New take on stability
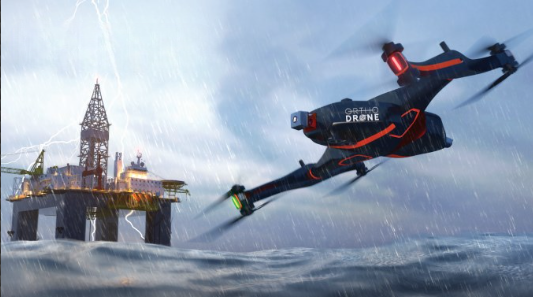
(Images courtesy of Orthodrone unless otherwise stated)
Peter Donaldson investigates a multicopter sturdy enough to endure harsh environments – the idea was born in Antartica after all
Orthodrone is developing a multicopter technology it calls Pivot, which embodies the radical concept of stabilising the entire fuselage while the propulsion system moves around it to compensate for wind coming from any direction.
The purpose of this departure from convention is to exploit the speed of response available when the rotors have far less mass to move around any axis when the fuselage is effectively decoupled from them in pitch and roll. The result is a platform stable enough to make the most of the helicopter-grade sensors it can carry.
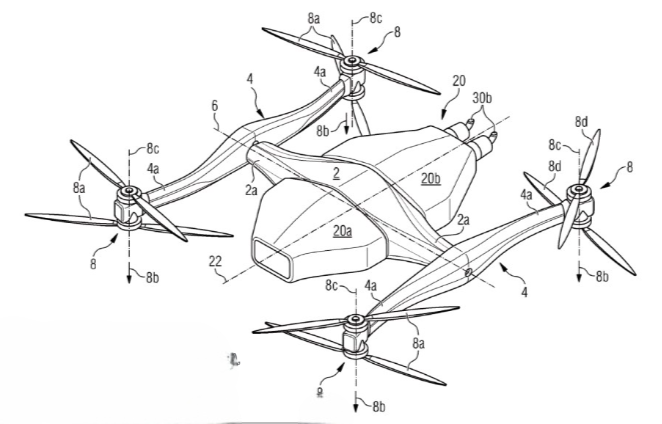
Antarctic mishap
The idea was born of a mishap suffered by the brand-new data acquisition business during a surveying trip to Antarctica in 2019, according to CEO Juri Klusak, who started Orthodrone straight out of Kiel University with friend and fellow geospatial data scientist Julian Teege, now Orthodrone’s COO.
All the way down south, the €60,000 (£45,000) industrial-grade multicopter they bought from a reputable manufacturer failed due to a temperature related fault in its flight controller.
“I was standing in front of the Belgian Antarctic research station and I had this big drone with €250,000 worth of sensor equipment. Everyone was excited to see it flying – and it fell out of the sky,” he recalls.
“I had a backup, a smaller drone, and I got enough data for the project, but it was not what I wanted for the company.”
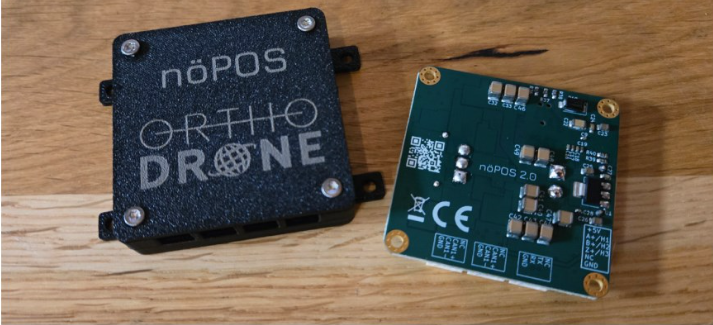
Scientists turn UAS developers
Klusak studied environmental geography and management at university, working with consumer drones for data acquisition, modelling coastlines, gauging the risk of erosion and mapping sea grass, presenting his thesis at the European Geoscience Union (EGU) in 2018.
“I showcased my bachelor’s thesis and my data sets, and I realised then that within the science community there was a massive need for that kind of data and there was a huge knowledge gap in how to achieve quality data, how to manage it and how to analyse it.”
Upon returning to Germany, Klusak consulted a few friends and former classmates, including Teege, and together they realised there was a promising business case. Their aim was to provide services centred on data gathered using consumer-grade UAS, but they soon found the available systems were lacking.
“We had a very clear vision for the company right from the beginning: we wanted to survey in extreme environments and generate very high-quality data, replacing helicopters in high-risk environments,” Klusak notes, lamenting: “I got back from Antarctica and realised that we were really shackled by the airframe technology.”
A subsequent operation based on an icebreaker reinforced the need for more reliable equipment for operating in extreme environments, and Orthodrone concluded that they should develop its own.
Klusak then ran the team’s idea past Mirko Denecke, whom he met in Antarctica while Denecke was the senior superintendent of the German Antarctica Station. “We got along really well, and it turned out that he’s an ArduPilot core developer,” Klusak says, adding that Denecke quickly joined the project.
Given their previous experience, it was clear that a significant payload capacity was essential to carry the kind of heavy, survey-grade sensor systems typically mounted on helicopters, as well as a flight time of at least two hours.
