Servos
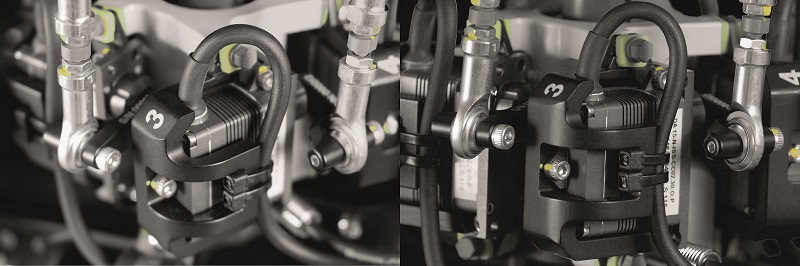
A growing demand for servo reliability and safety is pushing designers to offer high-end products that don’t bust budgets. Rory Jackson reports
Quality control
Although advances in servo design and technology are always in demand throughout the UAV industry, a few key trends among autonomous aircraft OEMs are driving companies to make new leaps in the range and capabilities of their actuators – both rotary and linear types – for the evolving needs of professional customers.
For one, while reliability is a perennial concern for servos, given the need for consistent and accurate movement of control surfaces and other actuated subsystems, there is a huge push for safety across the industry as certification goes from being an elusive and distant idea to becoming a clear, tangible target (or list of requirements) on UAV manufacturers’ roadmaps, both for their vehicles and their components.
And while many OEMs with mature aircraft are eyeing civilian and/or military certification within the next 5-6 years, there is a new wave of manufacturers looking to move from the world of hobby-grade customers and components into manufacturing professional UAVs. These OEMs aim to make UAVs that will serve as tools for small businesses targeting markets such as geospatial survey, last-mile airborne delivery or infrastructure point inspections.
For such users, there is a wide gap between low-cost, low-performance, short-lifespan actuators and high-price, high-performance, long-lasting actuators. Servo manufacturers are therefore moving quickly to try to fill that gap with a new class of cost-effective, high-value servos that will outperform and outlast hobby-grade devices without breaking the bank.
Also, the drive for better data for informing maintenance decisions and real-time monitoring of actuators has led to a predominance of CAN across new servo architectures. The question is not when CAN will displace PWM as the standard in high-end autonomous aircraft (it already has) but which variety of CAN will win out, as a few are in use and more lie on the horizon.
All these trends and others feed into the rule that quality is king in servo designs. Adopting high-end mechanical and electronic components is widespread across servos for the UAV market.
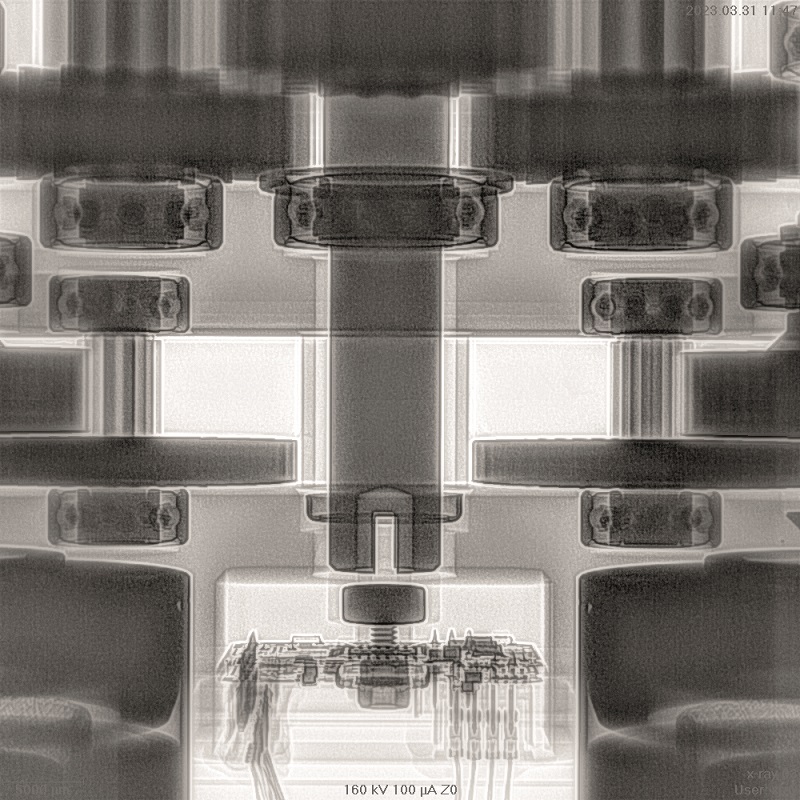
Large servo architectures
The airborne autonomy market offers plenty of designs for air taxis, HAPS and heavy cargo UAVs, whose manufacturers and prospective operators want to deploy them in operations over populated regions. That means OEMs must think beyond the reliability of their platforms and instead about ‘safety’, as defined by regulators and other aviation authorities.
In the context of servo actuators, maximising their reliability has often been skewed towards adding more and more control surfaces to a UAV’s wings and tail. For instance, instead of one pair of ailerons and one pair of flaps, a design engineer might plan for three pairs of each or more across a given wingspan so that if one breaks in mid-flight, others can pick up the slack, in a flight control sense.
However, given the maintenance overheads this might bring (due to having far more servos to replace per aircraft), it is becoming more common to produce inherently redundant versions without causing an equivalent increase in operating inventory and labour costs.
Inside these servos, there are often dual control and power electronics, BLDC motors and geartrains acting on a common output shaft. They would therefore be dual redundant, mechanically and electronically, enabling robust UAV platforms and good protection against the overwhelming majority of failure modes.
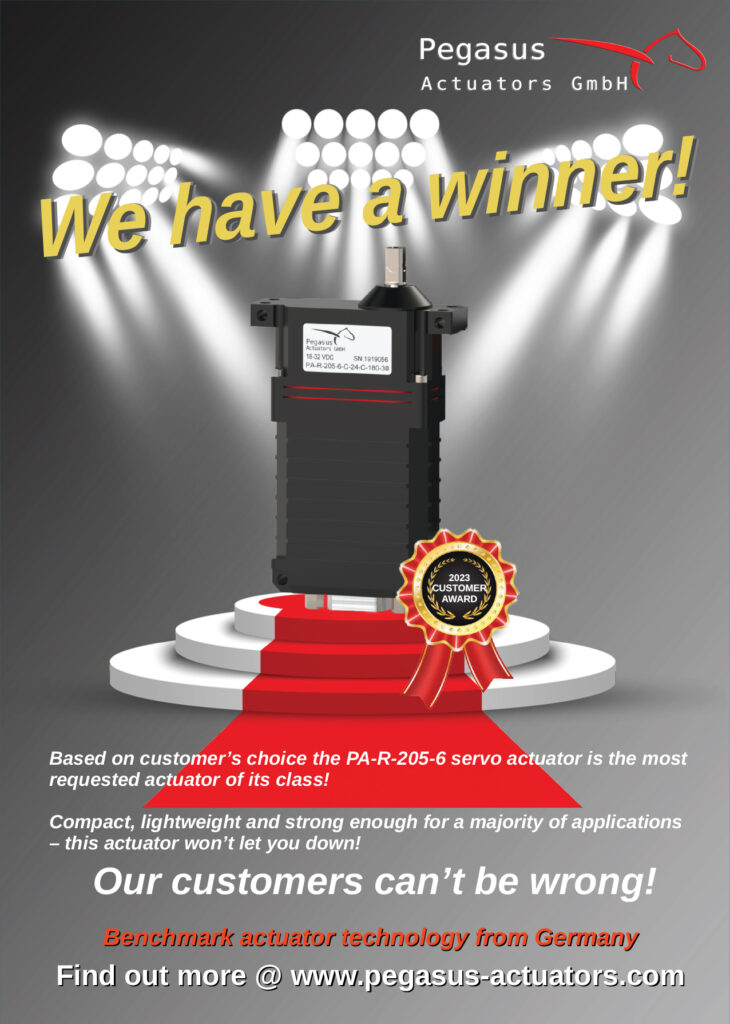
As far as the regulators are concerned though, the reliability of this type of ‘duplex’ architecture is not necessarily synonymous with safety. To aviation authorities, safety for UAV servos (as with commercial airline servos) can be achieved with a single lane of electronics, motors and gearboxes, paired with a dual-redundant command link.
