Safety testing of Amazon UAVs
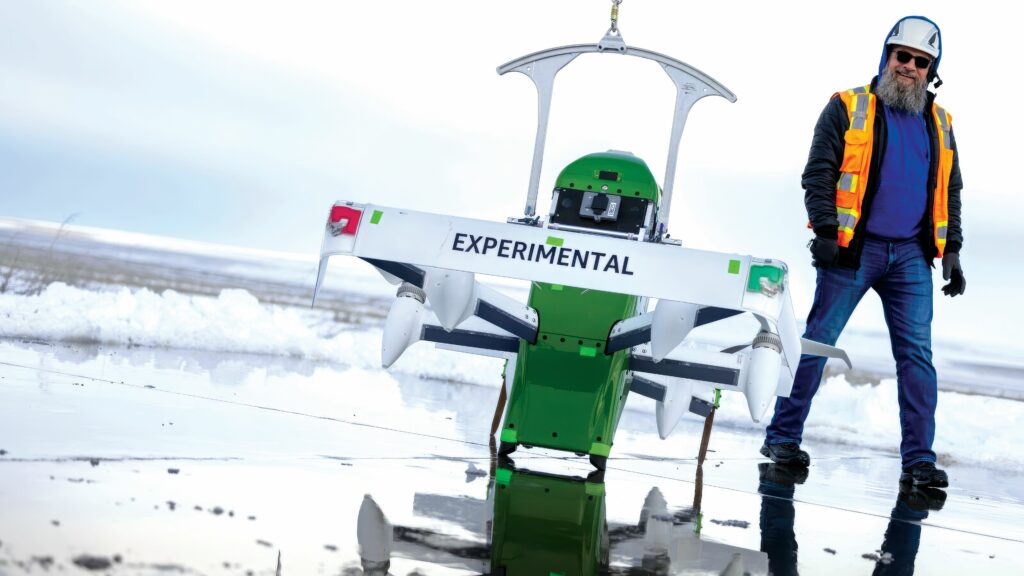
(Image courtesy of Amazon)
Amazon has received approval to begin UAV deliveries to customers following a key safety programme, writes Nick Flaherty.
The MK30 UAV has been specifically designed for airborne Beyond Visual Line of Sight deliveries using an on-board detect and avoid system.
The MK30 went through an aerospace-grade certification process and flies twice as far as Amazon’s previous craft, is about 50% quieter and is built to fly in rainy weather.
One of the issues with operating in Phoenix, Arizona, is the greater quantity of airborne dust than found in other places. One example of the testing process was the revelation that dust can sometimes interfere with the readings of the altitude sensor. In extremely rare cases, this could have caused the drone to receive an inaccurate reading about its altitude.
The ARP4761 standard is designed to assess the safety of an aircraft and it has been adapted for delivery UAVs.
The test team also drew ideas from the automotive industry’s expertise in testing smaller vehicles, the self-driving car’s approach to autonomous creations, and military standards for system safety. Following these protocols helped the team identify and design-out points of single failure, such as using the same power source to supply a component and its backup.
In a ‘MEP out test’, the team used software to stop the MK30’s motor, its electronic speed controller, or propeller, to verify that it can stay in flight, safely return to the launch site, and land at a designated pad that is reserved for such scenarios.
In switchover testing, they injected a failure that knocked out the primary flight computer, to verify that it can switch to a backup that can take control and safely return the drone to base. Both tests were conducted at different points of a mission: in horizontal and vertical flight, right after launch and at the moment of delivery.
Before a flight, the Airspace and Mission Orchestration System generates a high-fidelity model of the operating area. That model creates flight paths that avoid known obstacles such as buildings, bridges and power lines.
However, knowing that there is no guarantee of a clear landing spot at a customer’s delivery location, the team created a test regime that ensures that the UAV can understand when it shouldn’t deliver a package while hovering 4 m above ground.
As a rule, the operations team restricts the UAVs to specific airspace that should be clear and monitors the ADS-B signals that aircraft use to broadcast their position. The ability to spot and dodge an aircraft might be the last option, but it also needs to be tested as realistically as possible.
