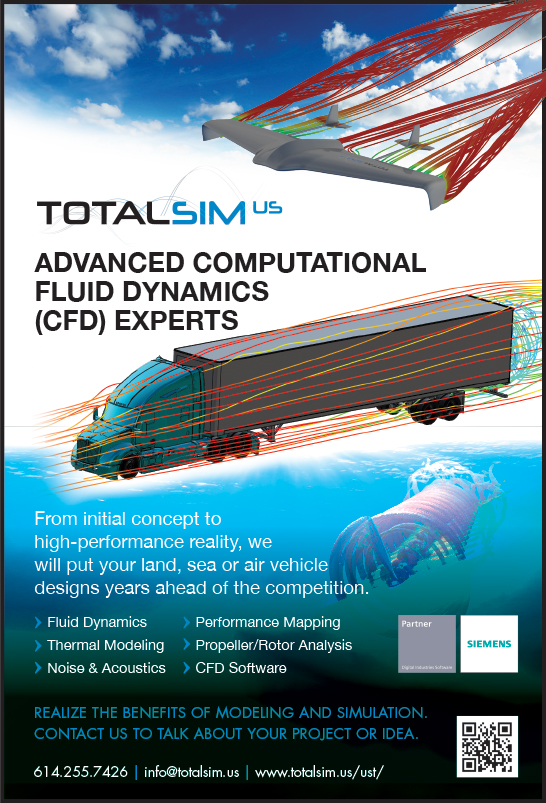
“Each battery has its own primary, water-glycol cooling loop, which connects to a dedicated heat exchanger and a wider vessel-cooling loop; the latter, wider loop rejecting heat via a keel cooler.”
As of writing, the keel cooler is scaled for optimal performance in sea water temperatures of 20 C (globally, they rarely exceed 25 C), but such is the thermal headroom of the two primary cooling loops that the keel cooling loop will mainly be needed when customers are maxing out the power consumption of the onboard subsystems.
“Modularity depends on a solid foundation for the modular ‘Lego blocks’ to be stacked upon, and the cooling systems are a big part of that foundation in that they’re not modular, they’re rigid, and they’ll stay as they are because they’re what allow us to put the various other systems onboard,” Anuyagu says.
Thrusters
Through early system-wide analysis, Mulcahy identified the propeller as the highest potential source of efficiency losses: a 50% efficiency rate is typical with a decent propeller, whereas most onboard electrical and electronics perform with over 90% efficiency.
“Hence, I focused on finding something highly efficient at the speed we picked, and we picked it on the basis of ‘must, should and could’. Our ‘must’ was 4 knots, our ‘should’ was 6 knots and our ‘could’ was 8 knots,” he recounts.
It soon became clear that fixating on 4 knots and striving for 6 knots would be suitable for Pioneer’s drivetrain. After researching market solutions, ACUA Ocean decided that CJR Propulsion understood its requirements and matched its speed profile with a highly efficient propeller design, borne out of hundreds of simulation runs and manual adjustments of simulation models.