In this type of ‘simplex’ architecture, one lane is responsible principally for taking commands from the autopilot and using them to drive the servo’s electric motor. A second lane is responsible for monitoring the first, and shutting it down if it is found to be generating or propagating errors. Most failure modes as defined by the regulations are therefore covered by simply having the servo monitor itself when working, and shutting itself down when it is not.
Simplex servo architectures are expected to become increasingly common among large autonomous aircraft, given that they can meet certification requirements while avoiding the much higher manufacturing costs and complexities of dual-redundant servos, and their far more stringent testing requirements. With two of almost every electronic and mechanical part, there are many more failure modes and permutations than in single-lane, dual-command servos.
In some cases though, large autonomous aircraft manufacturers will still opt for duplex servos in the belief that they are innately safer. In fact they go so far as to over-spec and bulk-order actuators that produce more torque than their control surfaces and linkages can withstand, thinking that a stronger servo is a safer one.
For such cases, deploying duplex actuators with intelligent, embedded software modules written to electronically limit torque outputs can be vital. The reasons are to prevent accidental damage to flaps and ailerons, and to disengage the limiter function when one lane fails so that the single lane is free to generate its maximum torque, and make up for the torque now missing from the failed motor and geartrain.
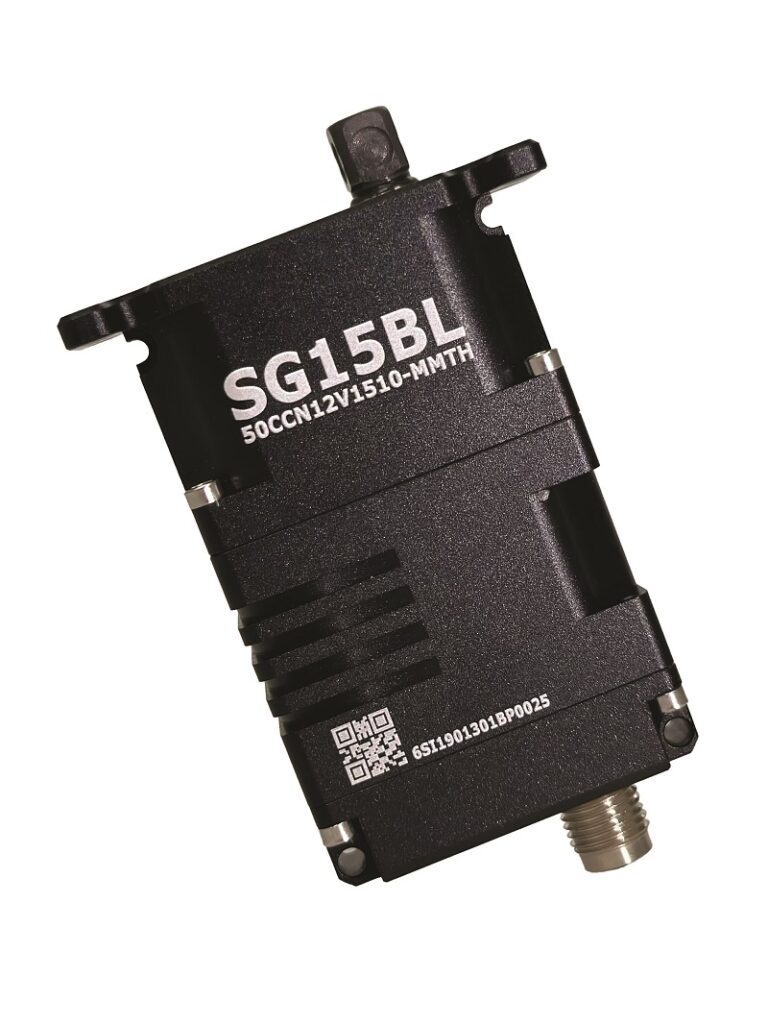
Smaller servos
In the past few years, there has been a rise in demand for small but robust servos, capable of up to 2000 hours between failures, with interfaces such as CAN or RS-485 to provide feedback on parameters such as current and temperature. That helps professional UAV operators across logistics and defence to minimise their maintenance costs.
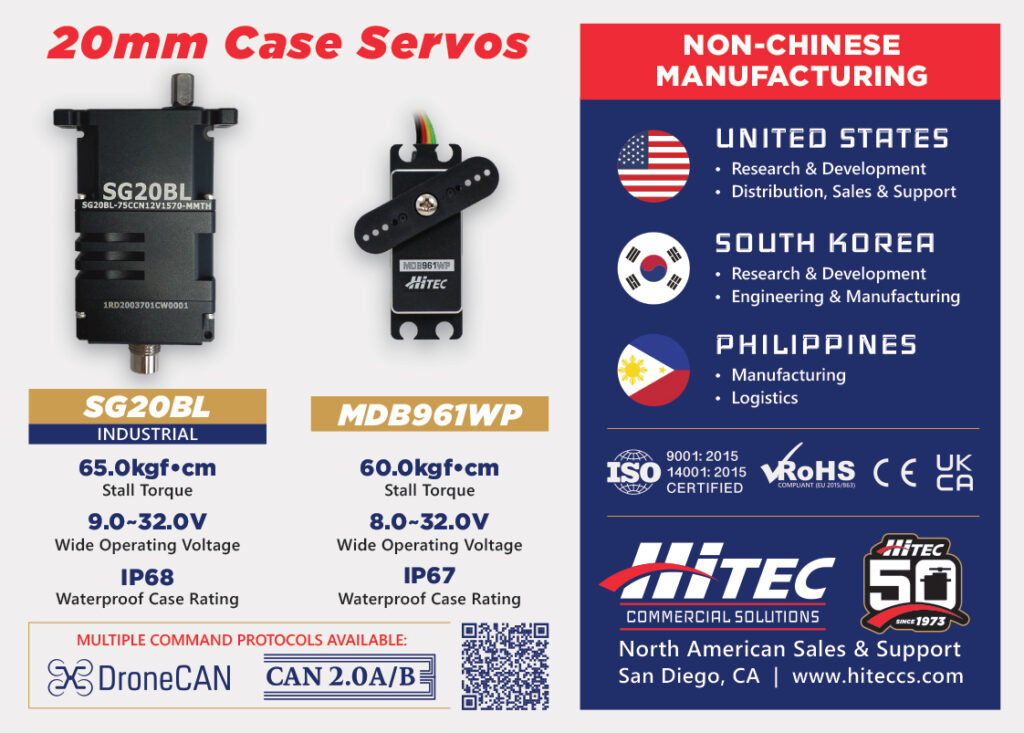
That trend has continued, and there are now some servos weighing 30-60 g that are capable of CAN comms and many thousands of hours of operation, not to mention significant torque and power efficiency for their sizes. Naturally, these capabilities stem from the use of high-end motors, gears, bearings and cases.
