3D-printed rotor actuator
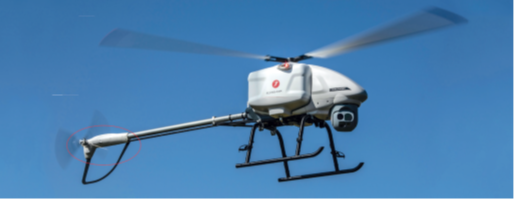
Flying-Cam has used 3D printing to develop a tail rotor actuator for its latest UAV (writes Nick Flaherty).
The actuator is built using a powder bed fusion (PBF) process with the Windform XT 2.0 carbon fibre-reinforced composite from CRP Technology. This has been used for the Discovery single rotor uncrewed helicopter, which has a 75 kg MTOW to carry payloads ranging from high-resolution cameras to remote sensing equipment for BVLOS missions.
Windform XT 2.0 has an 8% greater tensile strength and 2% greater tensile modulus than the previous-generation material, as well as a 46% increase in elongation at break.
Flying-Cam has also worked with CRP Technology on the former’s SARAH 4.0 eVTOL uncrewed system, 3D printing the airframe structure, air-guide cooling system, tail unit and main battery connection.
“The tail rotor actuator is clamped on the tail boom and supports the carbon plate used as a tail rotor ground protection,” said Emmanuel Previnaire, CEO of Flying-Cam. “For this reason, a good stress resistance was needed.