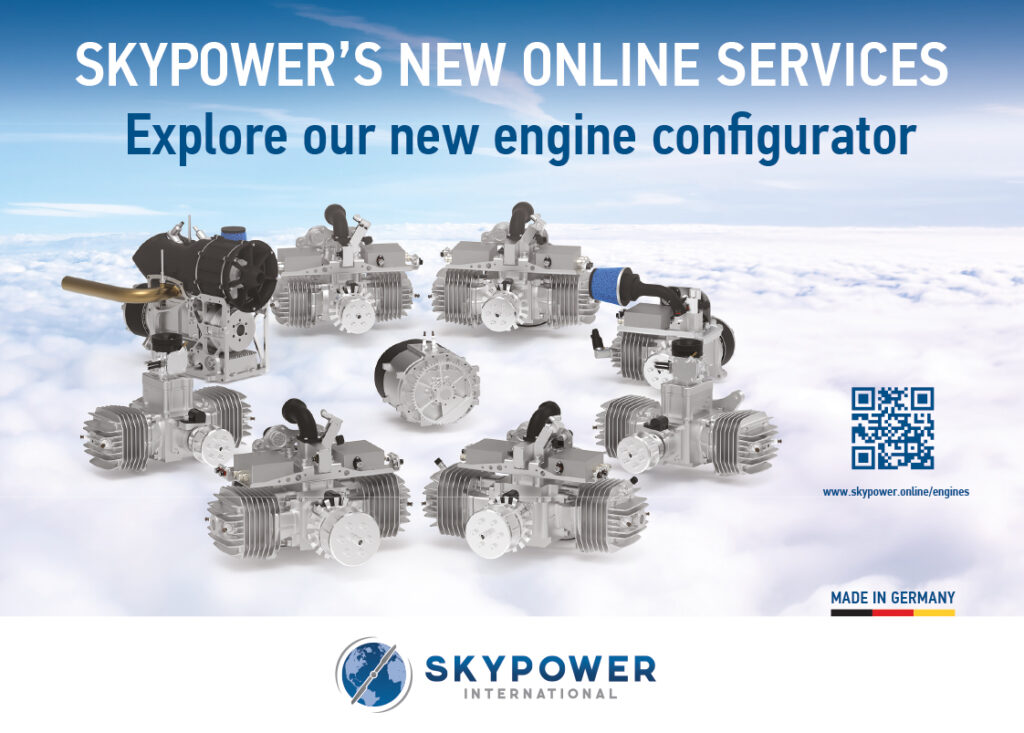
“We are at three hours now, with a 5 kg payload, so we’re pretty happy with that.”
The team also wanted something that would withstand very harsh conditions with wind gusts of up to 20 m/sec (72 kph). “We are very clear about our market,” Klusak says. “We’re focusing on offshore.”
It soon became clear that the vehicle would have to carry multiple gimbals, or a mix of gimballed and non-gimballed payloads, which proved to be cumbersome, he recalls. This motivated the team to find a solution to the data-quality issues arising from having multiple sensors with different positional reference systems.
“We went around that by making the drone a gimbal, because this way all the payloads are stabilised and have the same references – that loops back to our spatial data expertise.”
Klusak stresses that the position and attitude references for the payloads collectively are not those used by the UAV for navigation. These are higher-quality survey-grade solutions, such as Trimble Aplanix APX-20, which are rigidly connected to all the sensor systems and GNSS antennas within the payload bay, allowing for calibrated, highly accurate, multi-sensor payloads.
“This is where you get superior data quality out of all these systems.”
A fully stabilised fuselage makes a significant difference compared with any vehicle that carries a gimballed sensor and mounts its GNSS antennas on the fuselage, as is the convention, because the gimbal moves separately from those antennas, creating an undesirable offset.
“You can compensate for that by reading out the positions of the gimbal’s motors or placing extra IMUs on different parts, so you know where each payload is pointing, and then calculate the correction,” says Klusak.
“But then you’re always adding weight and complexity, and you are losing quality because each of those additions brings its own errors, and they all add up. If it’s one fixed system, you’re in a very different league.
“Also, because our system is always stabilised, the antenna is always at the same spot and always pointing upright. There are no lever arms, no parts moving around and you always have the entire sensor payload sitting exactly where you want it. There is no open point in the system where the errors add up.”
When a gust hits, the propulsion system moves around the fuselage, which supports the sensors, fuel storage and powertrain, correcting for pitch and roll so the sensors stay where they are, regardless of the flight direction or wind compensation.
“And this really is the trick,” Klusak says. “A good example is Lidar data acquisition. Lidar data depends on really good trajectories, so you know where you were in every split second of data acquisition, otherwise it doesn’t work.
“These trajectories depend very much on the position and attitude of the sensor, and then on the accuracy of how you record that attitude to compensate for the position sampling rate. Our system makes that a lot easier because the sensor attitude changes so much less, and eliminates all the little jerking motions usually associated with multi-rotor flight.”
Pivoting the yoke and the propulsion system around the fuselage involves moving significantly less mass than is typical for a drone of similar size. While many off-the-shelf gimbal systems have fairly big, heavy motors, Orthodrone is implementing “rather small” motors from Swiss manufacturer Maxon with Orthodrone’s own nöPOS control board and a custom drive system, creating a stabilisation technology that weighs no more than that of a mid-sized single-camera gimbal, Klusak notes.
Sensing the motion to which the servos react to stabilise the fuselage is a set of IMUs for which fast response is much more important than the low drift required for accurate navigation.
Addressing another category of use cases, Klusak says the Pivot concept solves what he regards as one of the biggest issues for heavy lift drones: the shift in the centre of gravity when the UAV picks up a load, particularly an underslung one. “With a Pivot system, you carry the load in the centre of the system, and it will fly very similarly, whether it is empty or fully loaded.”
He also sees an application for it in eVTOL air taxis, particularly those of a conventional multicopter configuration, which he considers likely to be prone to inducing motion sickness in passengers when subject to rough air, including gusty winds.
Using Pivot technology to control fuselage attitude, it is possible to control the direction in which occupants feel acceleration forces.
“It can make sure you just feel it pressing you into the seat. Then it’s just like gravity increasing a little, and we are all OK with that.”
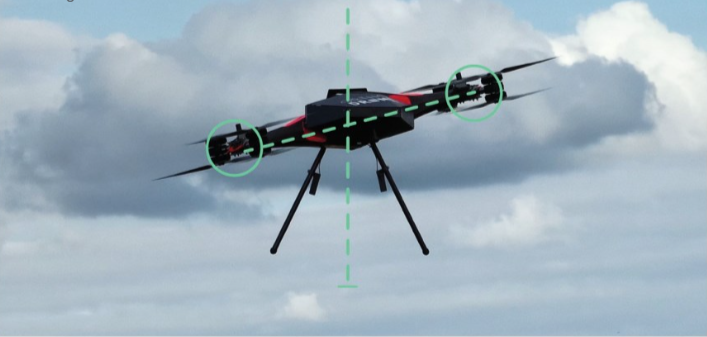
Development challenges
Klusak and his team faced a number of challenges in creating the Pivot technology, not least of which was developing a control scheme for a vehicle subject to complex coupled dynamics between the stabilised fuselage and the pivoting propulsion system.
They also had to undertake a weight-reduction process for most of the key components. For example, while it was easy to find electric motors with the power-to-weight ratio they were looking for, motor controllers fitting their specifications proved elusive.
“A big part of the job was downsizing the controllers, and we ended up redoing some printed circuit boards (PCBs). We’re a small team and we were very lucky with the talent we have acquired, so we have been able to do things like that in-house,” he says.