Such servos have also proliferated for the underwater market, with UUV integrators having clear options for oil-filled, pressure-tolerant actuators capable of a variety of depths, sometimes several thousand metres below sea level.
However, with the rise of hobbyist aircraft and UAV manufacturers moving into the semi-professional UAV space for smaller business providing services such as agricultural surveys or bridge inspections, servo manufacturers are finding ways to meet the low price points these new manufacturers need without creating a low-quality or unsafe actuator, for instance by targeting 400-500 hours of service life.
In some cases, this is made easier through large inventories of spare parts. The UAV industry requires so many customised versions of COTS servos in small batches that servo manufacturers cannot help but re-use leftover PCBs, connectors, cases and so on in their assemblies, but which have not necessarily been designed with integration in mind.
Serving such end-users can also be achieved by sacrificing a small amount of subsystem quality to save on assembly costs. For instance, the hardened steel geartrains typical of high-end servos could be manufactured and passed through quality control with wider tolerances on the cut of the gear teeth. Similarly, housings can be manufactured with simpler designs that lack features such as cooling fins or internal mounting frames.
As another example, new entrants to the professional UAV space do not typically look for CAN bus or RS-485 in their servos. Not only is tracking health and performance-related diagnostic feedback for intelligent maintenance analytics outside their usual or immediate concerns, but relying on PWM can in fact be useful during early prototyping and optimisation of a UAV’s control architecture thanks to its simplicity of use.
Some cost savings can therefore be made by omitting more advanced interfaces, partly in software engineering and hardware components but more so in the ongoing technical support that inevitably needs to be provided with the more technically complex buses.
Although these types of servos will probably fulfil the requirements for some lower levels of certification, enabling legal flights but with some restrictions, in the long term it is anticipated that their users will gradually switch to more capable and advanced devices, particularly as higher levels of certification become hard requirements for commercial UAV applications such as deliveries over populated areas or long-distance surveys of road networks.
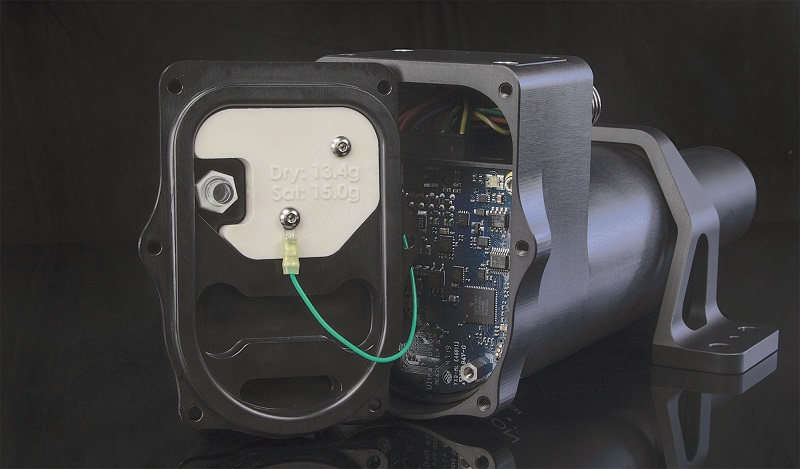
Mechanics
High-quality steel geartrains are increasingly common in UAV servos for the longer lifespan and higher reliability they can provide. The geartrain is often seen as the most critical mechanical component in the servo, as it is ‘consumed’ the fastest owing to the high amount of friction it has to endure. Therefore, much like a metal mould in manufacturing outlasts a plastic mould by orders of magnitude, using a steel geartrain is often the biggest factor in scaling back the rate at which servos – the most frequently replaced part in most UAVs – have to be replaced.
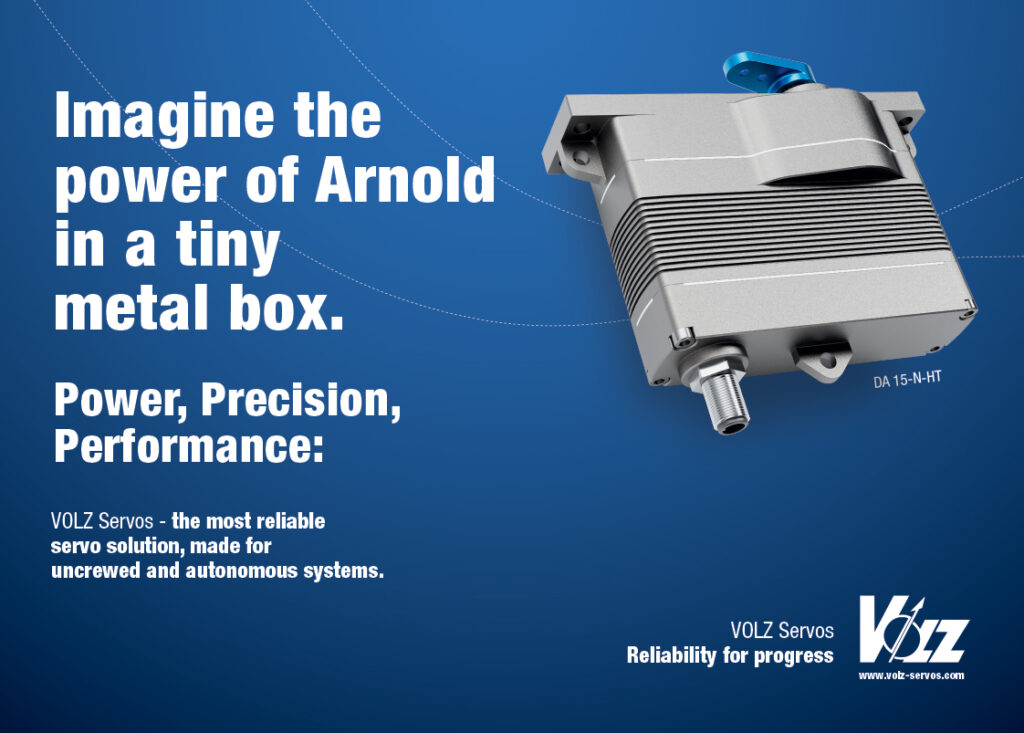
Different design choices can make better use of these parts inside the servo or tailor the actuator for improved capabilities. Back-driving for instance can be desirable for enabling a control surface to return passively to its starting position in the event of a jam or loss of power. Also, designing a geartrain with a lower (or smaller) gear reduction ratio than is standard will make it easier to back-drive, although obviously at a slight cost to torque output.