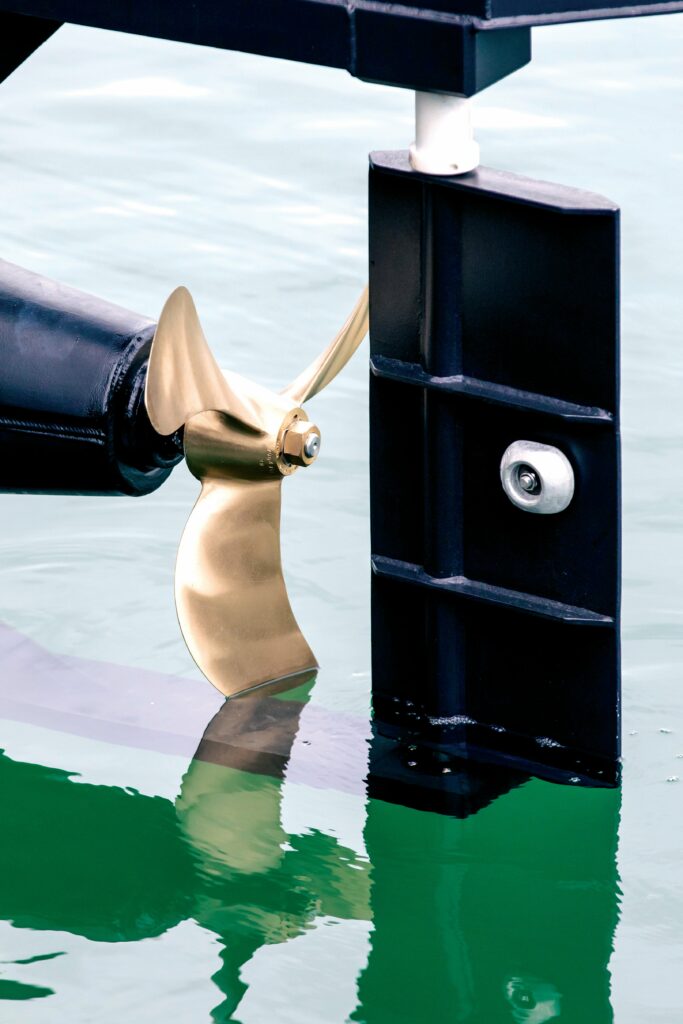
“Then, CJR made use of an incredibly well-refined manufacturing process, heavily utilising robotics first to cut the moulds before they’re used for casting the propeller parts in a foundry,” Mulcahy says.
“The rough-cast elements that come out of that are already quite precise, because they’ve been produced by Kuka robots in CJR’s factory, but they’re then put into a five-axis CNC machine and milled down to an incredibly precise and hydrodynamic finish. That gives us a propeller that is just over 70% efficient, which has very dramatic benefits for the endurance of the vessel, potentially making the difference of tens of days of endurance, depending on the type and quantity of fuel.”
Forward from each propeller is a standard assembly of propeller shafts with thrust bearings and stern seals. The propulsion assembly enables differential thrust, with a 9 m beam that enables Pioneer to rotate approximately around its centre. Each propeller is driven by an axial-flux electric motor, outputting roughly 60 hp (44 kW) in normal operation or up to 124 kW at peak. A rudder adds steering redundancy in the event of the loss of a shaft.
“Axial-flux motors are incredibly compact, and one of the highest energy-density propulsion configurations available, which is important as it gets quite cramped inside the demi-hulls,” Mulcahy says.
Over the iron sea
Following its first trial deployment in December 2024, ACUA Ocean plans to rapidly accumulate further trial hours on the waters outside Plymouth, and continue working with current and new partners to demonstrate payloads, as well as other technologies, in 2025.
Beyond 2025, this will include any new developments in liquid hydrogen that come along. While technical advancements and commercial confidence in liquid hydrogen will need to accumulate (with diesel and even gaseous hydrogen being far more widely used and trusted than liquid hydrogen, as of writing), it remains a guiding star in ACUA Ocean’s ambitions to produce world-leading zero-carbon USVs.
