Roboat & Holland Shipyards Group
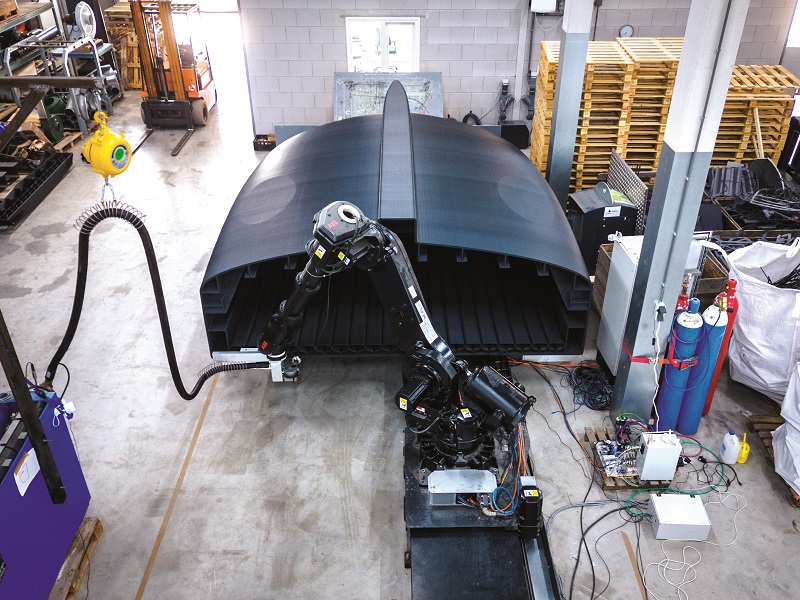
A newly built autonomous vessel is poised to ferry Parisians, Olympics athletes and tourists this summer, reports Rory Jackson
Four years ago, we covered the work being performed by Roboat, a Netherlands-based spin-out from MIT and the Amsterdam Institute for Advanced Metropolitan Solutions (AMS Institute), to develop its eponymous uncrewed service vehicle (USV) for applications including autonomous waste logistics and water taxiing through the canals of cities such as Amsterdam (Issue 31, April/May 2020). Since then, the company has continued to specialise and mature its USV designs for those use-cases, while also seeking new, tangible ways of applying its body of technical knowledge.
The most recent to catch its eye was a tender published by VNF (Voies navigables de France), the navigation authority responsible for managing most of France’s inland waterways and associated facilities, for an autonomous ferry to transport pedestrians across the River Seine during the upcoming Paris 2024 Olympics.
“We saw this as not just a way to demonstrate the precision and reliability of our technology in autonomous waterway navigation and collision avoidance, but to also do so in an application that was actively being demanded by a municipal body,” says Joshua Jordan, co-founder of Roboat.
While the Roboat water taxi provided a number of key design and functional inspirations for the type of ferry that could work, the project needed to result in a significantly larger vessel.
“To ensure a sufficiently large and professionally built ferry, we leveraged some prior connections with Holland Shipyards Group (HSG), a very seasoned boat and ship builder, who soon agreed to partner with us on the project as its constructor and main integrator, with Sequana Développement coming onboard soon after for key consultation and managing commercial operations of the boat,” says Jonathan Klein Schiphorst, co-founder of Roboat.
That autonomous vessel has now been built and is poised to transport Parisians, Olympics athletes and tourists alike starting in the summer. The boat, nicknamed ‘Tony’ as of writing, is a 9 m long, 3.9 m beam, 1.7 m draft, 3.1 m air-draft monohull. It displaces 9.5 t, provides seating for 35 passengers and moves through the water at 12 kph.
Movement comes from a fully electric and hence zero-emissions powertrain. Perhaps most unusually, the ferry’s structure and body have been manufactured predominantly from recycled plastic through the use of large-form additive printing.
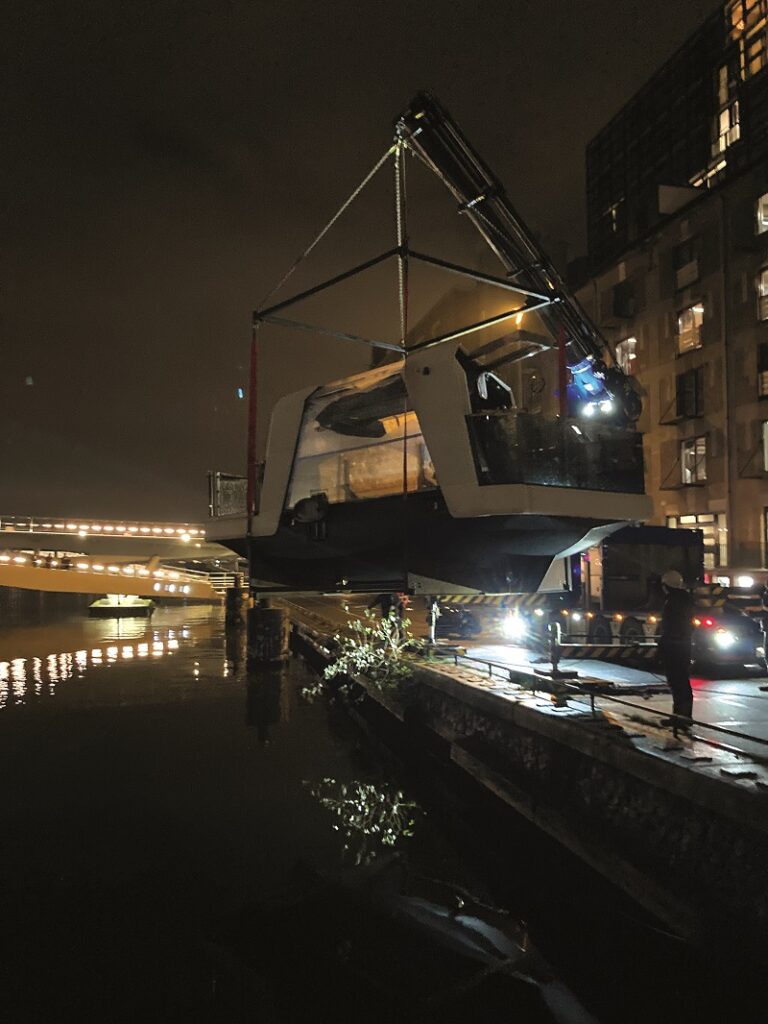
Project history
Using the small Roboat autonomous water taxi as a design basis, HSG broadly took responsibility for the mechanical manufacturing and assembly of the boat, including integration of most of the components, with Roboat providing critical input on the sensor- and software-related aspects key to the boat’s autonomy and control.