“The clamping strength depends on the construction material’s capabilities. We chose Windform XT 2.0 as it allows us to achieve that with a good weightresistance ratio.”
“Using 3D printing and composite materials gave us the ability to create complex wiring channels with strong attachment points, in one piece.”
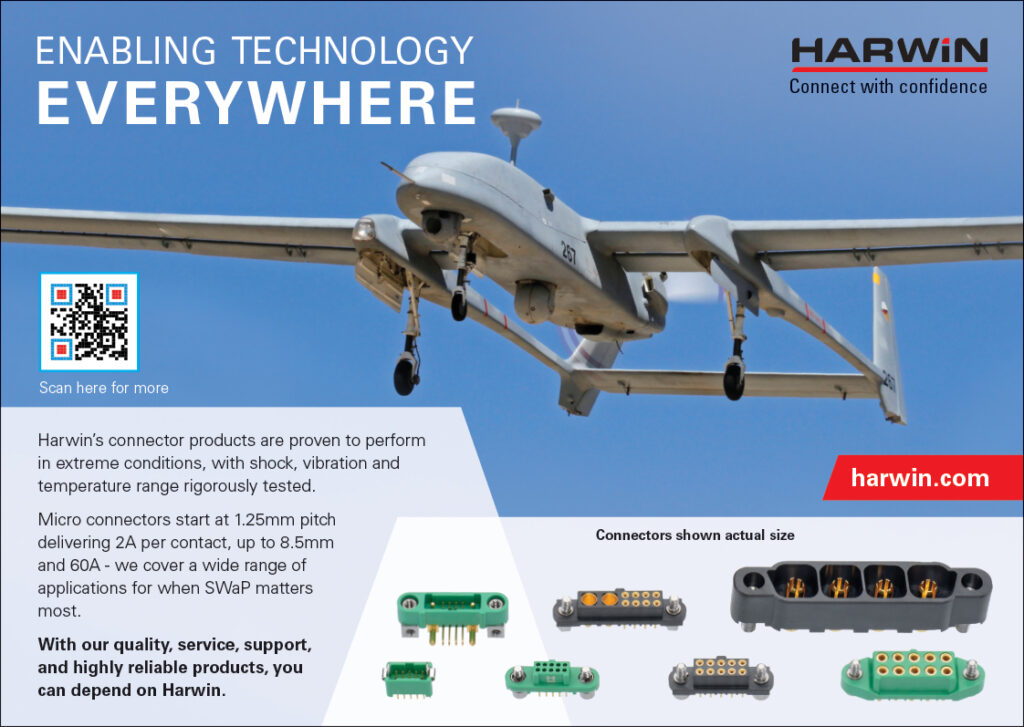
UPCOMING EVENTS
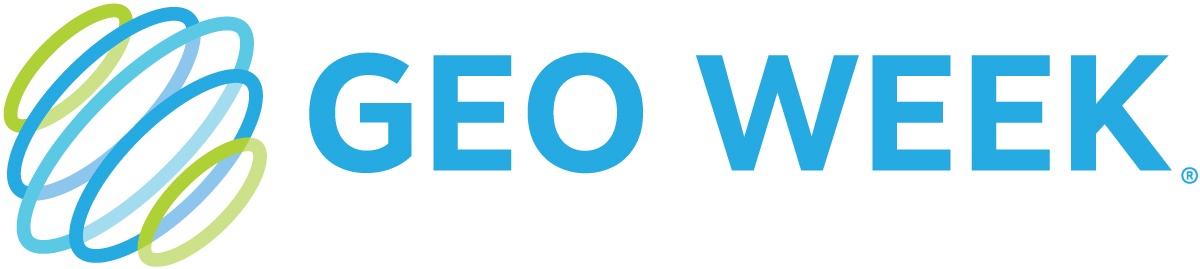