Having a core developer of ArduPilot on board has also proven valuable, Klusak says, enabling the team to determine how to use it to control more of the vehicle’s functionality directly.
“We started by running many of our systems on a companion computer, but now we are at a point where we are able to do more through-scripting and just run it on the autopilot, which is a great step for us because it needs less hardware.”
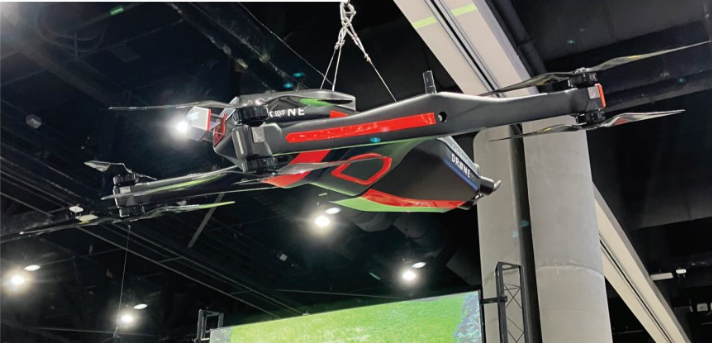
(Image courtesy of the author)
Proof of concept
The process of building and testing prototypes was spurred by the Covid pandemic when travel restrictions and lockdowns made it difficult for the team to complete in-person fieldwork. In November 2020, Klusak held a team meeting to introduce the idea of developing a UAV, and he recalls that no one had heard of the idea behind Pivot.
Despite Klusak’s worry that someone would tell the spatial data scientist to stick to his maps, the team thought the idea could work, and they were so enthusiastic that they built a proof-of-concept vehicle by the end of December. The 4 kg machine was not pretty, he recalls, but it flew around the office canteen carrying a raw egg, which survived the experience intact.
“Once you’ve proved that your idea works then the work begins,” he says. “The leap from an idea to a product is huge.”
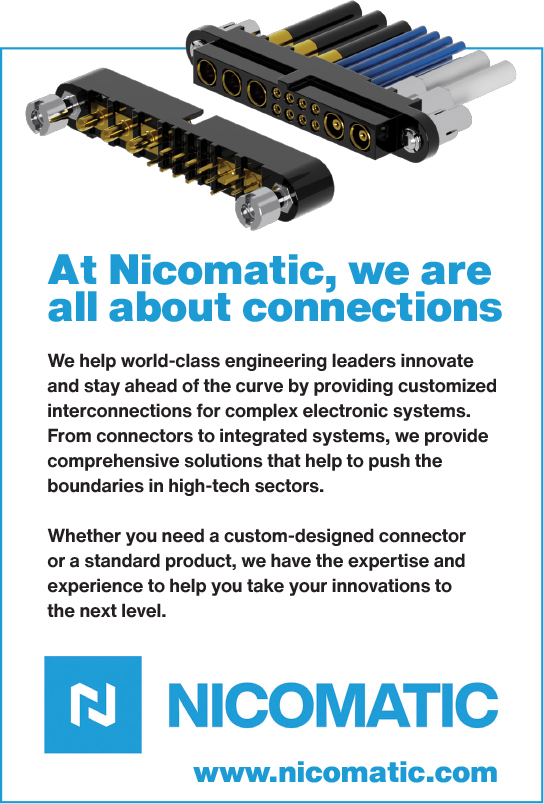
As they went through development, building subsequent prototypes, things changed drastically. “The first thing we flew looked like a cut-out model, and in fact it was cut out from carbon-fibre foam sandwiched sheets. It had off-the-shelf, super-cheap servos we bought on Amazon. We had a little companion computer running some parts at first, and we changed from that,” Klusak says.
“We iterated the motors we were using, and the way we were driving our pivoting axes. We changed the type of bearings, their interfaces on the axes and how we used them several times. We moved from concepts that move the arms independently of each other to a fixed system and back a couple of times. We’re probably going to release versions with each because both have pros and cons.”
The Pivot MK-V, a mock-up of which was presented at the Commercial UAV Expo in early September, is optimised for hovering. It has two arms that move in a permanently fixed relationship, each supporting two pairs of motors and propellers. However, the technology can also be used in VTOL vehicles with fixed-wing and lift-body configurations.
“One of the big issues you have is that to get such a VTOL to yaw in strong winds is very hard, because the yaw force induced by motor-speed variation only is not enough to counteract the push of the wind on the wing,” says Klusak.
“But if you can move the arms perpendicularly to one another you can induce yaw by pitching one forward and one backward. Then you have a very strong yaw moment. There are use cases where that makes sense and also cases where it is just not necessary.”
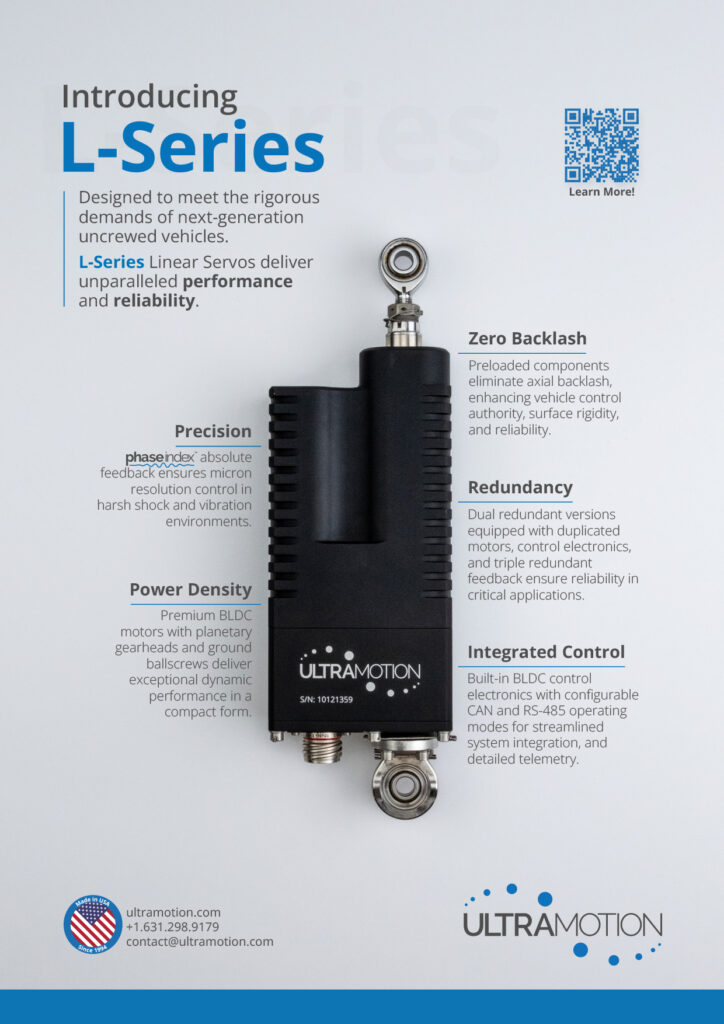
Powertrain development
Orthodrone decided early on to use a hybrid powertrain with a piston engine driving a generator to meet its range and endurance requirements. They chose a 4 kW Pegasus GE70 unit with electronic fuel injection, which provides power for the propulsion and control systems, ‘hotel’ loads and payloads.