Also, cutting gears to close tolerances is vital to making them safe and efficient, particularly with regard to backlash, so that the servos are not inherently inefficient when actively reversing. Backlash is the amount of lost or wasted motion due to clearances or slack between gear teeth, when movement is reversed and time passes before contact is re-established.
For rotary servos, this is often a matter of sourcing high-quality and hence costly gear manufacturers. In general however, linear servos are easier to design with low backlash, down to a few thousandths of an inch, owing to the innate differences in how their geartrains are shaped.
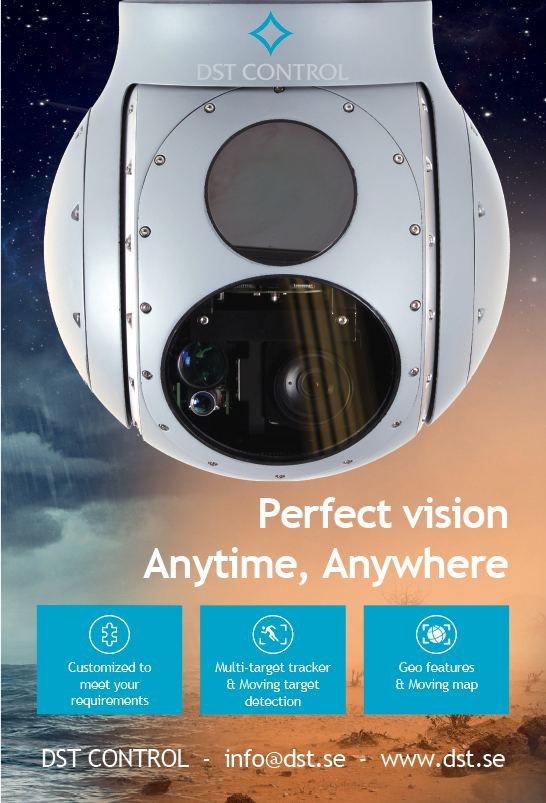
That in turn makes them comparatively easier to back-drive. Other measures, such as helically skewing the electric motor to prevent detent torque (produced by the motor when its windings are not energised) from interfering with back-drive forces can be invaluable in guaranteeing good performance.
Taken together, techniques such as these will become more important as UAVs are demanded for high speed and dynamics in flight, for instance in emergency medical or industrial repair deliveries or in special forces operations. A faster UAV needs more control authority over its flaps and ailerons, so keeping backlash to a minimum will be an increasingly mission-critical requirement for such applications.
Across most of the UAV world though, the key determinant of geartrain quality will be rapid customisations for end-users. As mentioned, lowering or widening the tolerances in a metal geartrain can have an impact on its performance and lifespan, but it will also reduce the price of the actuator.
For manufacturers and operators, this will be a bigger benefit than the extra hundreds or thousands of hours between replacement. This will be especially true if the geartrain is set to last far longer than other parts inside the servo, as many engineers would prefer to replace the whole actuator than open it and replace a single part.
Future improvements in mechanical parts will probably also include r&d into housing and ruggedisation enhancements, one notable example being a custom injection-moulded molecular sieve, applied as a desiccant block near the control electronics and BLDC stator. This adsorbs moisture – meaning it causes moisture to stick to its surface – at a slow rate over many years, and is a major performance improvement over more conventional silica-gel desiccants.
Electrics
While recent advances in small UAV electric motors and motor controllers have yet to feed into new types of motors for servos, there is a slight but noticeable trend towards higher voltages in actuation systems.
Higher voltages mean a more energy-efficient servo, as the high current rates needed for motor torque can be delivered more easily without significantly increasing energy losses through heat in the windings inside (or wires upstream of) the motor. As such, servo voltages up to 24 or 32 V are becoming increasingly common for UAVs across the 25 kg weight class and larger systems.
In most UAV servos now, using a higher voltage does not require using bigger connectors or cables. In fact it can help with hardware design and servo lifespan by eliminating the need for regulators, as these are among the most failure-prone components in an actuator.
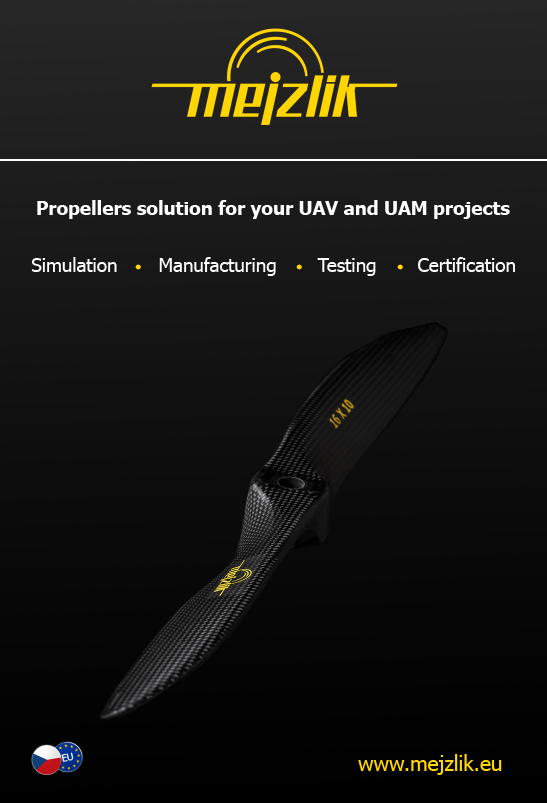
In the future however, as UAM, HAPS and heavy UAV designs proliferate, actuators built for 300-400 V buses and higher will become increasingly widespread, with the 800-1000 V levels of the EV industry likely to follow as electric autonomous air freight and other applications needing extremely large vehicles become a reality. These will need heavier connectors, cabling and protection systems to go with the larger servo sizes, as electrical safety becomes paramount for integrators and technicians.
Sensors
Careful monitoring and maintenance of servos depends on installing and using quality sensors for feedback on operations and health. For the most part, sensors for parameters such as voltage and current are standardised, although a few innovations can be seen in areas such as speed or position sensing.
For instance, advanced features such as the aforementioned torque limitation software cannot rely on current sensing to gauge the speed and torque of a servo. Current readings are extremely prone to noise interference from other electrical activity, and cannot therefore always be relied on to create a closed-loop control system.
Instead, deriving the speed of the servo from its position sensor – particularly a contactless position sensor using a method such as the Hall effect – can be far less prone to interference and will hence be much more reliable. Some actuator designs even integrate as many as three contactless position sensors, enabling triple redundancy and majority voting to make sure the speed and position of the servo are being read correctly.
Contactless position sensing is increasingly standard among high-end servos because of their far longer lifespan than any sensor needing persistent contact and hence causing friction with the motor. Different types of contactless sensor are available, with one design using two single-turn magnetic angle sensors coupled through a geartrain, enabling the encoding of revolutions though an interference pattern that is proportional to the gear timing.
This approach therefore provides position readings accurate to 1-2 microns and works immediately on actuator start-up.
