Applied EV Blanc Robot
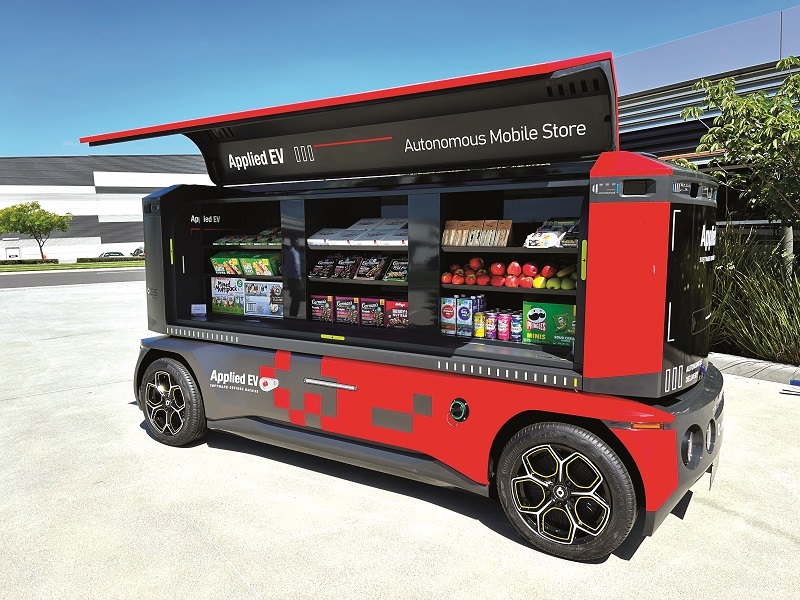
Rory Jackson learns about the Blanc Robot, a blank slate on which to build any body structure for any application
Founded in 2015, Applied EV is a company based in Sydney, Australia, whose raison d’être is to create transport solutions that it views as safer, cleaner and more efficient than existing conventional solutions, and by extension to unlock new business models and economics for transport through the development of its software-defined vehicles.
“Our team comes from a broad range of high-tech and automotive backgrounds with experience in business development, programme management and corporate governance, giving us experience across the full development lifecycle of automotive systems and software,” says Julian Broadbent, co-founder and CEO of Applied EV.
The company’s journey began with the design of a solution it calls the Digital Backbone, a purpose-built control system (analogous in many ways to an autopilot) that could be installed into theoretically any traditional road vehicle – although electric vehicles (EVs) are naturally preferred for their digitalised control networks – and, with the minimum of integration steps, make it autonomy-ready, with potentially just a sensor architecture installation as the missing piece for the integrator to decide upon.
The system contains all the hardware and functions needed for principal control and management of the vehicle, judiciously crafted to comply with the highest safety ratings.
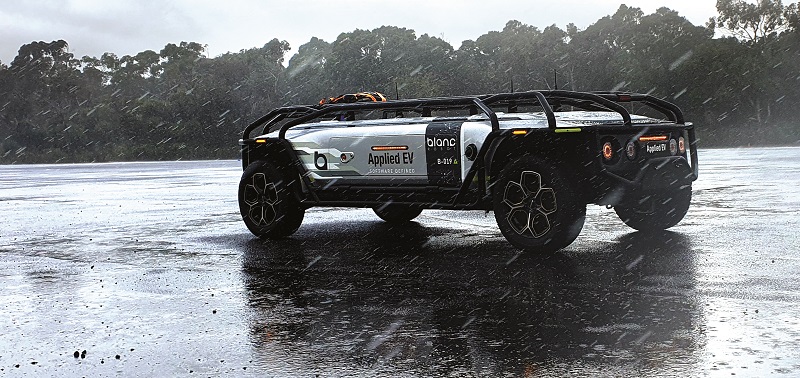
Applied EV anticipates that by packing the Digital Backbone with all the latest and most optimised software and hardware systems it could source or develop in-house for handling veritably all the functions of an autonomous EV, the turnkey solution could simplify vehicle architectures, remove hundreds of components, reduce production costs, increase efficiency and make the entire automotive ecosystem more sustainable.
To satisfy industry and market requirements, Applied EV aimed to ensure the complex control and management functions needed in the Digital Backbone were designed to the highest functional safety standards present in the automotive world.
In 2016, the company developed a key partnership with the University of Sydney’s Australian Centre for Field Robotics (ACFR), considered by many to be one of the leading robotics research institutes in the world.
Despite having spearheaded the development of numerous globally successful robotic systems from its facilities in the University of Sydney’s Faculty of Engineering over many decades, the ACFR needed additional resources to design and engineer purpose-built, software-defined vehicles from scratch.
The Applied EV team developed two such vehicles, going on to deliver them in late 2016 and early 2017, and such was the ACFR’s satisfaction that it continues to use those vehicles today.
“The Australian Centre for Field Robotics was our first customer, and our experiences with them immediately validated what we had already suspected: there had been a lot of big, missed opportunities and [there was] a market need for the kinds of products we were developing,” Broadbent says.
“Throughout my career, I have been fortunate enough to hold multiple senior positions at General Motors. Largely, my role was about understanding trends in customer behaviour and technology to develop business cases for future programmes.”
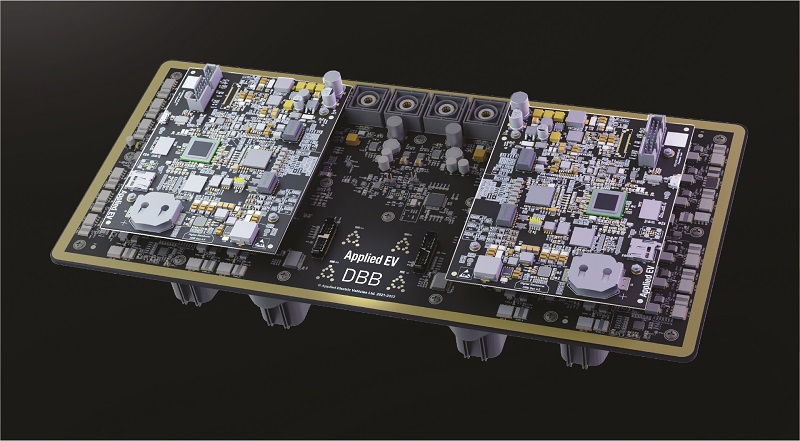
Through that understanding, amid the journey taken by Broadbent and his team to develop the Digital Backbone as a system that could turn traditional vehicles into autonomous-ready systems, they were confronted with the reality that many prospective autonomous vehicle developers were stuck working with automakers who were focused on rapid delivery of a minimum viable product (MVP), and worse, they wanted it to be built on legacy development and production lines.
Incumbent players and their suppliers are therefore taking an evolutionary approach, which is ultimately designed to build only on pre-existing capabilities, leverage only well-established development processes and protect sunk development costs, Broadbent says.
This is a logical approach in many ways, especially in terms of leapfrogging cost barriers, such as investing in and establishing new production lines. One may think, for example, of Toyota rejigging a pre-existing manufacturing line to mass-produce automotive hydrogen fuel cells. But, in Broadbent’s view, it fails to capture the real, long-term potential of autonomous systems.
“Ultimately, an incremental approach will not extract the true value of software, and the key question is: is an autonomous system truly autonomous if there is a safety driver sitting at the controls, ready to take over in case of an emergency?” he muses.
Applied EV estimates that about 50% of vehicle costs revolve around the driver-cockpit environment, from crash safety systems such as airbags and seatbelts to visibility items, like windshield glazings and mirrors, human machine interface (HMI) devices and comfort infrastructure.