“Our normal process for designing a vessel is something we call a ‘design spiral’. We take into account the requirements for hydrodynamics and structural stability, and lay out steps for specifying and fine-tuning those into a circle, such that we go around the circle, and sometimes we go around again multiple times to really minimise resistance, instability, weight and other key points,” says Tim van den Heuvel, research & development manager at Holland Shipyards Group.
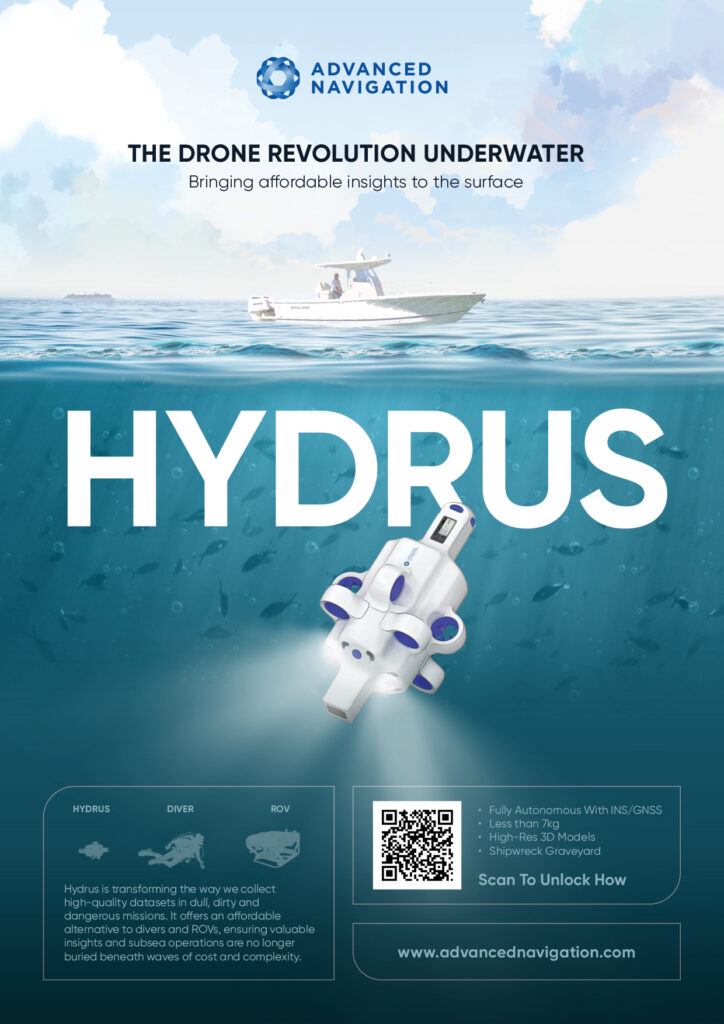
“Some key aspects, like the propulsion configuration, for instance, took key inspiration from what the Roboat team already had on its small water taxi, which is very unconventional for medium and larger vessels in that the fixed thrusters are positioned mid-ship on the port and starboard sides, with additional bow and stern thrusters.
“It’s more like a multirotor drone than any normal operational boat, but the end result is that the ferry’s reaction time and control response can be faster than regular boats using this propulsion setup.”
The electrified aspect of the powertrain was not new to HSG, as the Dutch shipyard had previously built several dozen fully electric ferries. Once the structural and electric parts were installed, Roboat was able to integrate its autonomy-related computers and sensors with the electrical subsystems.
Production of the boat began in September 2022, to meet the deadline for submitting the design in the following month. The verdict, in Roboat and HSG’s favour, came in December, followed by official signing of the tender in May 2023 (although HSG began designing and prototyping very quickly, in the week after the verdict).
“By May, we had already discussed the idea of 3D printing the vessel quite a bit internally,” van den Heuvel notes. “In the beginning, we had thought to build it conventionally from steel or aluminium, but, given the potential for labour cost and time savings, we thought additive manufacturing could be really interesting. It was a totally new technology and use-case for us, as a shipyard, but that just meant it presented huge learning opportunities, which could be used in the future.”
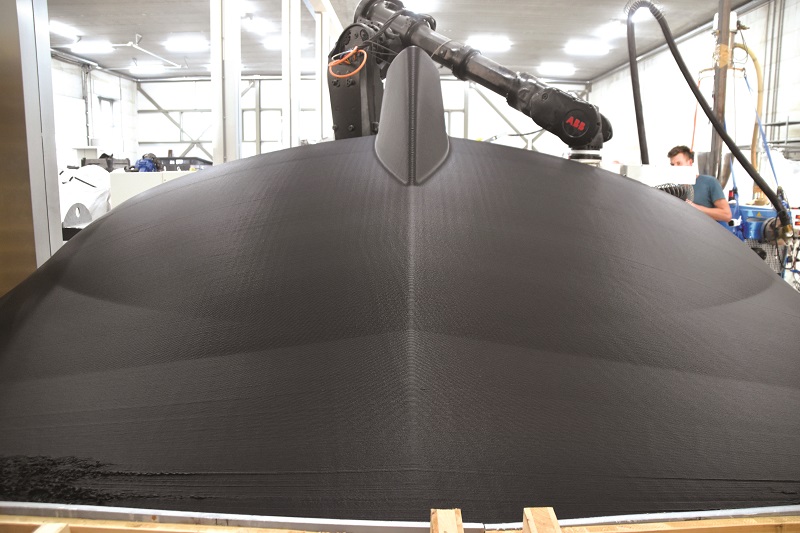
Printing process
HSG’s usual design spiral was performed with some additional constraints specific to additive manufacturing, such as the dynamics of printing machines, the forms that the edges of printed parts can take, and the inability to use certain types of extensional forms.