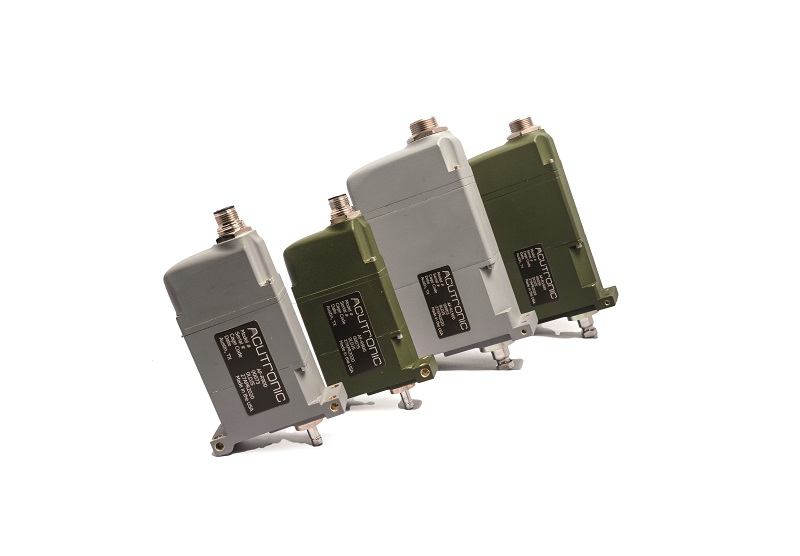
Protocols
As mentioned, CAN bus is prevalent across UAV servos because of its diagnostic feedback features and signal integrity, although a few varieties of it are now in use in uncrewed vehicles.
These generally fall under the umbrella of the CAN 2.0b standard, which was developed and published by Bosch (the original developer of CAN). It is based on the use of 29-bit identifiers, and is now used in a number of commercial UAV autopilot systems. However, as far as specifications beyond the base CAN go, DroneCAN has become one of the most widely adopted protocols in the UAS industry.
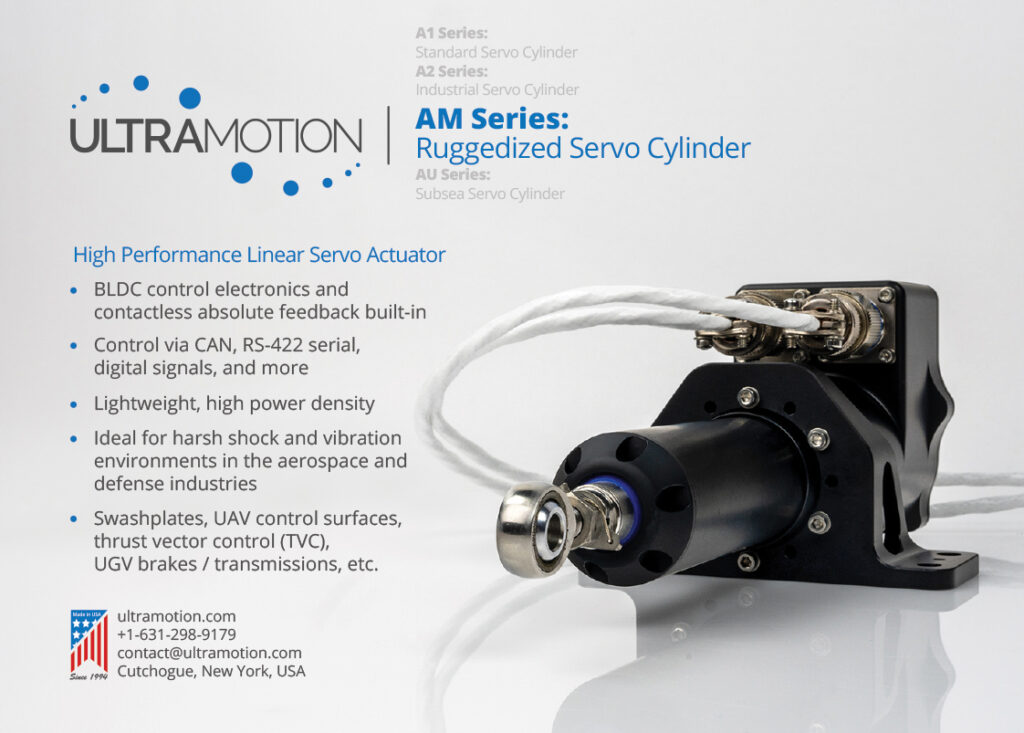
DroneCAN originated as an offshoot of UAVCAN, and has become the primary CAN protocol used in Ardupilot and PX4-based flight controllers for comms with servos and other CAN-based subsystems. It comes with advantages such as detailed protocol specifications, dynamic node allocations for assigning CAN node IDs, and a feature-rich GUI for diagnostics and device configurations.
The choice between DroneCAN and other standards sometimes comes down simply to the end-user’s choice of autopilot and their engineers’ personal preference. In addition, a growing number of ESCs, GNSS receivers and other components are being designed to communicate using DroneCAN, enabling its wider use in servos through compatibility across onboard component ecosystems.
A broader benefit of DroneCAN however is the way it has been consolidated down to a core number of critical features. This is in contrast to CAN-FD, say, which is widely used in cars but is far more complex and multi-faceted than is necessary for uncrewed aircraft, as it has to cover ancillary driver and passenger-related functions such as seatbelt sensors, check engine lights and airbags.
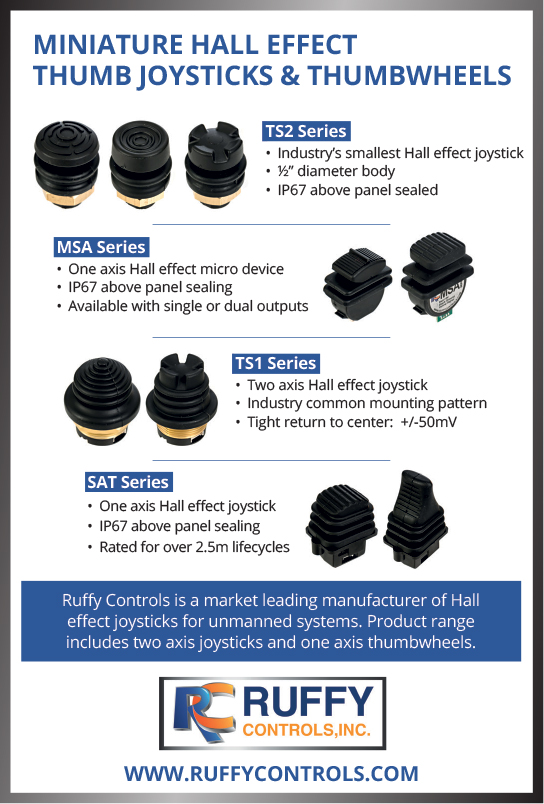
On top of that, the growing popularity of DroneCAN is somewhat self-perpetuating, as UAV OEMs know they can swap from one supplier’s servos to another if they both use it. Both sets of actuators will use the same code structure, minimising the integration work for their technicians. Delving into the structure might still be needed to determine and reconfigure node allocations and IDs, but unlike CAN-FD, say, it would not require exhaustive removal of nodes and IDs that go beyond platform requirements.