By removing the driver from its platform design and thus eliminating the need for all those types of components, Applied EV believes it has created the ideal blank slate for multipurpose, software-defined mobility applications; hence its name, the Blanc Robot.
The Blanc Robot is a 4WD, four-wheel-steering, battery-electric vehicle platform, constructed around the company’s Digital Backbone as its controller, thereby creating a system provident of 80-90% of the development work needed for a highly specialised autonomous road vehicle, offering a standard development environment for OEMs to create their own apps and features.
“The true value of an autonomous vehicle is from a platform specifically lacking a driver cabin – economically and ergonomically,” Broadbent says. “We knew we could create a self-driving software-defined vehicle with the necessary functional safety ratings and open architecture required to offer ASIL-D safety-rated features and applications, such as X-by-Wire driving, Level 3 ADAS support, or Level 4 or Level 5 Autonomy.
“With the Blanc Robot, we have a blank slate – pardon the pun – upon which we can build any body structure for any given application. We developed the first Blanc Robot in mid-2018, and rapidly developed very strong bonds with autonomous and automotive partners around the world, who understood what we wanted to do: start the process of showing the true value of autonomous vehicles to the world.”
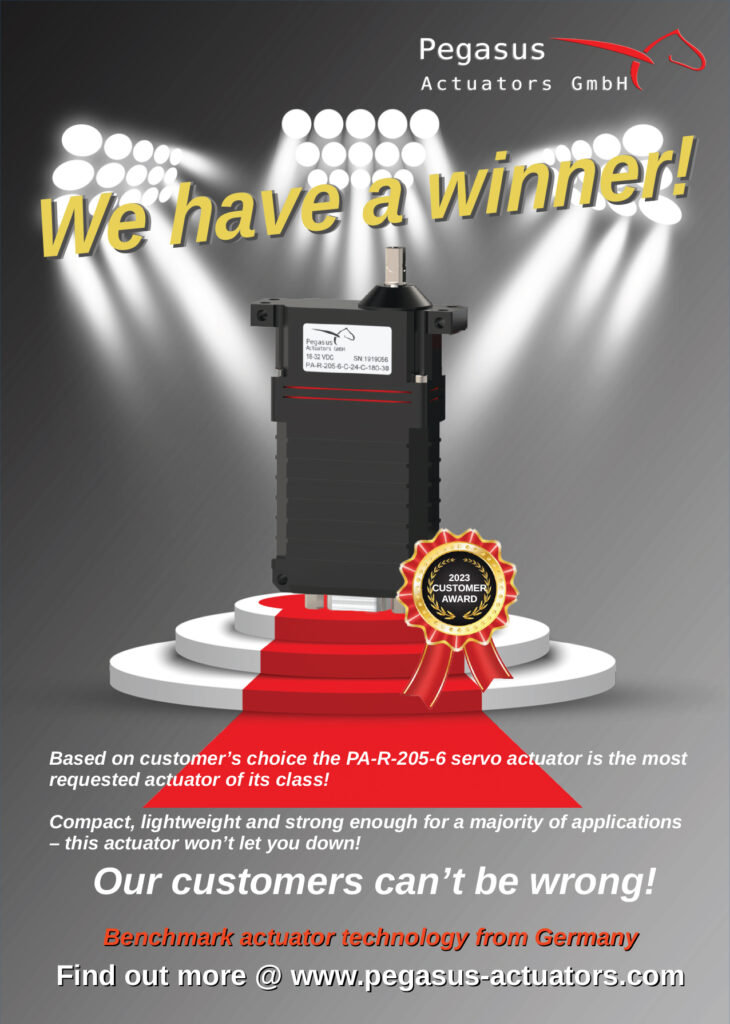
Standards of safety
The decision to remove the driver’s cabin from the Blanc Robot brought with it the realisation that without a driver, there was no safety fallback for Applied EV’s controller, and the Digital Backbone had to manage every aspect of the vehicle’s control and management functions entirely on software, without making a mistake.
This introduced new rounds of r&d for the Digital Backbone, as Broadbent recounts: “From early on, we knew we’d need significant layers of redundancy that were ‘always active’ and immune to total fault. We took to calling it the ‘Noah’s Ark strategy’ because we needed two of everything. Soon, we had two battery packs, two motors for steering, two for braking and four for traction.”
In addition, the second edition of the ISO 26262 standard was published in December 2018, having been expanded to cover the functional safety of electric and electronic systems in not only passenger vehicles but all road vehicles, except mopeds. This also led to the ‘ASIL’ definitions of safety requirements necessary for compliance with ISO 26262, from A to D (ASIL-D being the highest level of integrity requirements).
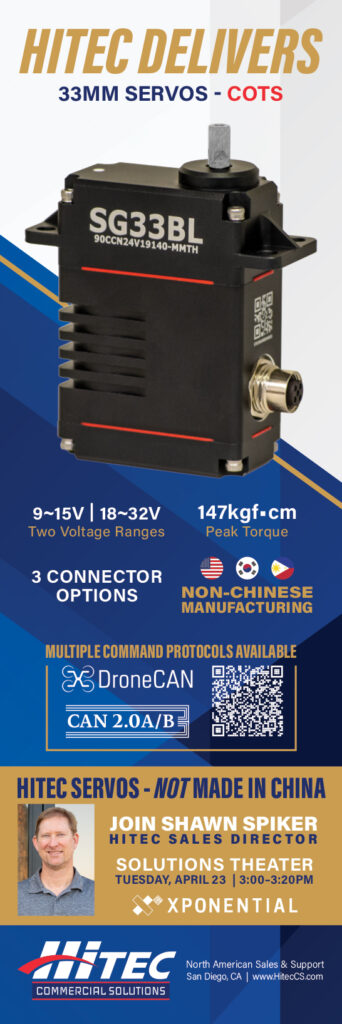
“We started to get involved with how ISO 26262 was being constructed, which defined how we developed as a business. ISO 26262 isn’t like ISO 9000, where a couple of suits come in with clipboards and audit your business for a week,” Broadbent says.
“It relies on your entire culture being built around safety. Even the biggest OEMs can’t fast-track their way to functionally safe, software-defined vehicles with cash. For an ISO 26262-compliant autonomous solution, you can’t have a single failure mode, or the vehicle fails and you have to recall every vehicle you’ve ever sold.”
Applied EV has henceforth worked to establish safety in its culture, organisation and functional safety processes, which can be adapted as needed as the certification project for the Blanc Robot proceeds.
Growing a Backbone
The Digital Backbone, now in its sixth generation, as of writing, has been updated in multiple incremental versions or generations (each with sub-versions) to date.
“Looking back, the fifth version was an especially significant moment for us, as it was embedded in the Blanc Robot that went to the UK to do the first-ever trial of an autonomous, cabinless vehicle with Oxa [then known as Oxbotica],” Broadbent recalls.
“Based on learnings between 2016 and 2018, we started in 2019 with a clean sheet and designed a software-based control system to accelerate commercialisation of autonomous applications, compliant with ISO 26262.”
The sixth generation incorporates numerous tunings aimed at functional safety, as well as suitable capacity for inputs and outputs – and sufficient future-proofing – for integration with a broad range of sensor architectures, powertrains, and power and signal network buses. The resulting control system architecture and product design for vehicles is equipped with redundant subsystems to fulfil the requirements for safety integrity levels, up to ASIL-D, with fail-operational safe states.