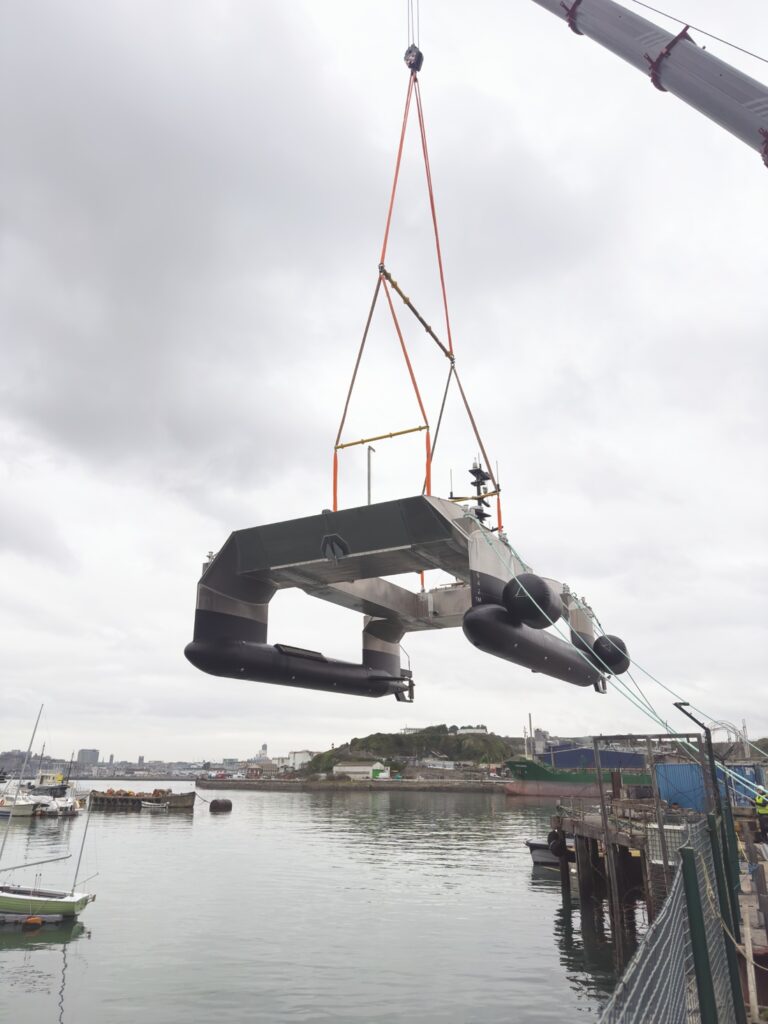
“But, even if Pioneer is offering capabilities that have never been available before, customers always ask for more. We’ve already teased about our Maelstrom concept vessel, which is slated to be a 24 m-long sibling to Pioneer, and we’re going to learn a lot in the water that informs future designs, workarounds and subsystem selections, which will feed into bigger H-USVs,” Mike says.
Once sea trials are completed (probably by close of Q1 2025), commercial sale and deployments of Pioneer-class USVs are expected to commence. Going forwards, in addition to expanding the physical shape of Pioneer, expansions of its autonomy and control capabilities are anticipated.
“Right now, one operator and engineer will be consumed with operating one Pioneer, which is a significant return over a crewed vessel and the potentially dozens of people needed for one of those,” Mulcahy says.
“But we hope to reduce the cognitive load on operators to the point that one operator-engineer pairing could run two, three or four vessels. As we move from IMO Autonomy level three to level four, possibly releasing update packages of helper functions in a ‘level 3.1, 3.2, then 3.3’ manner, the two personnel could start to sit back more and more, intervening solely when there are anomalies the USV can’t address itself.”
While naval vessels often have decade-long lead times, often meaning subsystems that are 10 or more years old, ACUA Ocean anticipates narrowing that gap, thanks to the agile, modular way that the H-USVs are manufactured and scaled.