That adds another layer of consideration regarding the level of customisability or preprogramming that can come with servos. It might be very useful for UAV manufacturers to receive actuators in which the nodes and IDs are initially undesignated, so that systems integrators can custom-define the architecture themselves. However, some actuator suppliers opt to predefine the architecture, as they have found that allowing customers plenty of configuration options too often leads to them introducing errors into the servos’ programming.
In the meantime, other protocols are gathering followings. For example, some servo models are now being designed to operate using CANaerospace, a protocol derived from the aviation-specific ARINC 825 standard’s guidelines but in a more streamlined format and now being adopted across some aviation engines for UAVs. That adoption has driven the use of CANaerospace in servos for flight control, to enable all the servos in a given UAV to run on a common protocol.
Beyond these three, there is a growing rate of requests for customised CAN-based protocols. They deviate from the standards and guidelines to suit individual UAV manufacturers and their unique implementations, and some of them are expected to feed into future variations of CAN that are further tailored to suit the evolving needs of uncrewed commercial and military fleet operators.
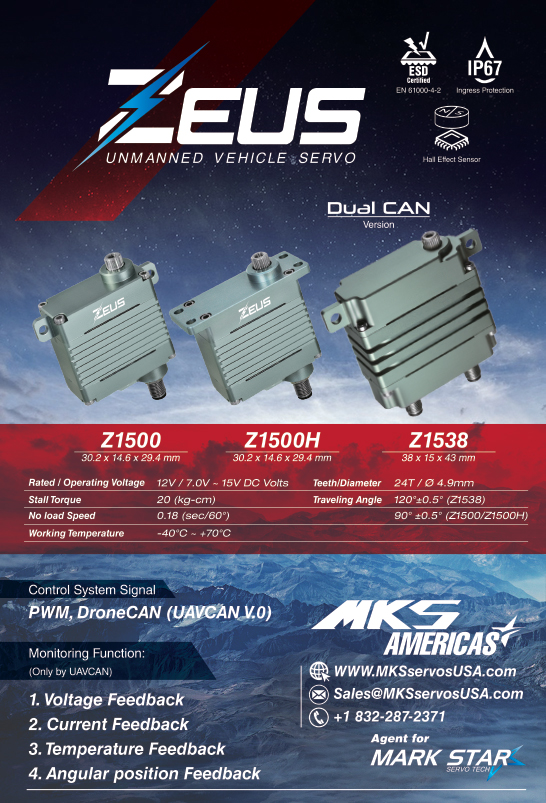
Future prospects
While the hardware and mechanics of servo actuators have no doubt undergone considerable innovation over the past few years, with reconfigurations and redesigns using established hardware in different ways, most future innovations that push the capabilities of servos can be expected to come from software developments.