“When we test the detect and avoid capability, we’re flying an airplane at the UAV,” said Adam Martin, who runs Prime Air’s flight test and safety organisations. “We’ll fly a helicopter at it and they’ll do it a whole bunch of times, with different routes, angles, heights, speeds and scenarios. We ran many, many tests of that type.”
UPCOMING EVENTS
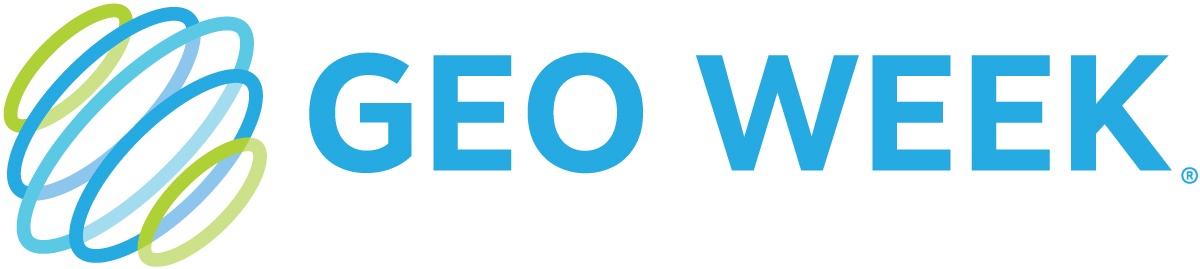