“We started looking for large-component additive-printing companies, and luckily, in our backyard in Hardinxveld there is such a company, by the name of 10XL,” van den Heuvel says.
“The structural design needed to be adapted to their printing machinery and processes, and you have to be careful and precise when you’re printing really huge parts running the length and width of something like our ferry design, because there’s a lot of shrinkage of the material as it cools following extrusion. You don’t just hit the print button – you have to pay close attention to see if the material contracts and sets as hoped.”
In the end, 10XL successfully printed all of HSG’s parts to the tolerances requested, with the design process for the prototype having taken between two and three months.
The smallest 25% of the ferry’s pieces were printed first, and these were then tested using a variety of methods (including destructive testing). These parts included the thruster foundations, as HSG wanted to integrate the thruster with a round flange, and hence sought to investigate how well that flange could be joined to the hull.
“To do that, we printed a flange, made it watertight and welded it to a vessel hull part, before carrying out destructive testing of those welds to see how much force and what kinds of forces the material could overcome,” van den Heuvel says. “In the end, we did a lot of testing of the material and the different hull parts before moving to printing and assembling the first complete vessel.”
Key standards on testing methods and strength requirements for the structural parts of vessels have been published by groups such as Bureau Veritas and Lloyd’s Register Group, and this provided some guidance for HSG to follow. However, such standards have yet to take strict account of the kinds of materials and processes leveraged in 10XL’s printing.
In the case of the Tony ferry, these were recycled polypropylene and fused deposition modelling (also known as fused filament fabrication, or sometimes just material extrusion additive manufacturing), which are still largely new to the boat-building world.
“We set up some tests in collaboration with the Dutch Transport Agency, which was responsible for certifying the ferry, because if, like us, you want to carry more than 12 passengers, you have to be certified under their transport rules. We also made use of Bureau Veritas’ rules and regulations related to HDPE [high-density polyethylene], as HDPE has quite similar mechanical and chemical properties to polypropylene,” van den Heuvel explains.
For added strength and stiffness, the polypropylene is combined with chopped glass fibres (at a 70/30 ratio of plastic to fibres) and printed as fibreglass.
“The glass granulate is also provided by recycling companies, and it sits in a sort of large hopper above the printer, such that, like the plastic, it is partially melted before entering and then leaving the extrusion head,” says van den Heuvel.
“The whole hull can be printed at once, in about 10 days, with some parts, such as the thruster foundation, printed separately, and we add some polypropylene brackets to those for welding them to the hull. The welding process was no different to our usual way of working with such plastics, so the fact that we were joining 100% polypropylene brackets to 70% polypropylene-fibreglass composite showed zero adverse effects and merited no changes to our welding technique.
“The boat thruster tunnels were made from a polypropylene pipe and welded into the hull. Printing such perfectly round structures is still a bit difficult for additive manufacturing machines, even if you want to print them separately and fit them into your hull afterwards. If an additively printed part cracks or breaks, it can sometimes be repaired via a weld, or in extreme cases we can reprint the part over a matter of days.”
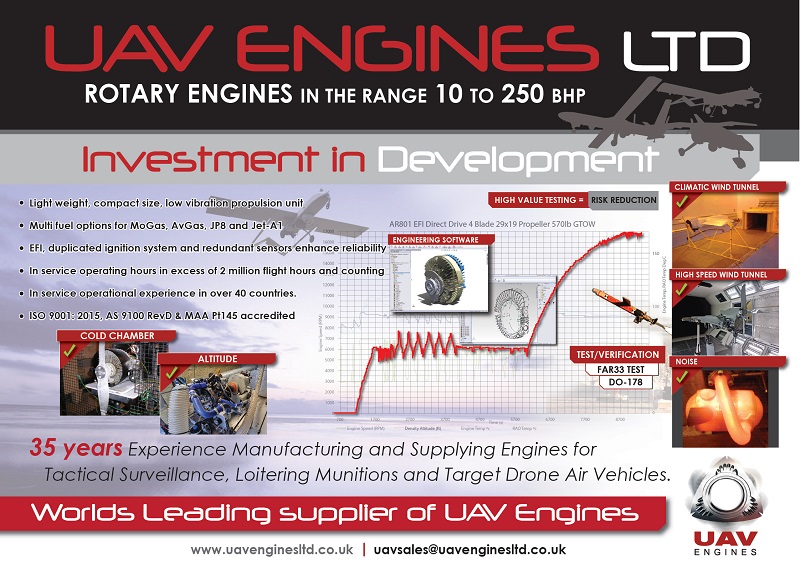
Outer hull
HSG considered designing the ferry as a catamaran early in the process, as catamarans are very stable at speeds above 15 kph, but as the ferry will mostly travel slower than that, it was determined that a monohull would be better for reducing hydrodynamic drag.