The Digital Backbone is presently capable of up to 1000 I/Os (input/output operations per second), with 22 controller area network (CAN) buses configured to ASIL-D standards for automotive users to connect and prioritise devices with the Digital Backbone’s functions. The high number of I/Os is intended to fully enable end-integrators to program as much software of their own as they could possibly want.
“Over the first five generations, we developed the fundamentals of the system to make it functionally safe, so that is really what has greenlit us to create APIs and pathways for others to write specific and unique software features and applications into our software-defined vehicles, which many are very keen to do,” Broadbent says.
As an example of the kinds of changes that would be enacted between subversions, the Gen 6.1 saw a traction-battery unit (TBU) integrated into the Digital Backbone, but subsequent versions also incorporated safety-rated energy systems to increasingly comply with regulations.
Additionally, the Gen 6.2 version incorporated a new battery management system (BMS); something critical for and linked to a new battery that had been integrated into the standard Blanc Robot (with the sole communication between the Digital Backbone and that BMS occurring via a CAN interface). The Blanc Robot, also in its sixth generation, has undergone gradual architectural improvements in areas such as battery configuration, brake components and other drivetrain qualities.
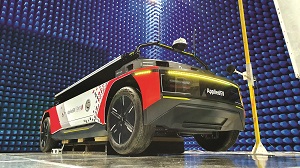
“Today, the overall vehicle is built from approximately 90% Applied EV components and 10% externally supplied parts. Although we designed it with automotive-grade safety compliance in mind, prototyping and low-volume builds currently come with a large development cost per unit,” Broadbent observes.
“So, for future production of the Gen 6 and beyond, we decided to speak with one of our key partners and investors, Suzuki Motor Corporation, which makes a similar-sized vehicle, and they agreed to be our manufacturer towards mass production.
“As we have gone through generations, we’ve sought to move away from making small numbers of high-end complex systems towards a mass-market automotive approach – one that turns the production side of things into something simplified and repeatable, so we can focus on our technology.”
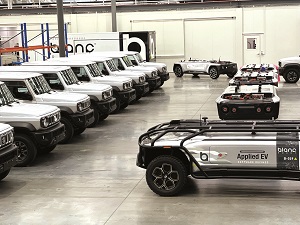
Blanc Robot anatomy
The Gen 6 Blanc Robot measures about 4 m long, 1.7 m wide, and 80 cm tall, and based on its current production process, it is comparable to a Suzuki 4WD Jimny SUV platform with the body removed.
The process by which the Blanc Robot is made out of the Jimny consists of Applied EV taking the ladder frame of the said platform and converting it into an autonomous, electric system.
Applied EV also installs a body above the chassis, inside of which one finds a battery pack, two electric motor drives, a proprietary braking system and a safety-rated steering system, which has been developed in-house.
At the centre of it all is the Digital Backbone, which receives health and performance data from each of these installed subsystems in real time, while also sending commands to each of them.
For non-Blanc Robot integrations, Applied EV works with its customers to integrate the Digital Backbone into a nominated vehicle architecture. This, it notes, can be anything from a specialty vehicle through to a mass-production passenger or truck application.
“Importantly, once the system has been integrated into a first architecture, subsequent architectures can be delivered rapidly, underpinned by our internal automotive knowledge and capabilities,” Broadbent says.
“It might sound simple, but it’s not easy to design for simplicity, and it’s very refreshing when you start to unbolt traditional components and realise definitively [that] your system is going to keep driving autonomously and safely without them.”
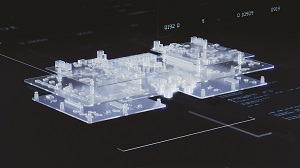
Inside the Digital Backbone
The Generation Six Digital Backbone central control unit (CCU) has four printed circuit board assemblies (PCBAs) compacted within an enclosure dimension of 215 x 295 x 54 mm. Each PCBA has an average of 12 layers of copper to accommodate the Digital Backbone CCU design’s complexity and required automotive robustness standard.
“We run our two main processor cards on the CCU. As well as embedding the most central parts of our autonomy software stack, they also have some logic subroutines to help perform arbitrations; for instance, when there is slightly different sensor readings coming in from doubled- or tripled-up sensors,” Broadbent says.
Assuming dual fail-operational redundancies has been a key part of the Digital Backbone architectural philosophy, going back to the original safety cases guiding Applied EV’s earliest engineering forays, which indicated to the company that compliant vehicles must, by design, have multiple power supplies going to each processor card.
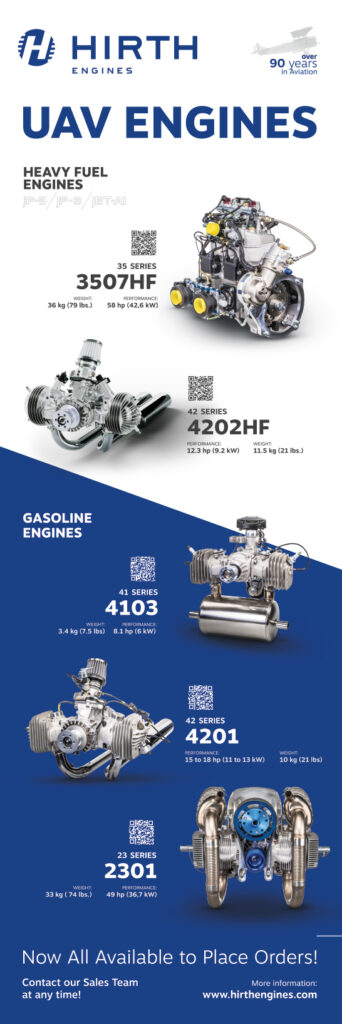
“You’ve got to make sure any one power connection could go down and the system would keep on running,” Broadbent explains.
Above the CCU is a large connector board, which carries the autonomous driving inputs via two large, 50-pin rectangular connectors, and two main bus connectors, which are also
50-pin devices. A variety of smaller connectors are also present on this board.
Below the CCU is the body control module (BCM), designed for managing vehicle ancillary systems – such as headlamps, infotainment and other cabin features, and locking devices – with about 200 I/Os designed into that board for such application-specific components.
“The BCM can be programmable. It’s where our partners have full, open access to write their own functions – whether that’s for their own connectivity features, customer-facing content or for interfacing with some traditional vehicle components,” Broadbent adds.
In addition to these boards within the Digital Backbone, Applied EV routinely assembles test boards, mounting electronics to perform automated tests, such as for electromagnetic radiation, extreme temperatures, vibration and other variables.
“At an architectural level, TÜV SÜD has certified the Digital Backbone as representing a suitable foundation for fulfilling the requirements of ASIL-D per standard ISO 26262. We’re therefore continuing subsequent design and implementation phases towards mass production,” Broadbent says.
Peering across the boards, one finds a heavy diversity of semiconductor types, from high-current switching transistors for the motor controllers to low-voltage network controllers for driving signal buses throughout the module, with the network carried from component to component by a wide array of rectangular and circular connectors.
Rectangular connectors do, however, make up the majority, given their generally thinner shape than the circular ones, and automotive- and mining- grade connectors have been used to guarantee the Digital Backbone’s survival in the event of heavy exposure to the elements.
“We recently moved to NXP’s S32G family of vehicle network processors, which are designed to accelerate the shift to simplified domain and zonal-based vehicle architectures,” Broadbent notes.
Low-latency autonomous driving
The pertinent performance metric targeted throughout the development of the Digital Backbone’s CAN and Ethernet buses has been latency. “The main high-level principle guiding our engineering has been the safety rating of our by-Wire functionality,” Broadbent comments.