“It’s the lightest generator system available and gives a power-to-weight ratio unlike any other,” Klusak says. “There are generator systems out there that look like chainsaws and even have pull knobs, and I don’t want that.”
Since meeting Pegasus shortly after Orthodrone’s inception, the two firms have developed a strong partnership.
“Over the years, we have learned what that generator system can do, and also how to get the most out of it through implementation into our hardware. For instance, we focused on custom solutions for the exhaust and cooling systems, and managed to gain 15% of power and a significant increase in fuel efficiency, enabling us to exceed our hover time and range goals,” says Klusak.
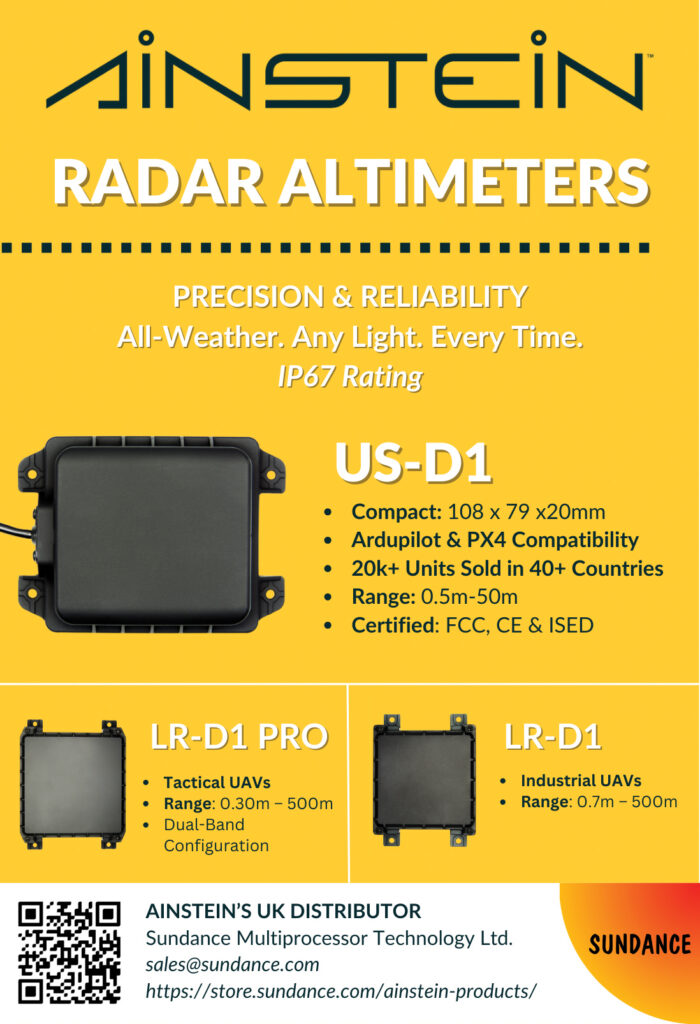
Orthodrone chose Alva Altus X60 Duo propulsion units, each consisting of two slotless motors that feature fibre-printed Halbach rotors. Each motor is fitted with a two-bladed Mezjlik propeller, developed especially for the X60 Duo units.
By design, the propulsion system has enough redundancy to save heavy, expensive sensors in the event of failure.
Keeping it smooth
“Vibration is probably one of the biggest issues in gas-hybrid UAS development and it is something we are continuously working on,” Klusak says. “We are very happy with where we are vibration-wise right now, but I think that’s work that will never stop, because the lower the vibration, the better the data you get.”
Vibration is affected by many factors, including the payload and anything else attached to the vehicle plus the method of attachment. Relatively small masses such as landing gear can have a significant effect. The forward portion of the Pivot MK-V’s gear is attached to the payload bay, and the rear portion to the engine bay, and there are significant differences in vibration of either based on the gear type and length.
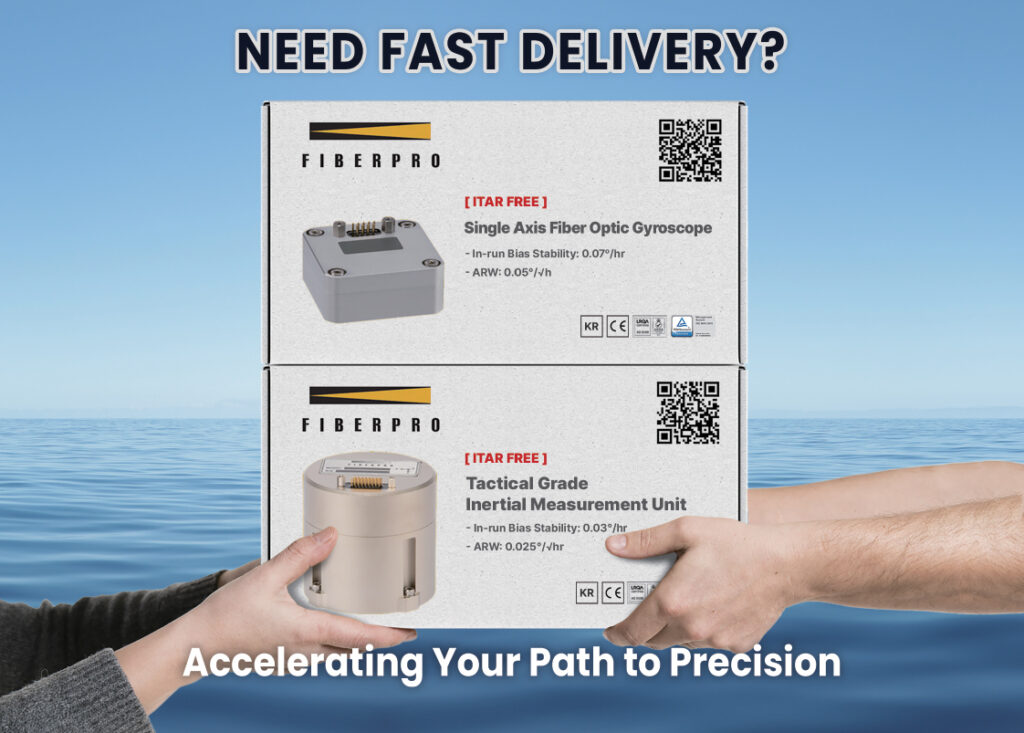
“I’ve seen systems that have a common rail for a vibrating range extender and a sensitive payload. And that, to me, does not make sense, particularly when using the kinds of high-quality sensors and IMUs we’ve been talking about,” he says.