“We have a fairly wide, simple monohull, except that we also had to design a shape for the four thrusters to fit under, and as we don’t sail very fast, hydrodynamics don’t play a big part in the energy consumption. In fact, the outer surface of the hull remains a little bit rough from the extrusion as we don’t presently grind or polish it, as we don’t need to streamline it for any high speeds,” van den Heuvel says.
Additionally, a conventional boat would make use of anti-fouling and anti-corrosion treatments, such as specialised coatings, particularly if made from steel, but for the printed composite, this was unnecessary.
“If we travel about 100 m of the Seine, we consume less than 1 kW/h, meaning a return trip across and back over its breadth takes less than a kilowatt per hour. It’s always good to save energy, of course, but in this application, and with our powertrain, we didn’t have to fight for every last watt/hour,” van den Heuvel adds.
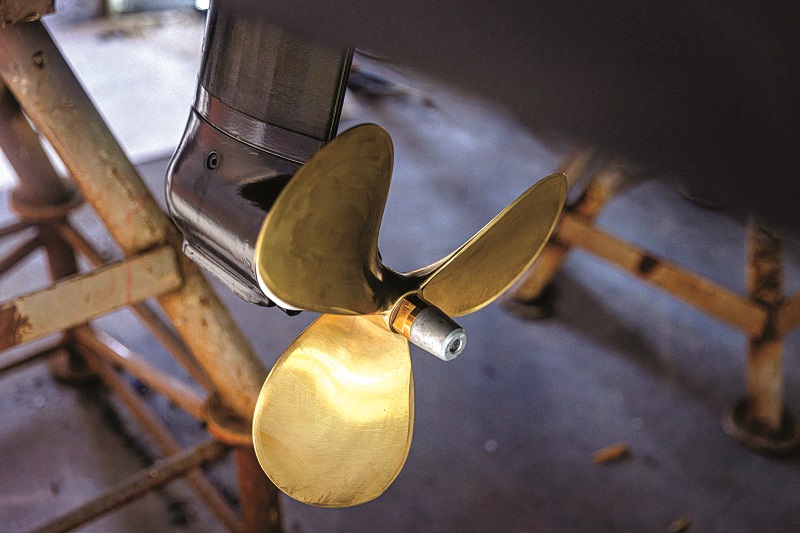
Electric powertrain
“Basing the ferry’s thruster arrangement on the Roboat USV reduced risk in our development. The timeline for this project was very tight, with a hard deadline to make it in time for the Paris Olympics,” Jordan says. “Since we had a powertrain that we knew worked for autonomous water transport, it made sense to just scale it up. We’re now doing water tests in Amsterdam with the full-sized ferry, and it behaves much as our Roboat USV does.”
Tony integrates two 11 kW pod thrusters for main propulsion at the ferry’s port and starboard mid-sections, and two 7 kW bow thrusters (a nautical term for laterally disposed manoeuvring thrusters) at its bow and stern centres. They are powered by a 28.8 kW/h battery pack, which can be charged at a rate of up to 12 kW via a conductive charging port.
Additionally, HSG designed a proprietary automatic mooring system, by which the conductive charging connector at the vessel’s port side is slid into a funnel at the pontoon side to ensure its correct positioning for a secure connection and power feed.
Getting the charging port to enter and exit the funnel requires high precision in the vessel’s movements, made possible by Roboat’s autonomous localisation and control. Once securely in the funnel, automatic charging continues, stable and safe under variable water levels, with up to 1 kW/h replenished every five minutes. So, if the ferry waits for five minutes while off- and onloading passengers, it could sail 24/7 without running out of energy.
“We had to do some calculations as the minimum speed required by the transport agency is 12 kph, and there aren’t many manufacturers of electric boat powertrains, particularly in this size and application, but we found and worked together with Kräutler in Austria for the thrusters and Top Systems here in the Netherlands for the batteries,” van den Heuvel says.
The reasons for choosing Kräutler included its thrusters’ high-power outputs, and its use of nickel, aluminium and bronze in its propellers, per industry standards on high-end and professionally made vessel propellers (some electric thruster suppliers still make their propellers from plastic, which HSG and Roboat deemed mechanically unsuitable).
A key benefit of Top Systems’ battery packs is that they can be configured for a 48 V battery bus, efficiently matching the 48 V of the Kräutler thrusters. They are built from lithium iron phosphate (LFP) cells, which come with a reduced risk of fire, compared with other cell cathode chemistries such as NMC, and have electrical efficiency advantages such as their output voltages not lowering with their state of charge.
Separate from the powertrain bus is a module with a DC/DC converter for stepping down to 30 V buses for the cabin, enabling passengers to plug in and recharge their personal devices during transit. The cabin has an open-air design for working in the Parisian summer, so there are no environmental systems requiring power.
Multi-layer navigation
To perceive its environment for localisation, navigation, and obstacle detection and avoidance, the ferry is equipped with a suite of sensors encompassing Lidars, cameras, inertial measurement units (IMUs), GNSS receivers, and a doppler velocity log (DVL). The vessel will carry human passengers, so it was deemed imperative to have multiple overlapping and redundant sensors.
“We have two sensor hubs on the ferry, set at opposite corners of the outer hull; one at the bow-starboard end and one at the stern-port corner, which gives us an effective, 360° view of our complete surroundings,” Jordan explains.
Klein Schiphorst adds: “As well as having many redundancies through this sensor arrangement, taking those sensor inputs and fusing them together lets us localise the ferry very accurately. Localisation via GNSS is a very well-established, tried and tested part of autonomous navigation, and we’ve stuck with the RTK-GNSS and IMU system from Swift Navigation as that continues to give us very good results. But, we will also be able to carry out some localisation using real-time Lidar modelling of landmarks along the Seine, just as we’ve done in Amsterdam’s canals in the past.”
As well as reading the locations of objects relative to the boat, Lidar helps the ferry analyse and classify those objects so that it can determine the degree of avoidance manoeuvring necessary, thereby moving wider or holding still for longer in the face of a moving boat versus a moored one.