A typical, commercially available road car with the bare minimum of modifications for autonomous driving is likely to experience latencies of up to 100 ms between the command being submitted by the ECU and that being executed at the tyre. Applied EV, by contrast, is targeting a latency of less than 20 ms.
“Engineering a lower latency into your autonomous driving system corresponds to a faster response time. This is very important for performance and safety, because it frees up processes and bandwidth for addressing other tasks, so achieving that realises a tangible compounding effect in terms of how we can optimise and shrink down our system,” Broadbent says.
Key contributors to reducing latency include a mixture of prudent component selection and programming rigour with regard to the network and the embedded software. On top of this, a huge part of the company’s effort has gone into careful management of signal prioritisation across the network bus.
“Going through the system processes has been fundamental to creating the right bandwidth architecturally for fast computational processing,” Broadbent says. “After that, it’s a matter of combing through software algorithms to develop highly efficient code. You can buy fast hardware, but you need to spend a lot of time developing fast software.”
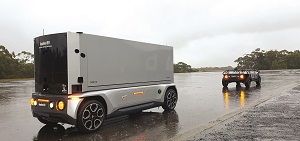
Software development
The arrangement of PCBs in the Digital Backbone’s hardware stack is somewhat echoed in the map of software modules responsible for the Blanc Robot’s sensor processing and control network.
To achieve that, Applied EV forgoes traditional coding in favour of model-based software engineering, requiring the entire system architecture to be drawn up and processed via a V-model from the very beginning.
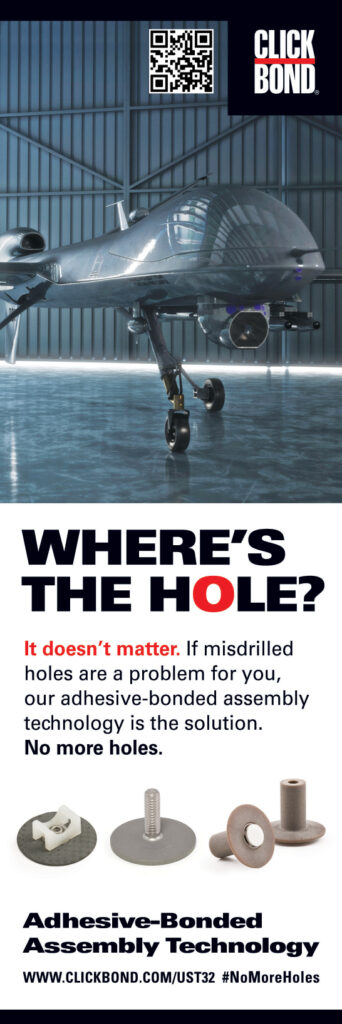
A V-model, also known as a Verification and Validation model, is a category of software development lifecycle in which the software is produced sequentially in a V-shape, starting with the gathering and analysis of requirements. The developer then progresses to the design, implementation, testing and maintenance of the software, with each developmental stage being tested before proceeding to the next, such that the following one can be informed by the results of the prior.
“There is a V-model for every single board and component, and doing that ensures we have full traceability of every software and hardware choice, from our upfront requirements to final delivery. We have leveraged significant automated code generation to get it done, and as difficult as it has been, it is the only way we could have achieved the safety rating we have,” Broadbent says. “Our programmers do find traditional coding more tangible and more real. The model-based software design architecture, by contrast, is extremely complex and it’s more heavily front-loaded.”
As per the ISO standards, all of the Applied EV’s software tool chains are required to be audited and approved by certification bodies as credible and safety-rated, so the selection of approaches for producing algorithms is defined by the required approvals.
“We know traditional coding is preferred by many, so we did produce an API and SDK for people outside of Applied EV to program certain Blanc Robot functions using traditional coding methods,” Broadbent says.
Computer to body
Just as the Blanc Robot can be adapted by application engineers and systems integrators for specific use-cases, the Digital Backbone, as a sensor-agnostic, monolithic solution, is expected to be available as a standalone product to other manufacturers in the future.
“For another company to implement the Digital Backbone into a vehicle, we would prefer them to have an EV platform,” Broadbent says. “To control a vehicle via software you need an electrified, digital system. To make a traditional vehicle into something that can be software-defined and safety rated, Applied EV needs to significantly replace, modify or adapt the necessary components.
“The real win for us is when we collaborate with an OEM to create mutual ground for collaboration. For example, with Suzuki’s platform, what they have on offer is what we call a ‘body on frame’ architecture, which relies on the idea of removing the top and being left with a ladder frame, and upon that we can build extra systems, purpose and scale.”
From composites to metals
Up to the fifth generation, the Blanc Robot looked very similar to a unibody chassis as it has both upper and lower stressed-skin structural elements for bearing tension and compression.
“Those elements are completely hollow on the inside, and are built around the packages of batteries and compute electronics,” Broadbent says.
Early in the development of the Blanc Robot, Applied EV had been interested in working with carbon fibre for its structural parts (much as the automotive industry increasingly is, and as motorsport already does), but concerns over its electromagnetic conductivity – and how that might block radio signals or cause EMI build-ups – motivated the move to glass fibre.
“We ended up working with a company in Japan called Teijin Automotive Technologies, which has a US-based subsidiary called Continental Structural Plastics. They do a lot of work for automotive OEMs in strong, lightweight body panels and similar components,” Broadbent says.
“Thanks to some great help from them, we were able to build a structure tying the whole ecosystem of parts together, it became immensely strong and extremely light.”
From the sixth generation onwards, Applied EV has adopted ladder-frame architectures with exposed systems to better work with automotive OEMs, and widen the opportunities to commercialise and manufacture the Blanc Robot at scale.
In this regard, future iterations of the structure are anticipated to utilise established automotive processes and metals, albeit with some influence from Applied EV’s side, where they see how such traditional structures could be improved or modernised for the needs of autonomous vehicles.
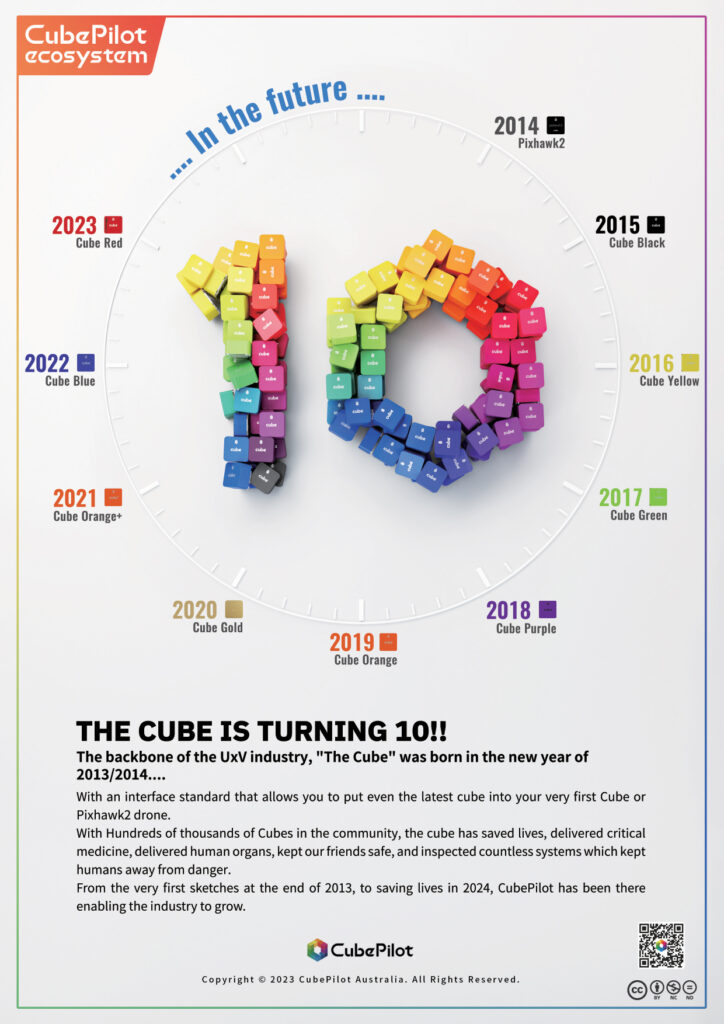
Open navigation
Notably, the Blanc Robot does not come with a sensor architecture for a few reasons. For one, Broadbent and his team view the world of autonomous navigation sensors as mature enough that there was no urgent need for Applied EV to try and develop or configure the ‘perfect’ combination of sensors in-house.