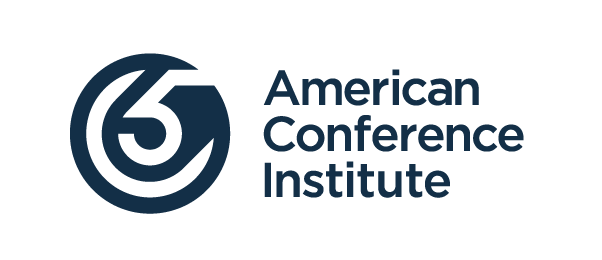
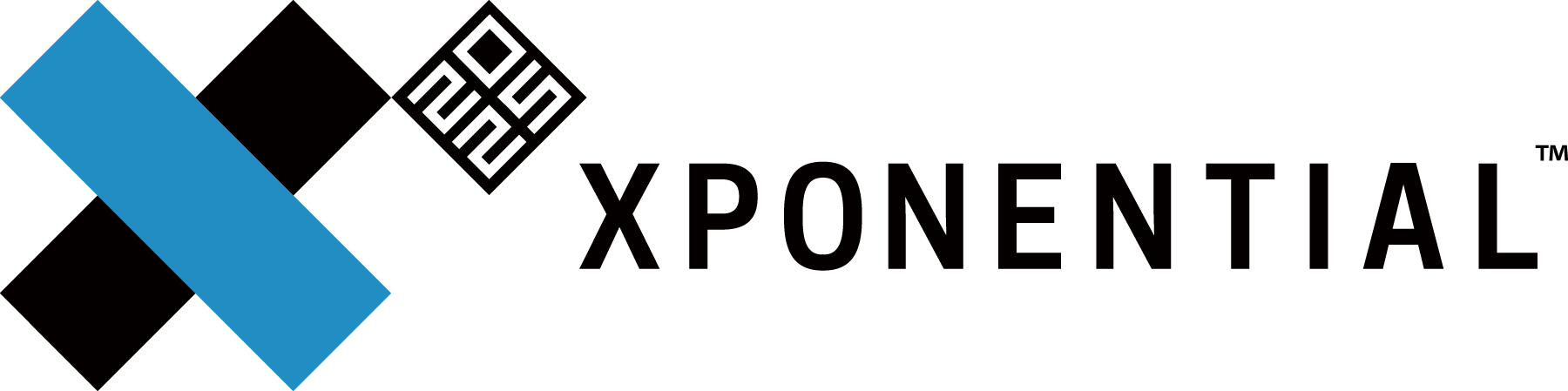
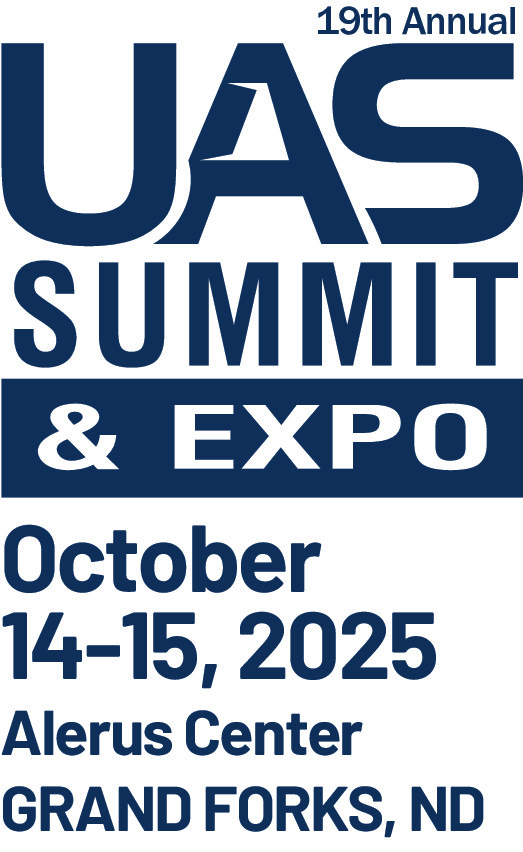
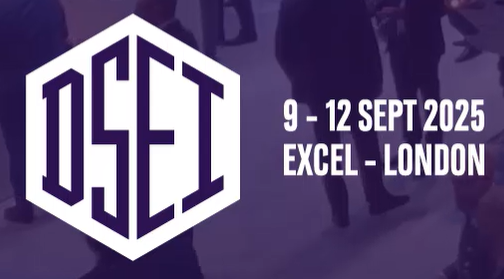