The model of Lidar used on the ferry is an OS1 from Ouster, with Roboat specifically selecting a configuration with 1024 horizontal channels and 128 vertical channels for its resolution requirements. The Lidar measures with a range resolution of 0.1 cm and an angular sampling accuracy of ±0.01°. Roboat has close familiarity in working with such 360° spinning Lidars, and while it is also interested in trialling solid-state Lidars, obtaining these for testing has proved to be challenging.
While the Lidars model objects around the ferry with close fidelity, each sensor module also integrates 6 MP cameras for defining and classifying those objects via the embedded computer vision. Klein Schiphorst says this may be more megapixels than the boat needs, but, given the fact that 35 souls may be carried per journey, excessive resolution, like excessive redundancy, was deemed the better side to err towards.
Over the past four years, Roboat has advanced key aspects of its computer vision and related intelligent sensing tech, including improvements in the calibration of its sensors, the incorporation of select software and hardware innovations from autonomous road vehicles (though adapting them for marine use), and expansions of its body of AI training data through work with a growing number of public water-transport companies in Amsterdam and elsewhere.
“We embed standard water maps into the ferry, so they know the limits of where the water is and isn’t, but most localisation is done in real time,” Klein Schiphorst notes. “And while there are rules and regulations on how the boat needs to move on water, they’re far more implicit than how cars need to move on roads, as boats don’t have to constantly deal with lane lines and traffic lights.”
While using a DVL for USV navigation is unusual, it enables the ferry to detect current flows for aiding motion stabilisation, and also adds localisation information based on detections of the river’s bed and banks.
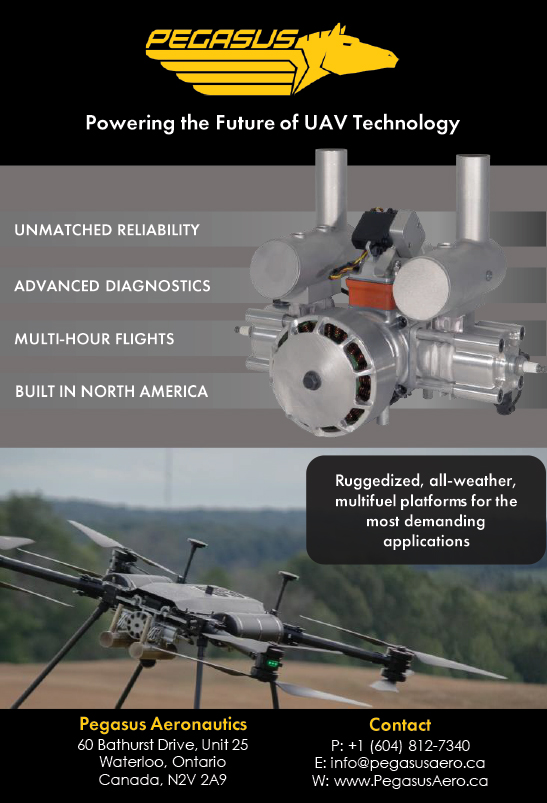
Intelligence
Data from all these sensors runs to the main computer, an NVidia Jetson AGX Orin, which comes with a 2.2 GHz CPU, 64 GB of eMMC memory, and H.265 video encoding and decoding.
“We connect that computer directly to the programmable logic controller (PLC) subsystem on the boat, which is installed by a company called Royal Van der Leun, and that’s what would traditionally be the point of coordination between a boat’s thrusters and a human pilot’s manual controls, so a very tried-and-tested technology that we can rely on to safely transmit signals for operating the boat autonomously,” Jordan says.
The PLC on the ferry can still be used this way. Regulations require that a human captain still be present on the ferry to take over via a manual control console if necessary, so both this operator (who will monitor the health and status of the ferry’s subsystems) and their interface will be located onboard in the cabin. As communication with the PLC relies on a Modbus protocol, Modbus is used for signals throughout the ferry’s network, via an Ethernet bus that serves as the physical transport layer.
Connectivity
In addition to the vessel captain on the boat, who will monitor Tony’s vitals via their Ethernet-connected display, a 4G/4G+ dual SIM cellular connection maintains a redundant live feed indicating these details to Roboat and the fleet operator, for remote monitoring and over-the-air firmware updates.
“It also allows corrections for the RTK-GNSS to maintain centimetric navigation precision,” Jordan says. “We’re capable of using 5G, but for the time being our industry-spec 4G+ gives us a satisfactory uplink bandwidth for detailed live analysis of the ferry’s Lidar and video streams, if needed.”
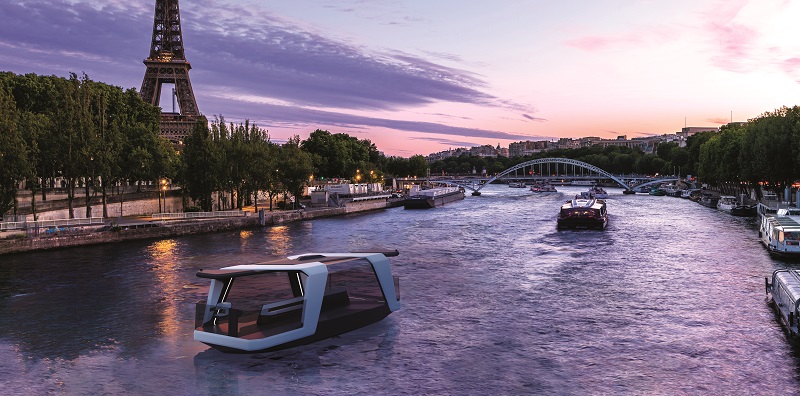
Looking ahead
As of writing, VNF has already requested a second ferry for operations near the first one during the Olympics, starting in July 2024. As well as ensuring higher throughput of passengers, this will demonstrate the capabilities of autonomous mobility, clean energy and additive manufacturing to wider audiences (in Paris and watching from afar), with the consortium targeting future means of optimising the cost-effectiveness of the autonomous ferry operation. It is noted that regulators removing the need for an onboard captain, particularly for short journeys with minimal need for human oversight, would make a considerable difference in this regard.