So, from the company’s perspective, Lidar, stereo cameras, thermal cameras, 4D radar or ultrasonics are technologies that have all matured and become readily available since the introduction of autonomous vehicles.
It additionally surmises that each autonomous driving partner has its own preferred configuration or array of sensors, with no two being identical. This can come from certain sensors being more appropriate to the working environment (thermal cameras, for instance, proving superior to electro-optical cameras in low-visibility conditions) or some sensors fitting better to certain vehicle bodies and chassis than others.
For many companies previously covered in this publication, geographical proximity to certain suppliers or positive experiences with them was also a key influence when it came to selection for vehicle and component manufacturing.
But more than the particulars of sensor architectures, Broadbent sees the real frontier in autonomous driving (and the engineering thereof) today as defining the edge cases. “It’s about working deep in the AI engine, understanding how to deal with events the system may not have seen during on-road testing,” he says.
“Autonomous driving software modules for core functions like path planning, free space allocation and even object classification algorithms can now be acquired from technical partners, thanks to the rapid pace of software development of the autonomous ecosystem.”
The standard Blanc Robot does, however, integrate MEMS inertial measurement units (IMUs) and GNSS receivers, as well as Ackerman-based steering and precise odometry into its navigation algorithms. This means tight turning circles are performed with inbuilt error to account for the vehicle’s inertia and centre of gravity, and to optimise dead reckoning in corners to reduce the potential for slip.
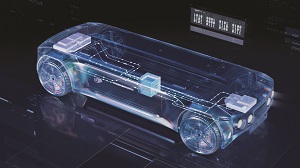
Lithium-titanate oxide
The Blanc Robot is designed with considerable battery pack space to allow for the higher end of customers’ range requirements, but Applied EV has taken care not to oversize the battery pack. Doing so would inevitably add a disproportionate degree of extra weight, given that the gravimetric energy density of battery cells remains far lower than 1 kWh/kg – estimates range from 0.01-0.2 kWh/kg, depending on the cell chemistry.
Therefore, an oversized battery pack would have made integrating a considerably more heavy-duty powertrain necessary to overcome the added inertia. That would then have increased the rate at which energy was consumed, which would have created the need for more onboard battery energy, thus resulting in a vicious cycle that has affected electrified vehicles for some time (and it is a major reason why many are far heavier than their equivalent ICE-powered counterparts).
The company has targeted 400 km of maximum range on the standard-issue Gen 6 Blanc Robot, the team having surmised that cabinless, software-defined vehicles should not need to travel more than 400 km between opportunities to charge or swap packs. Once the end-user’s driving cycle is identified, the charging cycle, and thus the battery, can be right-sized to maximise useful payload space.
Due to the ladder frame of the Jimny, the available space in the Blanc Robot for a battery is not square in shape. Instead, it measures about 700 x 170 x 2000 mm. By targeting 51 kWh of energy in the battery pack, Applied EV’s team has left enough space and carrying capacity (and put in enough energy) for a usable payload capacity of 1500 kg.
For previous generations, the company had constructed its own packs in-house, including performing its own laser welding and producing its own high-voltage BMS and junction boxes, mostly due to the difficulty of shipping prototype battery packs via airfreight.
The anode chemistry chosen for the cells in Applied EV’s Generation 5 Blanc Robot is lithium-titanate oxide (LTO), which we also saw in Clevon’s CLEVON 1 roadgoing UGV for logistics deliveries (Issue 47, December 2022/January 2023), chosen by the Estonian manufacturer for its safety properties.
“We believe LTO really is the safest chemistry presently available,” Broadbent says. “From a performance perspective, it offers very high rates of charge and discharge, which compensates really well for its low energy density relative to other cell types.”
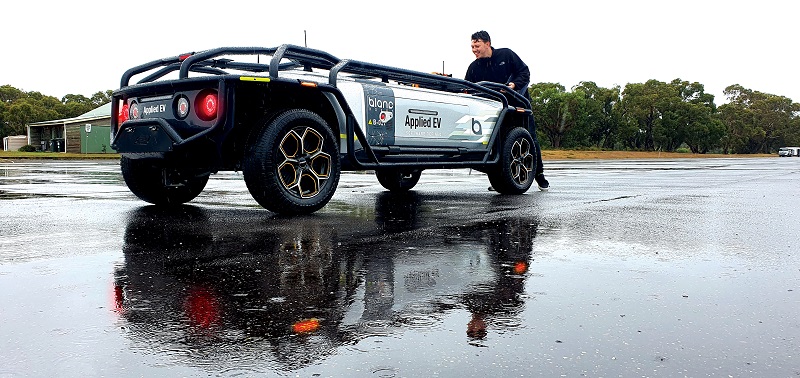
The powertrain
From the Gen 5 to the Gen 6, the Blanc Robot went from four highly customised in-wheel electric motors to two centralised-drive units at the front and rear (as is typical with OEM and OEM-reference designs for 4WD EVs).
Specifically, each motor is rated at 68 kW continuous power (99 kW peak), with a maximum motor speed of 11,300 pm and a continuous torque of 120 Nm (176 Nm peak).
“With such a strong reputation of reliability, capability and credibility, we wanted to preserve a lot of carryover components of the Suzuki Jimny ladder-frame architecture to maintain the DNA of the vehicle, and also manage the final cost of the vehicle while increasing its speed to market. Therefore, the electric motors have been coupled with a unique custom EV transmission, integrated with the original axle housing,” says Broadbent.
“Similarly, it was important to us to preserve traditional hardware in the braking system. We’ve partnered with Tier 1 and Tier 2 automotive suppliers for additional electronic braking components, which enables us to elevate the platform to be software-defined in its braking behaviour and achieve an ASIL-D safety rating. Additionally, the bidirectional steering setup enables advantages such as a very tight turn radius of 5.7 m when we’re in four-wheel steer mode.”
To maximise the Blanc Robot’s range, Applied EV has put significant effort into identifying its ideal tyre to balance overall performance and rolling resistance. “Anyone in automotive knows a high rolling resistance is the greatest source of inefficiency you can have. It isn’t mechanical or drag losses,” Broadbent says. “In our case, a narrower-width tyre is great for minimising rolling resistance, and there’s some nice high-efficiency compounds out there for the load rating we’re trying to achieve, as well as for the operating speed planned for the Blanc Robot.”
The Blanc Robot currently has a maximum speed of 80 kph, although this is a software-defined limitation in the system; hence, it cruises at 80 kph.