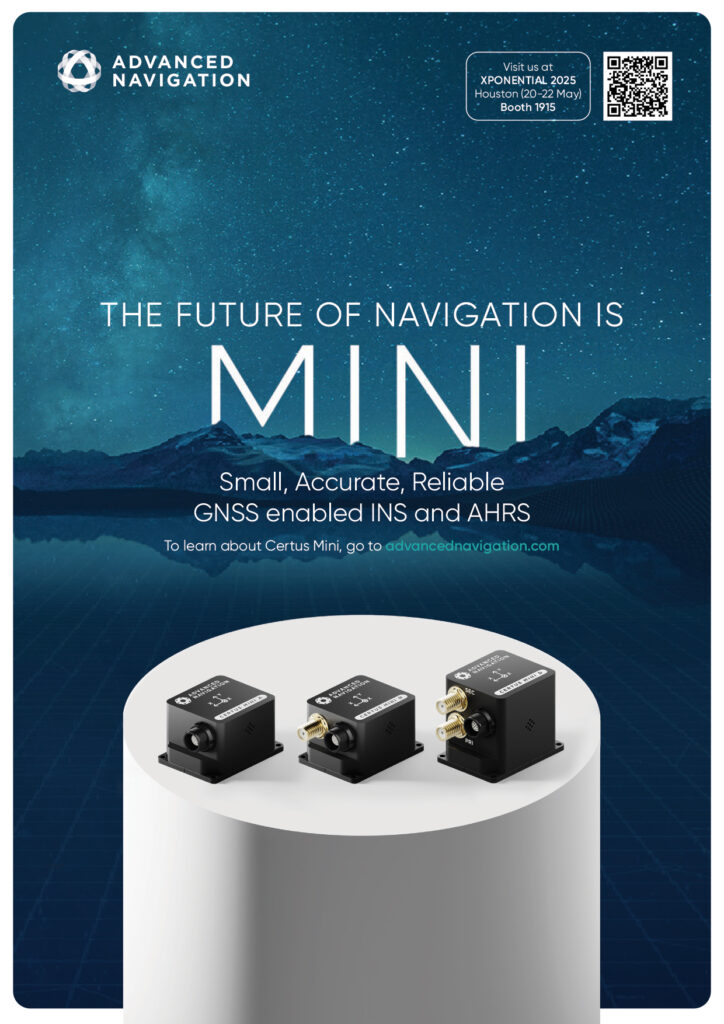
“We don’t see the Pioneer-class being built as a few batches of one or two units. We’re growing a company that will be capable of fielding hundreds of these vessels across dual-use cases and more complex multirole operations,” Mike says.
“In the North Sea, for instance, they’re not allowed to launch or recover ROVs when there are waves of 2 m or higher, which gives only 120 days of survey opportunity around Orkney and Shetland.