For now, such is Roboat’s satisfaction with the maturity of its core technological offering that Klein Schiphorst and Jordan aim to offer sensor fusion kits in the near future, which can be integrated onto virtually any boat to turn it into a USV, so long as power and an interface for the thrust and steering systems are provided.
“We’re very interested in additively manufacturing more boats, up to 20 m in length,” van den Heuvel says. “Printing this ferry takes 10 days now, but we’ve learned enough now that the process can be optimised and boats printed even faster, compared with taking weeks or months sometimes via conventional boat building.”
Key specifications
- Autonomous ferry ‘Tony’
- Monohull
- Fibreglass composite structure
- Battery-electric
- Length: 9 m
- Beam: 3.9 m
- Draft: 1.7 m
- Height above water: 3.1 m
- Displacement: 9.5 tonnes
- Maximum speed: 12 kph
- Passenger capacity: 35
Some key suppliers:
- Hull design & assembly: Holland Shipyards Group
- Additive manufacturing: 10XL
- Thrusters: Kräutler Elektromaschinen GmbH
- Battery: Top Systems
- Main computer: NVidia
- PLC: WAGO
- Lidars: Ouster
- GNSS-IMUs: Swift Navigation
- DVL: Nortek
- Cameras: Teledyne Flir
UPCOMING EVENTS
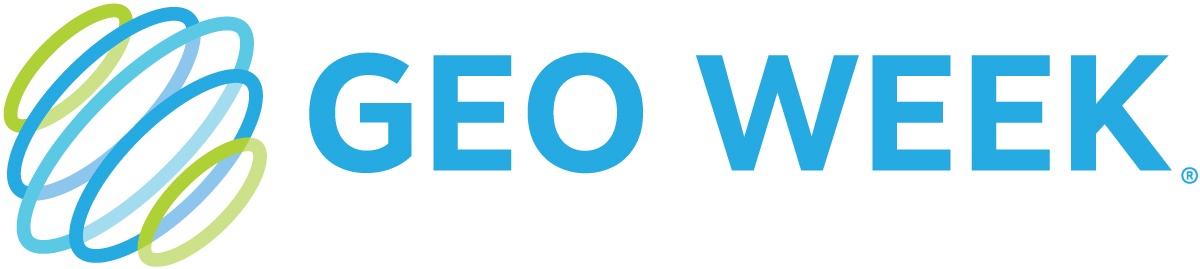
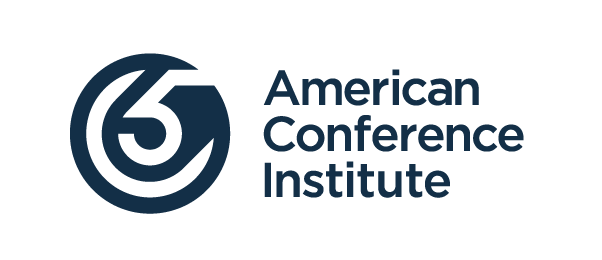
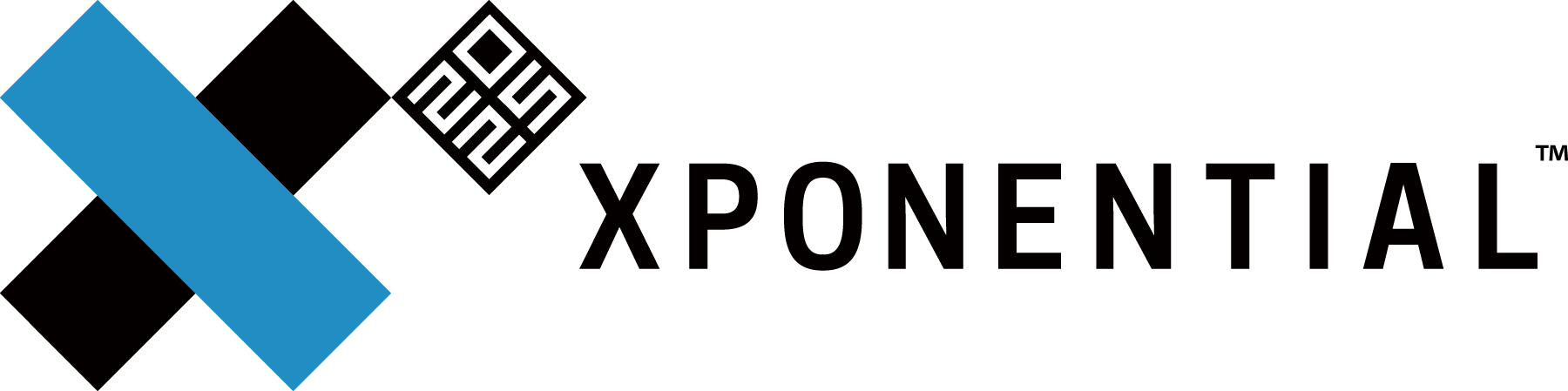
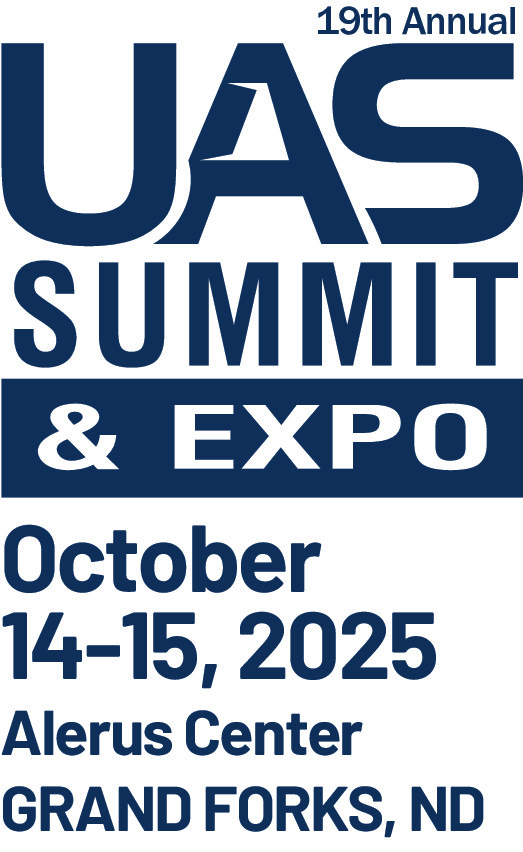
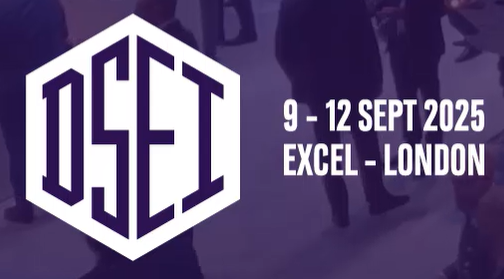
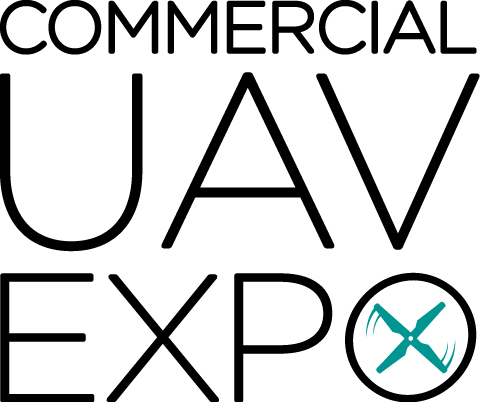
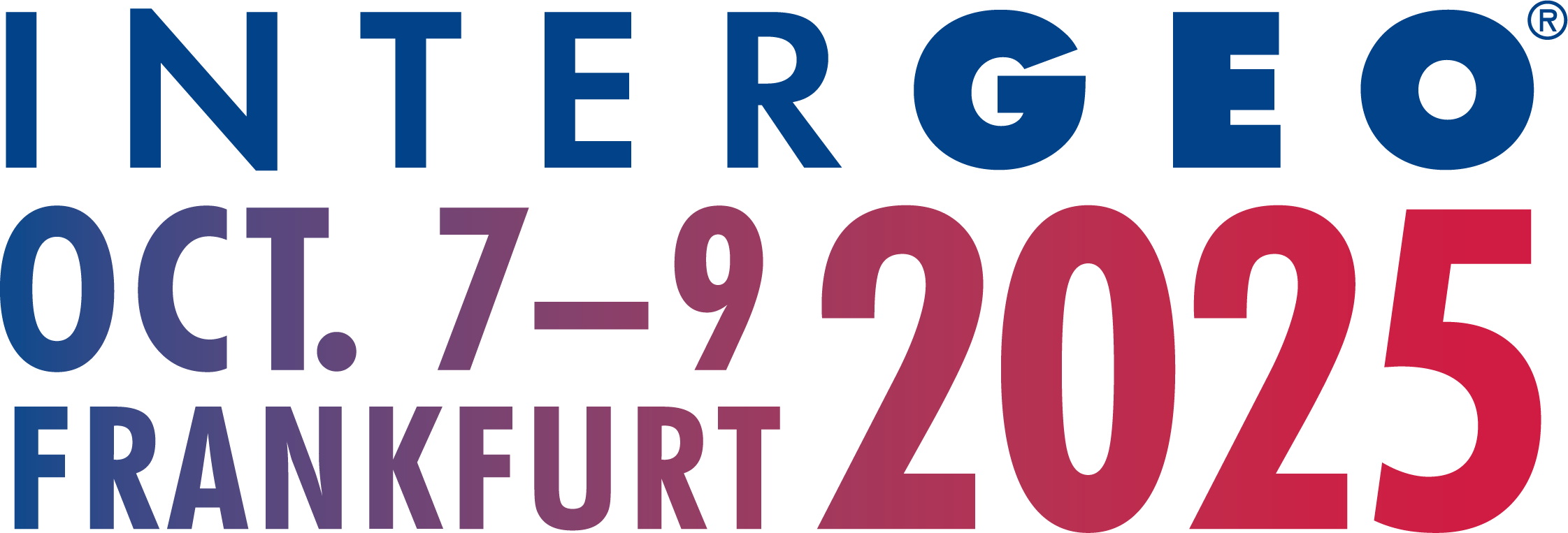
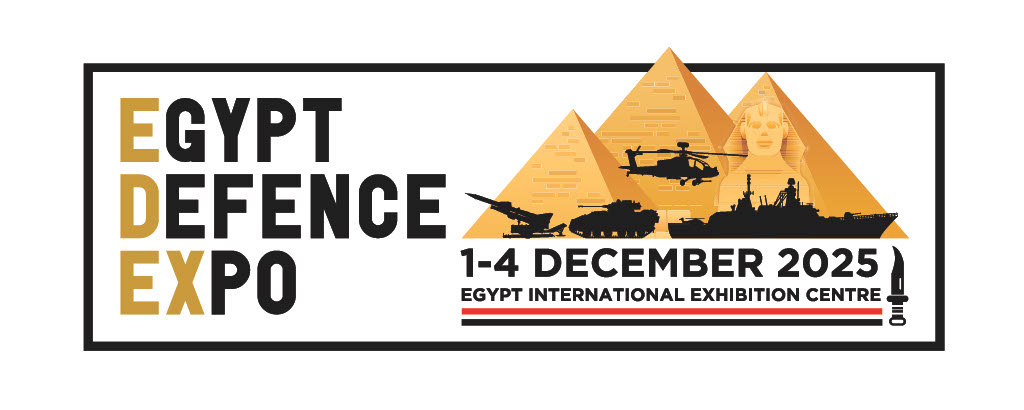
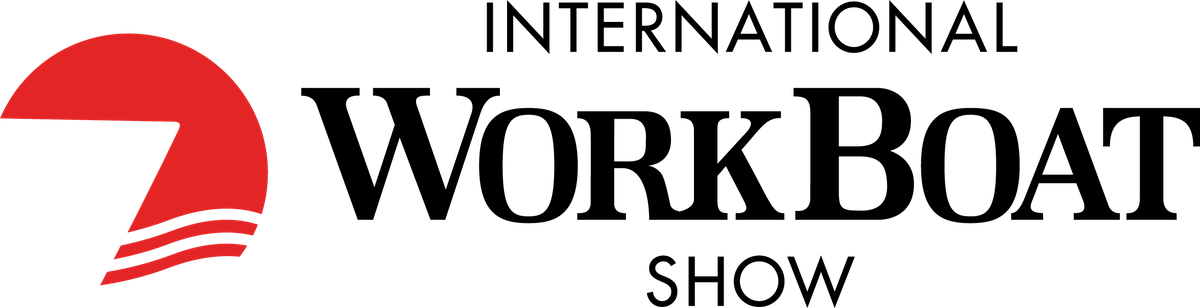
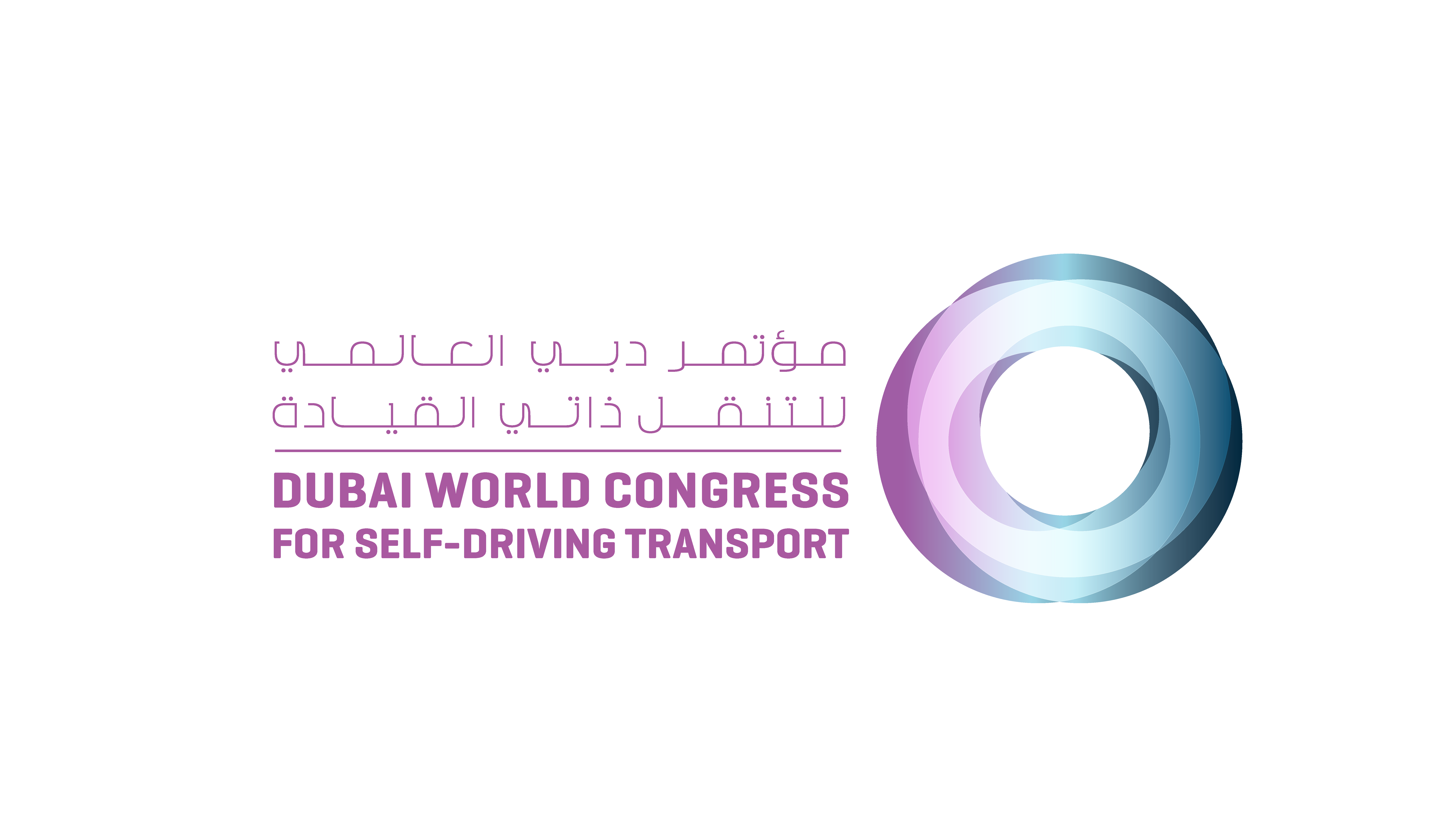