“On the Pivot, the generator and the payloads are decoupled, each on its own specially tuned vibration-damping mounting structure. In the engine itself, the main masses are naturally balanced as it is a horizontally opposed, twin-cylinder boxer unit. This is mounted on dampers that isolate its vibrations from the rest of the back part of the vehicle, while the payload bay is on damping mounts that attach it to the forward structure.”
“It all becomes a little esoteric, because you might end up with a whole chain of damping systems for different parts, with the final goal of ensuring your sensor systems are vibrating within spec. And our drone has some rigid carbon-fibre structure, so you’ve got to make sure you do not get into a natural resonance.”
The structure makes use of fibre-weaving and layering technology, optimised to put strength where it is most needed, saving weight elsewhere.
It proved difficult to source carbon-fibre parts of the required quality to connect the propulsion system to the fuselage, but they are now working with a German company that can supply them.
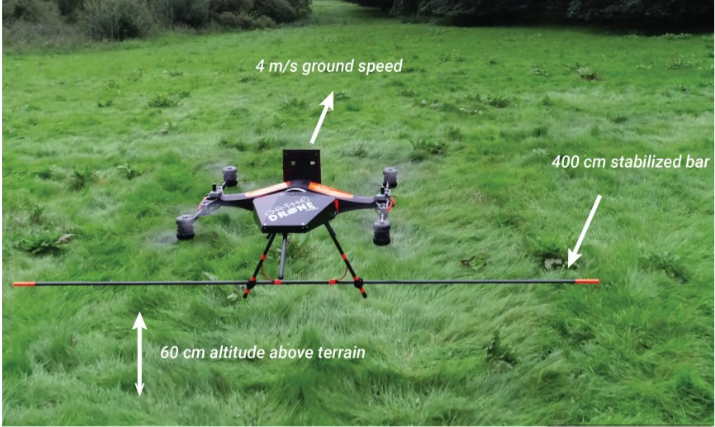
Commercial aims
The commercial plan for the Pivot MK-V and subsequent developments is to lease them out to customers, carrying out most operations remotely from a centre in Germany. However, with the current state of BVLOS regulations, there will have to be a customer representative onsite with remote control to take over in an emergency for the foreseeable future.
Klusak emphasises that the Pivot is currently at Technology Readiness Level (TRL) 6 and Orthodrone is planning to go to market next year. Depending on the regulatory regime that applies to its various deployment cases, it will have a maximum take-off weight (MTOW) of either 55 lb (25 kg) or 70 lb (31.75 kg).
The company is also planning a larger version with an MTOW of 110 lb (50 kg) and a payload of more than 55 lb (25 kg) to address use cases that are not part of what Klusak considers the company’s core market of offshore infrastructure inspection. These include deploying vehicle-grade sensors that look below the surface of the terrain, such as ground-penetrating radar (GPR) and magnetometers.
Such sensors require highly stable platforms to deploy them if they are to generate their highest-quality data, he says. The company has demonstrated the ability of one of its prototypes to keep the ends of a 4 m bar magnetometer 60 cm (+/- 1.27 cm) above the ground surface.
If you need to detect small, non-magnetic targets in the ground and be sure of finding what you are looking for, you need a high-resolution, vehicle-grade GPR system. That comes in a larger size – it’s just physics.
“That’s where building a bigger Pivot system gets very interesting,” Klusak says. “With our technology, the bigger you build it the more sense it makes, because we are just moving a fifth of the mass of the drone to change our thrust vectors. The remainder is resting mass. The bigger it gets, the less the centre wants to move.”
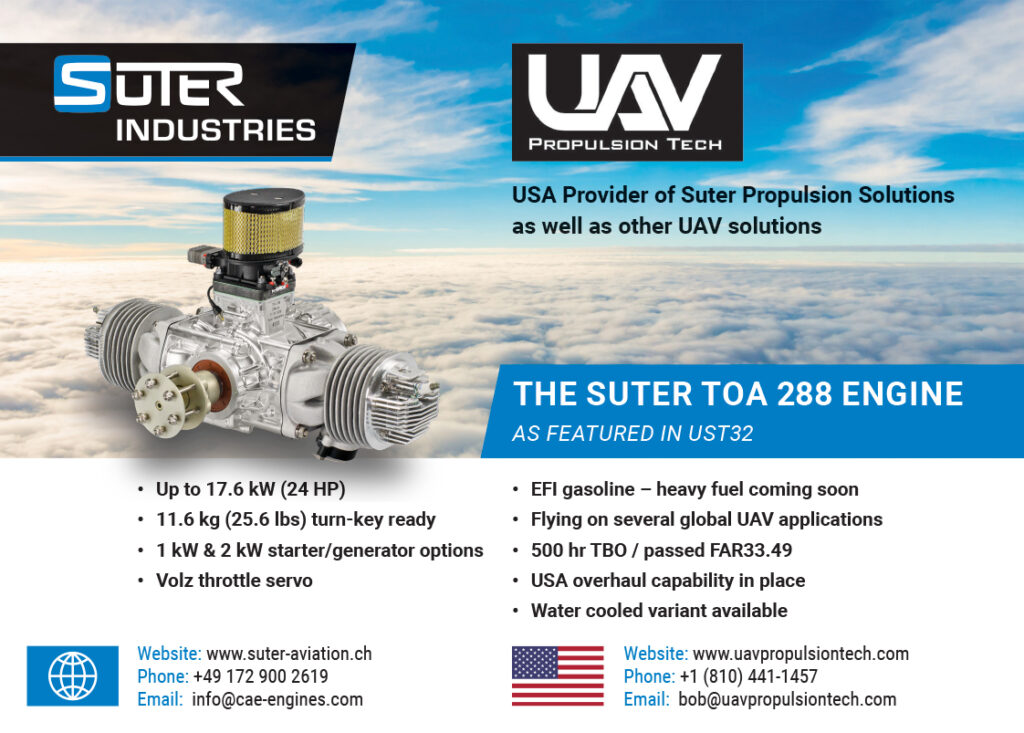
Open-source future
While key aspects of technology are protected, and Orthodrone has patents pending on Pivot in 42 countries, Klusak intends to licence it eventually for other companies to use in their own designs.