“By operating safely in waves of 4 m and higher, we widen the available survey time to over 250 days each year in sea states up to 3 m. That’s an absolute game-changer in these time- and
cost-sensitive industries, and it’s only going to get better from there.”
Key specifications
Pioneer-class H-USV
Small waterplane area, twin-hull (SWATH)
Aluminium vessel (with steel moon-pool booms)
Hybrid-electric (including hydrogen fuel cells)
Length: 14.2 m
Beam: 9 m
Draft: 1.6 m
Height (including mast): 8.1 m
Maximum displacement: 25.7 t
Payload capacity: 6.5 t
Moon-pool capacity: 6.5 m x 3.8 m (accommodates a TEU 20 ft ISO container, or two 10 ft ISO containers)
Maximum speed: 6.5 knots
Operating speed: 4 knots
Endurance: 18 days on H2, 50 days on diesel (4 knots average speed)
Some key suppliers
SWATH engineering consultation: Ad Hoc Marine Designs
Vessel design and construction: Aluminium Marine Consultants
Vessel automation and control software: Robosys Automation
Hydrogen fuel cells: Nuvera
Batteries: Kreisel
Batteries: Victron Energy
Electric power distribution systems: Trident Marine Electrical
Electric drive systems: RAD Propulsion
Propellers: CJR
Keel cooler: Kort
Keel cooler: RW Fenstrum
Cable glands: Roxtec
Weather sensor: Airmar
Radar: Simrad
PTZ cameras: Dupre Marine
EO cameras: Garmin
CCTV and spotlight cameras: Redvision
IR cameras: Teledyne FLIR
Video-streaming: Videosoft