For instance, given the increased breadth, quantity and quality of data accessible from servos thanks to the primacy of CAN bus, some servo manufacturers are working on solutions for predictive maintenance. These will enable increasingly accurate projections of remaining lifetimes, calculations for individual failure mode probabilities, and detailed requirements of firmware patches.
The potential gold mine of big data in the servo world is likely to drive investments and advances in new types of diagnostic sensors, new ways for AI to help with analyses and predictions, and potentially more SWaP-optimised processors that are able to perform the required predictive computing at the edge.
Beyond this, the ongoing search for reduced weight in servos should be expected to continue. Some low-hanging fruit remains in this regard, with possible approaches such as making actuator housings from carbon composite or magnesium representing valuable opportunities. Similarly, electric motors with iron-less stator cores could save weight and enable improvements in energy efficiency. These and other advances can be expected in the years ahead.
Acknowledgements
The author would like to thank Phillipp Volz, Mark Juhrig and Felix Thun at Volz Servos; Tom Quartararo at Ultra Motion; Thomas Cooke at MKS Servos; David Baillie at HTServo and Shawn Spiker at Hitec Commercial Solutions for their help with researching this article.
Some key suppliers of servo actuators
GERMANY
Kollmorgen | +49 21 029 394 0 | www.kollmorgen.com |
Pegasus Actuators | +49 60 349 399 699 | www.pegasus-actuators.com |
Volz Servos | +49 69 985 580 0 | www.volz-servos.com |