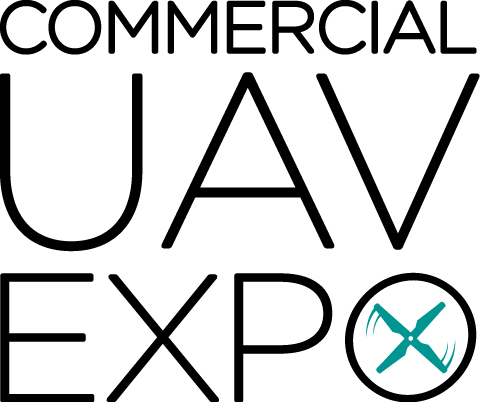
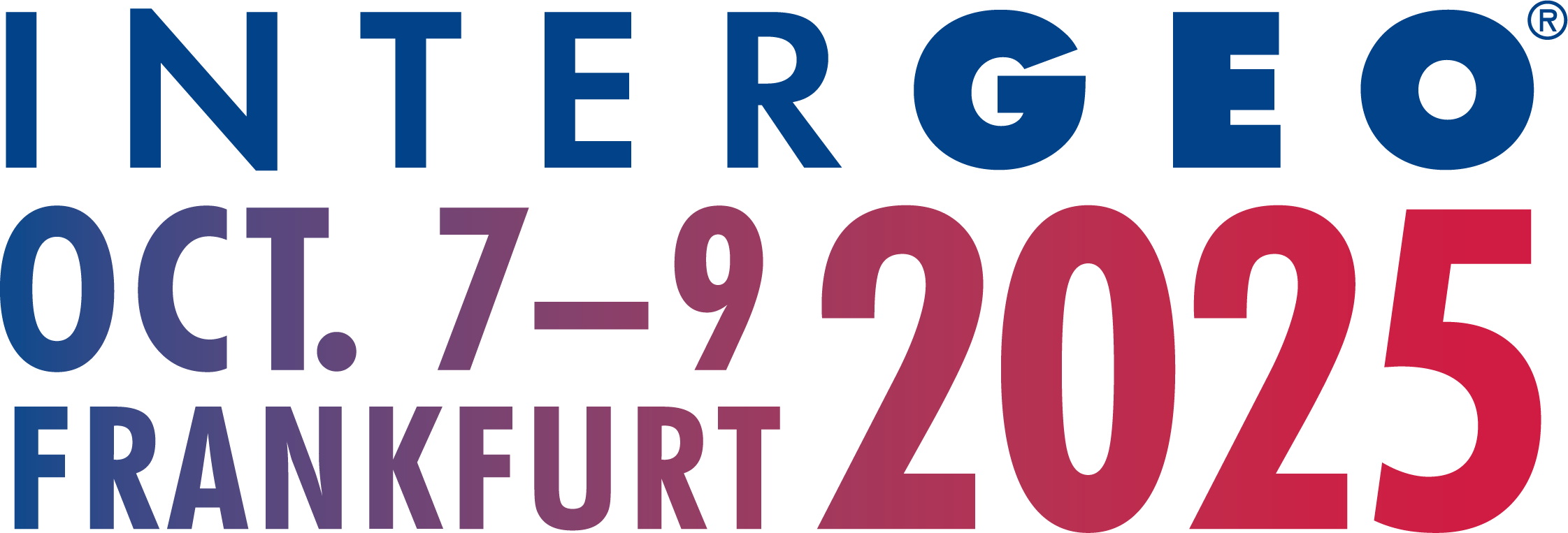
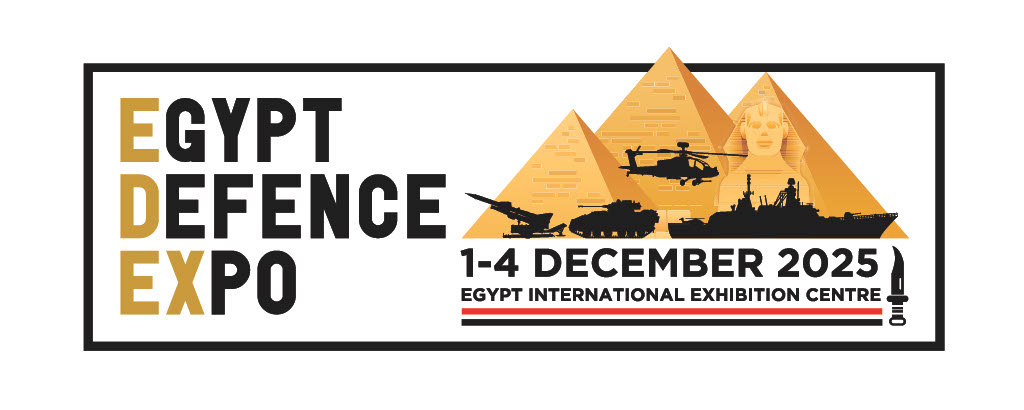
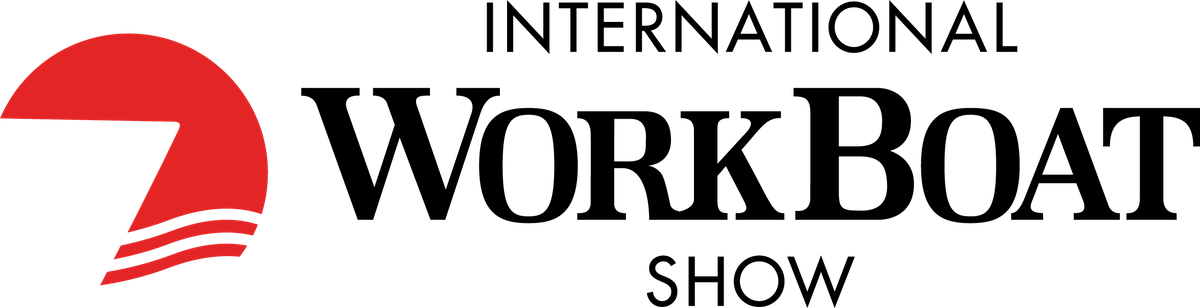
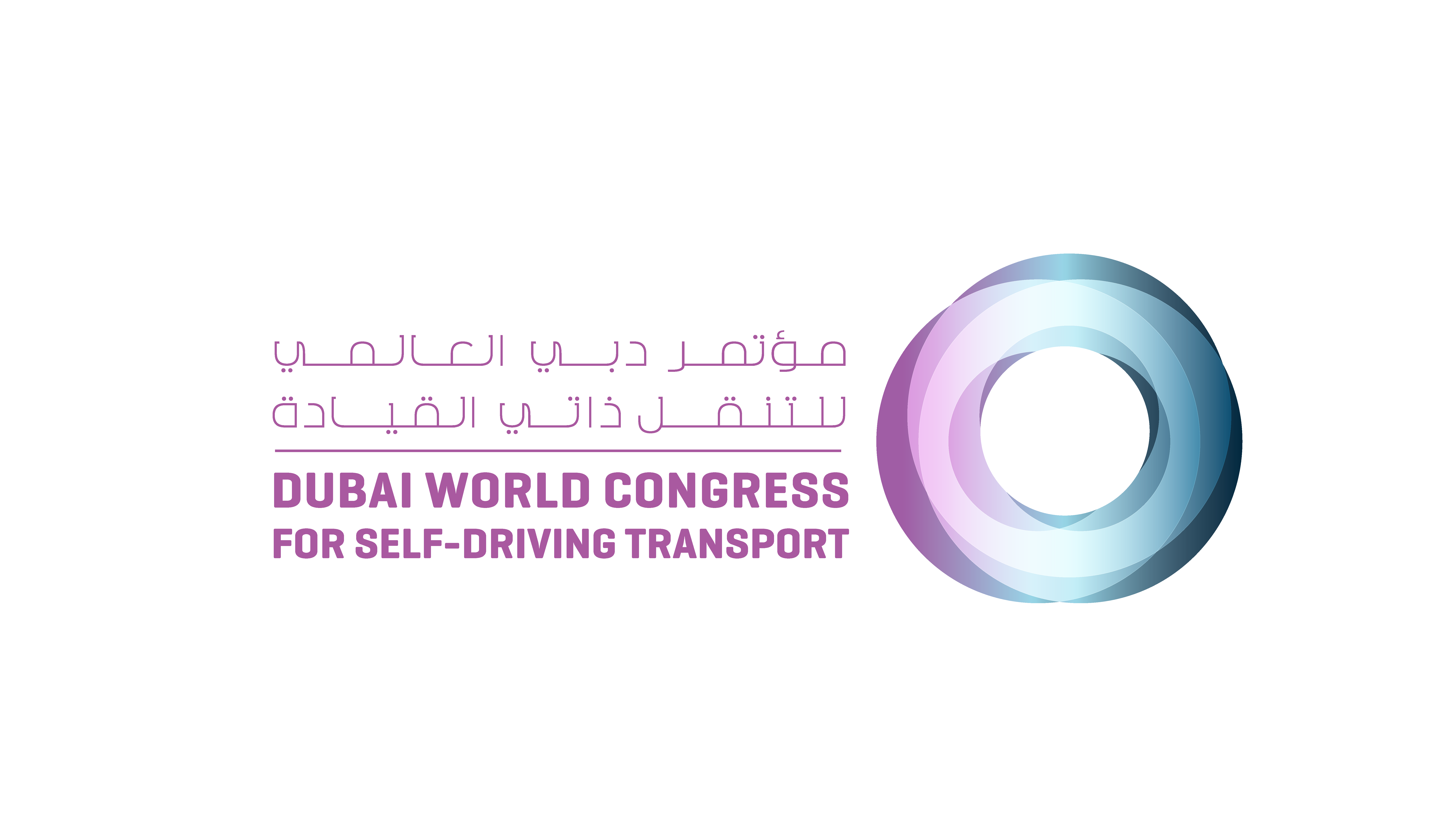