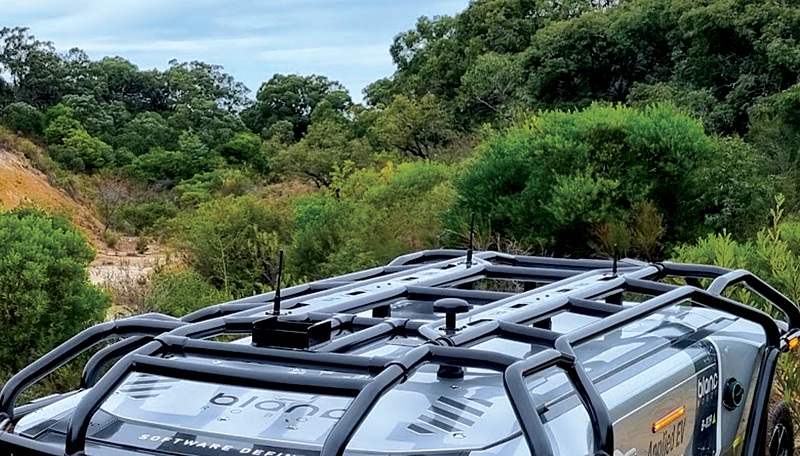
Secure connectivity
As connectivity is an essential component of deployments of the Blanc Robot in industrial services, the Generation 6.2 Digital Backbone CCU has integrated 4G and 5G LTE, as well as wi-fi and Bluetooth WIFI/BT. These integrations enable secure over-the-air as well as cloud connectivity, with GNSS connectivity also installed, as mentioned, to ensure precise localisation and orientation, and real-time telemetry.
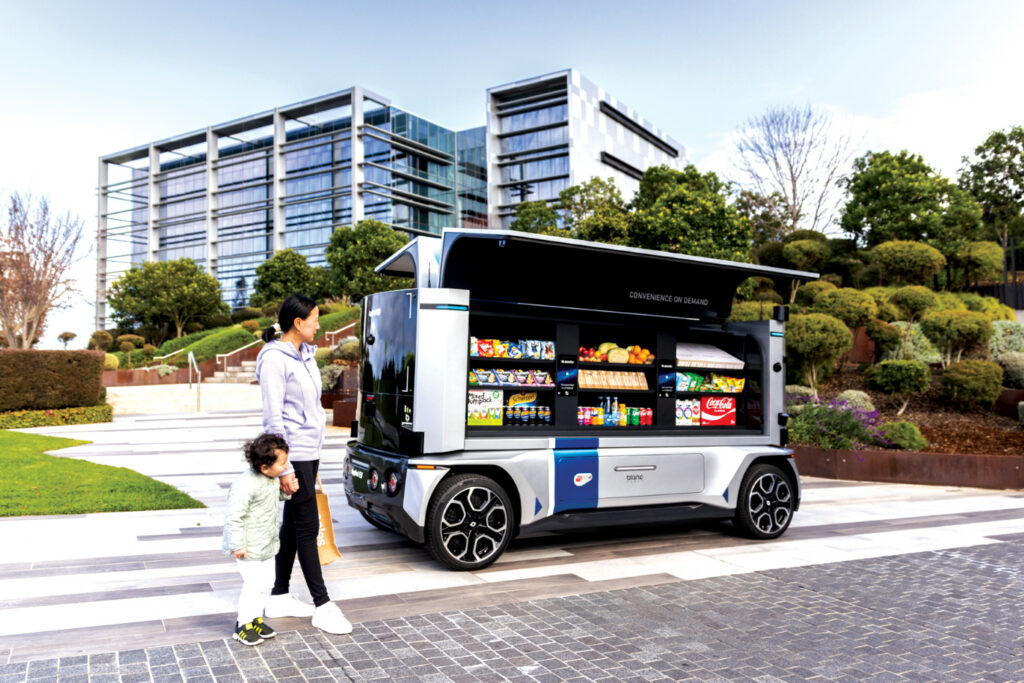
Future moves
As the industry becomes aware of the benefits of using autonomous vehicles across logistics and commercial applications where they can be deployed safely, technology companies such as Applied EV are moving from development to commercialisation.
“As far as we can see, automakers aren’t at the point where they’re going to make vehicles that can integrate the necessary sensor and computer complement for fully autonomous safety-rated driving,” Broadbent says.
“Through a mix of clear vision, smart design and hard work, we have delivered our software-defined vehicle in a solution that is safety rated, as well as being highly adaptable and future-proof for autonomous applications, providing capabilities that are years ahead of many OEM roadmaps.
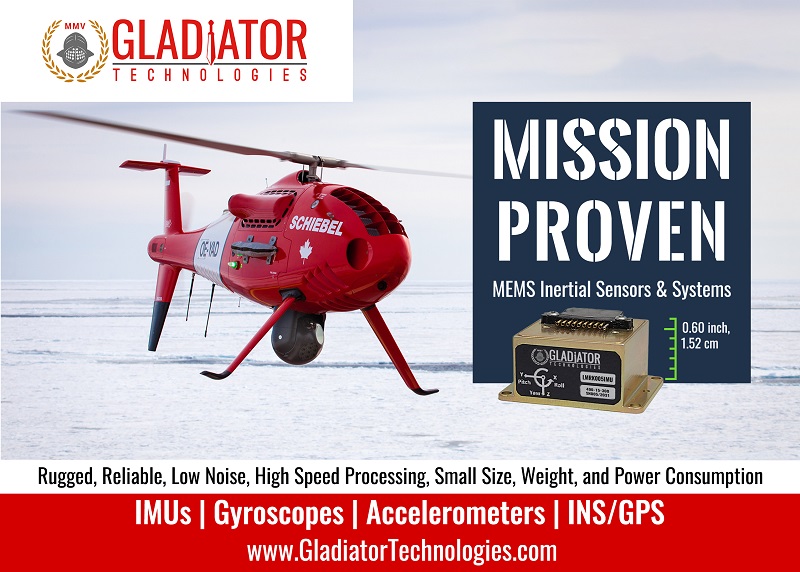
“Another key goal of ours is to deploy the Digital Backbone in a range of vehicle architectures, and we’ve built a business model to support this, with a strong focus on automotive integration capability. We’re already working on several vehicle integrations and are ready to expand.
“Our customers and partners can fast-track their software-defined vehicle-development plans, maximising the potential for cost reduction, decarbonisation and new revenue models, while addressing their strategic objectives for a brighter transport future.
“To do our part in making that happen, we just need to keep maturing our tech, testing it over and over, and making it as safe as possible.”