“Down the line, we are confident you’re going to see more and more Pivot-style drones, and from that standpoint I’m very happy that we’re working with a lot of open-source technology,” he says.
“Personally, I think open source is the only way that makes sense in the drone world, because it allows us to have thousands and thousands of flight hours on crucial software and hardware. Everyone benefits from the testing other people do.
“It’s great to see that the growing UAS market and industry are still, to a sizeable part, a group effort.”
Key specifications
- Max take-off weight: 55 lb/70 lb
- (25 kg/32 kg) depending on regulations
- Payload: 5 kg (11 lb)
- Endurance: 3 hours
- Structural material: carbon-fibre reinforced polymer
- Some key suppliers
- Hybrid powerplant:
- Pegasus Aeronautics
- Tilt/stabilisation motors: Maxon
- Propulsion motors: Alva
- Propellers: Mezjlik
- High-resolution RGB camera: Phase One
- Lidar: Riegl
UPCOMING EVENTS
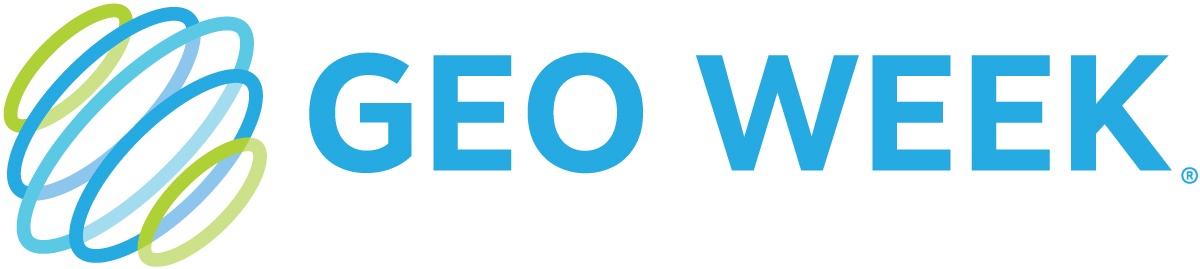
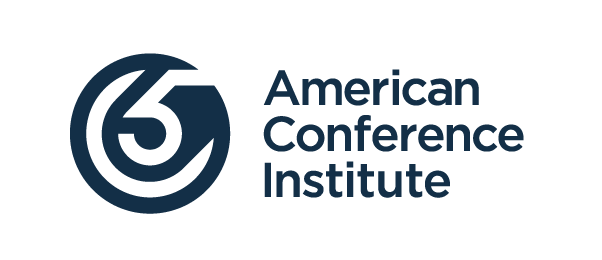
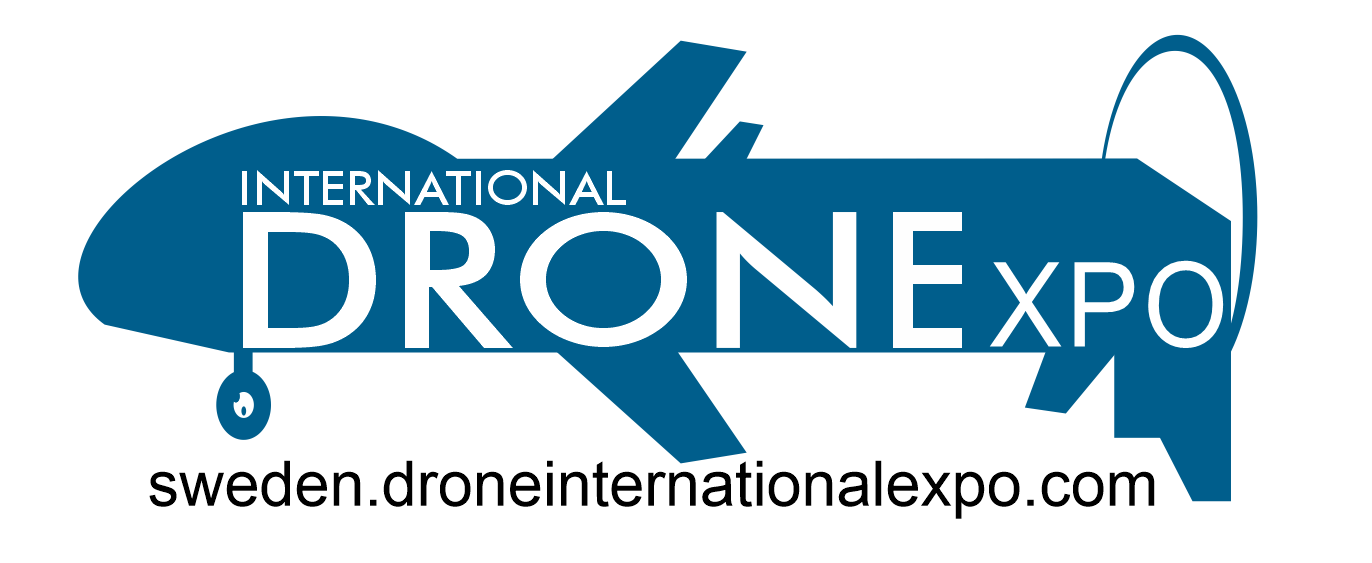
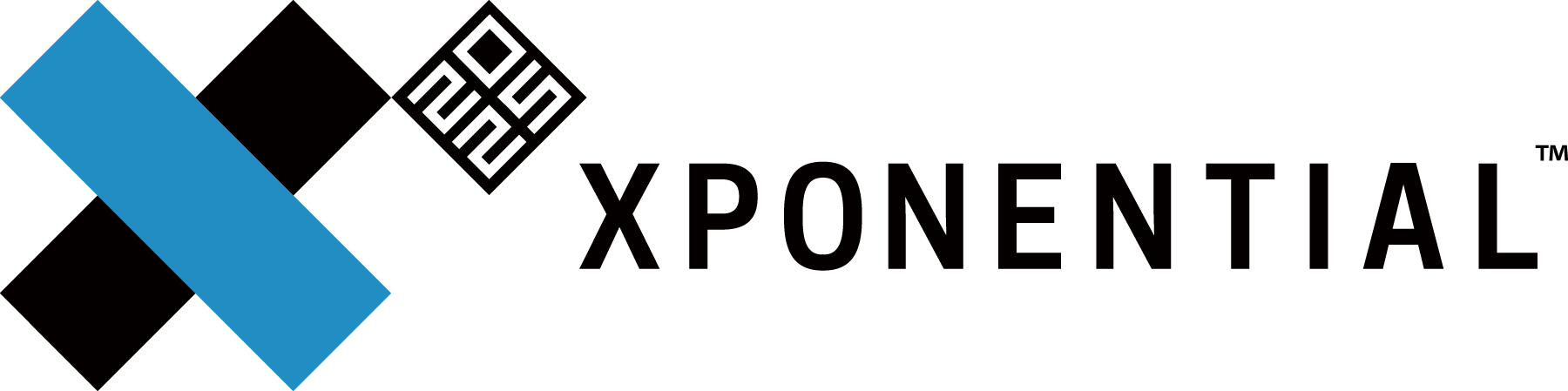
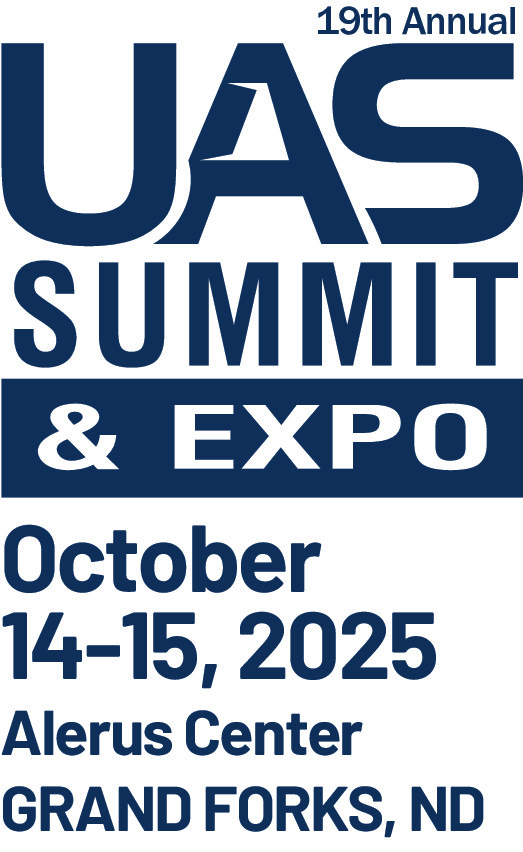

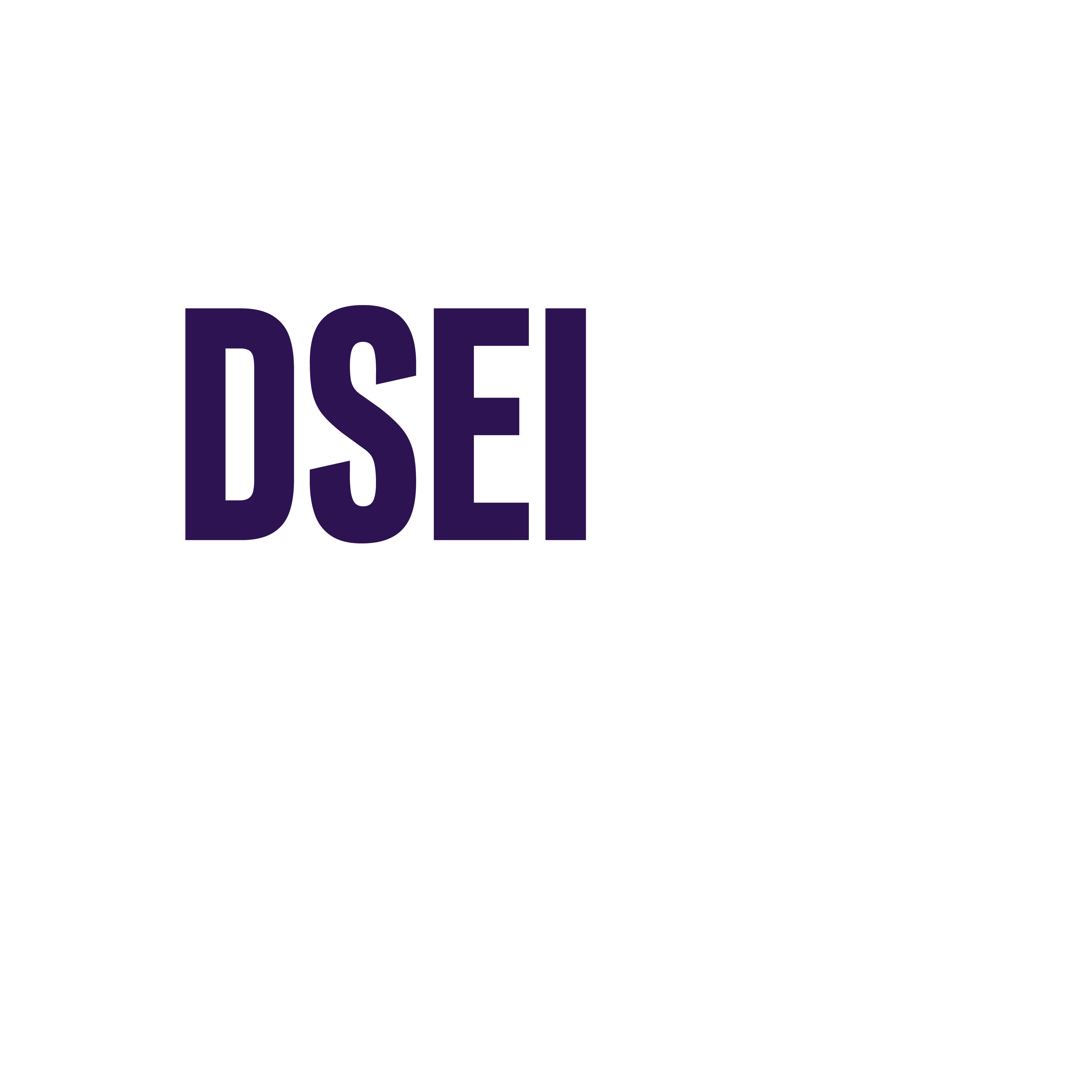
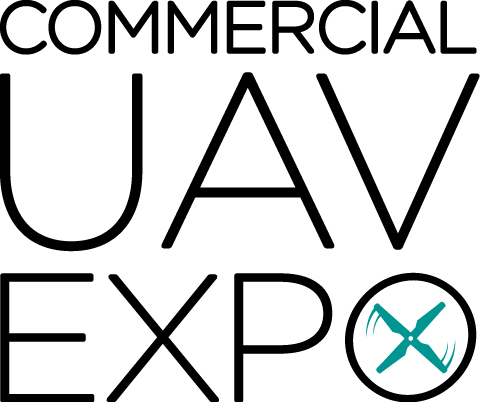
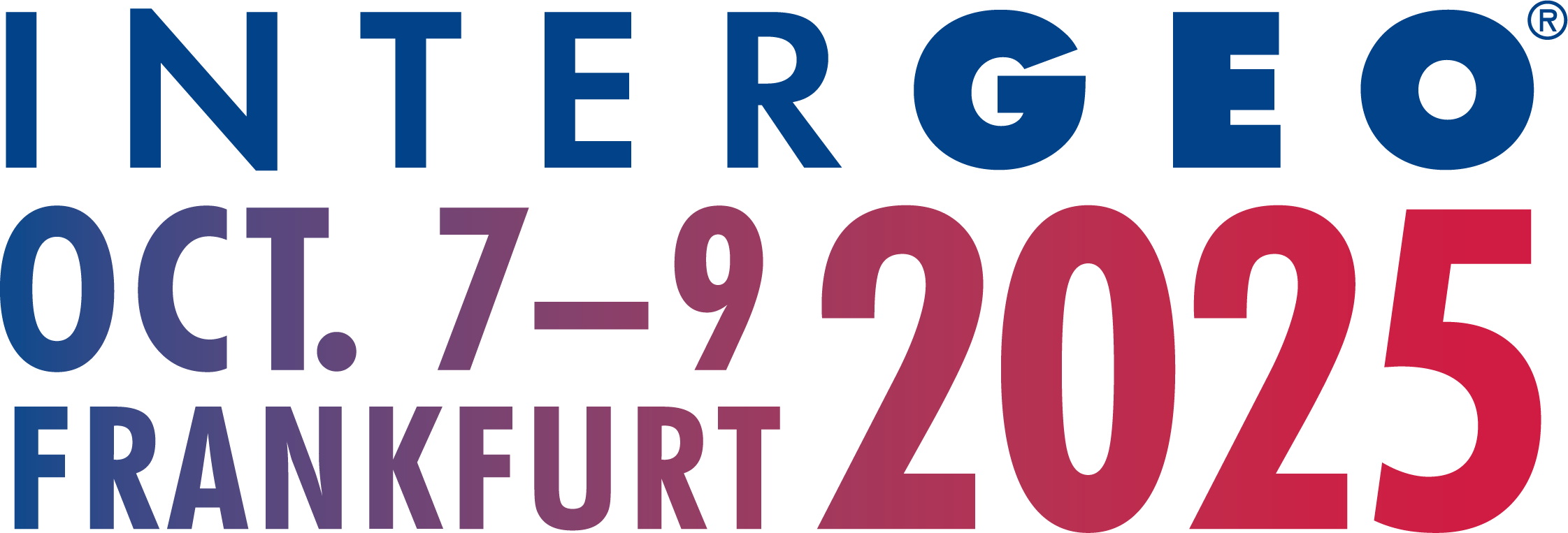
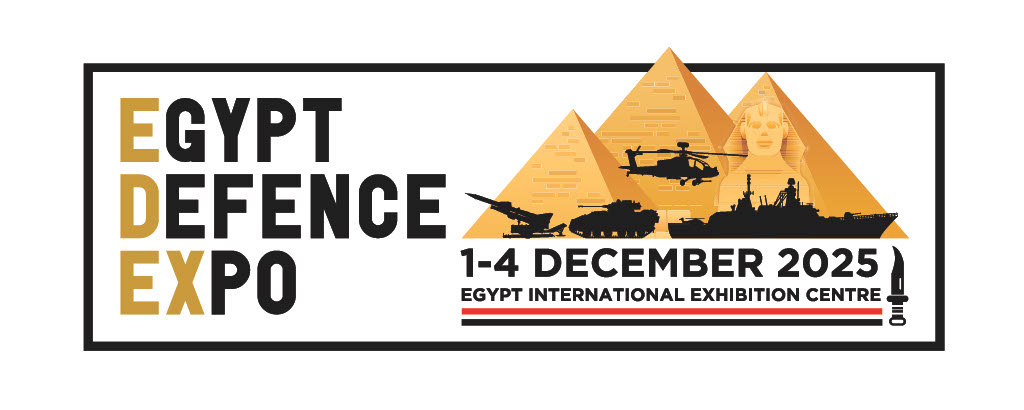
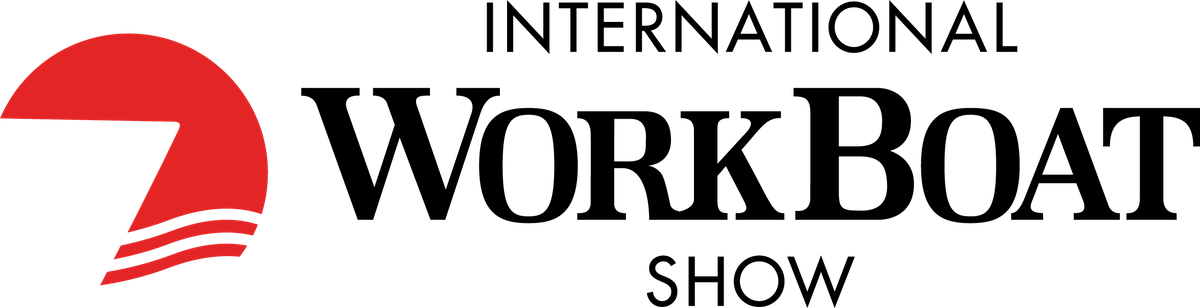