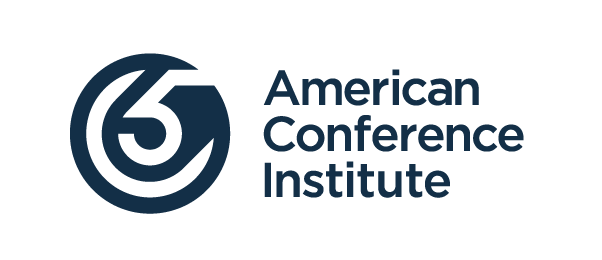
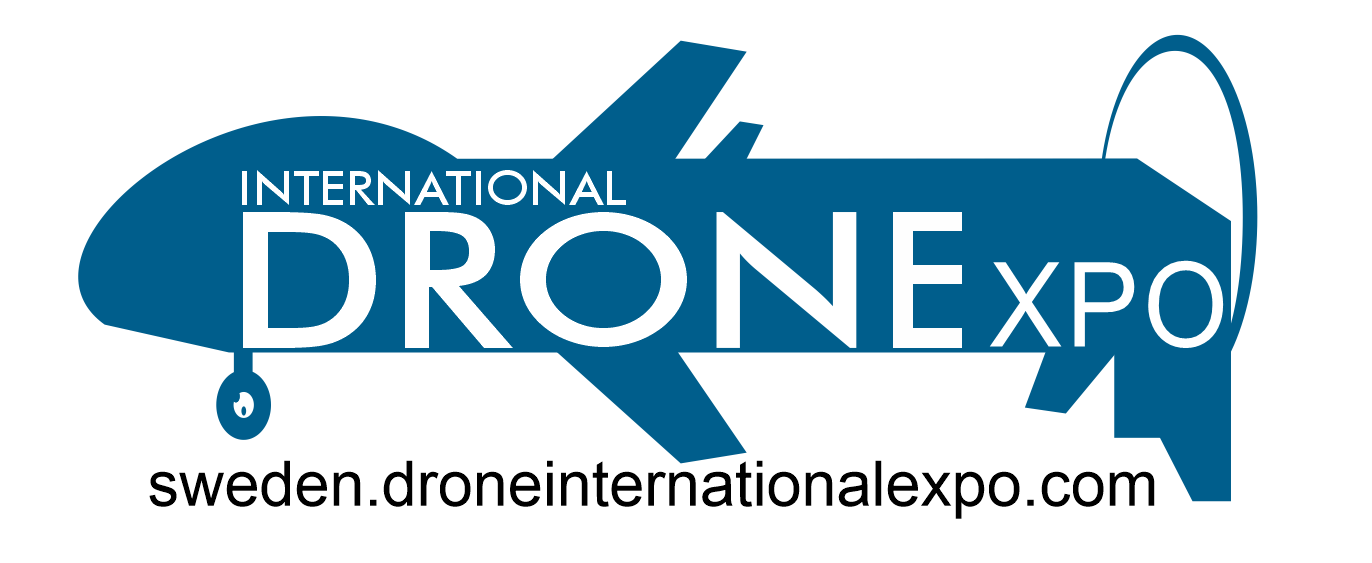
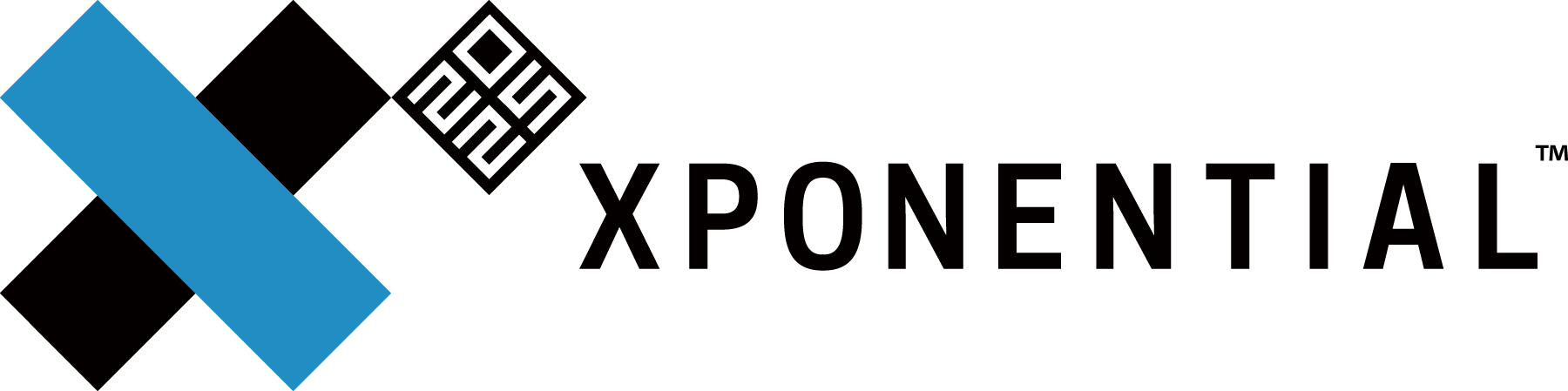
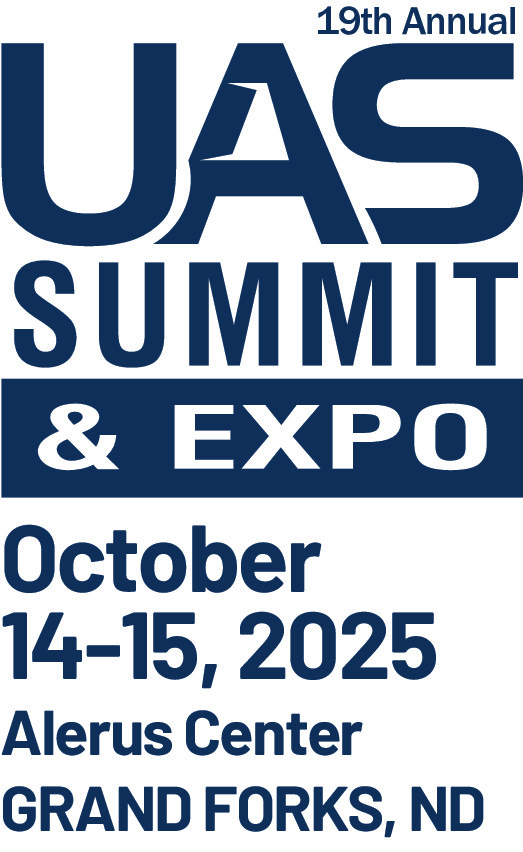

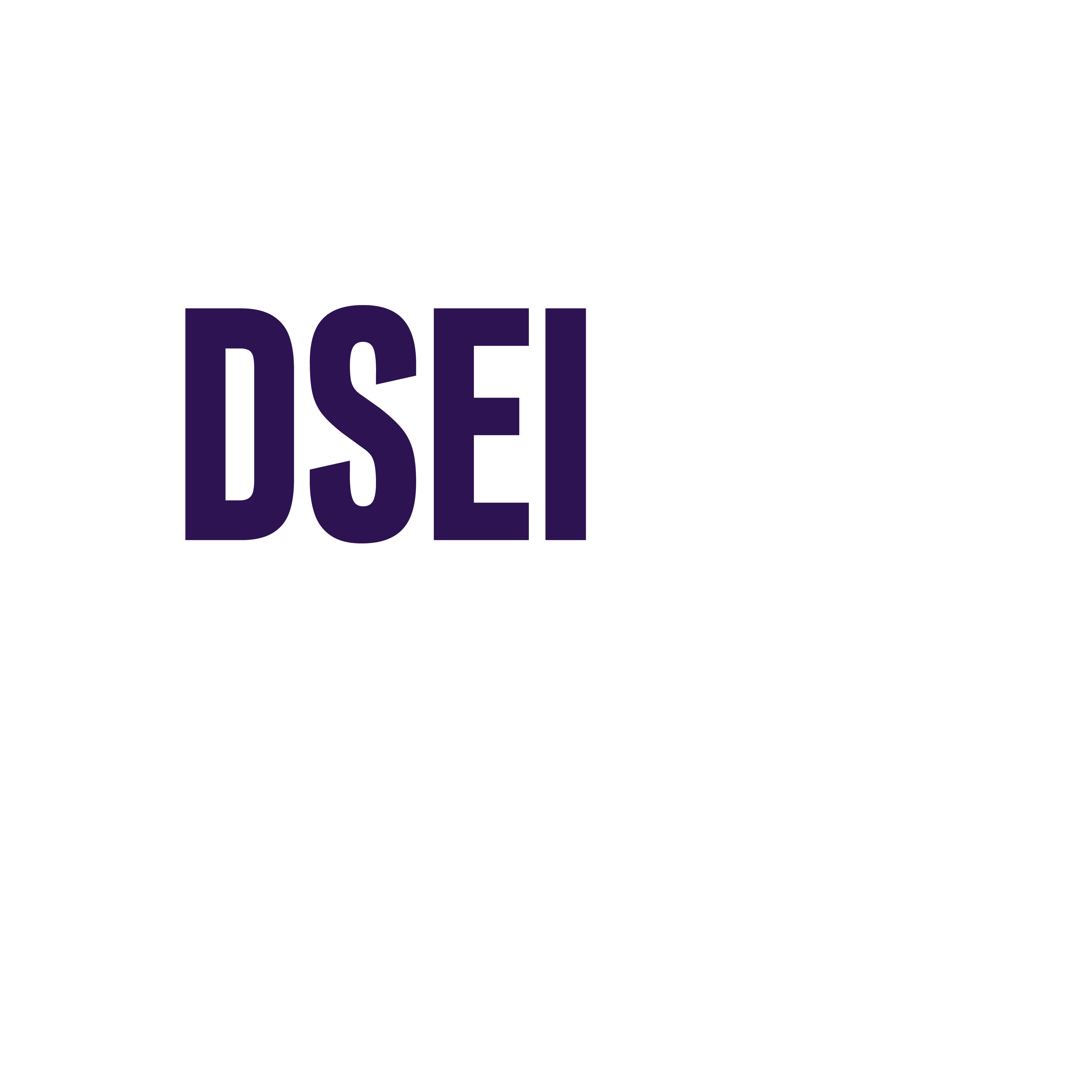
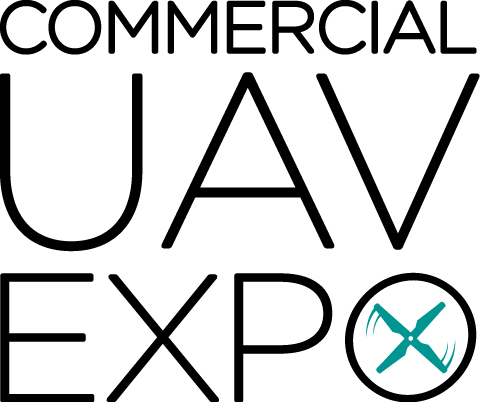
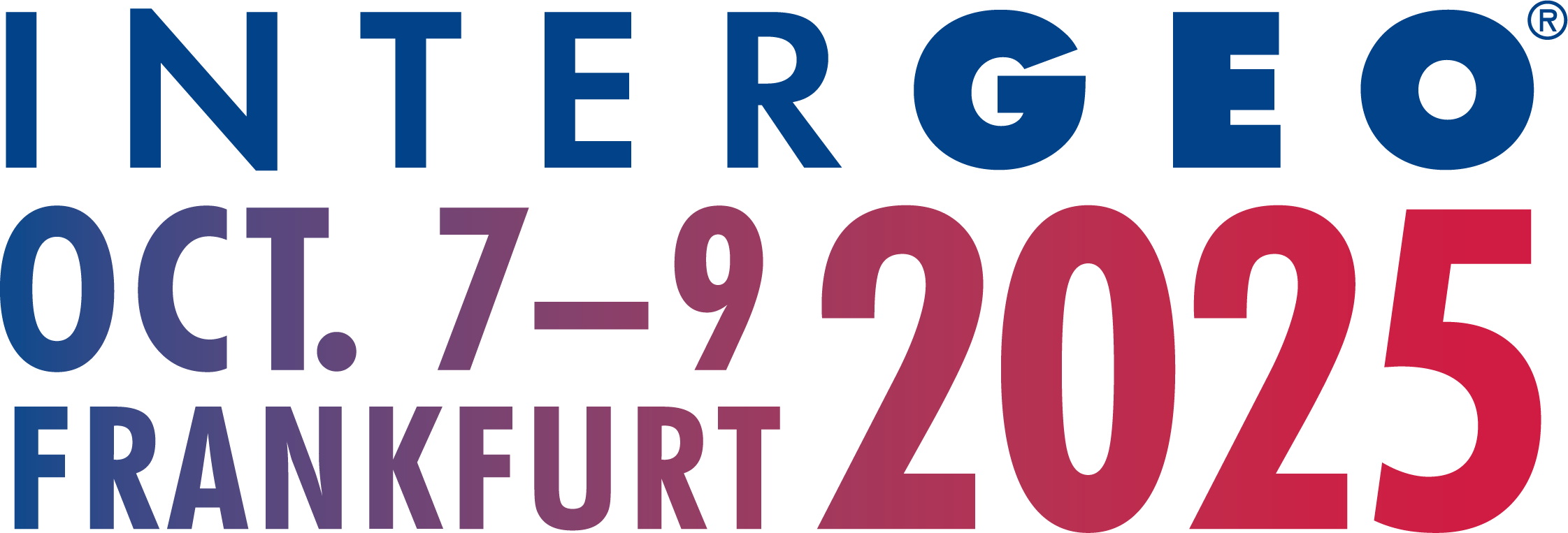
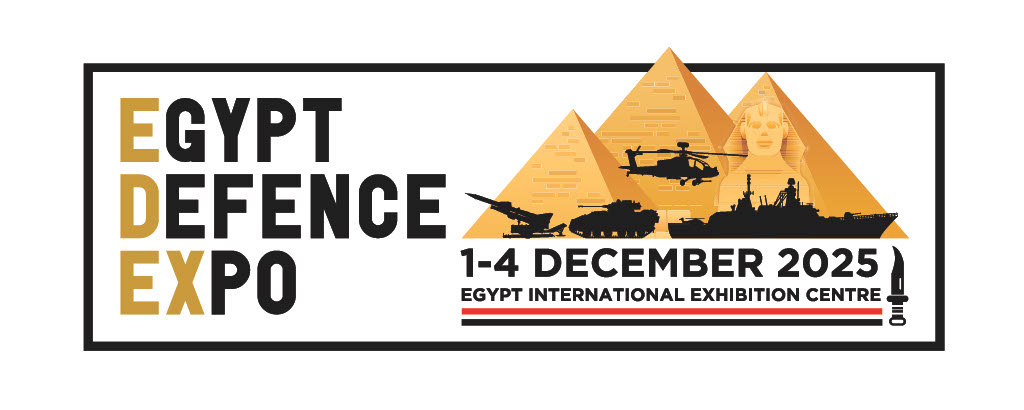
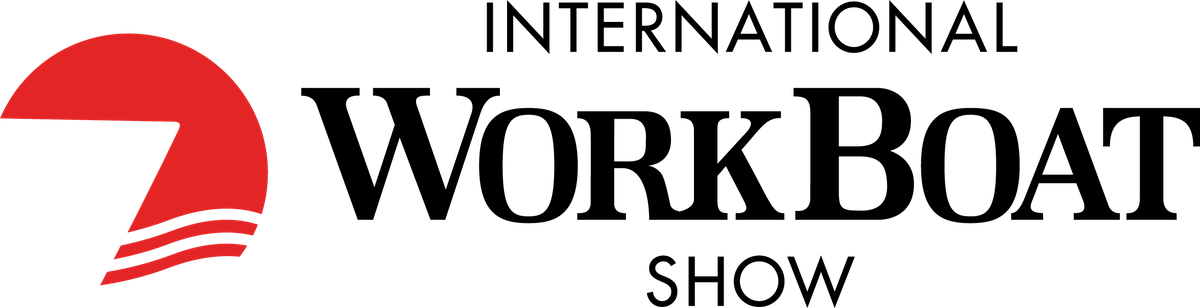