ISRAEL
Bental Motion Systems | +972 4 696 0199 | www.bental.co.il |
Elmo Motion Control | +972 3 929 2300 | www.elmomc.com |
MTC Industries | +972 4 998 7772 | www.mtcind.com |
SOUTH KOREA
Contromax | +82 42 822 0630 | www.contromax.com |
SWITZERLAND
Faulhaber Minimotor | +41 91 611 3100 | www.faulhaber.com |
TURKEY
Femsan Electric Motors | +90 216 378 8888 | www.femsan.com |
Tork | +90 216 364 3405 | www.smstork.com |
Volt Electric Motors | +90 232 877 1060 | www.voltmotor.com.tr |
UK
HTServo | +44 19 0382 3014 | www.htservo.com |
OTM Servo | +44 17 8443 3155 | www.otmservo.co.uk |
USA
Acutronic USA | +1 412 926 1200 | www.acutronic.com |
Advanced Motion Controls | +1 805 389 1935 | www.a-m-c.com |
Designatronics | +1 800 819 8900 | www.designatronics.com |
ESI Motion | +1 800 823 3235 | www.esimotion.com |
Fast Optimal Engineering | +1 661 257 8481 | www.foengineering.com |
Futaba USA | +1 256 461 9399 | www.futabausa.com |
Harmonic Drive | +1 978 532 1800 | www.harmonicdrive.net |
Hitec Commercial Solutions | +1 858 737 9220 306 | www.hiteccs.com |
Kearfott | +1 828 350 5300 | www.kearfott.com |
MKS Servos USA | +1 832 287 2371 | www.mksservosusa.com |
MOOG | +1 716 652 2000 | www.moog.com |
Ultra Motion | +1 631 298 9179 | www.ultramotion.com |
UPCOMING EVENTS
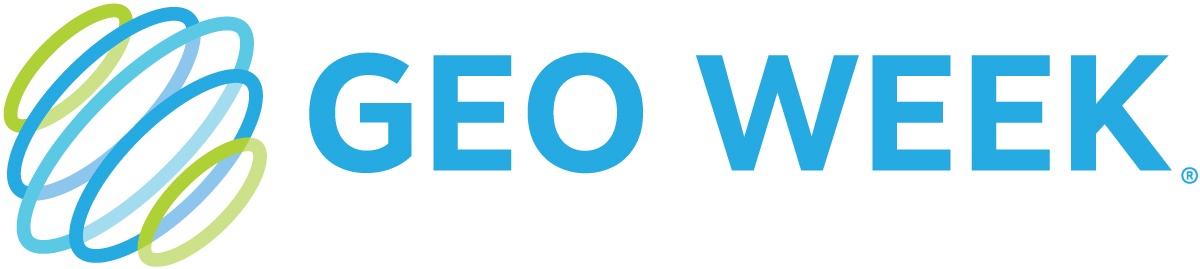
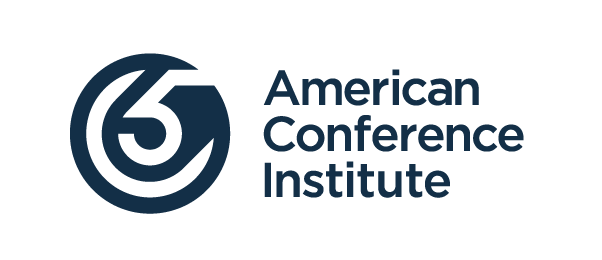
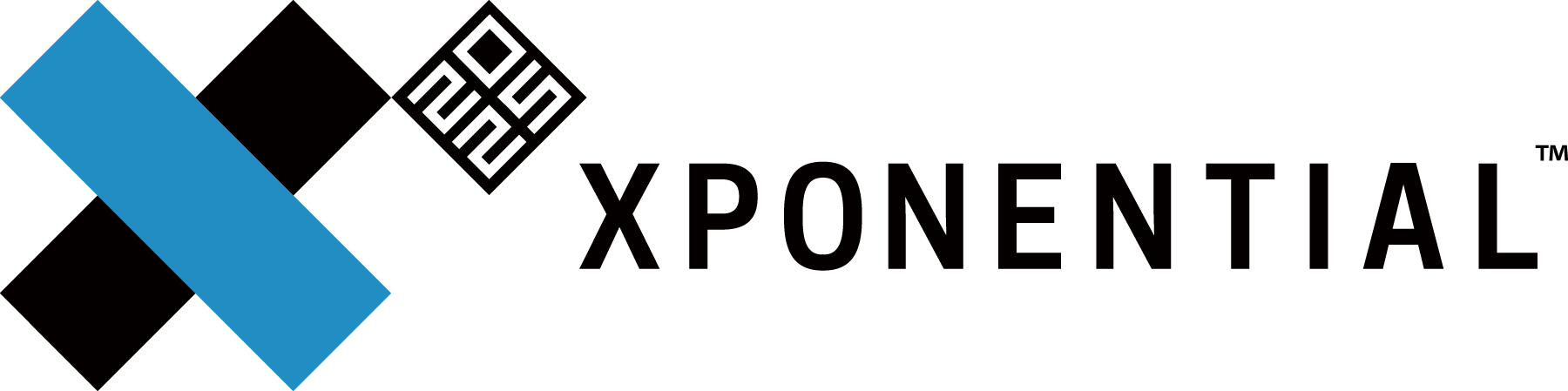
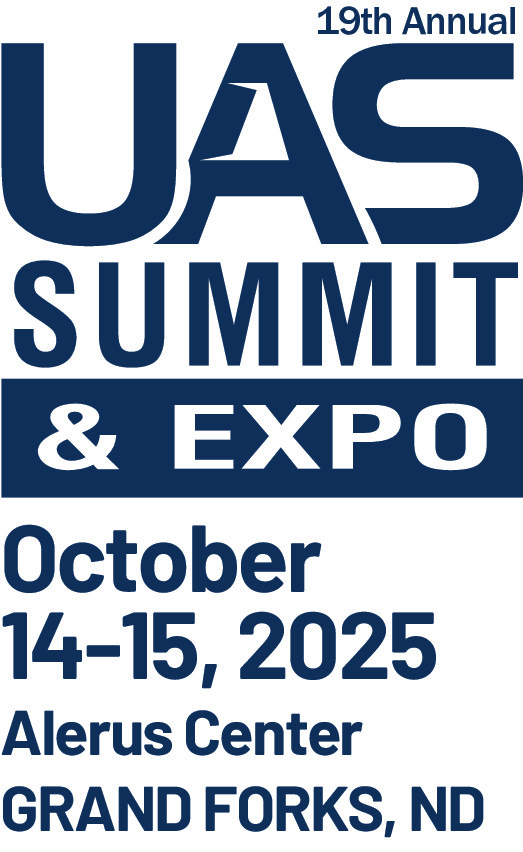
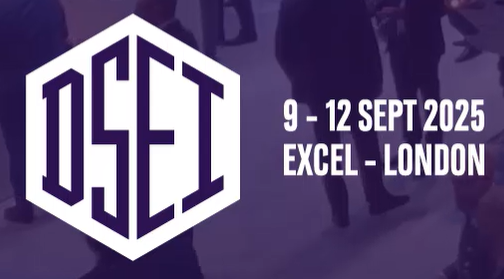
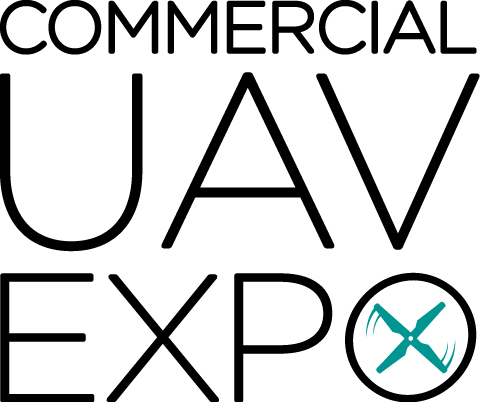
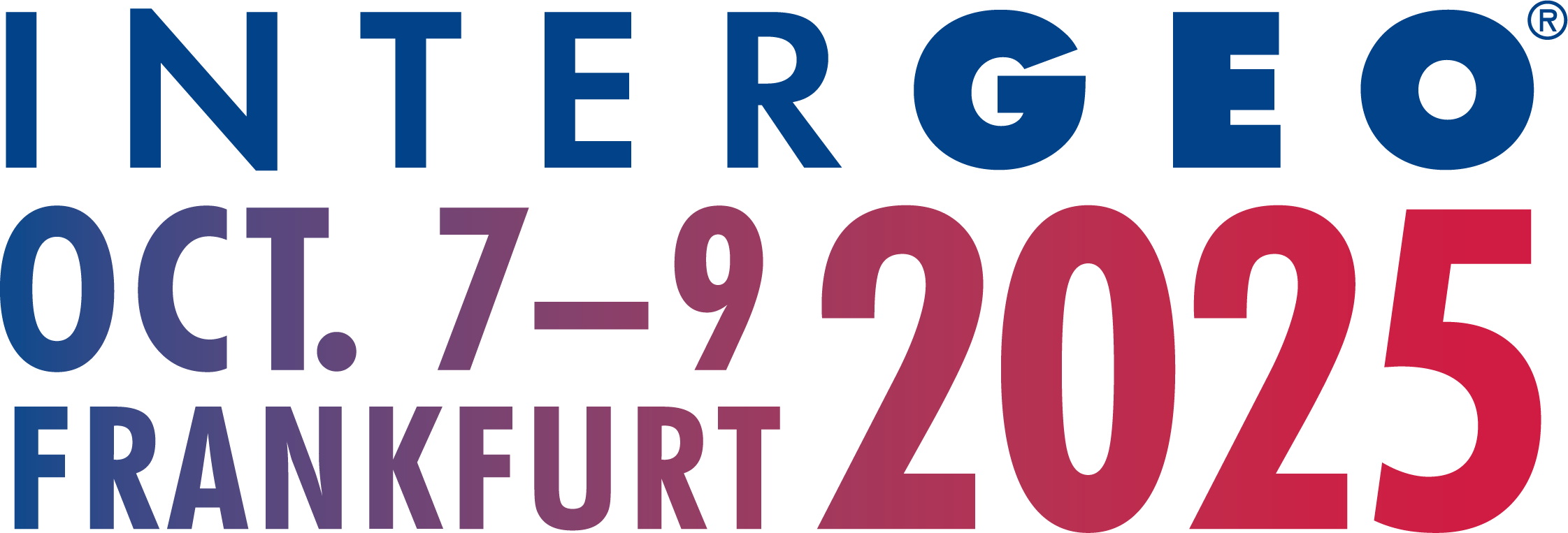
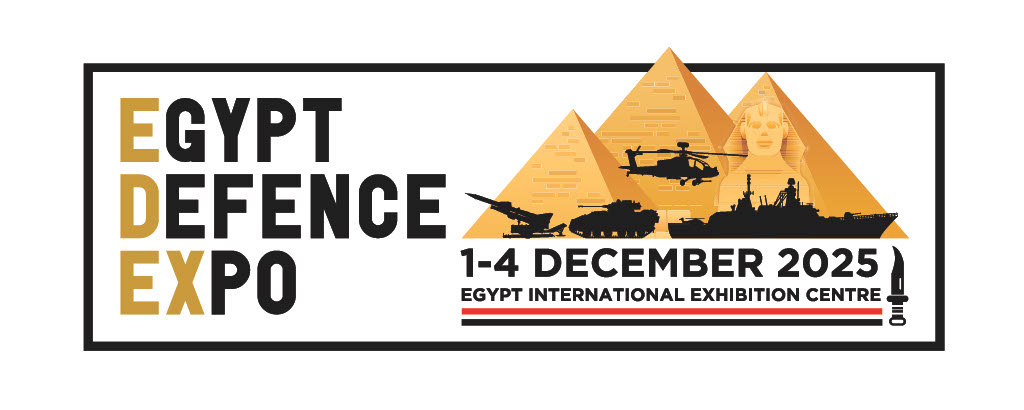
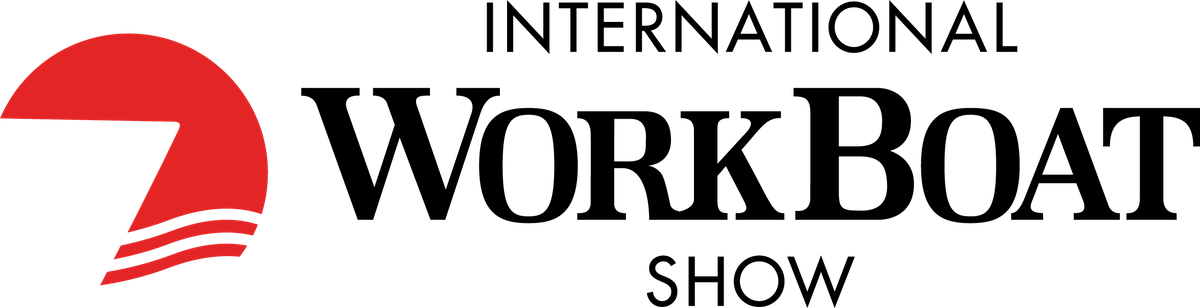
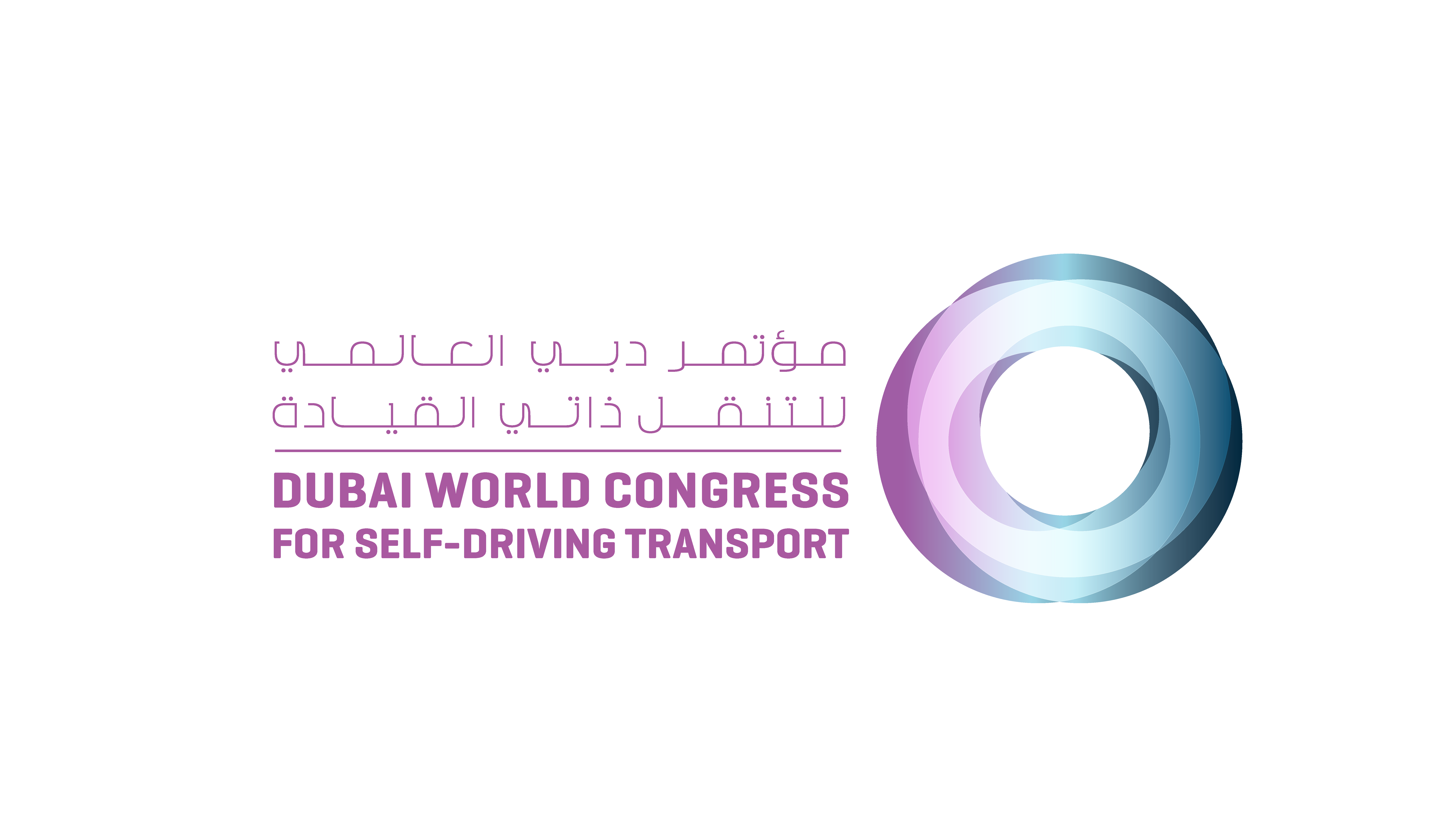