UHF data link: Fort Robotics
UPCOMING EVENTS
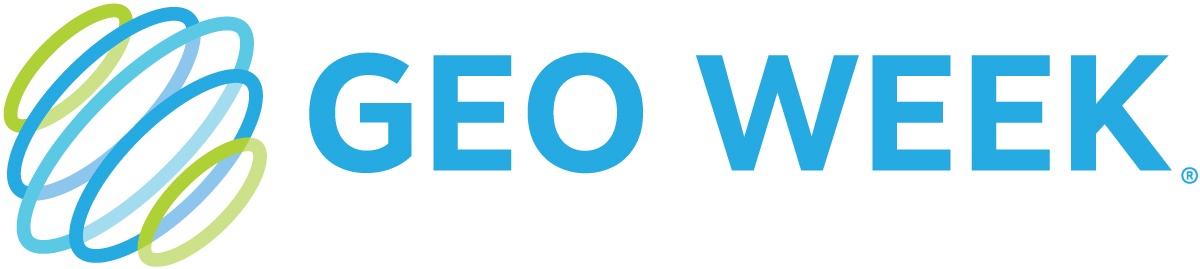
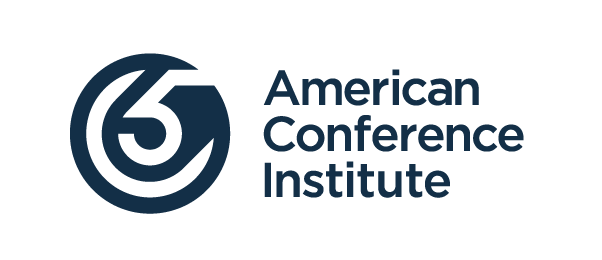
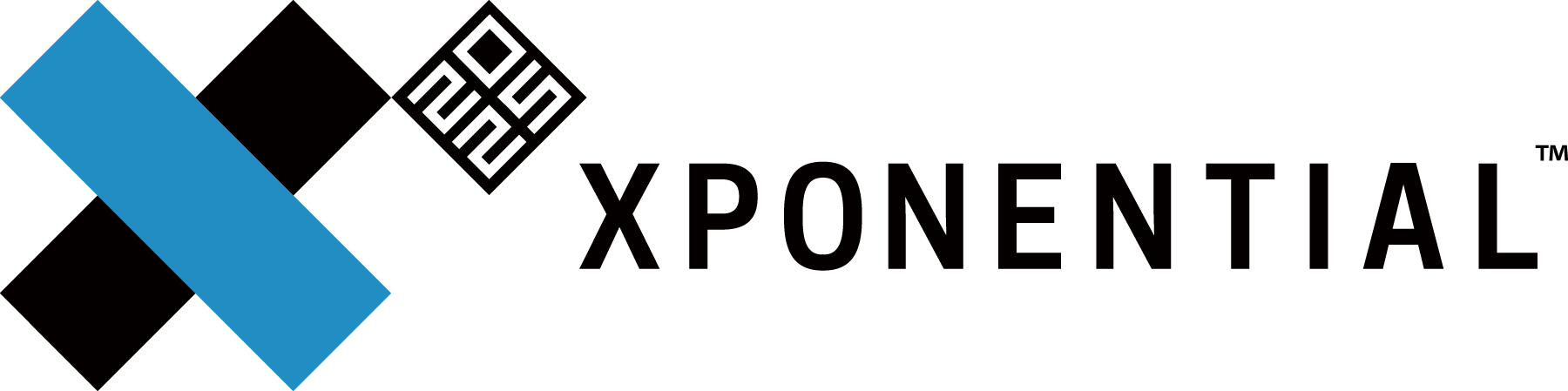
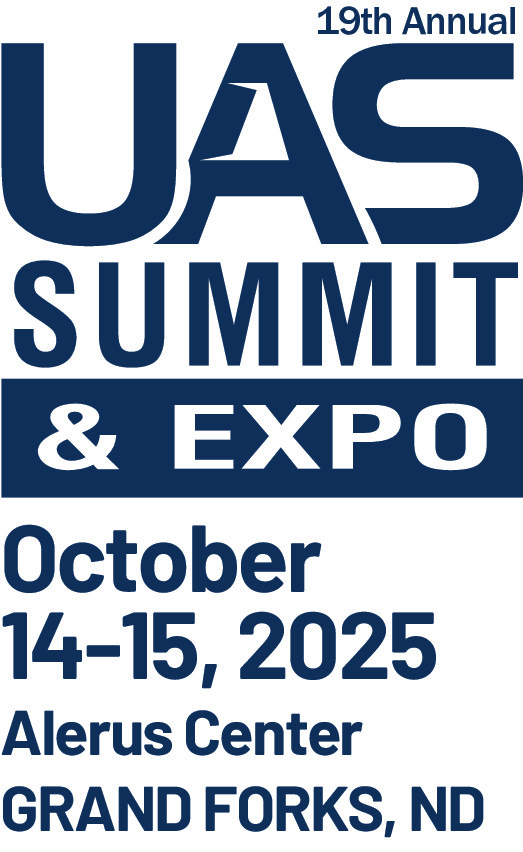
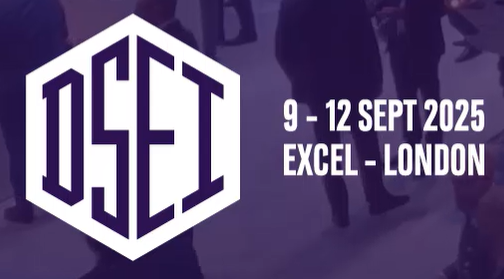
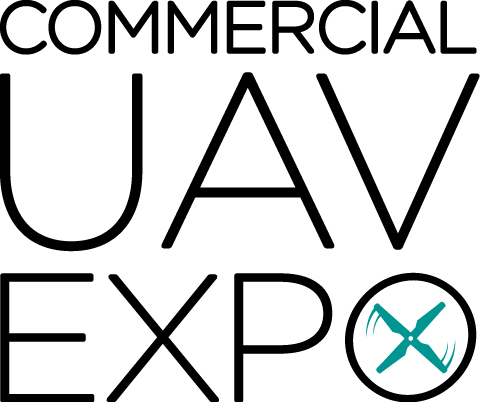
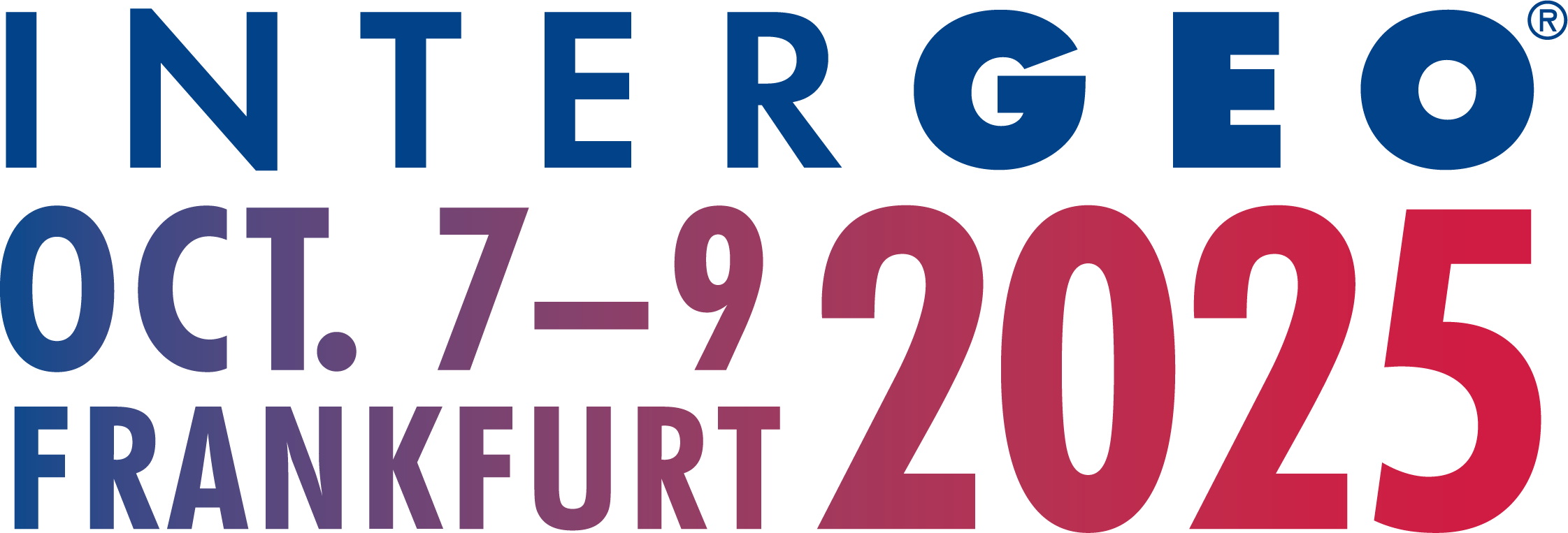
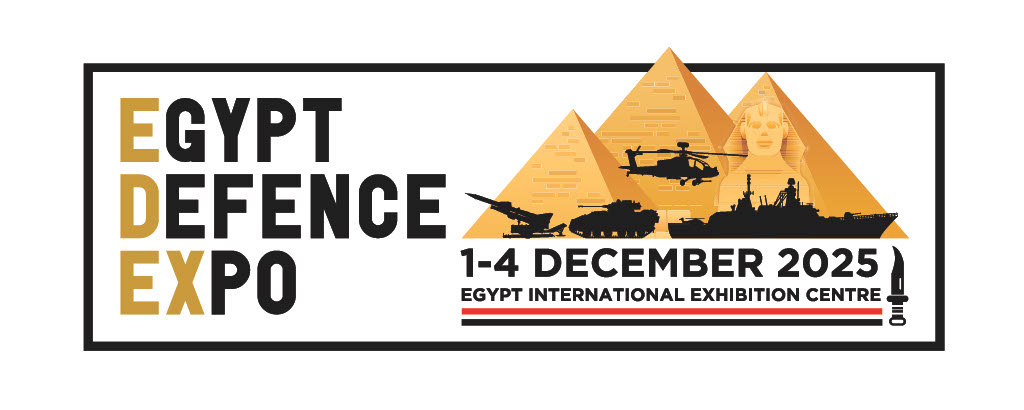
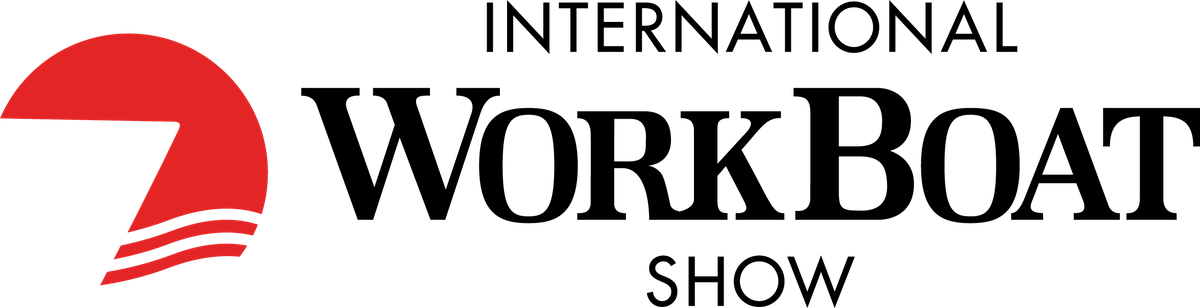
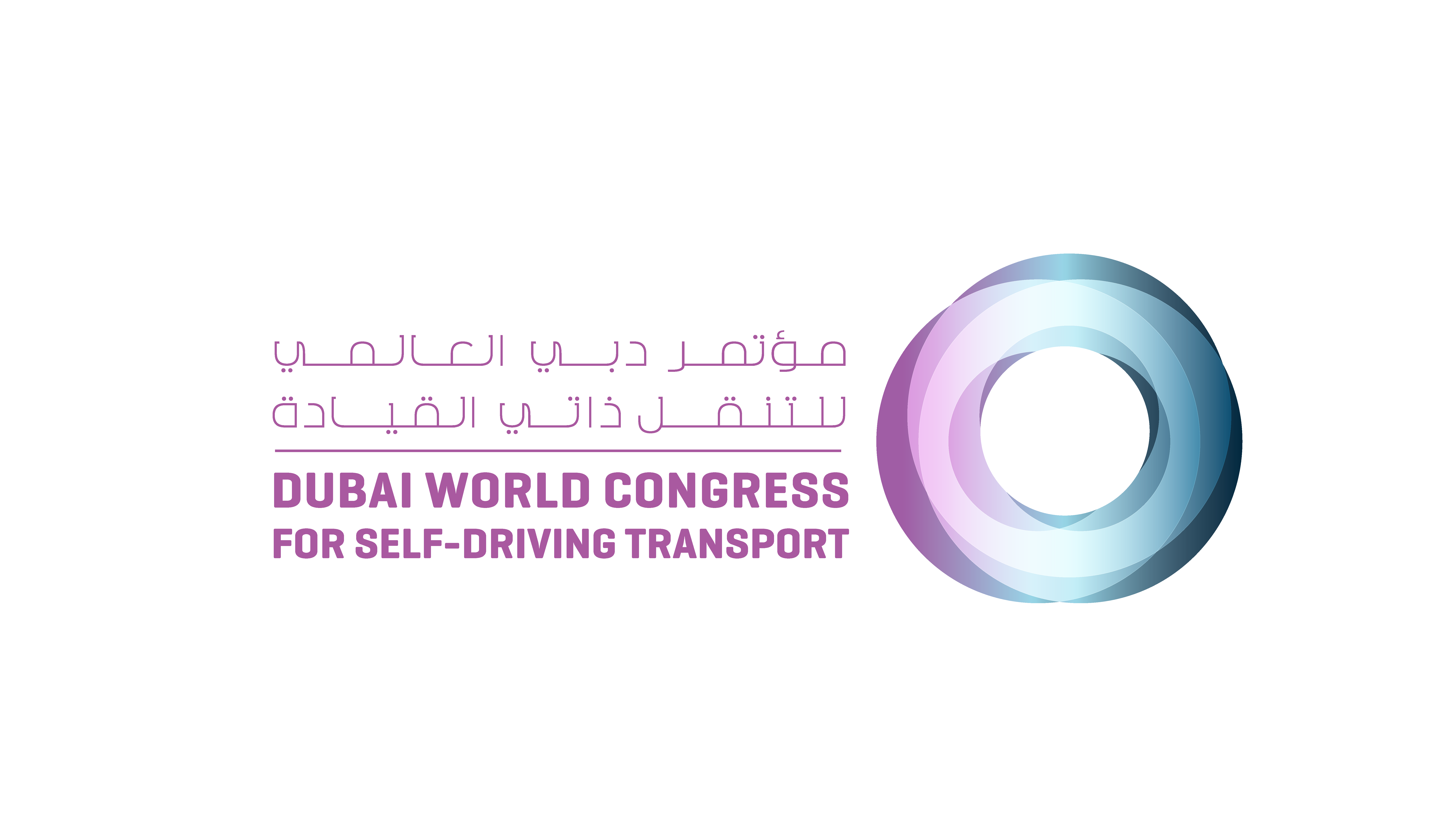