Key specifications
- Blanc Robot
- Battery-electric
- Bidirectional steering
- 4WD
- Dimensions: 4 m x 1.7 m x 0.8 m
- Curb mass: 1200 kg
- Payload capacity: 1500 kg
- Cruising speed: 80 kph (software limited)
- Maximum speed: 80 kph (software limited)
- Maximum range between charges: 400 km
- Maximum endurance: depends on mass, speed and use case (duty cycle)
- Maximum charging rate: 6 C
Some key suppliers:
- Automotive OEM: Suzuki Motor Corporation
- Semiconductors: NXP
- Design and quality assurance software: Siemens
- Engineering tool: MathWorks
- Tool chain and engineering process accreditations: ISO 9001
UPCOMING EVENTS
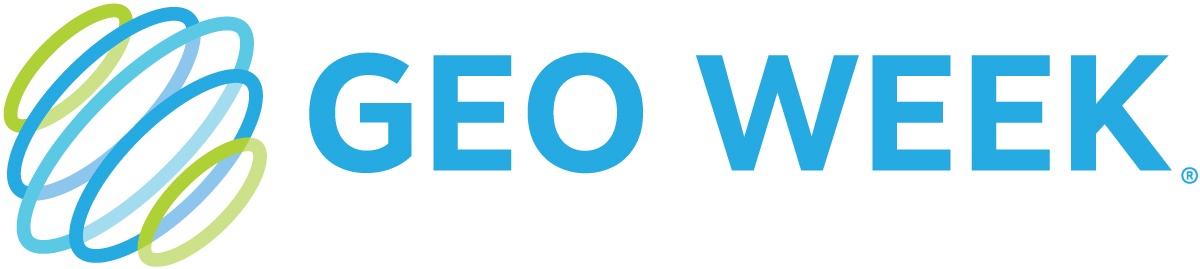
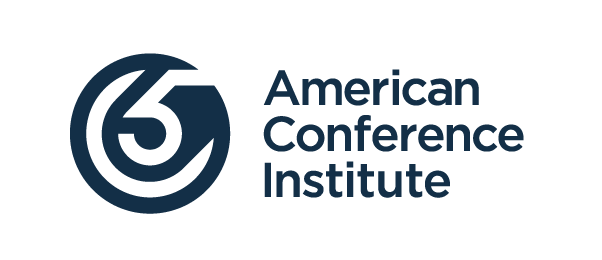
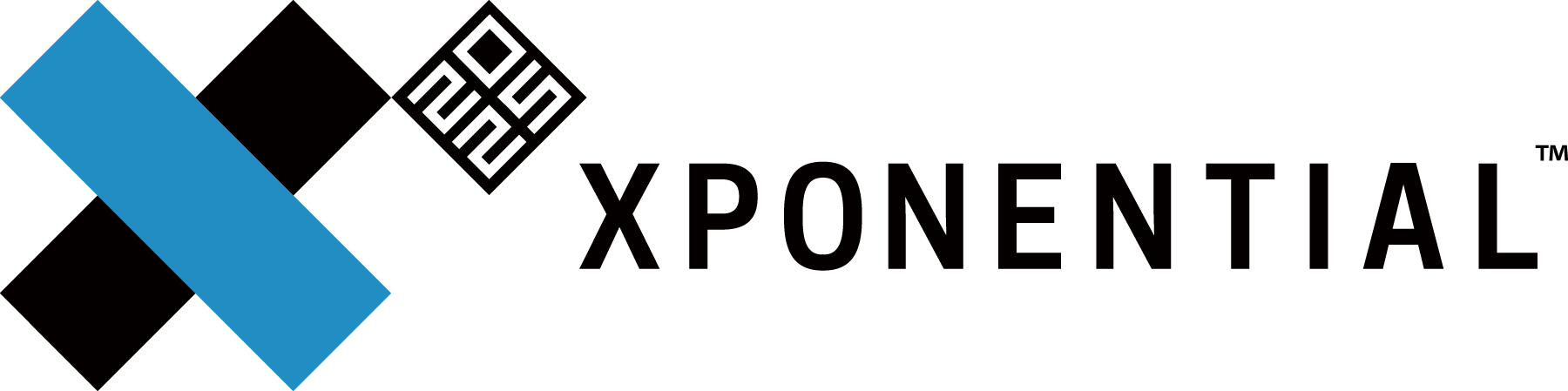
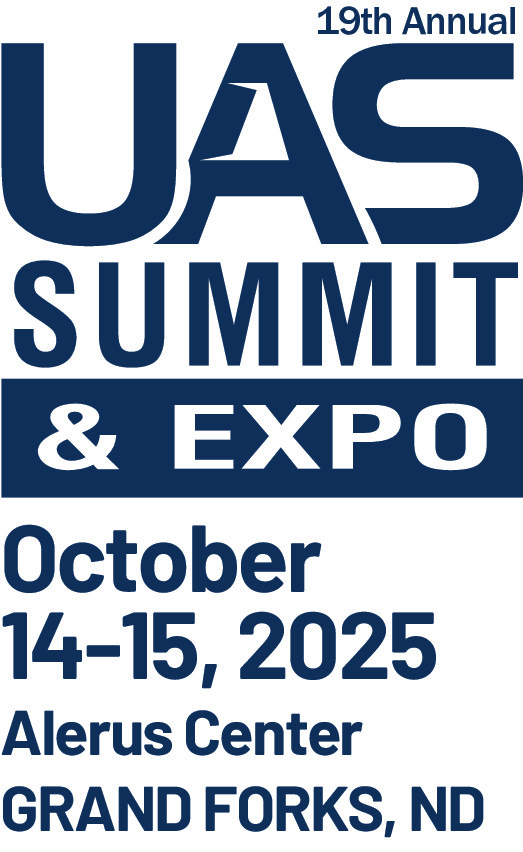
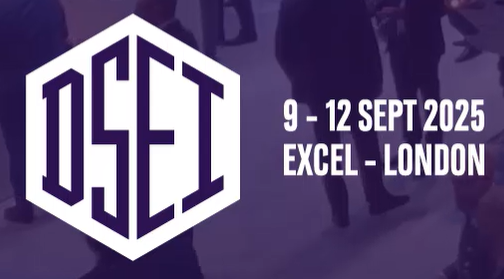
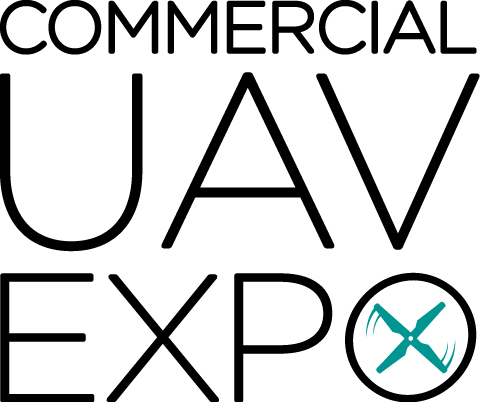
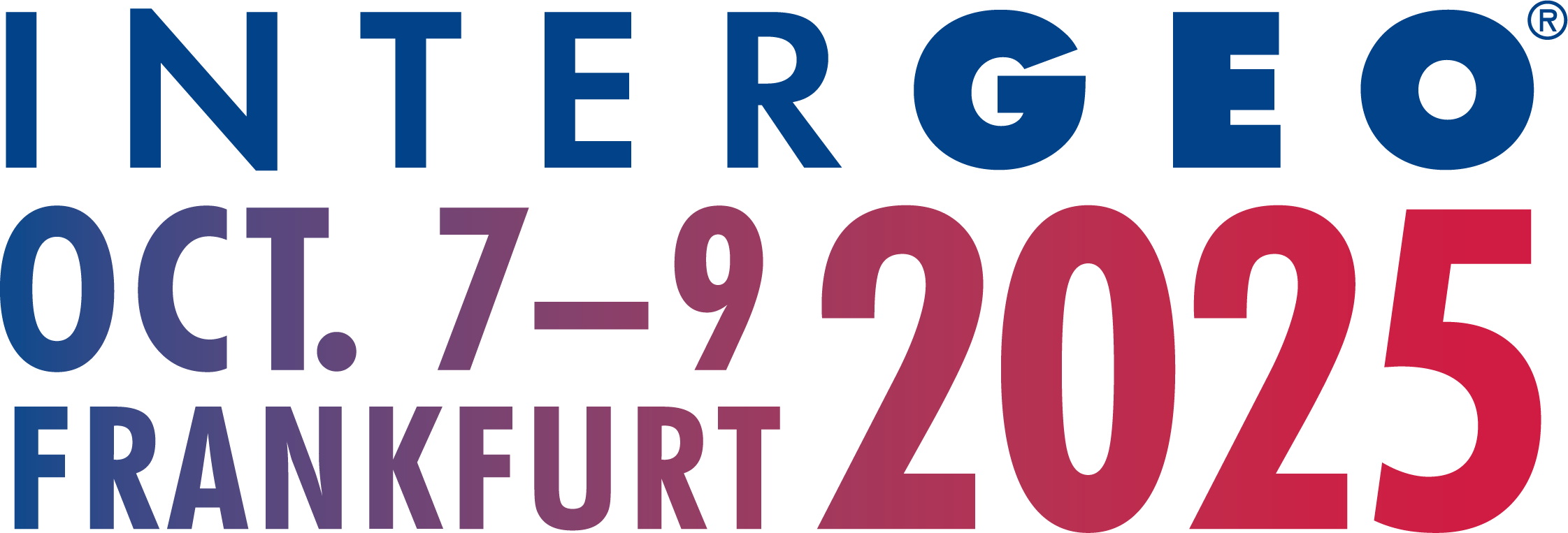
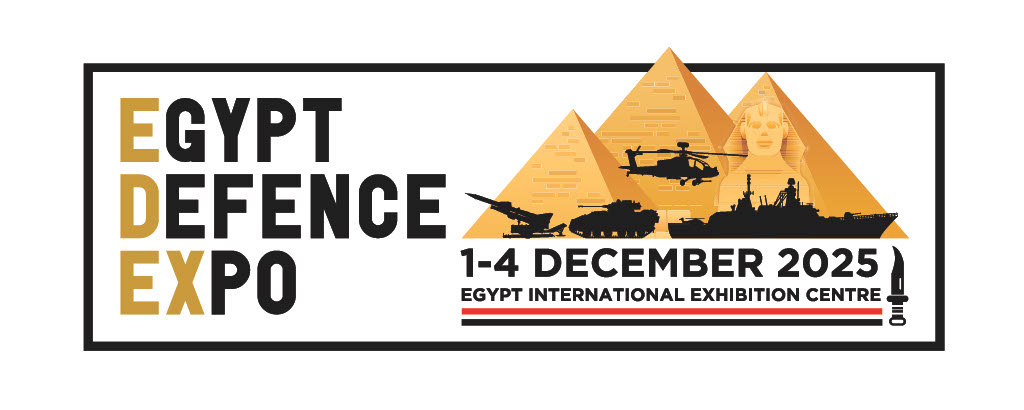
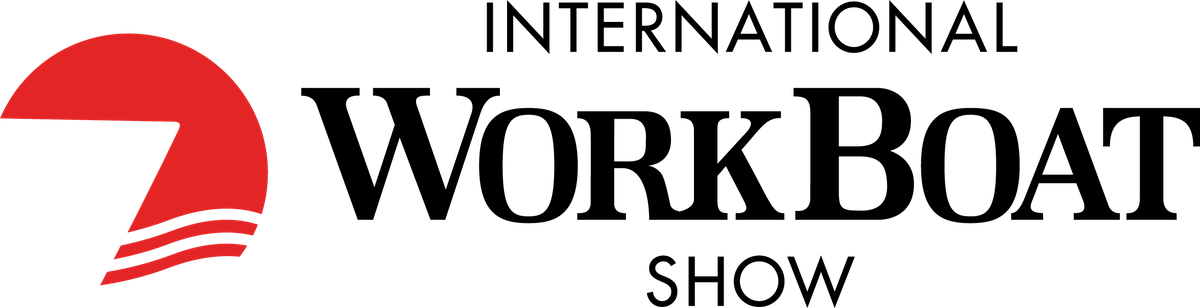
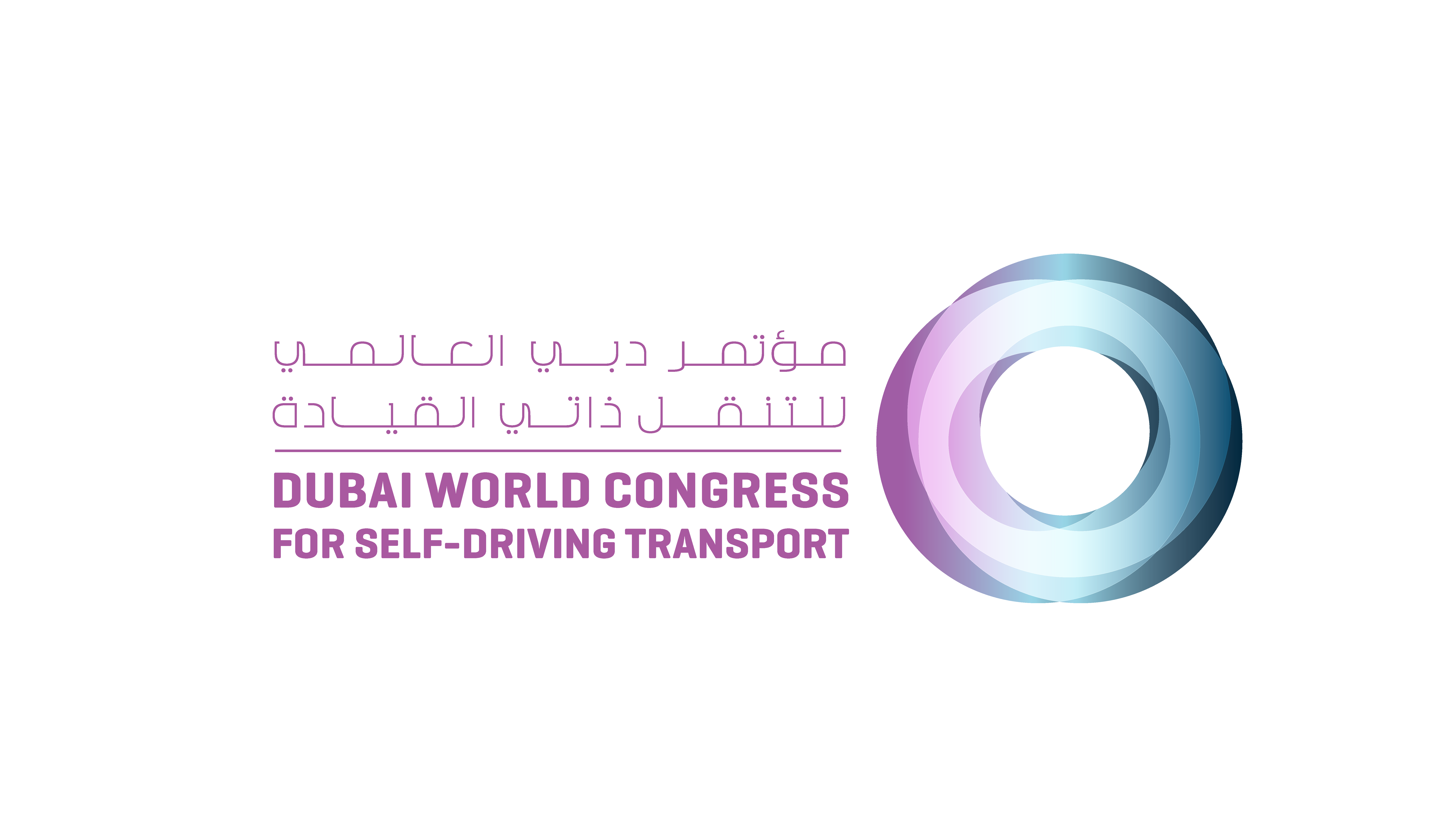
